And carbon effect on steel
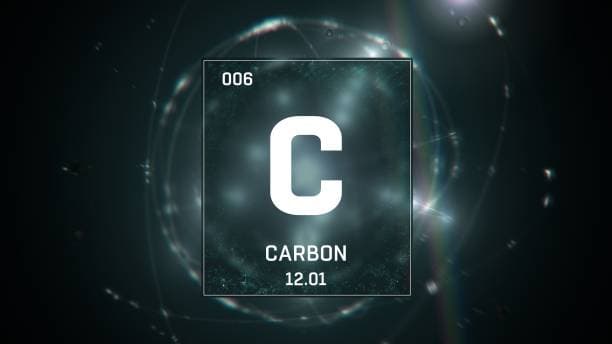
The role of carbon in steel is a delicate balance. On the one hand, as the carbon content increases, the yield strength and tensile strength of steel increase, but on the other hand, its plasticity and impact resistance decrease.
As a result, the carbon content must be adapted to the intended use of the steel. When the carbon content exceeds 0.23%, welding performance deteriorates significantly, which is why the carbon content of low-alloy structural steel used for welding should not exceed 0.20%.
Additionally, excessive carbon content reduces the steel's resistance to atmospheric corrosion, making high-carbon steel in outdoor environments vulnerable to corrosion.
However, high carbon content is not entirely negative, as it can also improve the steel's cold brittleness and aging sensitivity.
And silicon effect on steel

Silicon is added as a reducing agent and deoxidizing agent during the steelmaking process, resulting in steel that contains 0.15-0.30% silicon. When the silicon content exceeds 0.50-0.60%, it is considered an alloying element.
Silicon can significantly increase the yield strength, yield strength and tensile strength of steel, and is therefore widely used in spring steels such as 65Mn and 82B, which contain 0.15-0.37% silicon.
Adding 1.0-1.2% silicon to quenched and tempered structural steel can increase its strength by 15-20%.
Additionally, when combined with elements such as molybdenum, tungsten and chromium, silicon improves the corrosion and oxidation resistance of steel and is used to produce heat-resistant steel.
Low carbon steel containing 1.0-4.0% silicon has extremely high magnetic permeability and is used to manufacture silicon steel sheets in the electrical industry.
However, silicon has the disadvantage of reducing the welding performance of steel.
And the effect of manganese on steel

During the steelmaking process, manganese acts as a good deoxidizer and desulfurizer, and steel typically contains 0.30-0.50% manganese.
If more than 0.70% manganese is added to carbon steel, it is considered “manganese steel”.
This type of steel not only has adequate toughness, but also greater strength and hardness than normal steel. Manganese improves the hardenability and hot workability of steel; for example, the yield strength of 16Mn steel is 40% higher than that of A3 steel.
Steel containing 11-14% manganese has extremely high wear resistance and is used in applications such as excavator buckets and ball mill linings. However, the high manganese content also has disadvantages.
When the manganese content is high, the steel is more prone to brittleness upon tempering. Manganese promotes grain growth, which must be taken into account during heat treatment. When the mass fraction of manganese exceeds 1%, the welding performance of steel decreases.
And the effect of sulfur on steel
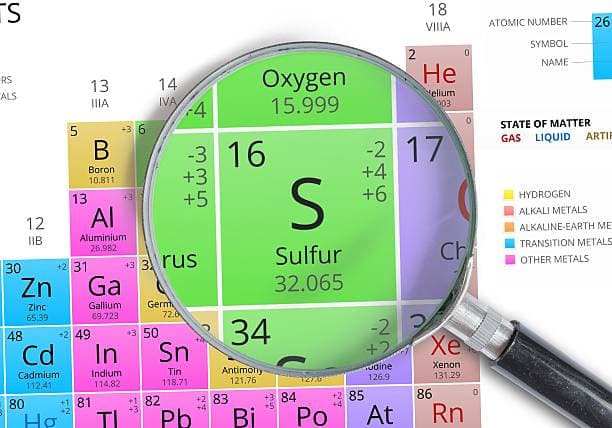
Sulfur is a harmful element in steel from steel ore and fuel coke. In steel, sulfur exists in the form of FeS and forms compounds with Fe that have a low melting point (985°C), while the hot working temperature of steel is typically 1150-1200°C.
As a result, during hot working, the FeS compound melts prematurely, causing the part to crack, a phenomenon known as “hot brittleness.” The higher the sulfur content, the more severe the hot brittleness will be, so the sulfur content must be controlled.
For high-quality steel, the sulfur content is less than 0.02-0.03%; for quality steel it is less than 0.03-0.045%; and for common steel, it is less than 0.055-0.07%. In some cases, sulfur is added to the steel.
For example, adding 0.08-0.20% sulfur to steel can improve its workability in cutting, resulting in what is known as free-cutting steel.
However, sulfur also has negative effects on welding performance and can reduce corrosion resistance.
And effect of p phosphorus on steel
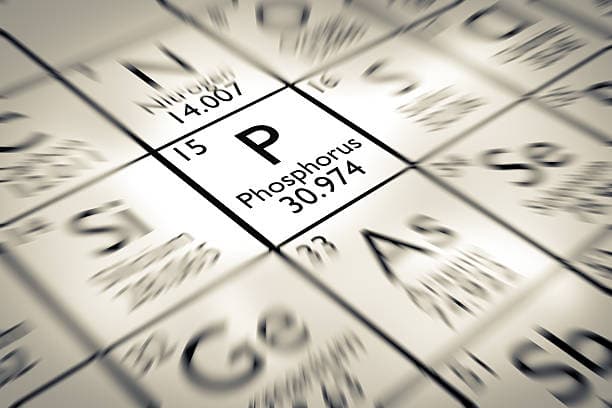
Phosphorus is introduced into the steel through the ore. Generally speaking, phosphorus is a harmful element for steel. Although it can increase the strength and hardness of steel, it greatly reduces its plasticity and impact resistance.
At low temperatures, phosphorus makes steel significantly brittle, a phenomenon known as “cold brittleness,” which deteriorates its cold working and weldability.
The higher the phosphorus content, the more severe the cold brittleness, so the control of the phosphorus content in steel is strict.
High-quality steel has a phosphorus content of less than 0.025%, quality steel has a phosphorus content of less than 0.04%, and ordinary steel has a phosphorus content of less than 0.085%.
And the effect of oxygen on steel

Oxygen is a harmful element in steel that naturally enters the steel manufacturing process. Despite the addition of manganese, silicon, iron and aluminum for deoxidation at the end of the steelmaking process, it is not possible to remove all the oxygen.
Oxygen appears in steel as FeO, MnO, SiO2, Al2O3 and other inclusions, which reduce the strength and plasticity of the steel. In particular, it has a significant impact on fatigue resistance and impact resistance.
And effect of n nitrogen on steel

Ferrite has a low capacity to dissolve nitrogen. When nitrogen is supersaturated in steel, it will precipitate in the form of nitrides after a long period of time or after heating to 200-300°C, increasing the hardness and strength of the steel, but reducing its plasticity and causing aging.
To eliminate the aging tendency, Al, Ti or V can be added to the molten steel for nitrogen fixation treatment, which fixes nitrogen in the form of AlN, TiN or VN.
And chrome effect on steel

Chromium greatly increases the strength, hardness and wear resistance of structural steel and tool steel, providing the steel with good resistance to oxidation and corrosion.
As a result, chromium is an important alloying element for stainless steel and heat-resistant steel. Chromium also improves the hardenability of steel and is a crucial alloying element.
However, chromium also increases the brittle transition temperature of steel, increases its brittleness upon tempering, and can cause difficulties in the processing process.
And Nickel effect on steel

Nickel increases the strength of steel, preserving good plasticity and toughness. It has high resistance to acid and alkali corrosion and is resistant to rust and heat at high temperatures. However, because nickel is a scarce resource, other alloying elements are often used instead of nickel-chromium steel.
And effect of olybdenum on steel

Molybdenum refines the grain structure of steel, improves hardenability and hot strength, and maintains sufficient strength and creep resistance at high temperatures (when deformation occurs under long-term stress at high temperatures).
When added to structural steel, molybdenum improves its mechanical properties and also reduces the brittleness of the steel alloy due to fire. Additionally, when added to tool steel, molybdenum improves its red hardness.
And titanium effect on steel
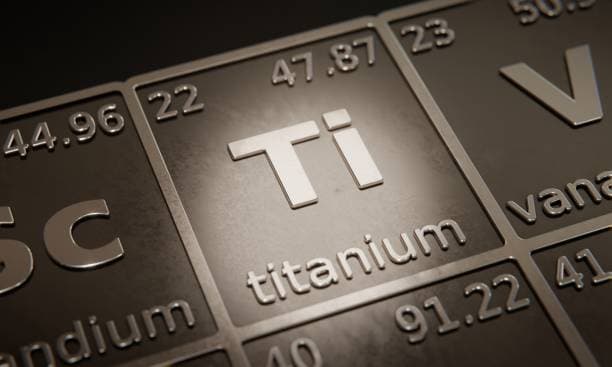
Titanium is a strong steel deoxidizer. It makes the steel's internal structure denser, refines its grain structure, reduces aging sensitivity and cold brittleness, and improves welding performance. Adding appropriate amount of titanium to Cr18Ni9 austenitic stainless steel can prevent intergranular corrosion.
E effect of v anadium on steel

Vanadium is an excellent steel deoxidizer. By adding 0.5% vanadium to steel, the grain structure is refined and strength and toughness are improved. Carbides formed by combining vanadium and carbon increase resistance to hydrogen corrosion under high temperature and pressure.
And tungsten effect on steel

Tungsten has a high melting point and high density, making it a crucial alloying element. Carbides formed from tungsten and carbon have high hardness and wear resistance. Adding tungsten to tool steel significantly improves its red hardness and heat resistance, making it suitable for use as cutting tools and forging dies.
And effect of n iobium on steel

Niobium refines the grain structure of steel and reduces its sensitivity to overheating and temper brittleness, while improving its strength but decreasing its plasticity and toughness.
The addition of niobium to common low-alloy steel increases its resistance to atmospheric corrosion and corrosion by hydrogen, nitrogen and ammonia at high temperatures. Niobium also improves welding performance. When added to austenitic stainless steel, niobium prevents intergranular corrosion.
And cobalt effect on steel

Cobalt is a rare and valuable metal used mainly in special steels and alloys, such as heat-resistant steel and magnetic materials.
And steel coper effect

WISCO steel, made from Daye Ore, often contains copper. Copper increases strength and toughness, particularly performance against atmospheric corrosion. The disadvantage is that hot brittleness is more likely to occur during hot processing. When the copper content exceeds 0.5%, the plasticity is greatly reduced, but when the copper content is less than 0.50%, it has no impact on weldability.
And effect of aluminum on steel
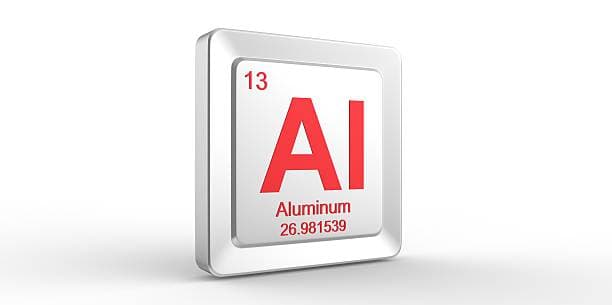
Aluminum is a common deoxidizer in steel. By adding a small amount of aluminum to steel, the grain structure is refined and impact resistance is improved, as seen in 08Al steel used for deep drawing sheets. Aluminum also has resistance to oxidation and corrosion.
When combined with chromium and silicon, aluminum greatly improves high-temperature non-galling performance and high-temperature corrosion resistance. However, aluminum negatively impacts the hot workability, welding performance, and cutting performance of steel.
And boron effect on steel

By adding a small amount of boron to steel, the compaction and hot rolling properties of the steel are improved and its strength increases.
And effect of R are and art and element in steel

Rare earth elements refer to the 15 lanthanides with atomic numbers 57-71 on the periodic table. These elements are all metals, but their oxides are similar to “earth,” which is why they are commonly called rare earths. The addition of rare earth elements to steel modifies the composition, shape, distribution and properties of inclusions in the steel, improving various properties such as toughness, weldability and cold workability. Adding rare earth elements to plow iron improves wear resistance.
See too:
- Effects of a total of 48 alloying elements on steel