1. L-Bend
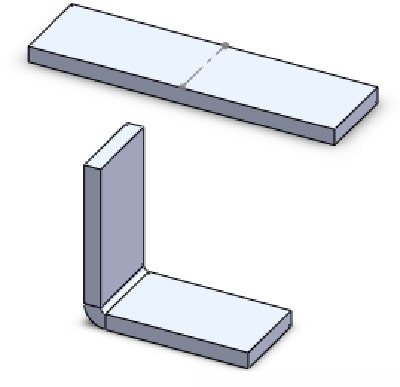
According to the angle, it can be divided into two categories: 90-degree turns and non-90-degree turns.
According to the processing method, it can be divided into two categories: general processing (L > V/2) and special processing (L < V/2).
- Mold selection should be based on material, plate thickness and forming angle.
- Inclined principle:
(1) Based on the principle of two backstops and positioning based on the shape of the workpiece.
(2) When using a back gauge, it is important to consider the deflection and ensure that it is aligned with the center line of the workpiece bend size.
(3) For small curves, it is more efficient to process them in reverse positioning.
(4) It is recommended to place the back gauge below the middle to avoid lifting when tilting.
(5) It is best to position yourself close to the back gauge.
(6) It is recommended to lean with the longer side of the workpiece.
(7) Templates can be used to assist with irregular positioning and tilting of the hypotenuse.
- Precautions:
When processing, pay attention to the positioning method and the movement of the anti-recoil mechanism in various positioning methods.
When installing the mold, it must be folded and the anti-return mechanism retracted to prevent deformation of the part during bending.
When bending large parts internally, it can be challenging to position the part or avoid damage due to the larger shape and smaller bending area. To avoid this, a positioning point can be added in the longitudinal direction during processing. This two-way processing method facilitates positioning, improves safety, prevents damage to the part and increases production efficiency.
2. N curve
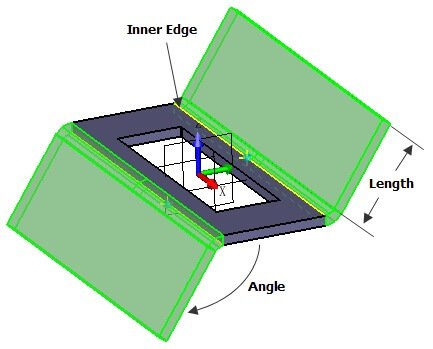
N curves must use different processing methods based on the shape. When bending, the internal dimensions must be greater than 4 mm, and the size of the X dimension is limited by the shape of the mold. If the material size is less than 4 mm, special processing methods must be used.
- Choose the mold based on the thickness, size, material and bending angle of the material.
- Inclined principle:
(1) Make sure the workpiece does not interfere with the tools.
(2) Make sure the tilt angle is slightly less than 90 degrees.
(3) It is best to use two backrest mechanisms for leaning, except in special cases.
- Precautions:
(1) After L-bending, the angle should be 90 degrees or a little less than 90 degrees to facilitate processing and positioning.
(2) During the processing of the second bend, the workpiece should be positioned in the center of the processing surface.
3. Z Curve
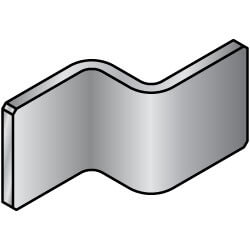
Z-folding, also known as offset folding, refers to folding in the opposite direction. The angle is divided based on the difference between the hypotenuse and the ruler. The minimum size of the bending process is limited by the mold, and the maximum size is determined by the shape of the processing machine. In general, when the internal size of the Z-fold is less than 3.5 times the thickness (T), an offset die is used. When it is greater than 3.5T, the normal processing method is applied.
- Inclined principle:
(1) Convenient inclined position and good stability.
(2) The inclined position is generally the same as the L-bend.
(3) During the second tilt, the workpiece must be level with the lower die.
- Precautions:
(1) The L-bend processing angle must be in place, and the general requirement is 89.5 to 90 degrees.
(2) Pay attention to the deformation of the part when retracting.
(3) The processing order must be correct.
(4) For special processing, the following methods can be used:
- Centerline separation method (eccentric machining)
- Small V machining (increased bending factor required)
- Easy molding
- Grinding the bottom mold.
4. Acute flexion and hem
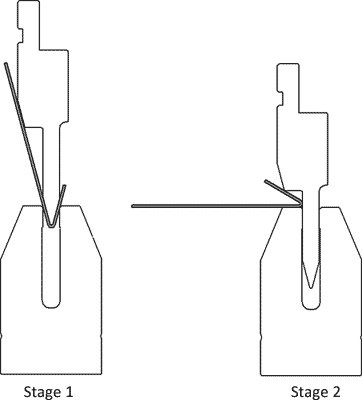
The processing steps for sharp folds and hems are:
- First, bend the material to a depth of approximately 35 degrees.
- Then use a Hemming die to flatten it to a flat, closed position.
- Mold selection:
Based on 5 to 6 times the thickness of the material, select the width of the bottom die V-groove with a depth of 30 degrees. Choose the top die based on the specific flattening edge conditions.
- Precautions:
The flat side must pay attention to the parallelism of both sides. For longer flattening edges, it is recommended to bend first and then flatten. For shorter flattening edges, fill processing can be used.
5. Press Hardware
Using a press brake to press riveted hardware generally requires the use of concave molds, fixtures, and other auxiliary mold processing tools. Common hardware items include crimp nuts, pins, screws, and others.
Precautions:
When the shape of the workpiece needs to be protected, prevention processing must be done.
After processing, inspect the torque, check whether the thrust meets the standard, and make sure the hardware and workpiece are flat and closed.
When pressing the hardware close to the machine after bending and riveting, pay attention to avoid processing and maintain parallelism between the mold and the part.
If bulging occurs, make sure there are no cracks in the protruding edge and that the protruding edge is not higher than the surface of the workpiece.
6. Special I old training

General special molding processing includes:
Small offsets, hooks, pull bridges, pull bags, pumpkins and some irregular shapes.
Special molds are usually positioned using back gauge fingers or self-positioning.
The most important aspect of processing with special molds is to ensure that their functions and assembly requirements are not affected and that their appearance is normal.