Preface
To ensure the proper functioning of a mechanical system or structure, each component must be capable of effectively performing its intended function. The objective of engineering component safety design is to ensure that components have adequate strength, stiffness, and stability.
Stability is a widely understood concept, referring to the ability to maintain or recover its original state of balance under external force. For example, the sudden bending of a thin rod under pressure, the collapse of a building column due to load-bearing failure, or the buckling of thin-walled members are examples of instability.
Today, I will focus on discussing my understanding of stiffness and strength.
Strength
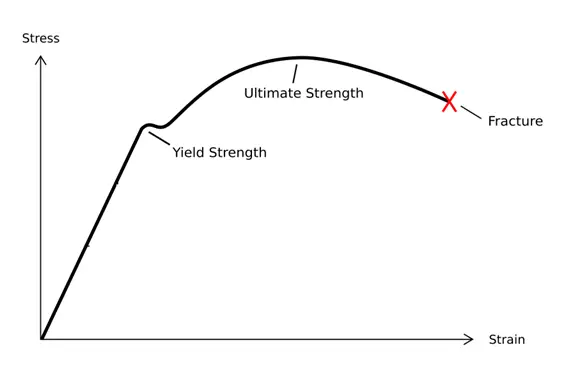
What is strength?
Definition: The ability of components or parts to resist damage (fracture) or substantial deformation when subjected to external forces.
For example, Tom used his iPad as a scale, but when he stood on it, the screen broke, indicating a lack of strength. Likewise, many large branches break during strong winds in summer, demonstrating a lack of strength.
Strength is a measure of a material's ability to resist failure, such as fracture. Typically encompasses tensile strength and compressive strength, which reflect the amount of failure of the material under tension.
The unit of measurement for resistance is commonly expressed in MPa.
Type of power failure
Brittle fracture: a sudden fracture that occurs without obvious plastic deformation.
For example, the fracture of a cast iron sample along the cross section during a tensile test and the fracture of a cast iron sample with a circular cross section along the oblique section during a torsion test.
Plastic performance: the material produces significant plastic deformations and causes the component to lose its work capacity.
For example, the low carbon steel sample will have significant plastic deformation during tension or twisting.
Force theory
1. Maximum tensile stress theory:
When the maximum tensile stress σ1 at a point on the member reaches the ultimate stress σb under unidirectional stress conditions, the material will undergo brittle fracture. Thus, the criteria for brittle fracture failure of components with critical points under complex stress conditions are: σ1 = σb.
Consequently, the resistance conditions established by the first resistance theory are: σ1 ≤ σb.
2. Theory of maximum tensile deformation:
When the maximum tensile strain ε1 reaches the limiting value εu under unidirectional stress conditions, the material will fail due to brittle fracture. This can be expressed as ε1 = εu.
From the generalized Hooke's Law, we can calculate ε1 as: ε1 = (σ1 – u(σ2 + σ3)) / E, then σ1 – u(σ2 + σ3) = σb.
The resistance conditions established by the second resistance theory are: σ1 – u(σ2 + σ3) ≤ σb.
3. Maximum shear stress theory:
When the maximum shear stress τMax reaches the ultimate shear stress τ0 under unidirectional stress conditions, the material will fail due to yielding. This can be expressed as τMax = τ0.
The formula for the shear stress in an inclined section during axial tension is τ0 = σs/2 (σs being the normal stress in the cross section). The formula for τMax is (σ1 – σ3)/2. Thus, the damage condition can be rewritten as σ1 – σ3 = σs.
The resistance condition established by the third resistance theory is: σ1 – σ3 ≤ σs.
4. Specific energy theory of shape change:
When the rate of shape change at a point on the member reaches the limiting value under unidirectional stress conditions, the material will fail due to yielding.
The resistance condition established by the fourth resistance theory is:
√(σ1^2 + σ2^2 + σ3^2 – σ1σ2 – σ2σ3 – σ3σ1) < σs.
2. Rigidity
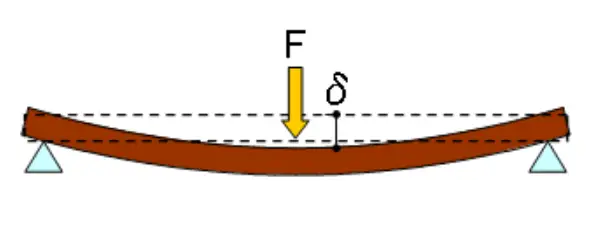
What is rigidity
Definition: refers to the ability of members or parts to resist elastic deformation or displacement under the action of external force, that is, the elastic deformation or displacement must not exceed the allowable design range.
Stiffness is a parameter that reflects the relationship between structural deformation and force, indicating the amount of deformation produced by a given amount of applied force.
In simple terms, stiffness is similar to a spring, where the stiffness of the spring is defined as the ratio of tensile force to elongation. The unit of stiffness is normally expressed in N/m.
Stiffness type:
When the applied load is constant, it is called static stiffness.
When the load alternates, this is called dynamic stiffness.
Static stiffness encompasses structural stiffness and contact stiffness.
Structural stiffness refers to the stiffness of the member itself and includes bending stiffness and torsional stiffness.
1. Flexural stiffness: calculated according to the following formula:
K=P/δ
Where P — static load (n);
δ——Elastic deformation in the load direction (μm)。
2. Torsional stiffness is calculated according to the following formula:
K i =ML/θ
Where M — applied torque (n · m);
L — distance from the torque action position to the fixed end (m);
θ—— Twist angle (°)
3. Relationship between strength and stiffness
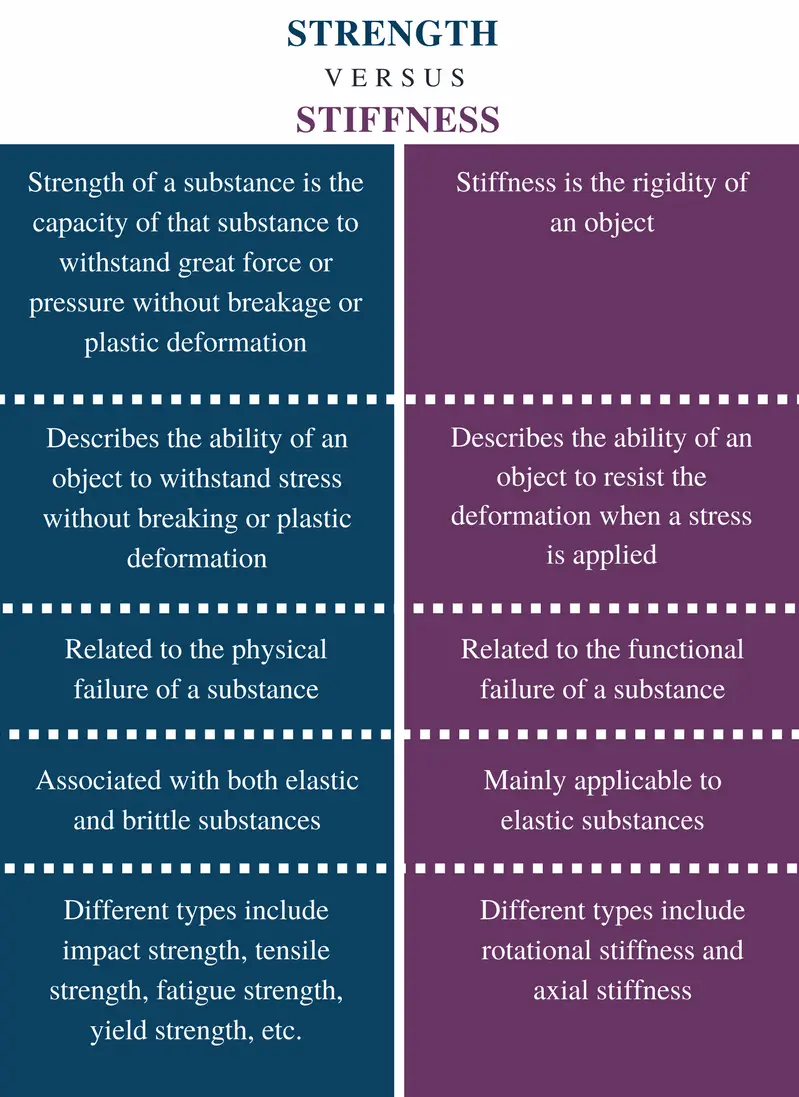
From the above explanation of strength and stiffness, it can be seen that strength focuses on failure under external force and is classified into plastic yielding and brittle fracture failure, which is related to the stress-strain curve during tensile testing. In comparison, stiffness refers to the relationship between deformation and force.
As shown in fig.
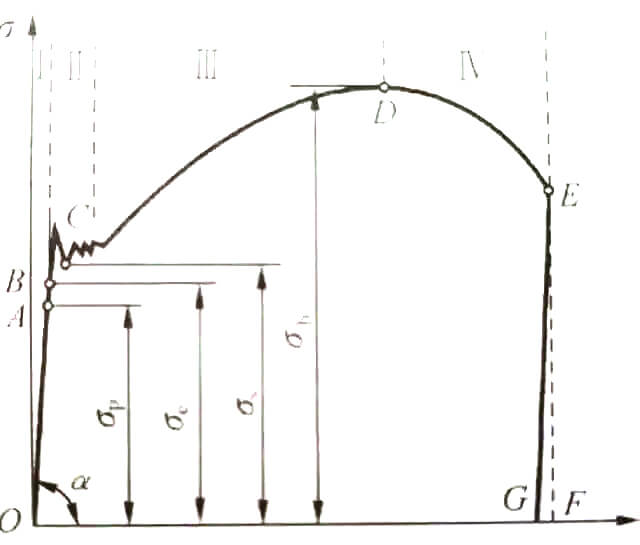
The curve in the figure can be divided into four stages:
1. Elastic deformation stage;
2. Income stage;
3. Strengthening stage;
4. Local narrowing stage.
Stiffness is defined as the resistance to elastic deformation, which occurs in the initial phase, and is governed by Hooke's law under elastic conditions.
The calculation of bending and torsional stiffness under static loads is similar to Hooke's law, suggesting that stiffness is only measured during the elastic deformation stage.
In the next step, when plastic deformation occurs during the tensile test, the residual deformation does not disappear. In the stress-strain curve, although the stress remains almost unchanged, the strain increases significantly. At this point, the stress reaches the yield point and the material enters the plastic yield failure stage. As the stress continues to increase, the strain also increases until the strength limit is reached.
Therefore, resistance measurement occurs after the material undergoes elastic deformation and before reaching the resistance limit.
Wrap it up
In conclusion, both stiffness and strength are evaluated during the failure phase of parts, with stiffness measured by tension and strength measured by deformation.
In terms of their order in the deformation process, stiffness occurs in the early phase, while strength occurs in the later phase.
Therefore, when evaluating the failure conditions of parts, as long as the stiffness requirements are met, the part should be able to withstand sufficient stresses during the elastic deformation stage, which in turn should meet the strength requirements.
This relationship is reflected in several projects, such as the axis in mechanical equipment. Typically, the shaft size is determined based on the strength conditions, and then its stiffness is checked based on the stiffness conditions.
Therefore, the stiffness requirements for precision machine shafts are very high, and the design of their cross-sectional size is often controlled by the stiffness conditions.