Causes of fatigue failure of welded structures
The causes of fatigue failure of welded structures mainly include the following aspects:
① Objectively, the static load capacity of welded joints is normally not weaker than that of the base metal. However, when subjected to alternating dynamic loads, their capacity is significantly lower and is closely related to the type of welded joint and structure. This is a major contributor to the premature failure of some structures due to fatigue in welded joints.
② The initial design of the welding structure mainly focused on static load resistance, ignoring fatigue design. Some welded joint designs are now considered unreasonable due to the lack of perfect fatigue design specifications.
③ Designers and engineering technicians lack adequate knowledge of the fatigue resistance characteristics of welded structures, leading to designs that often copy the fatigue design criteria and structural shapes of other metal structures.
④ Welded structures are becoming increasingly common, and in the design and manufacturing process, there is a trend towards lightweight and low-cost structures, resulting in increased design loads for these structures.
⑤ As welded structures advance toward high speeds and heavy loads, the demand for their dynamic load-bearing capacity continues to increase. However, the level of investigation into the fatigue resistance of welded structures remains inadequate.
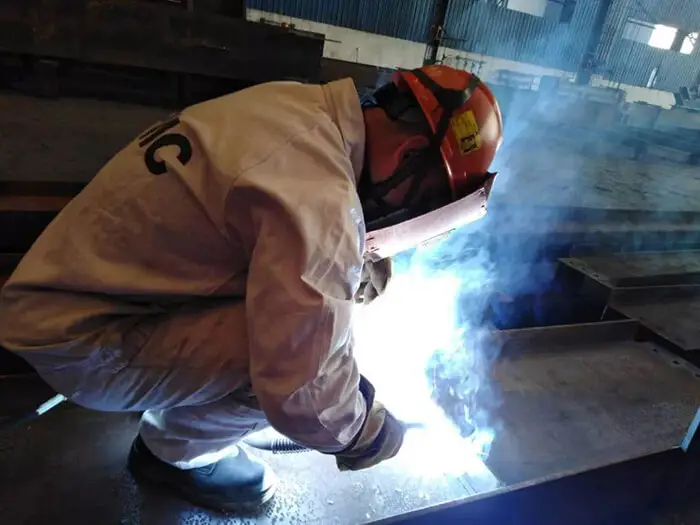
2. Causes of fatigue failure of welded structure
2.1 Effect of static load resistance on fatigue strength of welded structure
When studying iron and steel materials, researchers look for high specific strength, that is, the ability to withstand heavy loads and at the same time be light. This allows structures to have greater load capacity while maintaining the same weight, or to have the same capacity while being lighter. As a result, high-strength steel was developed and has high fatigue resistance.
The fatigue strength of base metals increases with increasing static load resistance. However, this does not apply to welded structures. The fatigue strength of welded joints has limited correlation with the static strength of the base metal, the weld metal, the microstructure and properties of the heat-affected zone, and the strength of the weld metal.
In other words, given the same welded joint details, the fatigue strength of high-strength steel and low-carbon steel is the same, and they have the same SN curve. This applies to various types of joints, such as butt joints, corner joints and welded beams.
Maddox conducted a study on fatigue crack growth in carbon-manganese steel with yield strengths ranging from 386 to 636 MPa, and weld metal and heat-affected zones welded using six different electrodes.
The results indicate that the mechanical properties of the material have some impact on the crack growth rate, but the effect is not significant.
In the design of welded structures subjected to alternating loads, the selection of high-strength steel is not significant in meeting engineering requirements. High-strength steel is only required for the base metal of the welded joint when the stress ratio is greater than +0.5 and the static strength condition plays a dominant role.
The reason for these results is the presence of undercut-like slag wedge defects along the fusion line at the weld tip of the joint, with a thickness of 0.075 mm to 0.5 mm and a tip radius of less than 0.015 mm. Sharp defects are the origin of fatigue cracks, equivalent to the fatigue crack formation stage.
Therefore, the fatigue life of the joint under a certain stress range is mainly determined by the propagation stage of the fatigue crack. These defects result in the same type of welded joints for all steels with the same fatigue strength, regardless of the static strength of the base metal and welding materials.
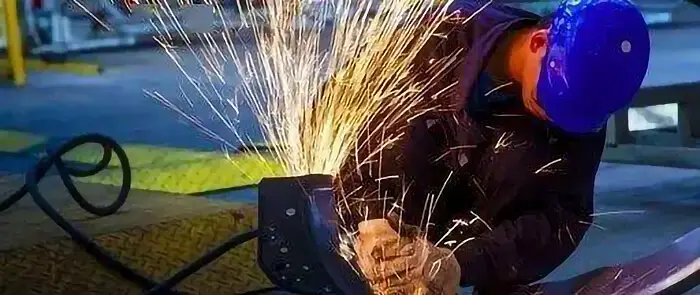
2.2 Effect of stress concentration on fatigue resistance
2.2.1 Influence of joint type
Welded joints include butt joints, cross joints, T-joints and lap joints. These joints are susceptible to stress concentration due to interference from the power transmission line.
Stress line interference from butt joints is minimal, resulting in low stress concentration and higher fatigue resistance compared to other joints. However, experiments have shown that the fatigue strength of butt joints can vary greatly due to various factors such as sample size, groove shape, welding method, electrode type, welding position, weld shape, processing of post-welding and post-welding welding. heat treatment.
The use of a permanent backer plate in a butt joint can cause significant stress concentration in the backer plate and reduce the fatigue strength of the joint. Fatigue cracks in this type of joint occur at the joint between the weld and the backing plate, rather than at the toe of the weld, and its fatigue resistance is generally equal to that of a worst-shaped butt joint without backing plate.
Transverse joints and T-joints are widely used in welded structures.
In these structural joints, the obvious change in section at the transition from weld to base metal results in a higher stress concentration factor compared to the butt joint, leading to lower fatigue strength for transverse and tee joints compared with butt joints. joints.
For non-chamfered joints connected by fillet welds and grooved joints with local penetration welds, fatigue fractures may occur at two weak links, i.e. at the junction between the base metal and the tip of the weld or weld, when the weld transmits stress of work. For channel-penetrating transverse joints, fractures generally occur only at the toe of the weld, not in the weld.
The fatigue resistance of T-shaped and cross joints, where the weld does not support working stresses, depends mainly on the stress concentration at the junction of the weld and the stressed main plate. T-joints have higher fatigue resistance, while cross joints have lower fatigue resistance.
Improving the fatigue strength of T-shaped or cross joints can be achieved by using channel welding and weld transition machining to create a smooth transition. This measure can greatly improve fatigue resistance.
The fatigue strength of lap joints is very low due to severe distortion of the force line. Using a so-called “reinforced” cover plate butt joint is extremely irrational.
The use of a cover plate in a butt joint significantly weakens its high fatigue resistance due to increased stress concentration.
In strong cover plate joints, fatigue cracks may occur in the base metal or weld. Additionally, changing the width of the cover plate or the length of the weld will change the stress distribution in the base metal, affecting the fatigue strength of the joint. The fatigue strength of the joint increases as the ratio of weld length to cover plate width increases, as this tends to result in a more uniform stress distribution in the base metal.
2.2.2 EU influence of weld shape
Regardless of the shape of the joint, they are connected by two types of welding: butt welding and fillet welding.
The shape of the welds affects the stress concentration factor, leading to significant variations in fatigue resistance.
The shape of the butt weld has the greatest impact on the fatigue strength of the joint.
(1) Influence of transition angle
Yamaguchi et al. established the relationship between fatigue resistance and the transition angle (external obtuse angle) between the base metal and the weld metal.
In the tests, the width (W) and height (H) of the weld changed, but the H/W ratio remained constant, that is, the included angle remained unchanged. The results showed that fatigue resistance also remained unchanged.
However, when the weld width remained constant and the height changed, it was found that an increase in height resulted in a decrease in the fatigue strength of the joint. This is clearly due to a decrease in the included external angle.
(2) Influence of the weld transition radius
The results of the research by Sander et al. indicate that the weld transition radius also significantly impacts the fatigue strength of the joint. As the transition radius increases (while the transition angle remains unchanged), fatigue resistance increases.
The shape of the fillet weld also has a significant impact on the fatigue strength of the joint. When the ratio of the calculated thickness (a) of a single weld to the plate thickness (b) is less than 0.6 to 0.7, it generally breaks at the weld. When a/b > 0.7, it generally ruptures the base metal.
Increasing the size of the weld cannot change the strength of another weak section, i.e. the base metal at the butt end of the weld, and therefore the fatigue strength cannot be exceeded at best.
Soete and Van Crombrugge conducted tests on 15 mm thick plates welded with different fillet welds under axial fatigue loading.
The results showed that when the weld leg was 13mm, fractures occurred in the base metal or at the weld tip. If the weld leg were smaller than this value, fatigue fractures would occur in the weld. When the leg size was 18 mm, fractures occurred in the base metal.
Based on these findings, they proposed a limit on weld leg size: S = 0.85B, where S is the weld leg size and B is the plate thickness.
Even though the size of the weld leg reached the thickness of the plate (15mm), fractures still occurred in the weld, which confirms the theoretical results.
2.2.3 influence of welding defects
There are numerous different types of weld tip defects that lead to early fatigue cracking and a significant decrease in the fatigue strength of the base metal (up to 80%).
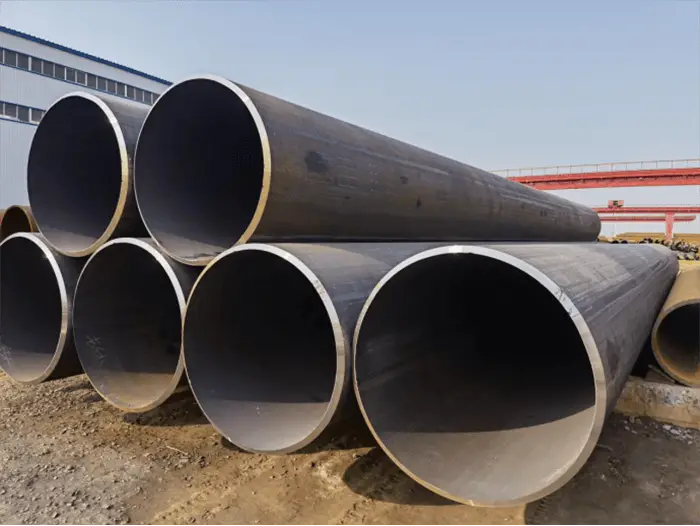
Welding defects can generally be divided into two categories:
Planar defects (such as cracks and lack of fusion) and volumetric defects (such as pores and slag inclusion) have varying degrees of influence.
Furthermore, the impact of welding defects on the fatigue strength of joints depends on the type, direction and location of the defects.
1) Crack
Welding cracks, such as cold and hot cracks, are significant sources of stress concentration, in addition to a fragile microstructure and can significantly reduce the fatigue resistance of structures or joints.
Previous studies have shown that in a sample of a low carbon steel butt joint with a width of 60mm and a thickness of 12.7mm, when there are cracks with a length of 25mm and a depth of 5.2mm in the weld (which occupy about 10% of the cross-sectional area of the sample), its fatigue resistance under alternating load is reduced by 55% to 65% after 2 million cycles.
2) Incomplete penetration
It is important to note that incomplete penetration is not always considered a defect, as it can be intentionally designed for certain joints, such as pressure vessel nozzles.
Incomplete penetration defects can be surface defects (one-sided weld) or internal defects (double-sided weld) and can be local or global. They mainly weaken the cross-sectional area and cause stress concentration.
Tests have shown that, compared to results without such defects, fatigue resistance is reduced by 25%, meaning the impact is not as severe as that from cracks.
3) Incomplete merger
Despite being a significant problem, there is limited research on this topic due to difficulties in sample preparation.
However, it is clear that lack of fusion is a type of planar defect and cannot be ignored. It is often treated as a form of incomplete penetration.
4) Undercut
The main parameters describing undercut are undercut length (L), undercut depth (h) and undercut width (W).
Currently, the main parameter that affects fatigue resistance is the depth of the recess (h), and can be evaluated both by depth (h) and by the ratio between depth and plate thickness (h/B).
5) Stomata
Harrison analyzed and summarized the results of previous tests related to volumetric defects.
The decrease in fatigue resistance is mainly due to the reduction in cross-sectional area caused by pores. There is a linear relationship between them.
However, some studies show that when the sample surface is machined, resulting in pores being located at or just below the surface, the negative impact of the pores will increase. They will act as a source of stress concentration and become the starting point for fatigue cracks.
This suggests that pore location has a greater impact on joint fatigue strength than joint size, and pores located at or below the surface have the most significant negative effect.
6) Slag inclusion
Research carried out by IIW showed that among volumetric defects, the inclusion of slag has a greater impact on the fatigue resistance of joints compared to porosity.
The impact of welding defects on the fatigue strength of joints not only depends on the size of the defect, but is also influenced by several other factors, such as surface defects that have a greater impact than internal defects and planar defects perpendicular to the direction of welding. strength. having a greater impact than in other directions.
The influence of defects located in areas of tensile residual stress is greater than those in areas of compressive residual stress, and defects located in areas of stress concentration, such as weld cracks, have a greater impact than the same defects in uniform stress fields.
2.3 Effect of welding residual stress on fatigue strength
Welding residual stress is a characteristic of welded structures that is widely studied for its impact on the fatigue strength of these structures. Numerous experimental studies have been conducted to examine this question.
Fatigue tests are often performed by comparing samples with welding residual stress with those that have undergone heat treatment to remove residual stress. This is because the generation of welding residual stress is often accompanied by changes in material properties resulting from the welding thermal cycle, and heat treatment not only eliminates residual stress but also partially or completely restores the material properties.
However, due to the variability of test results, there are different interpretations of the results and assessments of the impact of welding residual stress. This can be seen by looking at early and recent research conducted by various individuals.
For example, different researchers have reached different conclusions from 2×106 cycle tests on reinforced butt joints.
It was found that the fatigue resistance of a sample after heat treatment for stress relief was 12.5% higher than the same sample in its welded state. However, some studies found that the fatigue strength of welded and heat-treated samples was the same with little difference. In other findings, fatigue strength increased after heat treatment to remove residual stress, but the increase was much less than 12.5%.
Similar results were found in testing surface-grinded butt joint samples. Some tests showed that fatigue resistance could be increased by 17% after heat treatment, while others showed no improvement.
This question has been a source of confusion for some time. However, a series of tests under alternating loads conducted by scholars from the former Soviet Union helped to clarify the problem. Trufyakov's research on the effect of welding residual stress on joint fatigue strength under different stress cycle characteristics is especially noteworthy.
The tests were carried out using common 14Mn2 low alloy structural steel and involved a transverse butt weld on the sample, with a longitudinal weld bead overlapping on both sides.
One group of samples was subjected to heat treatment to eliminate residual stresses after welding, while the other group was not treated. The fatigue resistance comparison test was carried out using three coefficients characteristic of the stress cycle, r = -1, 0 and +0.3.
Under alternating loading (r = -1), the fatigue strength of the sample with residual stress relieved was close to 130 MPa, while the sample without elimination showed a fatigue strength of only 75 MPa.
Under pulsating load (r = 0), the fatigue strength of both groups of samples was the same, at 185 MPa.
When r = 0.3, the fatigue strength of the sample with residual stress eliminated by heat treatment was 260 MPa, slightly lower than that of the sample without heat treatment, which showed a fatigue strength of 270 MPa.
The main reasons for this phenomenon are:
When the value of r is high, such as under pulsating load (r = 0), the fatigue strength is high and the residual stress is quickly released under the influence of high tensile stress, reducing the impact of residual stress on fatigue strength . When r increases to 0.3, the residual stress decreases further under load, having no effect on fatigue strength.
Heat treatment not only eliminates residual stress but also softens the material, leading to a decrease in fatigue resistance after treatment.
This test demonstrates the influence of residual stress and material changes caused by the welding thermal cycle on fatigue resistance. It also indicates that the impact of welding residual stress on the fatigue strength of a joint is related to the stress cycle characteristics of the fatigue load. When the cycle characteristic value is low, the impact is relatively high.
It was previously noted that because residual stress reaches the yield point of the material in a structural weld, in a joint with a constant amplitude stress cycle, the actual stress cycle near the weld will fall below the yield point of the material, regardless of the original cycle. characteristics.
For example, the nominal voltage cycle should be +S1 to -S2, with a voltage range of S1 + S2. However, the actual stress cycle range in the joint will be from sy (stress amplitude at the yield point) to SY-(S1 + S2).
This is a crucial factor to consider when studying the fatigue resistance of welded joints, leading some design codes to replace the cyclic characteristic r with the stress range.
In addition, the sample size, loading mode, stress cycle relationship and loading spectrum also have a significant impact on fatigue resistance.
3. Process method to improve fatigue resistance of welded structure
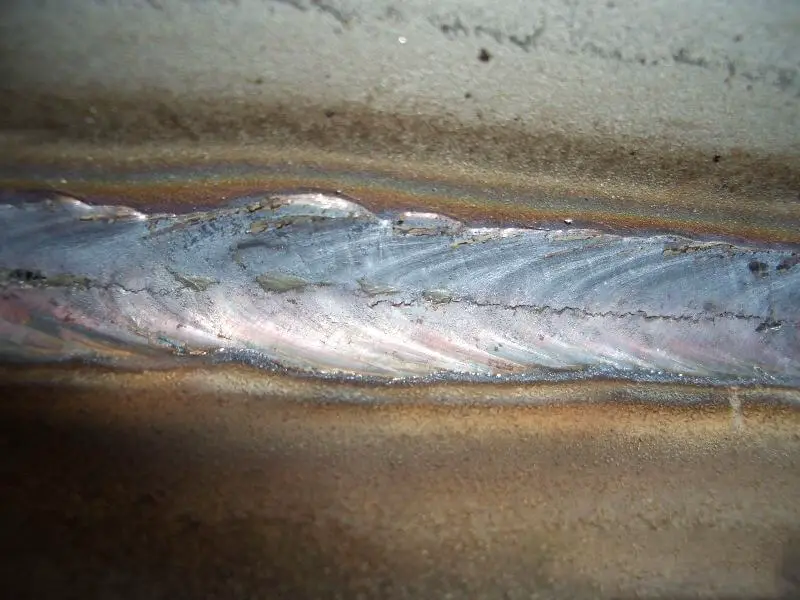
The initiation of fatigue cracking in welded joints typically occurs at the root and toe of the weld. If the risk of fatigue crack initiation at the weld root is controlled, the most vulnerable points in welded joints are concentrated at the weld tip.
There are several ways to improve the fatigue resistance of welded joints:
① Reduce or eliminate welding defects, especially openings;
② Improve the geometry of the weld tip and reduce the stress concentration factor;
③ Adjust the welding residual stress field to produce a compressive residual stress field. These improvement methods can be divided into two categories, as shown in Table 1.
Optimizing the welding process not only improves the fatigue resistance of the welded structure, but also increases the static load resistance and metallurgical properties of the welded joints. There is a vast amount of data on this topic, which will not be repeated here.
Table 1 Methods for improving the fatigue strength of the welded structure
Method of improving fatigue resistance of welded structure | Optimization of the welding process | Local geometry | Quality control | Welding defect control | 1 | |
Geometry improvement | two | |||||
Technological process | Welding sequence | 3 | ||||
Residual voltage(<0) | Weld toe metallurgical treatment | 4 | ||||
Weld bead modeling | Weld Toe Geometry | 5 | ||||
State of gold and metal | 6 | |||||
Welding improvement | Local geometry | Machining | Welding tip grinding | 7 | ||
Water impact | 8 | |||||
Local remelting | TG Repair | 9 | ||||
Plasma Repair | 10 | |||||
Residual stress | Stress Release Method | Heat treatment | 11 | |||
Mechanical treatment | 12 | |||||
Local heating | 13 | |||||
Mechanical method | mechanical contact | Shot peening | 14 | |||
Hammer | 15 | |||||
Ultrasonic impact | 16 | |||||
Welding | Stamping | 17 | ||||
Local compression | 18 |
The main methods for increasing the fatigue strength of welded joints are discussed in detail in three parts, focusing on process methods.
3.1M Methods for Improving Weld Tip Geometry and Reducing Stress Concentration
1) TIG dressing
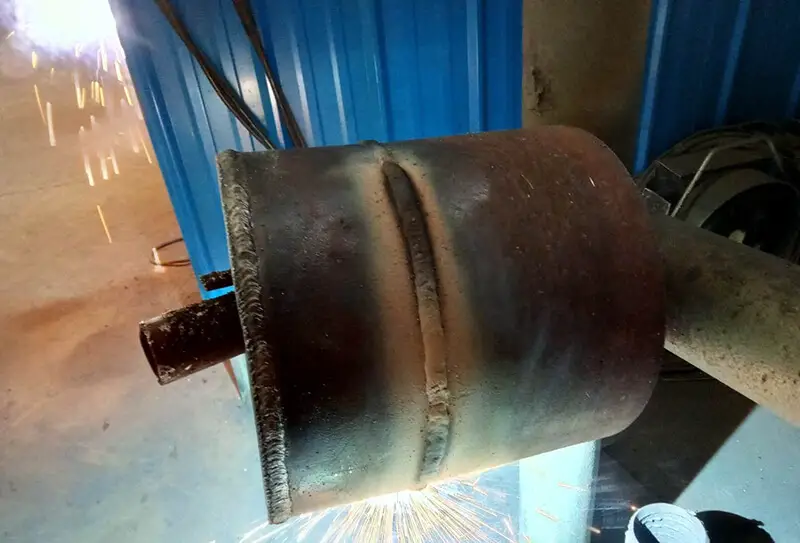
Studies have shown that TIG repair can significantly increase the fatigue resistance of welded joints, both nationally and internationally. The process involves using TIG welding to re-fuse the transition section of the welded joint, creating a smooth transition between the weld and the base metal. This reduces stress concentration and eliminates small inclusions of non-metallic slag, resulting in improved fatigue resistance of the joint.
The welding gun is normally positioned 0.5 to 1.5 mm away from the welding tip during the repair process, and the re-melted area must be kept clean. Adding a light grind beforehand will improve results.
It is crucial to properly handle the back-arc process if arc extinction occurs during remelting, as this will affect the quality of the remelted weld bead. The best position for the back arc is generally 6 mm in front of the weld bead crater.
Recently, the International Welding Society collaborated with welding research institutes in several European countries and Japan to conduct a unified study on the effectiveness of methods for increasing the fatigue resistance of joints. Samples were prepared by the British Welding Research Institute.
The study confirmed that the nominal fatigue strength of the joint after 2×10 6 cycles increased by 58% after treatment with this method. This nominal fatigue strength value of 211MPa corresponds to a characteristic value (K-index) of 144MPa. Exceeds the highest FAT value for fatigue resistance of joint details established by the International Welding Society.
2) Machining
Machining the weld surface can greatly reduce the stress concentration and improve the fatigue resistance of the butt joint. If the weld is free from defects, its fatigue resistance may even exceed that of the base metal. However, machining is an expensive process and should only be carried out when the benefits justify the cost.
In the case of welds with significant defects and without bottom welding, the stress concentration in the defect or at the root of the weld is much more severe than at the surface, making machining meaningless. If there is a lack of penetration defect, fatigue cracks will not initiate at the reinforcement and toe of the weld, but will be transferred to the root of the weld. In these cases, machining can actually reduce the fatigue strength of the joint.
Grinding just the tip of the weld, rather than the entire weld metal, can also improve the fatigue strength of the joint. Research has shown that the crack initiation point in this scenario is transferred from the weld tip to the weld defect.
Fatigue strength tests conducted by Makorov of the former Soviet Union on high-strength steel (tensile strength σb = 1080MPa) showed that the fatigue strength of transverse butt welds under alternating load was ±150MPa after 2×10 6 cycles as soldiers. Weld machining and reinforcement removal increased the fatigue strength to ±275MPa, equivalent to the fatigue strength of the base metal. Local grinding at the tip of the butt weld resulted in a fatigue strength of ±245MPa, equivalent to 83% of the machining effect and a 65% improvement over the welded state.
It is important to note that a suitable technique must be used in both machining and grinding to ensure the desired improvement in fatigue resistance.
3) Grinding wheel grinding

Grinding with a grinding wheel may not be as effective as machining, but it is still a useful method for increasing the fatigue resistance of welded joints. The International Welding Society recommends using a high-speed electric or hydraulic grinding wheel with a speed of 15,000 to 40,000 RPM, made of carbon and tungsten material. The diameter of the grinding wheel must ensure that the grinding depth and radius are equal to or greater than 1/4 of the plate thickness.
Recent research by the International Welding Society found that the nominal fatigue strength of the sample after 2 cycles increased by 45% after grinding. The nominal fatigue strength value of 199 MPa corresponds to a characteristic value (135 MPa), which is higher than the highest FAT value in joint detail fatigue strength established by the International Welding Society.
It is important to note that the grinding direction must be aligned with the direction of the stress line. Grinding in a different direction can leave a notch perpendicular to the stress line, effectively acting as a source of stress concentration and reducing the fatigue strength of the joint.
4) Special electrode method
This method involves developing a new type of electrode. Its liquid metal and liquid slag have high wettability, which increases the weld transition radius, reduces the angle at the weld tip, reduces the stress concentration at the weld tip and improves the fatigue resistance of the welded joint.
Like TIG welding repair, it has a strong preference for certain welding positions, particularly flat and fillet welding, while its benefits are significantly reduced for vertical, horizontal and overhead welding.
3.2M method of adjusting the residual stress field to produce compressive stress
1) Pre-overload method
When a tensile load is applied to a sample containing stress concentration until yielding occurs at the notch, resulting in some tensile plastic deformation, compressive stress will be generated at the location of tensile plastic deformation close to the loaded notch after unloading. . Tensile stress below the yield point will be balanced in other sections of the sample.
In subsequent fatigue tests, the stress range of the sample subjected to this treatment will be different from that of the original sample without preload and will be significantly reduced. This can improve the fatigue resistance of welded joints.
Research shows that a preload test is necessary before large welded structures, such as bridges and pressure vessels, are placed into service. This will improve your fatigue performance.
2) Local heating
Local heating can adjust the residual stress field in welding, generating compressive residual stresses at stress concentration points, which can improve the fatigue resistance of the joint. Currently, this method is only applicable to discontinuous longitudinal welds or joints with reinforced longitudinal plates.
For single-sided fillet plates, the heating position is typically about 1/3 of the plate width from the weld. For double-sided fillet plates, the heating position is the center of the plate. This generates compressive stresses in the weld, increasing the fatigue resistance of the joint.
Different researchers have obtained varying results using this method. For single-sided gusset plates, fatigue strength increased by 145-150%, while for double-sided gusset plates, fatigue strength increased by 70-187%.
The position of local heating has a significant impact on the fatigue strength of the joint. Point heating at the end of the weld causes compressive residual stress in the notch and increases fatigue resistance by 53%. However, point heating in the center of the sample at the weld end, with the same distance from the weld end, has the same metallographic effect, but produces tensile residual stress, resulting in the same fatigue strength as the untreated sample.
3) Extrusion method
The local extrusion mechanism is similar to the spot heating method in that it improves the joint's fatigue resistance by generating compressive residual stress. However, their action point differs and the extrusion position should be where the compressive residual stress is desired.
The extrusion method has a more significant effect on high-strength steel samples than on low-carbon steel.
4) Gurnnert method
Gunnert proposed a method for obtaining satisfactory results due to the difficulty in accurately determining the heating position and temperature in the local heating method. The key to this method is to heat the notch directly, rather than the surrounding area, to a temperature that can cause plastic deformation but is lower than the phase transformation temperature of 55°C or 550°C, and then cool it rapidly. .
Delayed cooling of the metal beneath the surface and surrounding metal that is not cooled will cause shrinkage and generate compressive stress on the cooled surface. This compressive stress can increase the fatigue resistance of the member.
It is important to note that the heating process must be slow to heat the bottom layer. Gunnert recommends a 3-minute warm-up time, while Harrison recommends 5 minutes.
Ohta successfully prevented fatigue cracks in butt tubes using this method. The external part of the pipe was heated by induction and the internal part was cooled by water circulation, generating compressive stress in the pipe and effectively preventing the formation of fatigue cracks. After treatment, the fatigue crack growth rate of the butt weld pipe was greatly reduced and reached the same crack growth rate as the base metal.
3.3M methods of stress concentration reduction and compressive stress generation
1) Hammering method
Hammering is a cold working method that creates compressive stress on the surface of the weld tip in a joint. The effectiveness of this method depends on the plastic deformation on the surface of the weld tip.
Furthermore, hammering can reduce notch sharpness and therefore stress concentration, leading to a significant improvement in joint fatigue resistance. The International Welding Society recommends a pneumatic hammer pressure of 5-6 Pa.
The top of the hammer head should be solid with a diameter of 8-12mm, and it is recommended to use four impacts to ensure a hammering depth of 0.6mm.
Research from the International Welding Society shows that for non-structural T-joints, hammering increases fatigue resistance by 54% under 2×10 6 cycles.
2) Shot peening
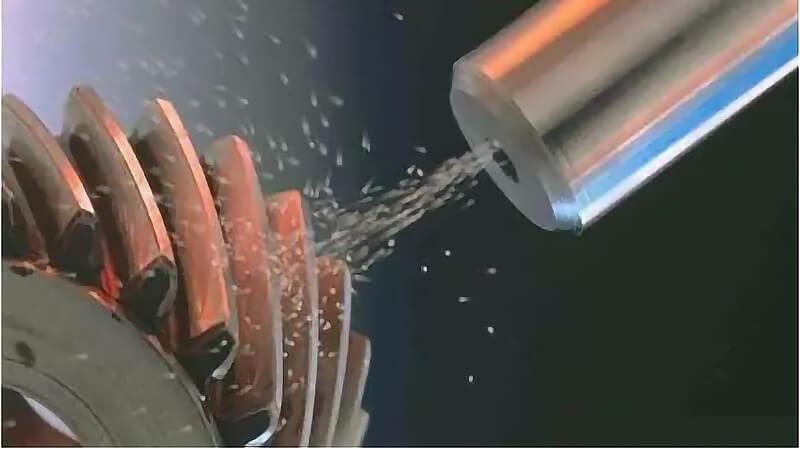
Shot peening is another form of hammering and is a type of impact machining. The effectiveness of shot peening depends on the diameter of the shot peening. The diameter should not be too large to resolve small defects, but not too small to achieve a certain level of cold work hardening. Shot peening can typically impact the surface to a depth of a few thousandths of a millimeter.
Research shows that shot peening can greatly improve the fatigue resistance of high-strength steel joints and has a particularly strong effect on argon arc welding of high-strength steel materials, even surpassing TIG repair. The use of shot peening can also increase the impact of TIG fusion repair.
4. The latest technology to improve the fatigue resistance of welded joints
4.1 Ultrasonic impact treatment method
In recent years, ultrasonic impact has been developed as a means of improving the fatigue resistance of joints and welded structures. Its mechanism is similar to hammering and shot peening.
However, ultrasonic impact has advantages such as light weight, good control, flexible and convenient use, minimal noise, high efficiency, fewer application restrictions, low cost and energy efficiency. It is suitable for all types of joints and is an effective method for improving the fatigue performance of welded joints after welding.
Studies have been carried out using ultrasonic impact treatment on butt joints and unsupported longitudinal corner joints of several typical welded structural steels. Comparative fatigue tests were then conducted on welded and impact treated joints. The results, presented in Table 2, indicate that the fatigue resistance of the welded joints increased by 50 to 170% after ultrasonic impact treatment.
Table 2 Comparison of fatigue resistance before and after ultrasonic impact treatment
Material and joint shape | Fatigue resistance Ds/MPa | Degree of increase (%) | |
---|---|---|---|
As a soldier | State treated for shock | ||
Q235B (R= 0.1) – butt joint | 152 | 230 | 51 |
SS800 (R= 0.05) – butt joint | 306 | 101 | |
16Mn (R= 0.1) – butt joint | 285 | 88 | |
Q235B (R=0.1) – longitudinal corner joint | 104 | 200 | 92 |
SS800 (R=0.05) – longitudinal corner joint | 279 | 168 | |
16Mn (R=0.1) – longitudinal corner joint | 212 | 104 |
4.2 l strip method of phase change spot welding
4.2.1 P Principle and development of improving fatigue resistance of welded joints
Compressive stress can increase the fatigue resistance of welded joints, which has been widely discussed in the literature. However, the challenge lies in how to easily introduce compressive stresses into welded joints.
It is well known that chemical composition, alloy content and cooling rate can result in different microstructural changes during the cooling process of iron and steel materials. These structural transformations are accompanied by volume expansion, which can create phase transformation stresses when constrained, leading to compressive stresses.
For the weld metal, this reduces tensile residual stress and even results in compressive residual stress, thus improving the mechanical properties of the welded joints.
Low transformation temperature welding electrode (LTTE) is a new welding material that uses phase transformation stress to produce compressive stress in welded joints and increase their fatigue resistance.
As early as the 1960s, welding experts in the former Soviet Union proposed the low-phase transformation spot welding strip method to improve the fatigue resistance of welded structures, although the term “low phase transformation spot welding strip” phase” was not used at the time and was simply referred to as a special electrode.
The surface metal composition mainly consists of 3-4% Mn to reduce the phase transformation temperature and achieve metallurgical phase transformation. Literature suggests that the fatigue resistance of small samples after coating with these special electrodes is 75% higher than without coating.
Recently, the development of ultra-low carbon steel and the use of Cr and Ni to reduce the martensitic transformation temperature of metal deposited in welding materials has led to rapid progress in low-transformation strip spot welding.
Both Japan and China have conducted extensive research in this area, although it is still in the laboratory phase.
4.2.2 And effect of LTTE electrode on improving fatigue resistance
Tianjin University School of Materials designed and optimized the low transformation temperature welding electrode (LTTE) and conducted extensive fatigue tests and process performance tests on various welded joints.
( 1) LTTE Method
Low transformation temperature welding electrode (LTTE) and common electrode E5015 were used to weld transverse butt joint, unloaded cross joint, longitudinal circumferential fillet joint, longitudinal parallel fillet weld joint and longitudinal top, respectively. A comparative fatigue test was carried out.
The results indicate that the fatigue strength of the phase change spot welding rod LTTE joint was 11%, 23%, 42%, 46% and 59% higher than that of the E5015 common electrode. Fatigue life increased from several times to hundreds of times.
Table 3 Fatigue resistance improvement effect of different types of welded joints
Electrode type | Transverse butt joint | Unloaded cross joint | Longitudinal Circumferential Fillet Weld Joint | Longitudinal Parallel Fillet Weld Joint | Longitudinal butt joint |
---|---|---|---|---|---|
E5015 welding rod | 176.9 | 202.1 | 167.0 | 182.7 | 179.4 |
LTTE Electrode | 157.8 | 164.8 | 118.3 | 124.9 | 113.0 |
Degree of improvement | 11% | 23% | 41% | 47% | 58% |
Stress concentration | Take K1 | Medium K2 | Fort K3 | N4 particularly strong | K4 particularly strong |
Degree of restriction | Big Small |
Because the low transformation temperature (LTTE) welding electrode creates residual compressive stress from the volumetric expansion of the martensitic transformation at a lower temperature, the magnitude of the residual compressive stress is closely linked to the restraint of the welded joint.
The tighter the welded joint, the greater the residual compressive stress and the more significant the improvement in fatigue strength.
(2) LTTE dressing method for low phase transformation spot welding
However, adding more alloy elements to welding materials to achieve martensitic transformation at a normal cooling rate and low temperature significantly increases the cost of low transformation temperature welding electrode (LTTE). If all welds in a welded structure are made with low phase change welding materials, the overall cost of the structure will also be significantly higher, making it economically unviable.
It is well known that fatigue fracture in welded joints generally occurs at the toe of the weld. If residual compressive stress is generated at the weld tip, the fatigue strength of the welded joint can be improved without using all low phase change spot welding strips, reducing the cost of materials.
With this idea in mind, Tianjin University proposed the low transformation temperature welding electrode (LTTE) dressing method to improve the fatigue resistance of welded joints based on experimental results. The fatigue resistance of LTTE dressing and common electrode welded joints was compared using two types of unloaded cross joint and longitudinal circumferential fillet weld joint. The fatigue resistance of the first was 19.9% and 41.7% higher than that of the second, respectively, proving the viability and practicality of the idea.
This preliminary research provides a more reasonable application of low transformation temperature welding electrode (LTTE) in engineering practice.
At the same time, the tip coating joint of low transformation temperature (LTTE) welding electrode can also reflect its application in overlay welds and weld beads near the tip tip.
4.2.3 A Advantages and disadvantages of low phase change spot welding strip
Advantage:
(1) The low transformation temperature welding electrode (LTTE) method is carried out during the welding process, eliminating the need for post-welding processing.
(2) The LTTE method does not require special operational skills, making it simple and convenient to use.
(3) When using low transformation temperature welding electrode (LTTE), the fatigue resistance of welded joints can be improved. As it is not affected by the thermal effects of subsequent weld beads, it is suitable for improving the fatigue resistance of hidden welds, covered welds, back welds of one-sided welding and other welds that cannot be processed after welding.
(4) LTTE electrode can also be used to repair fatigue cracks in welded structures.
Disadvantages:
Adding more alloying elements to welding materials increases the cost of low transformation temperature (LTTE) welding electrode materials, but this can be offset by the use of LTTE dressing and other methods.
5. Conclusion
In conclusion, dynamic bearing capacity requirements for welded structures have increased as they are used for heavy, high-speed loads. As a result, the development and use of new technologies to improve the fatigue performance of welded joints is crucial to the wider application of welded structures.
Both ultrasonic impact technology and the use of low transformation temperature welding electrode (LTTE) to improve the fatigue strength of welded joints are important research directions in the field of fatigue and process performance improvement of welded structures.