After 90 hours of operation, a broken rivet head was discovered at the junction between frame 15a and the inlet liner.
Observations and analysis of the fracture surface, including macro and micro observations, metallography, hardness testing and fatigue stress calculation, revealed that the failure of the rivet was caused by fatigue fracture.
A deviation in the alignment of the mounting hole between the frame and the rivet-connected shell resulted in an imbalance between normal bending and shear stress, compounded by the additional stress from airflow vibrations. This led to an increase in the initial stress on the rivet, causing it to fracture.
The results of the fracture surface analysis also showed that the rivet suffered a higher level of initial fatigue stress and a lower level of expansion stress.
Introduction
Riveting offers several benefits, including simple process and equipment, vibration and impact resistance, consistent force transmission, and durability and reliability.
As a result, riveting is a commonly used connection method.
To complete the riveting process, first align the connected parts and place them in the correct position. Then align the rivet holes and insert the rivets. Finally, use a tool to form the rivet heads and secure the rods in place.
The load is transferred through the frictional force on the mating surface of the connectors as the rivet is joined by the connecting tool.
Common stress and failure modes in rivets include:
- Rivet cutting;
- Shearing of the edge of the connection plate;
- Crushing of the rivet hole contact surface;
- Damage to the connection plate along the rivet hole;
- Tear on the edge of the connection plate.
The two main types of rivet design failures are shearing of the rivet shank and extrusion or collapse of the metal at the point of compression between the rivet and the connected parts.
In the production process, inadequate control of heat treatment is the main cause of rivet failure, both domestically and internationally. This can result in coarse grains, excessive burning or the presence of brittle phases in the raw materials.
During the upsetting process, high shear strength or cracking of the rivet head may occur during the riveting process. Abnormal external forces can also lead to rivet shearing.
Fatigue failure in rivets is rare due to their mode of connection, state of stress and other characteristics. However, abnormal assembly and other stress conditions during practical engineering applications can result in fatigue failure, causing the fastener connection to fail and increasing opening displacement. This can also lead to abnormal stresses on nearby rivets and result in fatigue failure of the connection.
Performing a rivet fatigue failure analysis is crucial. This can be done through visual observation, macro and micro examination of the fracture surface, metallography, hardness tests and other methods.
By combining the results of fracture surface analysis and estimation, this study reverses the crack growth characteristics and initial equivalent comprehensive stress of riveted engineering components, providing data support for the stress characteristics and size of the components. This information is useful for determining the root cause of the failure and resolving practical engineering problems.
1. Testing process and results
It was found that the first rivet head at the connection between frame 15a and the inlet liner fell out after 90 hours of service, which is equivalent to 130 takeoffs and landings (as shown in Fig. 1).
The rivet material is LY10 aluminum alloy, a medium strength duralumin with a tensile strength of 390 MPa and a high shear strength of 235 MPa. This material has sufficient plasticity for riveting under various conditions such as annealing, quenching, aging and heat conditions. It is commonly used to manufacture medium-strength rivets and structural parts.
1.1 Appearance observation
The rivet broke at the head arch transition.
From the side damage, it can be seen that the junction of the two connecting plates in the straight section of the rivet was severely deformed, indicating a deviation in the coaxiality of the mounting holes between the frame and the skin (as shown in Figure 2).
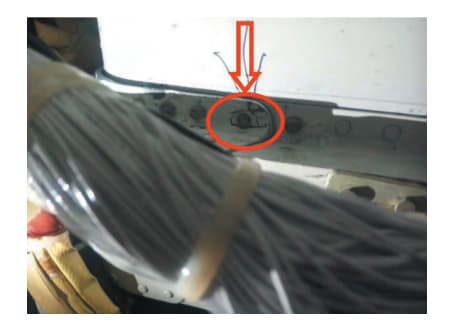
1.2 Macro and micro observation of the fracture surface
Place the fractured rivet under a scanning electron microscope for microscopic examination.
The source of rivet fracture is located on its outer surface (as seen in Figure 3a).
The fountain area features steps and extended edges, forming a large linear fountain that covers approximately one-sixth of the circumference.
No metallurgical defects or traces of processing were identified in the source area (as shown in Figures 3b and 3c).
During the crack growth phase, numerous small arcs and fatigue bands can be observed (as seen in Figure 3d), with the crack growing mainly through fatigue, representing more than 95% of the total cross-sectional area.
An analysis of the energy spectrum of the rivet fracture origin area and the expanded area revealed the absence of any foreign elements.
The side of the fracture source area was also examined and it was found that the anodized protective film on the surface was intact (as shown in Figure 3e).
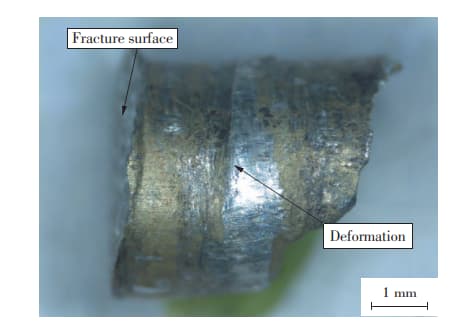
1.3 Material inspection
Metallographic and hardness inspection of the rivet revealed no abnormalities in its metallography and a relatively uniform hardness value.
2. Analysis and discussion
2.1 Analysis of rivet fracture property
Rivet fracture occurs at the transition point between the rivet head and the arc, and there are numerous small fatigue arcs and fatigue bands visible on the fracture surface.
This indicates that the rivet failure is due to fatigue.
Fracture occurs at the initial riveting location of the connecting frame, which is the connection between frame 15a and the air inlet liner.
If the riveting process is abnormal, the first rivet is more susceptible to failure, which is in line with the general principle of fastener failure in riveting.
2.2 Quantitative analysis and estimation of rivet fracture
In general, the most common mode of failure of rivets as fasteners is shear fracture.
When fatigue fracture occurs in the arc of the rivet head, it shows that its riveting function has been changed to some degree.
During proper assembly, there must be an interference fit between the rivet and the rivet hole of the connection plate, leading to minimal or no stress on the rivet head arc transition.
Observations show that the joint between the two connecting plates in the straight section of the rivet is severely deformed, indicating a deviation in the coaxiality of the mounting holes between the frame and the skin, resulting in abnormal mounting stresses on the rivet.
Under the combined effect of abnormal assembly stress and airflow vibration stress, the rivet suffers from fatigue cracking.
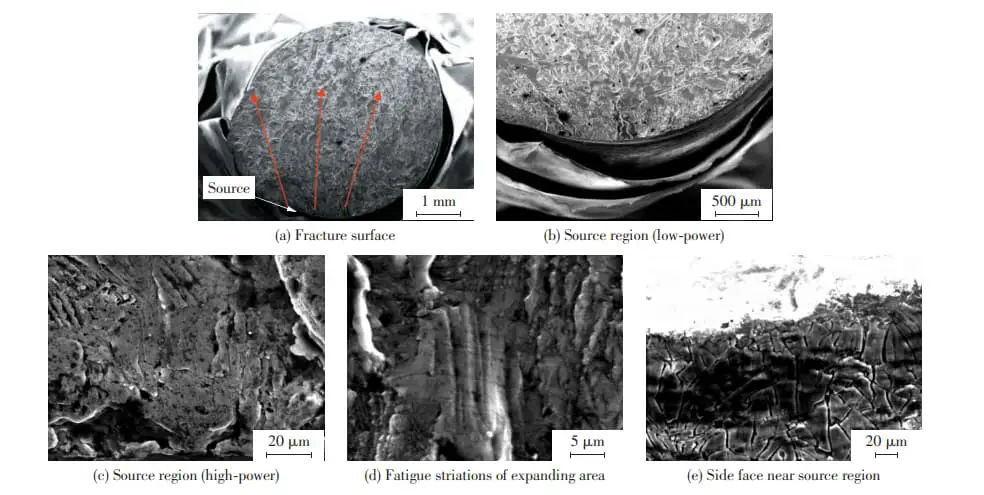
The surface of a fractured rivet exhibits a large line source, and the size of the source area can indicate the magnitude of the initial stress to some extent, allowing a preliminary assessment that the initial stress that led to the rivet fracture was significant.
The crack in the rivet is fully expanded and the fatigue area covers more than 95% of the total fracture area, suggesting that the initial stress in the rivet was substantial but the expansion stress was relatively low.
Because the fracture location of the rivet is at the stress concentration point at the arc transition of the rivet head, when the alternating stress is low, its fatigue crack may also have line source characteristics. Therefore, it is necessary to quantitatively reconstruct the fracture surface to deduce the comprehensive initial stress that the rivet withstood.
In normal operations, the rivet is interference fit and the stress at the arc fracture position is low or non-existent under force.
However, the rivet is susceptible to fatigue fractures, mainly due to the alternating bending stress it undergoes in the arc of the rivet head, caused by the up and down movement of the connecting plate, leading to the formation of a semi-surface crack. elliptic. .
When referencing the stress intensity factor model of “semi-elliptical surface crack under uniform tension and bending” in the literature, the model assumes a round rod specimen with diameter D that contains semi-elliptical surface cracks. The major axis of the crack is 2a, the semi-minor axis of the crack depth is b, and the stress intensity factor of the front edge of the crack under uniform stress and bending stress σ is calculated using the bending condition of the center of the voltage intensity factor model (as shown in Fig. 4).
Therefore, the stress intensity factor at each point on the front edge of the crack is:


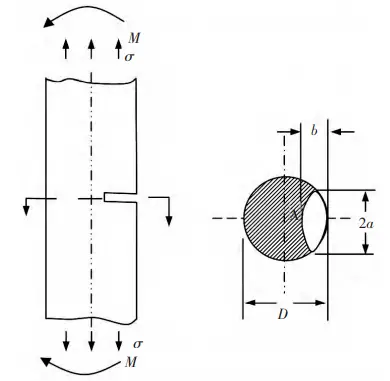
Fig.4 Sample model of round column, half-ellipse surface crack and uniform stress
See Table 1 and Figure 5 for comprehensive stress data from quantitative rivet analysis.
As shown in Fig. 5, the maximum comprehensive equivalent stress decreases continuously with an increase in crack length, and the reduction rate also decreases.
Given limited data, we conservatively estimated initial fracture stress by fitting a linear regression between crack length and stress data, yielding the equation Y=273-10.5x.
When x = 0, Y = 273 MPa, representing the maximum comprehensive equivalent stress at the start of the rivet, which is approximately 70% of the tensile strength (390 MPa) of LY10CZ aluminum alloy.
It is important to note that the rivet material is LY10 aluminum alloy and experiences a fatigue stress rating of R=-1. The cen material constants were not found, so we used the crack growth constant to the stress ratio of LY12 aluminum alloy (R = 0.25) for reverse inference in quantitative estimation.
Note that there may be errors in the maximum initial comprehensive equivalent voltage value.
The main focus of this study is to present the stress analysis method.
Table 1 results of quantitative analysis of rivet fatigue stress
No. | BA | B/mm | s | S/µ | △σ/MPa | σ max. /MPa |
1 | 0.31 | 0.53 | 0.987 | 0.08 | 200.9 | 267.9 |
two | 0.71 | 1.40 | 0.782 | 0.08 | 192.5 | 256.7 |
3 | 0.81 | 1.78 | 0.782 | 0.10 | 191.5 | 255.4 |
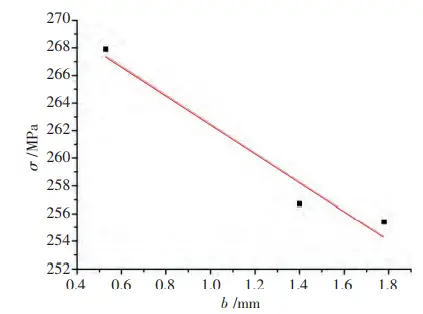
Fig.5 Linear adjustment of length and tension
As the crack propagates and the vibration displacement of the upper and lower connecting plates remains constant, the stress in the rivet gradually decreases, as does the stress at the crack tip. This corresponds to 95% of the entire fatigue range of rivet crack propagation.
Consequently, rivet fracture is a fatigue fracture characterized by a high initial stress but a relatively low expansion stress.
3. Conclusion
- Rivet fracture is due to fatigue.
- The mounting hole between the riveted frame and the skin has coaxiality deviation, and the main cause of fracture is due to improper mounting and stress caused by airflow vibration.
- Through a combination of quantitative analysis and fracture surface estimation, it was quantitatively determined that rivet fatigue has a higher initial stress and a lower expansion stress.