1. Introduction to gas cutting
Oxyfuel cutting, also known as oxyacetylene cutting or flame cutting, is a highly effective cutting process in equipment manufacturing.
Oxyfuel cutting equipment is simple and easy to operate, making it suitable for cutting carbon steel and common low-alloy steel. It can accurately cut straight lines, circles and various complex shapes, with a wide range of cutting thicknesses.
It is also easily automated, particularly with the application of CNC technology, photoelectric tracking technology and higher quality cutting nozzles, a trend that is becoming more evident. Gas cutting produces clean cutting edges and has a faster cutting speed. In addition, oxyfuel cutting can also cut chamfers directly.
The gas cutting torch is used for thermal cutting of materials by mixing fuel gas with oxygen to produce a flame. It is also known as oxygen cutting or flame cutting.
During gas cutting, the flame preheats the material at the cutting point to its ignition temperature and then oxygen is injected to cause vigorous combustion by oxidizing the metal material. The resulting oxide slag is expelled by the gas flow, creating a gash.
The purity of oxygen used for gas cutting must be greater than 99%. The fuel gas used is usually acetylene gas, but it can also be petroleum gas, natural gas or coal gas.
Acetylene gas provides greater cutting efficiency and better quality, but is more expensive. Gas cutting equipment mainly consists of the cutting torch and gas source.
The cutting torch is the tool that generates the gas flame, transfers and regulates the cutting thermal energy, and its structure affects the cutting speed and quality. Using fast cutting nozzles can improve cutting speed, resulting in straight cuts and smooth surfaces.
For manual operation, gas cutting torches use oxygen and fuel gas cylinders or generators as the gas source. Semi-automatic and automatic gas cutting machines are equipped with cutting torch drive mechanisms or coordinate drive mechanisms, contour cutting mechanisms, photoelectric tracking or digital control systems.
Automatic gas cutting machines used for mass production can be equipped with multiple cutting torches and computerized control systems.
2. Gas cut-off mechanism and conditions
The metal at the part's cutting point is preheated to ignition temperature using an oxygen-acetylene flame and then is blown vigorously with a high-velocity stream of pure oxygen.
At this point, the metal undergoes intense oxidation and the heat generated melts the metal oxide into a liquid.
At the same time, the oxygen flow eliminates the molten oxide, resulting in a clean cut on the workpiece. By moving the cutting torch forward, the workpiece can be cut continuously.
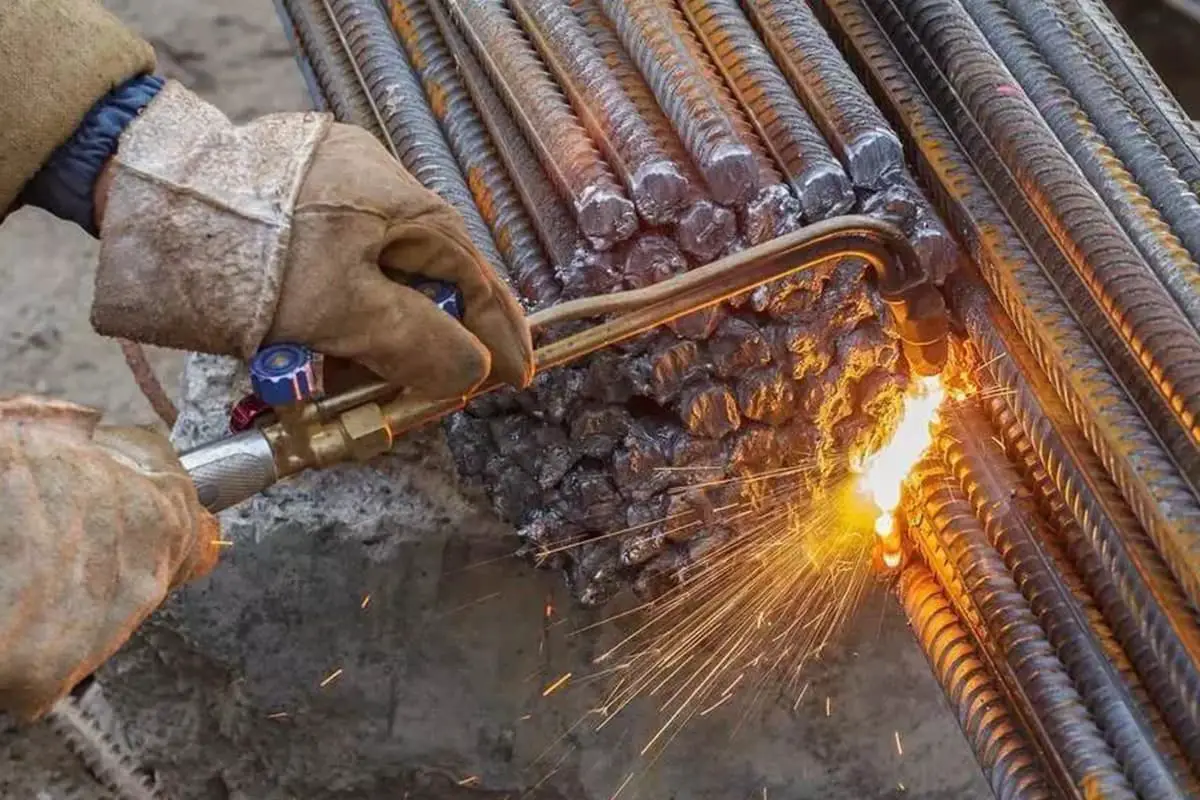
To achieve oxygen cutting, the following conditions must be met:
1) The ignition temperature of the metal must be lower than its melting point.
2) The melting point of the metal oxide must be lower than the melting point of the metal.
Pure iron, low-carbon steel, medium-carbon steel and ordinary low-alloy steel meet the above conditions and have good gas cutting performance. High-carbon steel, cast iron, stainless steel, as well as non-ferrous metals such as copper and aluminum are difficult for oxygen to cut.
3) Sufficient heat release during metal combustion:
Through testing and analysis, it has been determined that when cutting low carbon steel, approximately 70% of the total heat required is released during combustion, while flame preheating only accounts for 15%-30%. Therefore, this requirement can be met.
4) The thermal conductivity of the metal should not be too high:
The thermal conductivity of the metal should not be too high, as excessive heat loss from the preheating flame and the release of heat during the cutting process at the metal cutting point may prevent the cutting process from starting or continuing. For example, copper and copper alloys cannot be cut due to their high thermal conductivity.
5) Good fluidity of the generated oxide:
The oxide generated must have good fluidity. Otherwise, the oxide cannot be effectively eliminated during cutting, making the cutting process difficult.
3. Gas cutting equipment
Gas cutting machines are mechanized equipment that replace manual gas cutting torches. They feature higher productivity, better cut quality, lower labor intensity and lower costs compared to manual gas cutting.
1) Semi-automatic gas cutting machine:
It consists of a small carriage that automatically moves the cutting nozzle along a dedicated track, but the trajectory of the track needs to be adjusted manually.
2) Profile Gas Cutting Machine:
Gantry type: The cutting nozzle is driven along the profile by wheels.
Swing arm type: The cutting nozzle is driven by a swing arm mechanism.
3) Photoelectric tracking gas cutting machine:
This automated gas cutting equipment uses the principles of photoelectric tracking to automatically follow patterns and drive the cutting torch for profile cutting.
4) CNC Gas Cutting Machine:
CNC stands for Computer Numerical Control, which is a new control method where instructions (or programs) to control machine tools or equipment are provided in digital format. When these instructions are provided to the control equipment of an automatic CNC gas cutting machine, the machine can automatically perform cutting according to the provided program.
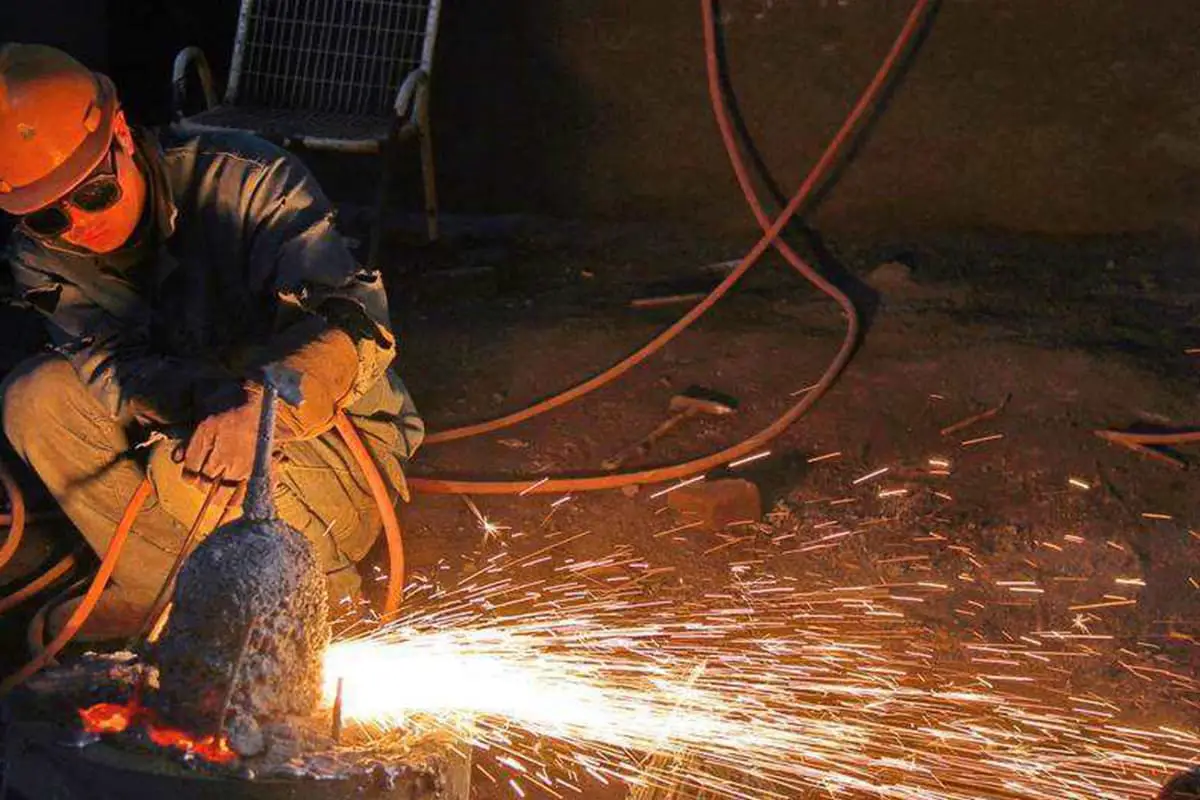
4. Gas cutting process
The gas cutting process mainly includes the cutting oxygen pressure, cutting speed, preheating flame efficiency, the inclination angle of the cutting nozzle and the workpiece, and the distance between the cutting nozzle and the workpiece.
1) Cutting oxygen pressure:
It is influenced by the thickness of the workpiece, the type of cutting nozzle and the purity of oxygen.
When cutting thin materials, a smaller cutting nozzle and lower oxygen pressure should be selected.
Oxygen purity has a significant impact on cutting speed, gas consumption and cut quality.
2) Cutting speed:
It depends on the thickness of the piece and the shape of the cutting nozzle. As the thickness increases, the cutting speed decreases.
The cutting speed should not be too fast or too slow as this may result in excessive drag and incomplete cuts.
Cutting speed accuracy is evaluated primarily based on the amount of drag in the cut.
3) Preheating flame efficiency:
A neutral or slightly oxidizing flame is used for preheating in gas cutting, and a carburizing flame should not be used.
The efficiency of the preheating flame is expressed in terms of the fuel gas consumption rate per hour.
The efficiency of the preheating flame is related to the thickness of the part.
4) Inclination angle of cutting nozzle and workpiece:
The angle of inclination of the cutting nozzle and the workpiece is mainly determined by the thickness of the workpiece.
The angle of inclination of the cutting nozzle and the workpiece directly affects the cutting speed and drag.
A backward tilt can reduce drag and increase cutting speed.
5) Distance between the cutting nozzle and the surface of the part:
The distance between the cutting nozzle and the workpiece surface should be determined based on the length of the preheating flame and the thickness of the workpiece, generally around 3 to 5 mm.
When δ<20mm, the flame can be longer and the distance can be increased accordingly.
When δ>=20mm, the flame should be shorter and the distance can be reduced.
6) Quality requirements for gas cutting cuts:
The gas cutting surface should be smooth and clean, with consistent thick and thin lines. The iron oxide slag produced during gas cutting is easy to separate. The gas cutting gap must be narrow and consistent, and there must be no melting of the edges of the steel plate.
Criteria for evaluating and classifying cut quality:
a) Surface roughness: Surface roughness refers to the distance between the peaks and valleys of the cutting surface (average of five arbitrary points), indicated by G.
b) Flatness: Flatness refers to the level of irregularity along the cutting direction perpendicular to the cutting surface. It is calculated as a percentage of the thickness δ of the cut steel sheet, indicated by B.
c) Degree of upper edge fusion: Refers to the extent of fusion or collapse during the gas cutting process, manifested by the presence of collapsed corners and the formation of intermittent or continuous molten droplets or strips, indicated by S.
d) Slag suspension: Slag suspension refers to iron oxide adhered to the lower edge of the cutting surface. It is classified into different grades based on the amount of adhesion and the difficulty of removal, indicated by Z.
e) Maximum defect spacing: Maximum defect spacing refers to the appearance of grooves on the cutting surface along the direction of the cutting line due to vibrations or interruptions, causing a sudden decrease in surface roughness. The groove depth is between 0.32mm and 1.2mm, and the groove width does not exceed 5mm. Such grooves are considered defects. The maximum spacing between defects is indicated by Q.
f) Straightness: Straightness refers to the gap between the straight line connecting the starting and ending points along the cutting direction and the crown-shaped cutting surface. It is indicated by P.
g) Perpendicularity: Perpendicularity refers to the maximum deviation between the actual cutting surface and the line perpendicular to the surface of the metal being cut.
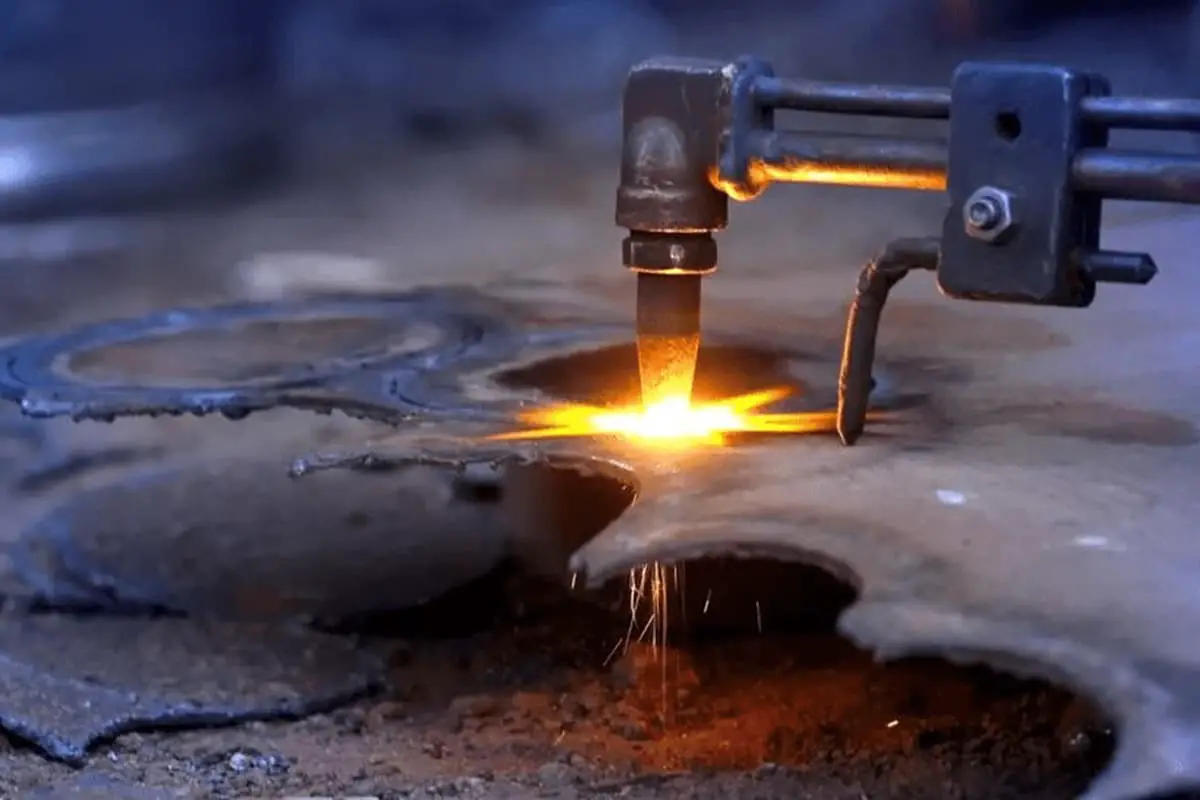
7) Causes and prevention methods of common defects:
(1) Excessive width and rough cutting surface:
This is caused by excessive oxygen pressure in the cut. When the cutting oxygen pressure is too low, the slag cannot be expelled, causing the slag to stick together and be difficult to remove.
Prevention: Adjust the cutting oxygen pressure to a level appropriate for the desired cutting width and surface roughness.
(2) Irregular surface or edge fusion:
This is caused by excessive preheating flame intensity or slow cutting speed. Insufficient intensity of the preheating flame can lead to interruptions in the cutting process and an uneven surface.
Prevention: Ensure adequate preheating flame intensity to obtain a regular and uniform cut.
(3) Excessive drag after cutting:
This occurs when the cutting speed is too fast, resulting in excessive drag and incomplete cuts. In severe cases, scum may fly upward and cause reheating.
Prevention: Adjust the cutting speed to an appropriate level to obtain a proper cut without excessive drag.
8) Ways to improve cutting surface quality:
(1) Suitable cutting oxygen pressure:
Excessive cutting oxygen pressure can result in a wider cut and a rough surface, wasting oxygen. Insufficient cutting oxygen pressure can cause slag to stick together and be difficult to remove.
Solution: Adjust the cutting oxygen pressure to a level appropriate for the desired cut quality.
(2) Suitable preheat flame intensity:
Excessive intensity of the preheating flame can lead to melting of the edges of the cutting surface, while insufficient intensity can cause interruptions in the cutting process and an uneven surface.
Solution: Ensure adequate preheat flame intensity for smooth, even cutting.
(3) Suitable cutting speed:
When the cutting speed is too fast, it can result in excessive drag, incomplete cuts, and slag flying upward, leading to reheating. When the cutting speed is too slow, the edges of the steel plate may melt, gas residue and thinner plates may suffer from excessive deformation and adhesion, making post-cut cleaning difficult.
Solution: Adjust the cutting speed to a level appropriate for the desired cutting quality.
5. Advantages and disadvantages of gas cutting
Advantages of gas cutting
1. Gas cutting is faster than other mechanical cutting methods, making it more efficient.
2. It is more economical to use oxygen-acetylene cutting to cut sections with difficult shapes and thicknesses that are challenging for mechanical cutting methods.
3. The investment in gas cutting equipment is lower compared to mechanical cutting, and the equipment is lightweight and portable, making it suitable for field operations.
4. When cutting small arcs, the cutting direction can be changed quickly. When cutting large parts, there is no need to move the part itself; only the oxygen-acetylene flame needs to be moved for fast cutting.
5. Gas cutting can be done manually or mechanically.
6. The equipment is portable and can be used on site.
7. Large metal sheets can be quickly cut on site by moving the cutting torch instead of moving the metal block.
Disadvantages of gas cutting
1. The dimensional tolerance is significantly smaller than that of mechanical cutting tools.
2. Although gas cutting can also cut metals prone to oxidation such as titanium, this process is mainly limited to cutting steel and cast iron in industrial applications.
3. The preheating flame and red-hot slag emitted pose a risk of fire and burns to operators.
4. Adequate smoke control and ventilation facilities are necessary for fuel combustion and metal oxidation.
5. Cutting high alloy steels and cast irons may require process improvements.
6. Cutting high hardness steels may require preheating before cutting and continuous heating after cutting to control the metallurgical structure and mechanical properties near the cutting edge.
7. Gas cutting is not recommended for long distance cutting over large areas.
6. Gas Cutting Applications
1. Widely used for steel plate cutting and welding chamfer preparation.
2. Suitable for cutting channel systems of castings, with cutting thicknesses of up to 300mm or more.
3. Mainly used for cutting various types of carbon steel and low alloy steel.
4. When cutting high-carbon steels and low-alloy steels with a tendency to quench, to avoid hardening or cracking on the cutting edge, it is necessary to increase the intensity of the preheating flame and decrease the cutting speed, or even pre-heat. Heat the material steel before cutting.