1. Understanding Screws
Screw definition: Type of fastener composed of two parts, a head and a screw (cylinder with external thread).
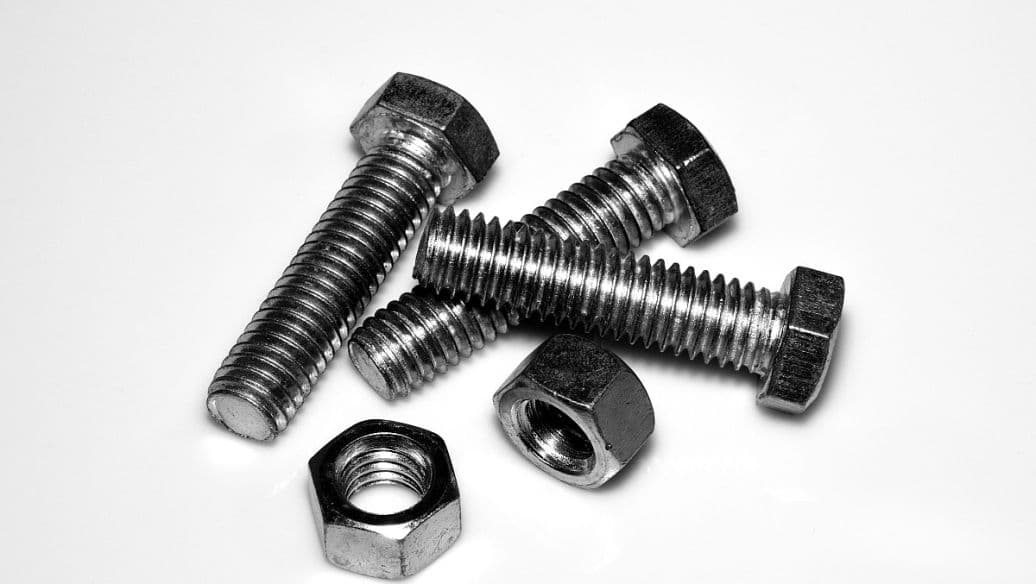
Screw classification:
Head shape: Hexagonal head, round head, square head, countersunk head, etc.
Line Length: Full Wire and Half Wire;
Thread tooth shape: triangle, trapezoid, tube shape, etc.
Line direction: right and left.
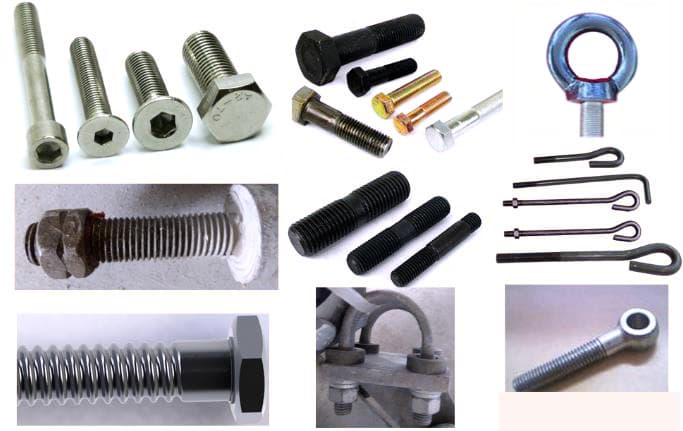
Screw Specifications: (GB/T1237)
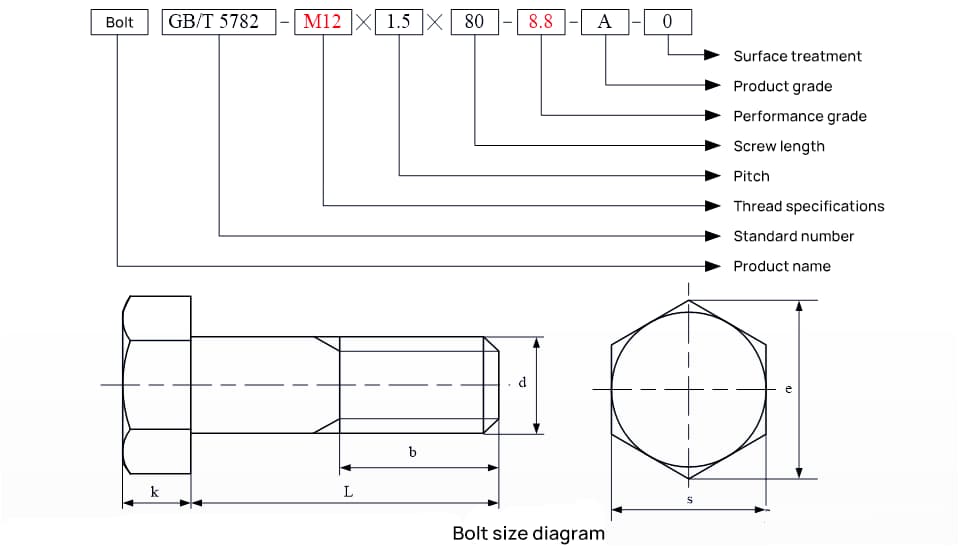
The thread specifications of the screws determine the specifications of the wrench used (GB/T4388)
Thread diameter d/mm |
Opposite dimension s/mm |
Key size S/mm |
Thread diameter d/mm |
Opposite dimension s/mm |
Key size S/mm |
M5 | 8 | 8 | M18 | 27 | 27 |
M6 | 10 | 10 | M20 | 30 | 30 |
M8 | 13 | 13/14 | M22 | 32 | 32 |
M10 | 17 | 16/17 | M24 | 36 | 36 |
M12 | 19 | 18/19 | M27 | 41 | 41 |
M14 | 22 | 22 | M30 | 46 | 46 |
M16 | 24 | 24 | M36 | 55 | 55 |
Bolt performance grades (GB/T3098.1-2010)
A bolt's performance grade designation is printed on its head and is usually represented by X and Y.
X100 represents the nominal value of the tensile strength of the screw material, in units of MPa.
X100 * (Y/10) represents the value of the screw's yield strength, in units of MPa.
There are more than 10 performance grades, including 3.6, 4.6, 4.8, 5.6, 6.8, 8.8, 9.8, 10.9 and 12.9.
High-strength bolts refer to bolts with performance grades of 8.8 or higher, made from low-carbon alloy steel or medium-carbon steel and heat treated (quenched and tempered).
Ordinary screws, also known as common screws, can be divided into refined screws (grades A and B: 5.6 or 8.8) and raw screws (grade C), with performance grades generally 4.6 or 4, 8.

2. Screw connection principles
Bolted connection refers to the use of bolts and nuts to secure the connection of two components with through holes and is a detachable connection.
Types of bolted connections can be divided based on the fit between the bolt and the through hole:
Common screw connection: There is a gap between the hole and the rod after assembly, the structure is simple, assembly and disassembly are convenient, it can be assembled and disassembled multiple times, and is widely used.
Screw connection with hinged hole: There is no play after assembly, mainly supporting lateral loads, and can also be used for positioning.
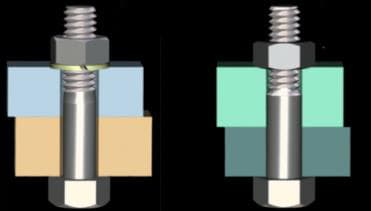
Screw connection working principle
Hooke's Law: When a solid material is subjected to stress, there is a linear relationship between the stress and the strain (unit strain) in the material.

Shear and tensile analysis of screw connections (I)
Shear Bolt Connection: Transmits energy through mutual compression of the bolt shank and hole wall.
Tension bolt connection: It mainly depends on the pre-tension of the bolt after tightening.
When the connected component has a high stiffness and the screws are arranged symmetrically, each screw will withstand the average stress in the connection.
When the connected component has a small stiffness, the connecting flange will bend and deform, generating leverage.
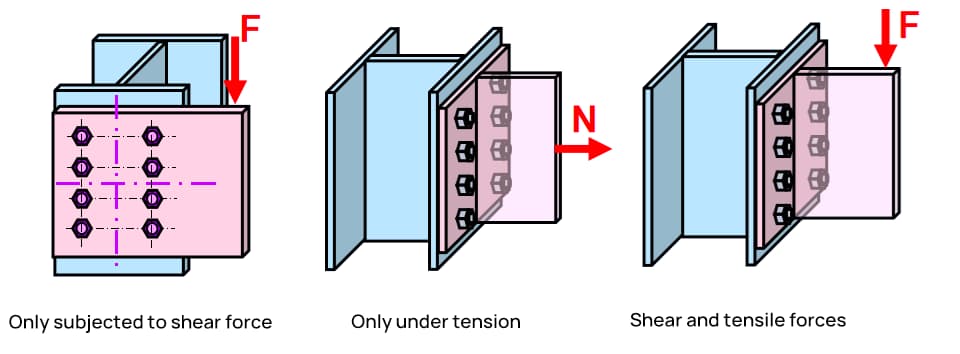
Shear and tensile analysis of screw connections (II)
In addition to shear and tension, bolted connections can also be subject to: vibration, temperature, lateral stresses (wind, flow, pressure, etc.), changes in loads and other forces.
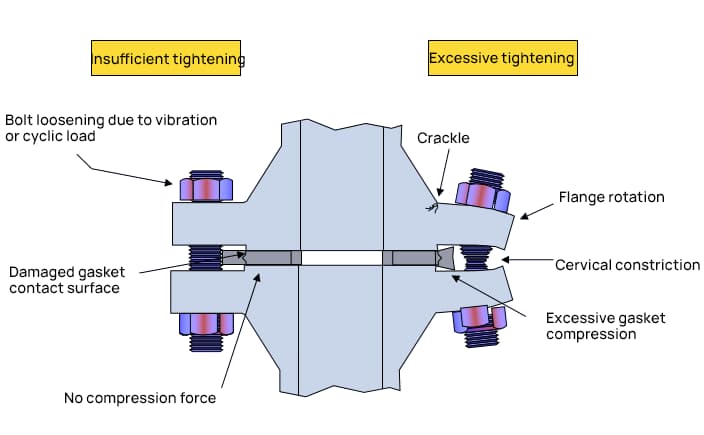
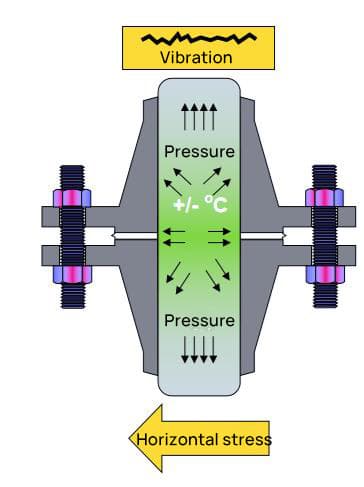
There are three methods of tightening screws:
Torque tightening method: The principle is that there is a certain relationship between the size of the torque and the pre-tightening axial force. This tightening method is simple and intuitive to operate and is widely used today.
Angular tightening method: The rotation angle is proportional to the sum of the screw extension and the looseness of the tightened component. Therefore, the method of rotating the screw at the specified angle to achieve the desired clamping force can be adopted.
Yield point tightening method: The theoretical objective is to tighten the screw just after the yield point.
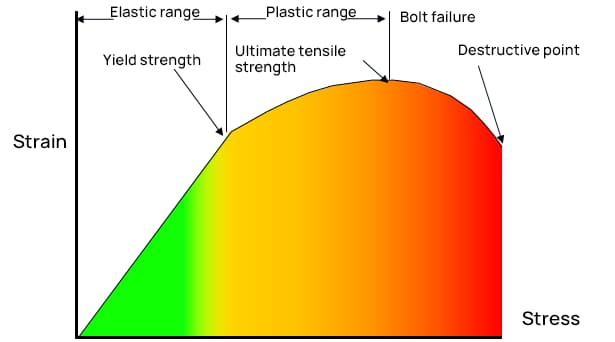
3. Screw tightening methods
Torque tightening method
Apply pre-tightening force to the fastener by turning the nut portion of the fastener
The applied torque follows the 5-4-1 rule.
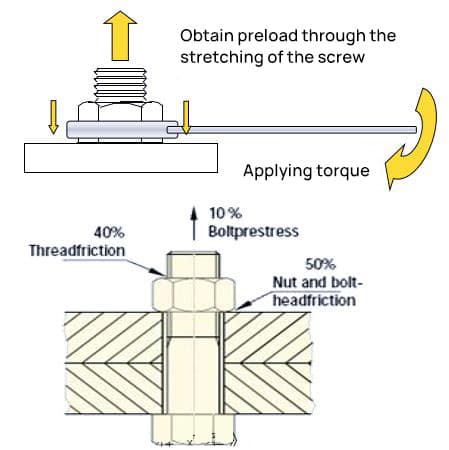
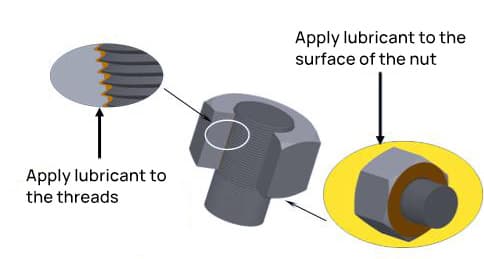
Lubrication only at the end of the screw/screw clamping part.
Screw head friction | Thread friction | Preload | |
General situation | 50% | 40% | 10% |
Screw head lubrication | 45% | 40% | 15% |
Thread lubrication | 50% | 30% | 20% |
Defective thread | 50% | 45% | 5% |
Principle of screw tightening sequence
Press in sequence starting from the middle, then on both sides, then diagonally and finally clockwise in stages.
Generally divided into two tightening stages: in the first stage, tighten with a torque of around 50% and in the second stage, tighten with a torque of 100%.
The end of the screw should protrude 1-3 steps beyond the nut.
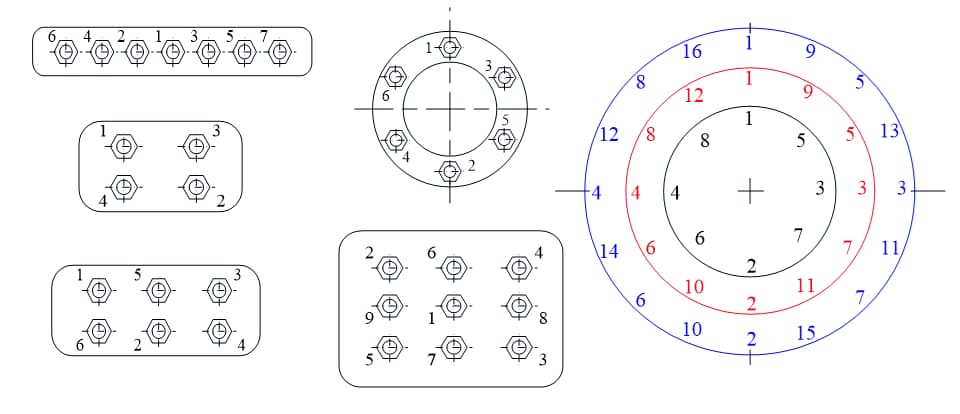
4. Matters needing attention when using screws
1. Before preparing the screw assembly it is necessary:
Check that the screw and nut are clean, free of rust and free of burrs and protrusions.
Check the contact plane between the connected part and the screw and nut and make sure it is perpendicular to the screw hole.
Also, check the tightness of the screw and nut.
2. When assembling the nut and flat washer, the nut and washer must be assembled with the back side facing the connected part.
The side of the nut marked with characters is the front side and the smooth side of the washer is the front side.
3. Force operation guidelines (for reference only):
d/mm screw specification | Applied torque M/Nm | Operational Fundamentals | d/mm screw specification | Applied torque M/Nm | Operational Fundamentals | |
M6 | 3.5 | Just wrist strength | M16 | 71 | Increase overall strength | |
M8 | 8.3 | Add wrist strength, elbow strength | M20 | 137 | total body weight | |
M10 | 16.4 | Increase overall strength | M24 | 235 | Add total body weight | |
M12 | 28.4 | Add half-body strength | / | / | / |
4. The key to preventing screw loosening in screw connections lies in avoiding relative rotation of the screw threads. There are three common methods of loosening screws:
Anti-loosening by friction
- Anti-loosening pressure washer
- Anti-loosening double nut
- Anti-loosening self-locking nut
Mechanical anti-loosening
- Anti-loosening cotter pin
- Anti-loosening pressure washer
Permanent anti-loosening
- Staking anti-loosening
- Anti-loosening adhesive
5. Common screw removal problems
When loosening flange bolts on pipes and valves:
Loosen half of the body screws first to allow any remaining oil, steam or water to discharge from the opposite side to avoid splashing or burning.
In the case of glued screws that cannot be loosened:
Most glue is an organic solution and can be soaked in banana oil or alcohol for half an hour, or covered with alcohol cotton on the screw. The longer the time, the more the glue will dissolve.
In the case of rusty screws that cannot be loosened:
Spray WD-40 and wait half an hour. The spray will penetrate the screw to dissolve the rust.
Other methods: vibration, lubrication, roasting, drilling
In the case of sliding screws that cannot be loosened:
Corrosive solutions such as dilute acid or hydrochloric acid can slowly corrode the screw.
Use acid for metal and alkali for plastic.
6. Common misconceptions in using screws
Thick instead of thin:
Some important joints, such as drive shafts and flywheels, use fine-thread screws.
Fine thread screws have a smaller pitch and angle and have advantages such as high strength and good self-locking performance. They have strong ability to withstand impacts, vibrations and shifting loads.
If coarse thread screws are used instead of fine thread screws, they may become loose or loose and cause accidents.
Incorrect adjustment:
Bolts that support transverse loads and shear forces (such as driveshaft bolts and flywheel bolts) have transitional fits with the bolt holes. The assembly must be solid and reliable and capable of withstanding lateral forces.
If not checked during assembly, there may still be large gaps between the screw and the screw hole, resulting in loose screws or cutting accidents.
Thicker Nuts:
Incorrect point of view: Thicker nuts can increase the number of working turns of the thread and improve the reliability of the joints.
In fact, the thicker the nut, the more uneven the load distribution will be between each turn of the thread, making the joint easier to loosen.
A nut with several washers:
Sometimes the assembled screws are too long, so some people put too many lock washers on one screw.
During the tightening process, the lock washers are subjected to unequal forces and some may break, reducing the pre-tightening force of the bolt.
Or generate eccentric loads, reducing the reliability of the bolted connection.
The washer is too large: (GB/T97.1-2002 Table 1, M5 to M36: the inner diameter of the washer is larger than the thread diameter by 0.3 mm to 1 mm)
Incorrect practice: Due to lack of suitable washers, a washer with a larger internal diameter is used as a substitute.
This results in a decrease in contact between the bottom of the screw head and the washer, leading to a decrease in the pressure bearing capacity or locking force of the washer. Under the influence of vibrations and impact loads, the screw tends to loosen.
The torque is not up to par:
Incorrect view: The belief that screws should be “tight but not loose” leads to an intentional increase in tightening torque.
Consequences: This results in the screw slipping or even breaking.
Incorrect practice: For important screws that need to be torqued, there is a tendency to use a manual wrench to save time.
Consequences: Screws loosen due to insufficient torque, leading to failure.
Inadequate locking: Important screws must be secured with anti-loosening devices after assembly.
When using split pin locking, a common mistake is to use too thin a split pin or half a split pin.
When using lock washer locking, a common mistake is that the washer opening is too small and loses its elasticity.
When using a lock washer, a common mistake is jamming the washer into the edge of the nut.
When using double nuts, a common mistake is using a thin nut on the outside and not tightening it.
False fortification:
The threads of screws, nuts or holes have rust stains, scales, iron chips, sand particles, burrs, etc.
Before assembly, they must be cleaned. During screw tightening, due to the blocking effect of impurities, the surface torque value reaches the requirement, but in fact, the connecting parts are not actually fixed.