Selection of power source for arc welding
Selection of the power source for arc welding is a critical part in determining the electrical performance of the welding equipment (welder). Although arc welding power sources have some degree of universality, different types of arc welding power sources vary in structure, electrical performance, and key technical parameters.
As shown in Tables 1 and 2, there are significant differences in characteristics and economics between AC arc welding power sources and DC arc welding power sources. Therefore, only reasonable selection can ensure the smooth running of the welding process, which is economical and achieves good welding results.
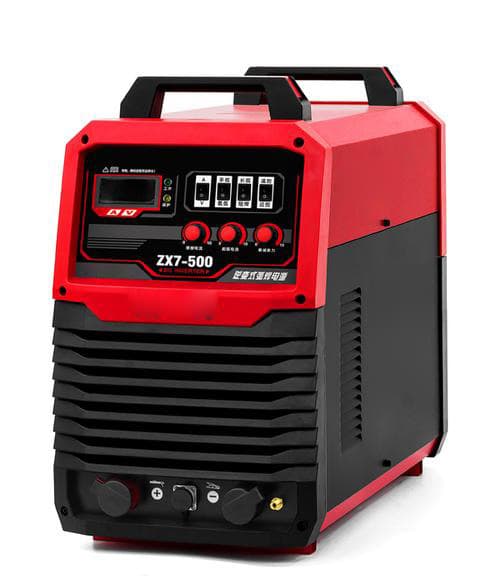
Generally, the power source for arc welding should be selected based on the following aspects:
- (1) Welding materials and workpiece materials;
- (2) Type of welding current;
- (3) Welding process method;
- (4) Arc welding power source power;
- (5) Working conditions and energy saving requirements;
- (6) Importance and economic value of the piece.
Table 1: Comparison of the characteristics of power sources for AC and DC arc welding.
Item | Alternating current | Direct current |
Arc stability | low | high |
Polarity interchangeability | anything | to have |
Influence of magnetic bias | small | more |
No-load voltage | higher | Lower |
Electric shock hazard | bigger | smaller |
Construction and maintenance | Simpler | More complex |
Noise | not big | Large generator, small rectifier and smaller inverter |
Cost | low | high |
Power supply | General single phase | Three-phase general |
Weight | lighter | Heavier and lighter inverter |
Table 2: Comparison of energy source savings for AC and DC arc welding.
Main indicators | DC Arc Welding Alternator | AC Arc Welding Generator | Arc Welding Rectifier | arc welding inverter |
Electricity consumption per kilogram of welded metal | 6~8kW.h | 3~4 kW.h | two. | |
0.3~0.6 | 0.65~0.90 | 0.6~0.75 | 0.8~0.9 | |
0.6~0.7 | 0.3~0.6 | 0.65~0.70 | 0.85~0.99 | |
No-load power factor | 0.4~0.5 | 0.1~0.2 | 0.30~0.4~ | 0.68~0.86 |
no-load power consumption | 2~3kW | 0.2 kW | 0.38~0.46kW | 0.03~0.1kW |
Manufacturing material consumption | 100% | 30~35% | 35~40% | 8~13% |
Man-hours for production of power source for arc welding | 100% | 20~30% | ||
Price | 100% | 30~40% | ||
Area occupied by each unit | 0.5~ 0.7m2 | 0.2~ 0.3m2 | 0.4~ 0.9m2 | 0.11~ 0.13m2 |
1. Selection of welding current type:
There are three basic types of welding current: DC, AC and pulse, and corresponding arc welding power sources are available: DC arc welding power source, AC arc welding power source and welding power source pulsed arc.
In addition, there is also the option of arc welding inverters. We should choose the type of arc welding power source reasonably according to the technical requirements, economic effects and working conditions.
2. Selection of welding process method and arc welding power source:
(1) Manual arc welding:
Acid electrodes are used for welding general metal structures, and dynamic iron core, dynamic coil or arc welding transformers with tap changer (such as BXl-300, BX3-300-1, BX6-120-1, etc. .) can be used.
Alkaline electrodes are used for welding most important structural steel and DC arc welding power sources such as arc welding rectifiers (such as ZXG-400, ZXl-250, ZX5-250, ZX5-400, ZX7-400, etc.), can be used. All of these arc welding power sources must have a downward characteristic.
(2) Submerged arc welding:
A larger capacity arc welding transformer is generally selected. If superior product quality is required, arc welding rectifiers or rectangular wave AC arc welding power sources should be used. These power sources for arc welding must generally have an external downward characteristic.
For constant speed wire feeding, a smoother descent characteristic is preferred, and for variable speed wire feeding, a steeper descent characteristic is preferred.
(3) Tungsten inert gas welding (TIG welding):
TIG welding requires an arc welding power source with constant current characteristics, such as an arc welding inverter or an arc welding rectifier. For welding aluminum and its alloys, an AC arc welding power source is preferred, preferably a rectangular wave AC arc welding power source.
(4) CO2 gas shielded welding and inert gas welding with melting electrode:
In these cases, arc welding rectifiers and arc welding inverters with flat characteristics (for constant speed wire feed) or downward characteristics (for variable speed wire feed) can be used. For high-quality TIG welding, a pulsed arc welding power source must be used.
(5) Plasma arc welding:
An arc welding rectifier or arc welding inverter with constant current characteristics is preferred. If using melting electrode plasma arc welding, select an arc welding power source according to the requirements of melting electrode inert gas welding.
(6) Pulsed arc welding:
Pulsed plasma arc welding and pulsed TIG welding must use a pulsed arc welding power source. In high demand situations, arc welding inverters or transistor pulse arc welding power sources are preferred.
As can be seen from above, a welding process method does not necessarily need to use a specific type of arc welding power source. However, the arc welding power source selected must meet the electrical performance requirements of that welding process method.
These include external characteristics, regulation performance, no-load voltage and dynamic characteristics. If some electrical performance does not meet the requirements, it can also be achieved through modification, which just shows that arc welding power sources have a certain degree of universality.
3. Selection of power source for arc welding
(1) Approximate determination of arc welding power source power
The main specification for welding is welding current. To put it simply, the capacity can be selected based on the required welding current by referring to the number on the back of the arc welding power source model. For example, the number “300” in BXl-300 represents that the rated current of the power supply is 300A.
(2) Allowable welding current under different load duration rates
As discussed in Chapter 2, the maximum output current of an arc welding power source is primarily determined by the allowable temperature rise.
Therefore, when determining the allowable welding current, the load duration rate must be considered. Under the rated load duration rate, the arc welding power source will not exceed its allowable temperature rise when working at the rated welding current.
When the load duration rate changes, the maximum current that the arc welding power source can use without exceeding the allowable temperature rise can be converted based on the principle of equal heat generation and achieve the same rated temperature.
4. Choose the power source for arc welding according to working conditions and energy saving requirements.
Under normal production conditions, single-station arc welding power sources should be used as much as possible. However, in large welding shops such as shipbuilding shops, where there are many welding stations and they are concentrated, multi-station arc welding power sources can be used.
Because DC arc welding power sources require a resistor box for current sharing, which consumes a lot of power, they should be used as little as possible.
In maintenance welding work, where the weld length is not long and the continuous use time of the power source is short, arc welding power sources with lower rated continuous load rating can be selected, such as those with ongoing rate of 40%, 25%, or up to 15%.
Because arc welding power sources consume a lot of energy, for the purpose of energy saving, high-efficiency and energy-saving arc welding power sources should be selected as much as possible, such as arc welding inverters, followed by arc welding rectifiers and transformers. Unless specifically required, DC arc welding generators do not need to be used.
Installation and use of power source for arc welding
1. Installation of power source for arc welding
Taking the most widely used manual arc welding power source as an example, this section will introduce the knowledge about installing an arc welding power source. The main circuit schematic diagram of the manual arc welding machine is shown in Figure 8-1.
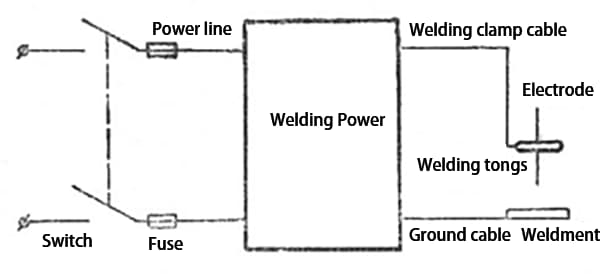
As can be seen from the diagram, in the main circuit, in addition to the power supply for arc welding, there are also accessories such as cables, fuses, switches, etc.
- Selection of cables, fuses and switches
(1) Cable Selection
Cables include power lines from the grid to the welding power source and welding cables from the welding power source to the welding torch and workpiece. When selecting power cords, the following factors should be considered:
- Material: Aluminum cables should be chosen whenever possible, as long as they do not affect performance.
- Voltage rating: AC cables with a withstand voltage of 500V are generally selected as power lines.
- Usage environment: Outdoor cables should be able to resist sun, rain and moisture, while indoor cables should have better insulation. Flexible multiconductor cables should be used in situations where mobility is required, while single-core cables should be used in fixed installations.
- Cable cross-sectional area: The allowable current density and cross-sectional area must be determined based on the allowable temperature rise. The allowable current density depends on the material properties and heat dissipation conditions.
When selecting welding cables, wear resistance, ability to withstand mechanical forces and flexibility of movement must be considered. The cross-sectional area of the welding cable can be selected according to Table 8-1 based on the current and cable length. Different types and models of power lines and welding cables can be selected according to the purpose and Table 8-1.
(2) Fuse Selection
Common fuses include tube, plug-in, and spiral fuses. The rated current of the fuse must be greater than or equal to that of the fuse.
For arc welding transformers, rectifiers and inverters, as long as the rated current of the fuse is slightly higher than or equal to the rated primary current of the welding power source, it is sufficient. For DC arc welding generators, because the starting current of the motor is very large, the fuse cannot be selected according to the rated current of the motor, but must be chosen based on the following formula:
Fuse rated current = (1.5~2.5) x Motor rated current If there is a start, the coefficient in the above formula should be 1.5.
(3) Key Selection
Common switches include knife switches and iron shell switches.
The rated switch current for arc welding transformers, rectifiers, inverters, transistorized arc welding power supplies, and rectangular wave AC arc welding power supplies must be greater than or equal to the rated current. The rated switch current for arc welding generators is three times the rated motor current.
- Arc welding power supply installation
(1) Arc welding rectifiers, inverters and transistorized arc welding power supplies
- Pre-installation inspection
The. For new power supplies that have not been used for a long time, the insulation must be checked before installation, which can be done using a 500V megohmmeter. Before testing, however, the rectifier or silicon rectifier element and the high-power transistor group must be short-circuited with wires to prevent the silicon element or transistor from being broken by overvoltage.
The insulation resistance between the welding circuit and the secondary winding of the box must be greater than 2.5M. The insulation resistance between the rectifier and the primary and secondary windings of the box should not be less than 2.5M.
The insulation resistance between the primary and secondary windings should not be less than 5M. The insulation resistance between the control circuit that is not connected to the primary and secondary circuits and the chassis or other circuits should not be less than 2.5M.
B. Check for any damage or loose connections inside the power supply due to transportation before installation.
- Precautions during installation
The. Check whether the power supply capacity of the network is in accordance with the rated capacity of the arc welding power source and whether the selection of switches, fuses and cables is correct and the insulation of the cables is good.
B. The wire section and length of the power line and welding cable line must be appropriate to ensure that the voltage drop of the power line does not exceed 5% of the mains voltage and the total voltage drop of the cable line of the welding circuit does not exceed 4V under rated load.
- Grounding and Zero Connection of the Box. If the network supply is three-phase with four wires, the housing must be connected to neutral. If the first is a three-phase system without earthing, the box must be earthed.
- Pay attention to moisture-proof measures.
- Install in a well-ventilated and dry place.
(2) Arc welding transformers
When wiring, pay attention to the primary voltage value marked on the factory nameplate. The primary voltage can be 380V, 220V or dual use. When installing multiple units, they must be connected to the three-phase mains separately to obtain the maximum possible balance of the three-phase load. Other matters are the same as arc welding rectifiers.
(3) DC Arc Welding Generators
In addition to the matters mentioned above, it is also important to highlight the following:
- If the network capacity is large enough, it can be started directly. If the network capacity is not sufficient, voltage reducing starting equipment must be used.
- For large-capacity arc welding power supplies, to ensure that the grid voltage is not affected by other high-capacity electrical equipment or to avoid affecting the work of other electrical equipment, special lines must be installed.
The use of power source for arc welding
Correct use and maintenance of arc welding power sources not only ensures their normal working performance, but also extends their service life.
Common sense for use and maintenance
(1) Before use, the arc welding power source must be inspected in accordance with the product manual or relevant national standards, and a certain knowledge base must be established to ensure correct use.
(2) Before welding, check whether all connections are correct, especially whether the welding cable joint is tight to prevent overheating or burning.
(3) Do not move or open the top cover of the machine when it is connected to the power supply or during welding.
(4) When operating without load, first check whether the sound is normal, and then inspect whether the cooling fan is blowing normally and the direction of rotation is correct.
(5) The machine must be kept clean and dust must be removed regularly with compressed air. Regular electrical testing, inspection and maintenance are also required.
(6) The necessary rigorous management and utilization systems must be established.
Parallel use of arc welding power sources:
When the welding current of one arc welding power source is insufficient, multiple arc welding power sources can be connected in parallel for use. However, it is important to ensure balanced current, polarity and other related issues.
Arc welding power source modification
Arc welding power sources have a certain versatility. However, when its versatility cannot meet certain requirements of the welding process, arc welding power sources of similar performance that can be easily modified can be selected and modified for use.
Arc welding rectifiers can also be easily modified to achieve the desired performance. For example, magnetic amplifier type arc welding rectifiers used for manual arc welding have an external downward characteristic.
To use them for CO2 gas shielded welding with thin wire and constant speed power, simply remove or increase the resistance of the magnetic amplifier's three internal bridge resistors to make it a CO2 arc welding power source. Thin thread with a characteristic plane or slow descending characteristic.
If it is necessary to use it as a power source for pulsed arc welding, it can be modified by changing the magnetic amplifier to an impedance imbalance, or by reducing the voltage of a certain phase, or by changing the constant excitation current to a constant excitation current. pulsed excitement.
When necessary, arc welding generators can also be modified. For example, by removing the degaussing winding of the AXl-500 and changing the parallel excitation winding to a series excitation winding, the downward characteristic can be changed to a flat characteristic and so on.
Energy Conservation and Safe Use of Electricity
Electricity Conservation
- Replace arc welding generators with high-efficiency, energy-saving arc welding power sources
To save electricity, it is better to replace DC arc welding generators with silicon arc welding rectifiers or thyristor arc welding rectifiers. With the improvement of the development and production level of arc welding inverters, its reliability and performance have reached the level of traditional arc welding power sources such as thyristor type, and even foreign arc welding power sources of first line.
In addition, they have good dynamic characteristics and welding process, save electricity and materials, and are affordable. They should be widely promoted and used.
- Improve power factor
As we all know, arc welding transformers are transformers with high leakage inductance or large reactance. The power factor is as low as about 0.4 ~ 0.6, so it is necessary to improve the power factor to reduce the reactive power supply to the grid and improve the power quality.
There are two ways to install capacitors to compensate power factor:
(1) Factories that extensively use arc welding power sources, such as shipyards, metal structure factories, bridge factories, etc., can adopt centralized compensation.
(2) For rural and small enterprises that do not have centralized compensation facilities, capacitors can be installed on arc welding transformers for compensation, as shown in Figure 3-1.
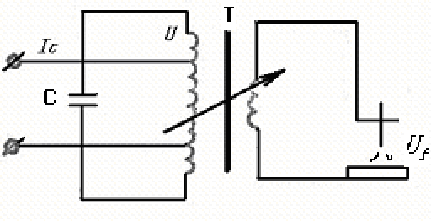
- Install “Energy Saving Devices”
Installing “energy-saving devices” on arc welding transformers not only has a certain effect on reducing no-load power loss, but also can effectively prevent electric shock.
Therefore, it can also be called “electric shock prevention and energy saving device”. These products are available both domestically and internationally.
Electrical Safety
Arc welding power source is an electrical equipment that can easily cause accidents to personnel and equipment if necessary safety measures are not taken or precautions are not taken. This can lead to irreparable losses, so it should be avoided as much as possible.
- Measures to protect personal safety
The no-load voltage of a manual arc welding power source is generally between 60-90V, and welders often operate in high humidity environments, which increases the risk of electric shock. The danger is especially greater when welding in high places and inside metal containers. An electrical current flowing through the heart of a human body can be fatal if it reaches a few milliamps. The following methods can be used to avoid electric shock:
(1) Avoid contact with energized parts:
- The energized terminals of the arc welding power source must be covered with protective covers;
- There must be good insulation between the energized parts of the arc welding power source and the machine housing;
- The connecting wires of the welding tongs must not be bare wires and must be insulated. The welding tongs themselves must have good insulation.
(2) Limit the voltage that people can come into contact with: Sometimes it is difficult to avoid contact with certain living objects, so it is necessary to limit the voltage of these living objects to ensure safety. For example, the maximum allowable value for the no-load voltage of an arc welding power source is specified; the AC voltage of the control circuit should not be more than 36V and the DC voltage should not be more than 48V; the working light voltage should not be more than 12V.
(3) Increase insulation resistance: The resistance of the human body is mainly in the skin, and the resistance value is related to whether the skin is dry or not. In summer, sweating reduces the human body's resistance, which increases the risk of electric shock. In addition, the resistance of the human body is also related to the state of health, mental state and emotional state. There are many ways to increase insulation resistance, such as using rubber gloves when contacting high voltage; wear leather gloves when performing manual arc welding; wear rubber shoes when working outdoors on rainy days; sitting on a wooden stool while working; and use a rubber lid when working inside a metal container.
(4) Ground or zero the machine housing: Under normal circumstances, the machine housing is not energized. However, the insulation between the energized parts within the arc welding power source and the machine housing can be broken, causing the machine housing to become energized due to contact. The following measures must be taken to ensure personal safety:
- Grounding protection: The central point of the electrical network is not grounded, therefore grounding protection must be used, which is connected to the ground wire through the grounding screw on the machine housing. Underground water pipes or metal structures (but not underground gas pipelines, to avoid explosions) can be used as a ground wire. It is best to install a grounding electrode, which can be a metal pipe (with a wall thickness of more than 3.5 mm, a diameter of more than 25-35 mm and a length of more than 2 m) or a flat iron (with a thickness of more than 4 mm, cross-sectional area greater than 48 and length greater than 2 m), buried in the ground to a depth of at least 0.5 m.
- Protective zero connection: This type of electrical network is a three-phase four-wire system, and the machine housing must be connected to the neutral line through the grounding screw. When contact is made with the housing, a large short-circuit current will flow through the neutral line and the machine housing,
- causing the fuse connected to the arc welding power source to blow immediately, cutting it off from the mains.
- Automatic voltage reduction device
The automatic voltage reduction device is actually an “energy saving device” mentioned earlier. There are many types of these devices and Figure 4 shows an example.
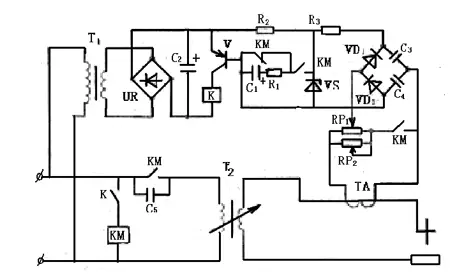
- Remote control device with anti-electric shock and energy saving functions
Arc welding transformers are usually manually adjusted directly on the transformer housing to adjust the welding current. When the workpiece is far from the arc welding transformer, this adjustment method becomes inconvenient.
Therefore, remote control can be used, which can be achieved by an electric motor, gearbox and relevant remote control circuit. The welder carries an adjusting rod with him and uses the welding tongs to hold the adjusting rod at the work site to control the forward and reverse rotation of the electric motor, thereby transmitting the current adjusting mechanism and changing the welding current. This remote control device is not only easy to operate, but also has anti-electric shock and energy-saving features, which can achieve the purpose of safe work and energy saving.
(1) Principle of Anti-Electric Shock and Energy Saving
When control transformer T2 is turned on, V1 is turned off, V2 is saturated and conducts, V3 is turned off, and relay K3 is not energized. Normally open contact K3-2 prevents AC contactors KM1 and KM2 from being energized. At this time, the arc welding transformer T1 is not connected to the 380V power grid and is in a safe, energy-saving non-working state.
(2) Principle of remote welding current adjustment
When the adjustment rod is placed between the welding tongs and the workpiece, if the diode on the adjustment rod is pointed toward the workpiece, a “negative at the bottom and positive at the top” DC voltage is generated at the R25 by rectifying the 24V AC voltage through the diode.
This voltage generates a current in the junction circuit VD18->R20->Emitter of V5->VD19->R25, causing V5 to saturate and conduct. K2 is then energized and contact K2-2 closes, causing the electric motor M to rotate forward, and the dynamic iron core (or winding) of arc welding transformer T1 to move outward or downward to increase the welding current. On the other hand, if the diode on the adjustment rod is pointed toward the welding tong, V4 conducts, K1 is energized, and contact K1-1 closes, causing M to rotate back and decrease the welding current.
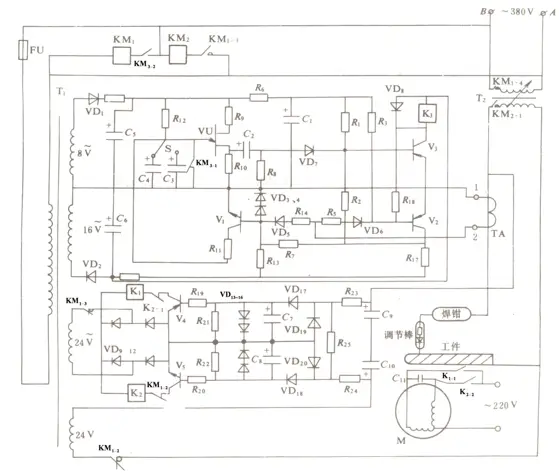
- Selection of low voltage no-load inverter arc welder
Due to the good dynamic characteristics of inverter arc welders, a relatively low no-load voltage is required. Furthermore, the voltage can be easily reduced to the desired value through simple methods without significantly affecting the arc performance.