Introduction
Brief overview of plasma cutting
Plasma arc cutting is a machining method that uses the heat from a high-temperature plasma arc to locally melt (and evaporate) the metal at the cutting edge and uses the momentum of the high-speed plasma to remove the molten metal to form a cut.
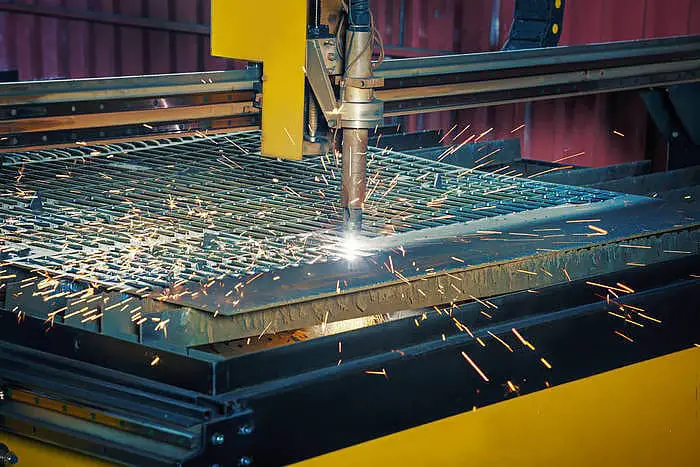
Advantages of plasma cutting over traditional cutting methods
CNC plasma cutting machines have improved cutting speed and range compared to flame cutting.
Compared with traditional cutting methods, plasma cutting has advantages such as high efficiency, high precision and high stability, especially for large-scale production and processing with high precision cutting requirements.
From a cost perspective, plasma cutting is more economical due to the elimination of cutting gas expenses.
Its control of processing costs will be more evident, especially when applied to large-scale production.
Plasma arc cutting is a relatively ideal cutting heat source, with the following advantages:
(1) Wide range of applications.
Plasma arcs can cut various metals with a melting point that other cutting methods cannot cut, such as stainless steel, heat-resistant steel, titanium, molybdenum, tungsten, cast iron, copper, aluminum and aluminum alloys, with a cutting thickness of more than 200 mm for stainless steel and aluminum, etc.
(2) Fast cutting speed and high productivity.
Among the various cutting methods currently used, plasma arc cutting is relatively fast and has high production efficiency.
For example, cutting 10mm aluminum plate, the cutting speed can reach 200-300m/h; cutting 12mm thick stainless steel, the cutting speed can reach 100-130m/h.
(3) High cutting quality.
During plasma arc cutting, narrow, smooth, perfect and residue-free cuts can be obtained, close to vertical, with minimal deformation and influence of heat on the cuts, and little change in hardness. The cut quality is good.
Understanding Plasma Cutters
Definition and basic principles of plasma cutting
Definition
Plasma arc cutting uses a mixture of gases passed through a high-frequency arc. The gas can be air or a mixture of hydrogen, argon and nitrogen.
The high-frequency arc causes some of the gas to “decompose” or ionize into basic atomic particles, resulting in “plasma.”
The arc then jumps to the stainless steel workpiece and the high-pressure gas blows the plasma out of the cutting torch nozzle with an exit velocity of 800 to 1000 meters per second (about mach 3).
This, combined with the high energy released when the various gases in the plasma return to their normal state, generates a high temperature of 2700°C.
This temperature is almost twice the melting point of stainless steel. This causes the stainless steel to melt quickly and the molten metal is expelled by the high-pressure gas flow.
Therefore, exhaust and slag removal equipment is required.

1- Plasma arc, arc length 6.4 mm, nozzle opening 0.76 mm
2-white tungsten arc, arc length 1.2 mm, tungsten electrode diameter 1 mm
Plasma arc cutting (plasma arc cutting) can be used to cut stainless steel with a thickness of 3.0 to 80.0 mm.
The cutting surface is oxidized and, due to the characteristics of the plasma, the cut has the shape of a figure eight.
Working principle
Plasma arc cutting is a thermal cutting method that uses plasma arc as a heat source and melts and removes molten metal to form a high-speed thermal ionic gas cut.
The working principle of plasma arc cutting is similar to that of plasma arc welding, but the power source has more than 150 volts of no-load voltage, and the arc voltage is also more than 100 volts.
The structure of the cutting torch is also larger than that of the welding torch and requires water cooling.
Plasma arc cutting generally uses high-purity nitrogen as the plasma gas, but mixed gases such as argon or argon-nitrogen or argon-hydrogen can also be used.
Generally, no shielding gas is used, and sometimes carbon dioxide can also be used as a shielding gas.
Classification
There are three types of plasma arc cutting:
Small current plasma arc cutting uses 70 to 100 amps of current, the arc belongs to a non-transfer arc, and is used for manual cutting of 5 to 25 mm thin sheets or for machining such as slotted castings and punching;
Large current plasma arc cutting uses 100 to 200 amps or more of current, the arc belongs to a transfer arc (see plasma arc welding) and is used for mechanical cutting of large thickness material (12 to 130 mm ) or modeling cut;
Waterjet plasma arc cutting uses large current, the outer jacket of the cutting torch has a ring-shaped waterjet nozzle, and the sprayed water can reduce the smoke and noise generated during cutting and improve the quality of the cut.
The plasma arc can cut stainless steel, high alloy steel, cast iron, aluminum and its alloys, as well as non-metallic materials such as ore, cement board, ceramics, etc.
Plasma arc cuts are narrow, smooth and flat, and the quality is similar to precision gas cutting.
Under the same conditions, the cutting speed of plasma arc is faster than that of gas cutting, and the range of cutting materials is also wider than that of gas cutting.
Plasma arc cutting parameters.
The selection of plasma arc cutting parameters is crucial to the quality, speed and efficiency of the cut.
1. Cutting current
The cutting current is the most important cutting parameter, which directly determines the thickness and cutting speed, i.e. the cutting capacity.
As the cutting current increases, the arc energy increases, the cutting capacity improves, the cutting speed is faster, the arc diameter increases, and the arc becomes thicker, causing the cut to become wider.
If the cutting current is too high, the thermal load on the nozzle increases, the nozzle is damaged too early and the cutting quality naturally decreases or even normal cutting is not possible.
Therefore, it is necessary to select the cutting current and corresponding nozzle based on the thickness of the material before cutting.
2. Cutting speed
Due to different thicknesses, materials, melting points, thermal conductivity and surface tension after material melting, the selected cutting speed is also different.
Moderately increasing the cutting speed can improve the cutting quality, that is, the cut is slightly narrower, the cutting surface is smoother, and the deformation is reduced.
If the cutting speed is too fast, the heat input during cutting is less than the required quantity, the cutting jet cannot blow the melt immediately, forming a larger residual quantity, accompanied by cutting slag, and the quality of the cutting surface decreases.
3. Arc Voltage
Plasma arc cutting machines generally have high no-load voltage and working voltage.
When using ionizing gases such as nitrogen, hydrogen or air, the voltage required to stabilize the plasma arc will be higher.
When the current is fixed, the increase in voltage means that the enthalpy of the arc increases, the jet diameter decreases and the gas flow rate increases, resulting in faster cutting speed and better cutting quality.
The no-load voltage is 120-600V, the arc column voltage cannot exceed 65% of the no-load voltage, and is generally half of the no-load voltage.
At present, the no-load voltage of plasma arc cutting machines on the market is generally 80-100V.
Main components of a plasma cutter
A plasma cutting machine is an industrial cutting equipment made up of the following main parts:
1. Cross beam: The cross beam is an important part of the plasma cutting machine for balancing and cross cutting. It is part of the machine body and moves horizontally to perform cutting work.
2. Base: The base is located on the guide rail and under the crosspiece, with wheels at the bottom. It is mainly used for the longitudinal movement and cutting action of the machine.
3. Lifting body: This part is located near the torch and on the crossbar. It is mainly used for the up and down movement of the torch to process plates of different thickness.
4. Control system: It is the command center of the CNC plasma cutting machine. It is mainly used to set the operating trajectory and related parameters of the machine.
5. Work table: Also known as a basic cutting table. It is a necessary device for the CNC cutting machine during operation. It is mainly used to place plate material and cool it during machine operation.
6. Plasma power supply: Provides power to the plasma cutting machine and is the main accessory of the machine.
Types of Plasma Cutters
CNC plasma cutting machines can be classified based on operation mode into dry plasma, semi-dry plasma and underwater plasma.
Based on the cutting quality, they can be classified into general plasma, fine plasma and laser-like plasma.
Safety Precautions
1. Check and confirm that the power source, gas source and water source are free from electrical leaks, gas leaks, water leaks and are safely grounded or zero connected.
2. The carriage and the workpiece must be located in the appropriate position, and the positive pole of the workpiece and the cutting circuit must be connected, and a slag pit must be provided under the cutting work surface.
3. Select the nozzle opening based on the workpiece material, type and thickness, and adjust the cutting energy source, gas flow and electrode contraction.
4. The automatic cutting carriage must be empty and the cutting speed must be selected.
5. Operators must wear protective masks, electric welding gloves, hats, filter mask respirators, and noise-cancelling ear protectors. People who do not wear protective glasses are strictly prohibited from directly observing the plasma arcs, and bare skin is strictly prohibited from approaching the plasma arcs.
6. When cutting, the operator must be positioned against the wind to operate. Air can be removed from the bottom of the worktable and the open area on the worktable should be reduced.
7. When cutting, if the no-load voltage is too high, check the electrical grounding, zeroing and insulation of the torch lead, isolate the work table from the ground, or install a no-load circuit breaker in the electrical control system.
8. The high frequency generator must have a shielding cover. After the high-frequency arc starts, the high-frequency circuit must be cut off immediately.
9. The use of thorium and tungsten electrodes must comply with the regulations established in Article 12.7.8 of JGJ33-2001.
10. Cutting operation personnel and support personnel must wear labor protection equipment as required. They must also take measures to prevent electric shocks, falls from high altitudes, gas poisoning, fire and other accidents.
11. The welding machine used on site must have a shed for protection against rain, moisture and sun protection, and must be equipped with corresponding fire-fighting equipment.
12. When welding or cutting at height, safety belts must be worn and fire prevention measures must be taken around and below the welding or cutting area, and there must be someone to supervise.
13. When welding or cutting pressure vessels, sealed containers, oil drums, pipelines or parts contaminated with flammable gas or solution, the pressure in the vessel or pipeline must be eliminated first and the flammable gas or solution must be removed.
Then the toxic, harmful and flammable substances must be rinsed off.
For containers with residual grease, steam or alkaline water should be used to rinse, and the lid should be opened to ensure that the container is clean, and then filled with clean water before welding.
Measures must be taken to avoid electric shock, poisoning and asphyxiation when welding or cutting inside containers.
Welding or cutting in sealed containers must have air holes and, if necessary, ventilation equipment must be installed at the air inlet and outlet holes.
The lighting voltage inside the container must not exceed 12V, and the welder and workpiece must be isolated. Someone must be appointed to supervise outside the container.
Welding inside containers painted or coated with oil or plastic is strictly prohibited.
14. Welding and cutting must not be carried out on pressurized containers and piping, electrically charged equipment, stressed parts of load-bearing structures, or containers containing flammable and explosive items.
15. No outdoor welding is permitted during rainy weather. When working in damp areas, the operator must step on insulating materials and wear insulated shoes.
16. After work, the power supply must be turned off and the gas and water sources closed.
Setting Up Your Plasma Cutter
Parameters on a CNC plasma cutting machine can be set. See how:
Arc start time: Also known as piercing time, it is usually entered directly from the keyboard.
Cutting speed and cutting compensation: Generally entered directly from the keyboard.
Arc height: Also known as piercing height, it is usually manually adjusted on the cutting gun.
Arc voltage: Generally adjusted manually on the arc voltage sensor.
As for how to operate a CNC plasma cutting machine, the specific answer is:
(1) Start the air compressor, followed by the machine control cabinet and plasma power source, then set the corresponding parameters, and finally start the program to start cutting work.
Please note that the order should not be reversed to avoid problems.
(2) Cutting steel plate and process parameters must be set reasonably and effectively.
(3) After cutting, immediately turn off the power and gas source.
Techniques for Effective Plasma Cutting
When using a CNC plasma cutting machine, if the cutting quality is unstable and the wearing parts need to be replaced frequently, it is often found that the user's operation of the CNC plasma cutting machine is not standardized enough and not enough attention is paid to some details.
Here are some tips for daily use of CNC plasma cutting machines to bring you convenience:
1. Start cutting from the edge
Start cutting from the edge as far as possible rather than piercing the cut. Using the edge as a starting point will extend the life of the wear parts. The correct method is to align the nozzle directly with the edge of the part and then start the plasma arc.
2. Reduce unnecessary “ignition (or pilot) time”
Ignition consumes the nozzle and electrode very quickly. Before beginning, the torch must be placed within cutting distance of the metal.
3. Don't overload the nozzle
Overloading the nozzle (i.e. exceeding the nozzle's working current) will cause the nozzle to fail quickly.
The current intensity must be 95% of the nozzle working current. For example, the current intensity of a 100A nozzle should be set to 95A.
4. Use a reasonable cutting distance
According to the instructions, use a reasonable cutting distance, which is the distance between the cutting nozzle and the surface of the workpiece. When punching, try to use 2 times the normal cutting distance or the maximum height that the plasma arc can transfer.
5. The perforation thickness must be within the allowable range of the machine system
The cutting machine cannot pierce a steel plate that exceeds the working thickness. Typical punching thickness is 1/2 of normal cutting thickness.
Keep the torch and wear parts clean; Any dirt on the torch and wear parts will greatly affect the performance of the plasma system.
When replacing wear parts, place them on a clean cloth and frequently check the torch connection, clean the electrode contact surface and nozzle with cleaning agents such as hydrogen peroxide.
Troubleshooting Common Plasma Cutting Problems
Index. | Lack | Failure causes | The method to eliminate the problem. |
1 | Turning on the power button. | 1. The fuse in the power supply switch is broken. | To replace. |
The power indicator light does not light up after turning on the power button. | 2. The fuse in the power box has blown. | Check and replace. | |
3. The control transformer is bad. | To replace | ||
4. The power switch is damaged. | To replace | ||
5.The indicator light is defective. | To replace | ||
two | It was not possible to pre-adjust the cutting gas pressure. | 1.The air source is not connected or there is no air in the air source. | Turn on the air source. |
2. The power switch is not in the “on” position. | To connect. | ||
3. The pressure reducing valve is damaged. | Repair or replace. | ||
4. The wiring of the electromagnetic valve is poor. | Check the wiring | ||
5.The electromagnetic valve is broken. | To replace | ||
3 | When pressing the cutting torch button during operation, there is no gas flow. | 1.Pipe leak. | Repair the leaking part. |
2. An electromagnetic valve is damaged. | To replace | ||
4 | The work indicator light turns on after pressing the cutting torch button, but the plasma arc is not lit even though the conductive nozzle is in contact with the workpiece. | 1.KT1wrong | To replace |
2. The high frequency transformer is damaged. | Check or replace. | ||
3. Ignition rod surface oxidation or inadequate clearance distance. | Polish or adjust. | ||
4. Short circuit of high-frequency capacitor C7. | To replace | ||
5. Air pressure is too high | Lowering | ||
6. The loss of the conductive nozzle is very short | to replace | ||
7. Open circuit or short circuit of the rectifier element of the rectifier bridge | Check and replace it | ||
8. Poor contact or open circuit in the cutting torch cable | Repair or replace | ||
9. The workpiece ground wire is not connected to the workpiece | Connected to the workpiece | ||
10. There is a thick layer of paint or dirt on the surface of the workpiece | Clean and make conductive | ||
5 | The cutting indicator light does not light up when the conductive nozzle is in contact with the workpiece and the cutting button is pressed. | 1. Thermal control switch action | Wait for it to cool down or work again |
2. Cutting torch button switch is damaged | to replace | ||
6 | Check the fuse tripping after high frequency starting. | 1. Damaged high frequency transformer | Check and replace |
2. Damaged control transformer | Check and replace | ||
3. Contactor coil short circuit | to replace | ||
7 | The main power switch fuse has melted. | 1. Short circuit of the rectifier element | Check and replace |
2 Main transformer failure | Check and replace | ||
3. Contactor coil short circuit | Check and replace | ||
8 | High frequency occurs, but no arc is generated. | 1. The rectifier component is defective (there is an abnormal sound inside the machine) | Check and replace |
2. The main transformer is damaged | Check and replace | ||
3. C1-C7 down | Check and replace | ||
9 | Long-term work without arc ignition. | 1. Main transformer temperature is too high and thermal control switch is activated | Wait until it cools down before working. Pay attention to whether the cooling fan is working and the wind direction |
1. Damaged high frequency transformer | Check and repair |
Maintenance and care of your plasma cutter
1. Proper torch installation
Install the torch properly and carefully, ensuring that all parts are securely fitted and that the flow of cooling gas and air is smooth. Install all parts on a clean cloth to prevent dirt from sticking to the parts. Apply appropriate lubricating oil to the O-ring until it shines, but do not add too much.
2. Replace consumables before they are completely damaged
Do not wait until consumables are completely damaged before replacing them, as severely worn electrodes, nozzles, and rotational rings will produce uncontrollable plasma arcs that are likely to cause serious damage to the torch. Therefore, when you notice the first drop in cutting quality, immediately check the consumables.
3. Clean the torch connection threads
When replacing consumables or performing daily maintenance checks, be sure to keep the internal and external threads of the torch clean. If necessary, clean or repair the connection threads.
4. Clean the electrode and nozzle contact surfaces
In many torches, the contact surface between the nozzle and the electrode is a charged contact surface. If these contact surfaces are dirty, the torch will not function properly and must be cleaned with peroxide-based cleaners.
5. Check gas and refrigerant flow and pressure daily
Check gas and refrigerant flow and pressure daily. If insufficient flow or leaks are found, stop the machine immediately to eliminate the fault.
6. Prevent torch collision damage
To prevent collision damage to the torch, program the system correctly to prevent excessive movement and install collision protection devices that effectively prevent damage to the torch during collisions.
7. The most common causes of torch damage
(1) Torch collision.
(2) Destructive plasma arc caused by damaged consumables.
(3) Destructive plasma arc caused by dirt.
(4) Destructive plasma arc caused by loose parts.
8. Precautions
(1) Do not apply grease to the torch.
(2) Do not overuse the O-ring lubricant.
(3) Do not spray anti-splash chemicals while the protective cover is still on the torch.
(4) Do not use the hand torch as a hammer.
Conclusion
This article presents the scientific principles and methods of using plasma cutters. As long as you follow safety equipment and preventive measures, using a plasma cutter is very easy.
Plasma cutters can help you save time and money and are a versatile, easy-to-use machine with many options available on the market.