1. Maximum tensile stress theory (the first theory of strength is maximum principal stress):
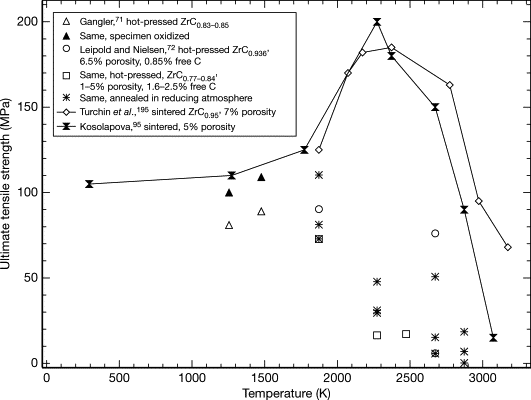
This theory is commonly referred to as the first theory of force. It states that the main cause of failure is maximum tensile stress. If the first principal stress reaches the uniaxial tensile strength limit, regardless of the complexity or simplicity of the stress state, it will result in fracture.
Failure form: Fracture
Damage conditions: σ1 =σb
Resistance condition: σ1≤(σ)
Experiments have shown that this strength theory can better explain the fracture phenomenon of brittle materials such as stone and cast iron, particularly in areas where maximum tensile stress is located. However, it is not suitable for cases without tensile stress, such as one-way compression or three-way compression.
Disadvantage: Does not consider the other two main voltages.
Scope of application: This theory is suitable for the tension of brittle materials such as stretching and twisting of cast iron.
2. Maximum elongation linear deformation theory (the second resistance theory is maximum principal deformation)
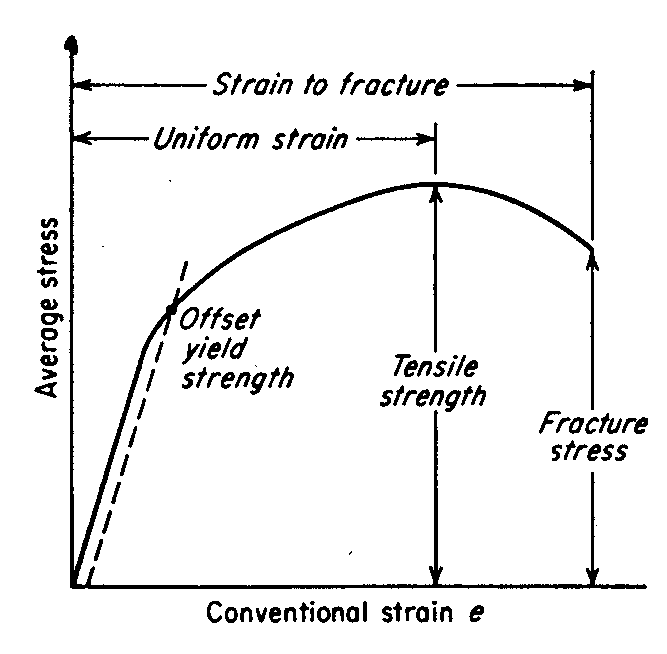
This theory is commonly referred to as the second theory of force. It postulates that the main cause of failure is maximum linear stretching deformation. If the first principal deformation reaches the limiting value of uniaxial stress, regardless of the complexity or simplicity of the stress state, fracture results.
Failure Assumption: The maximum elongation strain reaches the simple stress limit (assuming that Hooke's law can still be used to calculate until fracture occurs).
Failure form: Fracture
Brittle fracture conditions: ε1 = εu = σb/E;
ε1 = 1/E (σ1−μ(σ2+σ3));
Damage conditions: σ1−μ(σ2+σ3) = σb;
Resistance condition: σ1−μ(σ2+σ3)≤(σ)
Experiments have shown that this strength theory can better explain the fracture phenomenon of brittle materials such as stone and concrete under axial stress. However, it has been rarely used because its experimental results are consistent with only a few materials and cannot largely explain the general law of brittle fracture failure.
Disadvantage: Does not explain the general law of failure due to brittle fracture.
Scope of application: This theory is suitable for the axial compression of stone and concrete.
3. Theory of maximum shear stress (the third theory of strength, namely Tresca strength):
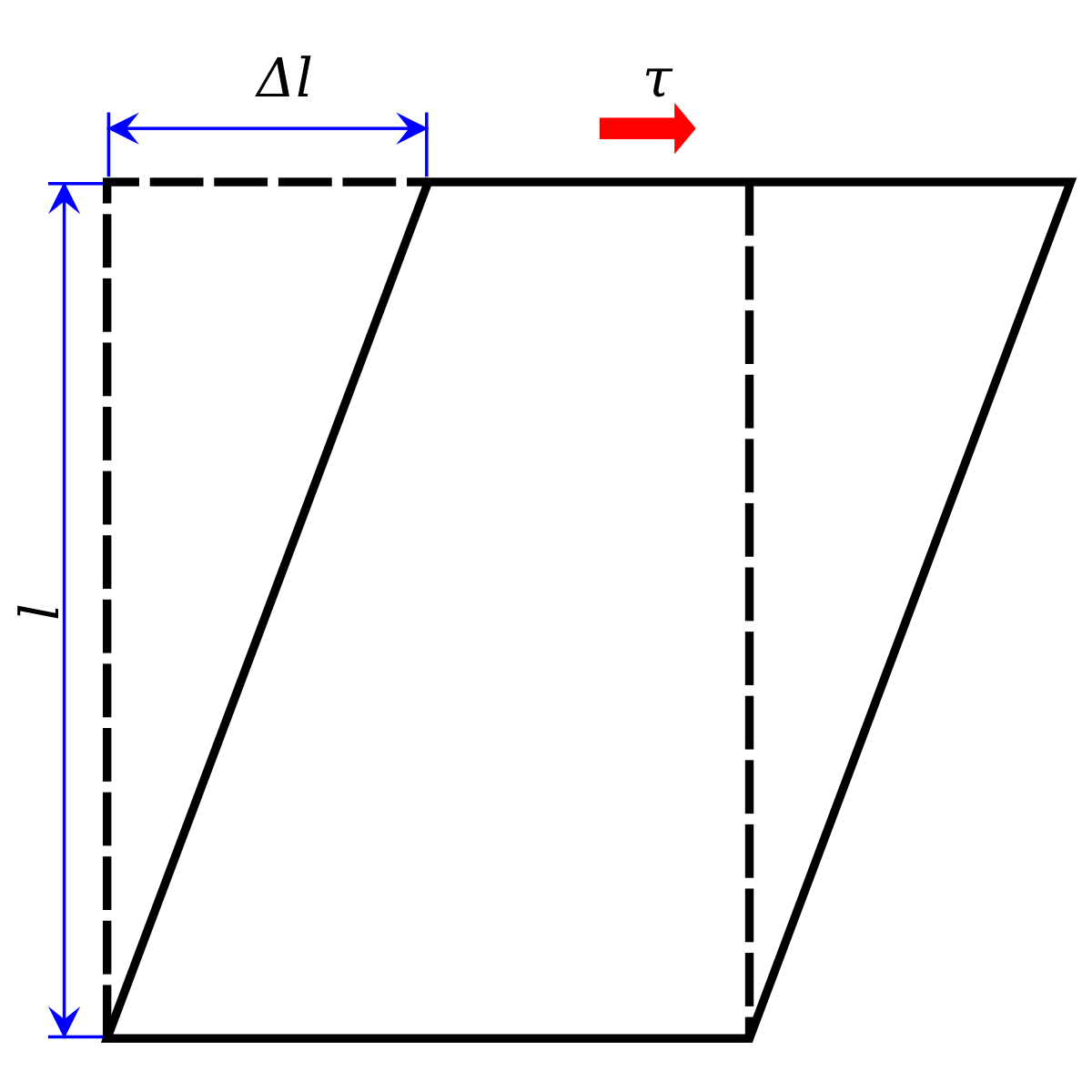
This theory, known as the third strength theory, postulates that the main cause of failure is the maximum shear stress (τmax). The theory states that regardless of the complexity or simplicity of the stress state, once the maximum shear stress reaches the final value of shear stress under uniaxial tension, yielding will occur.
The failure assumption is that when the maximum shear stress in a complex stress state reaches the shear stress limit of the material during simple tension and compression, failure will occur in the form of yielding. The main factor contributing to failure is the maximum shear stress, which is equal to the ultimate shear stress (τmax=τu=σs/2).
The yield failure condition is defined as τmax=1/2(σ1−σ3), and the damage conditions are met when σ1−σ3=σs. The strength condition is stated as σ1−σ3≤(σ).
Experiments have shown that this theory provides a better explanation for the plastic deformation of plastic materials. However, it should be noted that this theory does not take into account the influence of 2σ, and as a result, components designed based on this theory tend to be overly conservative.
Disadvantages: no influence 2 σ
Scope of application: suitable for general conditions of plastic materials.
The form is simple, the concept is clear, and the machinery is widely used.
But the theoretical result is safer than the real one.
4. Specific energy theory of shape change (fourth theory of force, namely von Mises force)
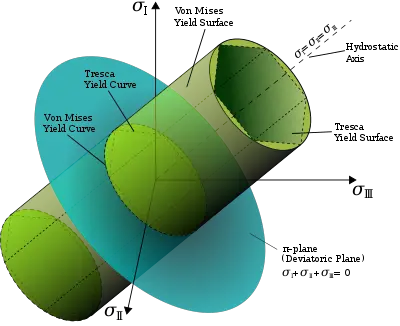
This theory is referred to as the fourth resistance theory and postulates that the reason for the yielding of a material is the specific energy (DU) of the shape change reaching a certain threshold value, regardless of the state of stress.
The damage conditions are defined as 1/2(σ1−σ2)2+2(σ2−σ3)2+(σ3−σ1)2=σs, and the strength condition is given as σr4= 1/2(σ1− σ2) 2+ (σ2−σ3)2 + (σ3−σ1)2≤(σ).
Experimental data from testing thin tubes on various materials (steel, copper, aluminum) showed that the theory of specific energy of shape change is more in line with experimental results compared to the third resistance theory.
A unified form of the four resistance theories can be established by having an equivalent stress (σrn) that has a unified expression of the resistance condition (σrn≤(σ)). The equivalent voltage can be expressed as follows:
σr1=σ 1≤(σ)
σr2=σ1−μ(σ2+σ3)≤(σ)
σr3=σ1−σ3≤ (σ)
σr4= 1/2(σ1−σ2)2+(σ2−σ3)2+(σ3−σ1)2≤ (σ)
5. Mohr's force theory
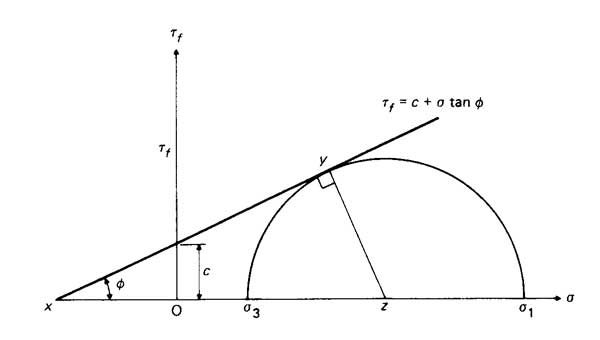
Mohr's strength theory is not based on the assumption that failure in materials is caused by a single factor (such as stress, strain, or specific energy) reaching its limiting value. Instead, it is a theory of strength based on the results of failure tests of materials under various states of stress.
This theory considers the differences between the tensile and compressive strengths of materials, recognizes the maximum shear stress as the main cause of yielding and takes into account the influence of normal stress in the shear plane.
Although Mohr's strength theory recognizes the different tensile and compressive capabilities of materials, which is consistent with brittle materials (such as rock and concrete), it does not take into account the influence of the intermediate principal stress 2a, which is a limitation of theory.
6. Scope of application of resistance theory
The strength of a material is not only determined by the nature of the material, but also by the state of stress at the point of failure.
Brittle materials are typically analyzed using brittle fracture strength theory or Mohr's strength theory, while plastic materials are analyzed using yield strength theory.
However, the failure mode in materials is also related to the stress state. For example, under the condition of three-dimensional tensile stress, whether it is a plastic or brittle material, it will fail in the form of fracture, and the maximum tensile stress theory must be used. In the case of three-dimensional compressive stress, plastic deformation occurs, and the third or fourth strength theory must be used.