Heat treatment principle

Transformation of steel during heating
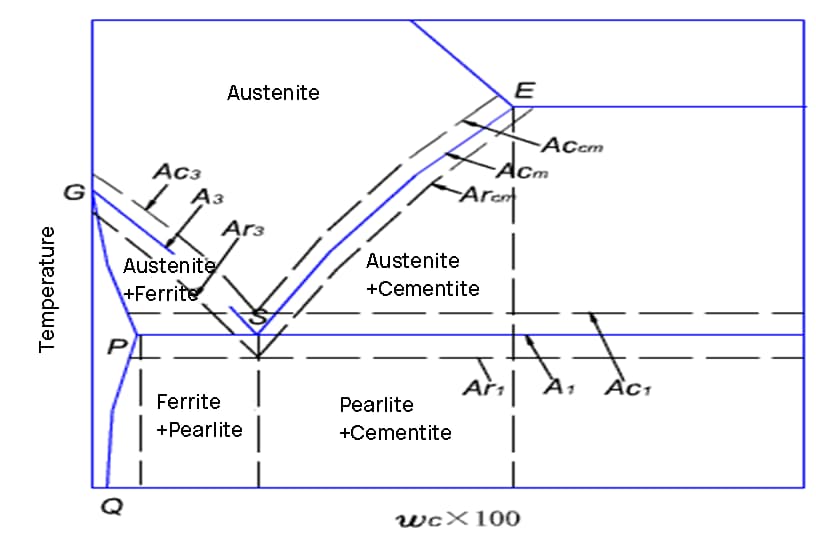
Curve C
The C curve is a tool used to analyze the transformation of the microstructure of carbon steel during cooling after heating to form austenite.
There are two methods to cool steel in the heat treatment process:
- Isothermal Cooling Transformation: This process involves cooling the steel, which has been heated to form austenite, to a specific temperature below the A1 line at a relatively rapid rate and then isolating it to allow the austenite to undergo a structural transformation at a constant temperature.
- Continuous Cooling Transition: This refers to the continuous decrease in temperature that occurs over time during the cooling process.
In practical production, continuous cooling is the most commonly used method.
1. Method of cooling steel during heat treatment


Isothermal transformation curve of subcooled austenite to eutectoid steel

The. High temperature transition
The austenite in eutectoid steel is cooled to a temperature ranging from A1 to 550°C, resulting in a pearlite structure through the isothermal transformation process. This transformation of austenite to pearlite is the result of the alternating nucleation and growth of ferrite and cementite, as illustrated in Figure 3-7.
Pearlite formation
Firstly, the nucleus of cementite crystals is formed at the grain boundary of austenite.
The carbon content of cementite is greater than that of austenite, leading to the absorption of carbon atoms from the surrounding austenite.
As a result, the carbon content of nearby austenite is reduced, creating conditions for the formation of ferrite and converting this part of the austenite into ferrite.
The low carbon solubility of ferrite means that excess carbon must be transferred to the adjacent austenite as it grows, causing the carbon content of the adjacent region of the austenite to increase and creating conditions for the formation of new cementite.
Through this process, the austenite is eventually completely transformed into a pearlite structure with alternating layers of ferrite and cementite.

The formation of pearlite requires the movement of carbon atoms, and the distance of movement determines the width of the pearlite lamellae. At high temperatures, the movement of carbon atoms is more extensive, resulting in wider pearlite lamellae.
On the other hand, at low temperatures, carbon atoms have difficulty moving and therefore pearlite lamellae are denser. The microstructure transformed from 727°C to 650°C is pearlite.

The structure obtained through transformation between 650°C and 600°C is known as sorbite, also called fine pearlite. The transformation between 600°C and 550°C results in the formation of troostite, also known as very fine pearlite.

These three types of pearlite structures are differentiated only by lamellar spacing and do not present fundamental differences.
B. Intermediate Temperature Transition
The products of the isothermal transformation of austenite to eutectoid steel, from subcooling to a temperature range of 550°C to 240°C, belong to the bainite structure. Upper bainite is formed in the upper part of this temperature range, while lower bainite is obtained in the lower part. Lower bainite has improved hardness and strength, as well as better plasticity and toughness. However, upper bainite has no practical applications.

w. Low temperature transition
It is highly challenging for the carbon atoms in austenite to move below 240°C.
Austenite undergoes only one isomorphic transformation, changing from a face-centered cubic structure (y-iron) to a body-centered cubic structure (α-iron).
All carbon atoms of the original austenite remain in the body-centered cubic lattice, resulting in supersaturated α-iron.
This supersaturated solid solution of carbon in α-iron is called martensite.
Retained austenite
When the austenite in eutectoid steel is cooled to 240°C (MS), it begins to transform into martensite.
As the temperature continues to drop, the amount of martensite increases while the undercooled austenite decreases.
When the temperature reaches -50°C (MF), the undercooled austenite has completely transformed into martensite.
Thus, the structure between MS and MF consists of martensite and retained austenite.
Due to variations in carbon content, martensite comes in two forms.
High-carbon martensite takes the shape of a needle, known as needle-shaped martensite.
Low-carbon martensite, on the other hand, is plate-like and is called plate-like martensite.

Tissue | Carbon content (%) | Mechanical properties | |||
CDH | (Mpa) | OK J/ cm2 |
Ψ(%) | ||
Low carbon | 0.2 | 40~45 | 1500 | 60 | 20~30 |
High carbon | 1.2 | 60~65 | 500 | 5 | 2~4 |
Table 4-5 comparison of properties of 15MnVB low carbon martensite steel and quenched and tempered 40Cr steel
Steel Grade | 15MnVB40Cr |
state | Quenching and tempering state of low carbon martensite |
CDH | 4338 |
σ o.2 /MPa | 1133800 |
σb /MPa | 13531000 |
δ5 (%) | 12.69 |
φ(%) | 5145 |
a k /Jcm -2 | 9560 |
at k (-50℃)/J.cm -2 | 70≤40 |
(2) Continuous cooling

Fig. 3-9 Cooling transformation curve of eutectoid steel
The. Oven cooling
When the cooling curve crosses the initial line of pearlite transformation, the transformation of austenite to pearlite begins.
Once the cooling curve intersects the end line of the transition, the transformation is complete.
As a result of the transformation that occurs in the pearlite region, a pearlite structure is formed.
B. Air cooling
As a result of the rapid cooling rate, transformation occurs in the sorbite region, producing ferrite as the transformation product.
w. oil cooling
The cooling curve only intersects with the initial line of the pearlite transformation (in the troostite transformation zone), but does not intersect with the final line.
As a result, only part of the austenite is transformed, resulting in the formation of troostite as a transformation product. The remaining portion of austenite transforms into martensite upon cooling to the MS line.
Finally, a mixed structure of martensite and troostite is obtained.
Refers to the product that has been cooled in oil.
d. Water cooling.
Due to the rapid cooling rate, the cooling curve does not intersect with the initial line of pearlite transformation.
When cooled below the initial line for martensite transformation, austenite will transform into martensite.
Comparison between continuous cooling curve and isothermal C curve
The continuous cooling curve is located in the lower right part of the isothermal C curve, with a lower P transformation temperature and a longer duration.
Eutectoid and hypereutectoid steel have a P-transformation termination line but no B-type transformations during continuous cooling.
For hypoeutectoid steel, subcooling in a specific temperature range during continuous cooling can result in partial transformation to B.
Determining the continuous cooling transformation curve is a challenge, which is why many steels still lack this information.
In practical heat treatment, the continuous cooling transformation process is often estimated with reference to the C curve.
Comparison of TTT curve and CCT curve of eutectoid carbon steel


TT curve of hypoeutectoid and hypereutectoid steels
2. Hardenability of steel
(1) Concept of hardenability
Steel hardness refers to the depth to which steel can be hardened during quenching, which is a characteristic of steel.
During quenching, the cooling rate varies in different sections of the part.
The surface cools at the fastest rate, exceeding the critical cooling rate for martensite formation. As a result, a martensitic structure is formed after quenching.
As the rate of cooling decreases towards the center, if the rate of cooling at a certain depth from the surface falls below the critical rate of cooling required for the formation of martensite in the steel, then the workpiece will not fully harden as There will be a non-martensitic structure present after quenching.

(2) Effect of hardenability on mechanical properties
The mechanical properties of steels with good hardenability are uniform across the section, while those of steels with low hardenability vary across the section. Mechanical properties, particularly toughness, decrease as you get closer to the center.
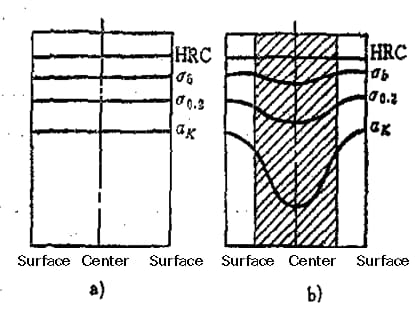
Fig. 5-53 comparison of mechanical properties of steels with different hardenability after quenching and tempering treatment
a) Hardened shaft
b) Unhardened shaft
(3) Determination and expression of hardenability
There are several methods for determining hardenability. The most commonly used method, as specified in GB225, is the end temper test for structural steel. This test measures the thickness of the hardenable layer.
Another commonly used measure of hardenability is the critical diameter. This value represents the maximum diameter of the semi-martensitic structure (50%) that can be achieved in the center of the steel after quenching in a cooling medium. It is denoted as Do.
Top tempering method

Quenching critical diameter
