Industrial rotating machines rely on bearings to reduce friction, energy consumption and heat generation, while supporting increasingly heavier applied loads at higher speeds and with a greater degree of precision. Thousands of bearing types and styles offer a wide range of solutions suitable for applications across a variety of industries.
However, some application conditions will present specific challenges for bearings, posing potential threats to optimizing bearing performance and service life. In this context, several special bearing coatings have been developed to address specific threats and, in the process, help improve bearing performance and machine operation.
Most types of bearings can be coated (by the manufacturer) to serve in new applications or as drop-in replacements in existing machines. In both cases, the bearing dimensions remain unchanged. Depending on the formulation and purpose, bearing coatings can reduce the harmful effects of vibration, improve performance under low lubrication conditions, help prevent adhesive wear (stain damage), improve corrosion resistance and reduce friction.
Wear resistance
Bearings in service may be subject to wear for a variety of reasons, whether due to poor lubrication conditions (associated with high temperatures and/or low lubricant viscosities), sudden changes in load or speed, stationary vibration and/or particulate or liquid contaminants . All of this can lead to significantly shorter bearing (and machine) life over time.
Providing an effective defense against premature bearing wear and other conditions, a patented wear-resistant carbon coating, just a few microns thick, can be applied to the internal bearing contact surfaces (rolling elements and/or races). Coated steel surfaces retain the toughness of the underlying material by adopting the enhanced hardness, reduced friction properties and enhanced wear resistance of carbon coating, which has a similar appearance and texture to silicon nitride (ceramic).
The most common execution involves coating the rolling elements of the bearings, using traditional steel tracks. During the break-in period, small amounts of coating material will transfer to the counter surfaces. This transfer strengthens friction reduction and improves resistance to wear and grinding damage.
Typical wear coating applications include industrial fans, gearboxes, paper machines and compressors, among many others. Such a coating can especially withstand a variety of severe operating conditions, including scratches from stains, insufficient lubrication film, sudden load changes, light loads, rapid speed changes, vibrations and oscillations, and high operating temperatures. The coating's unique properties further improve high-speed capabilities and help tolerate contaminated and/or poor lubrication conditions.
Expected results for the coated bearing include greater reliability, longer service life and a reduced chance of premature failure due to friction, wear, surface tension and fatigue.
Eddy current insulator
When an AC or DC stray current in an electric motor or generator uses a bearing as a path to ground, electrical erosion of the bearing will likely occur. The most common causes of stray electrical current leading to potential erosion are asymmetry in a motor's magnetic circuit, unshielded power cables, and/or fast-switching pulse-width modulation (PWM) frequency converters used in inverters variable frequency drive (VFD).
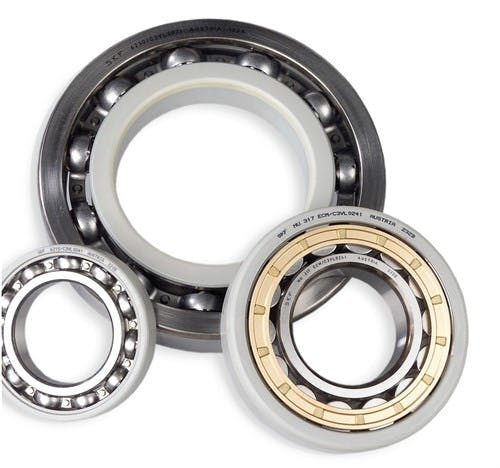
A variety of bearings that integrate special coatings
Stray electrical currents can damage bearings in at least three ways:
Excessive current erosion. When electrical current passes through a bearing from one ring to another via rolling elements, it creates a process similar to electric arc welding, concentrating a high current density on a small contact surface. As a result, localized extreme temperatures cause melting and welding of the bearing material, which creates microcraters, corrosion and changes in the grain structure of the bearing steel.
Current leakage erosion. When a low-intensity stray electrical current passes through a bearing, the transfer of electrical energy causes damaging arcs within the bearing. Secondary bearing damage may appear as grooves (“washboard”) in the bearing races and/or rolling elements. The surface finish of rolling elements may become dull and dull in appearance. The extent of damage will depend on bearing type, bearing size, electrical speed, bearing load, speed and lubricant.
Lubricant degradation. High bearing temperatures caused by electrical current can cause a lubricant's additives to carbonize or burn, resulting in faster wear of the additives. The increase in temperature also causes rapid aging and oxidation of the lubricant. In the case of grease lubrication, the grease becomes black and hard. This rapid breakdown drastically reduces the life of the grease and, in turn, the life of the bearings due to wear and surface fatigue (chipping).
Once bearing damage due to electrical erosion begins, increased noise levels, reduced bearing lubricant effectiveness, increased heat and excessive vibration can occur, all threatening to drastically reduce a bearing's operating potential.
Bearings that suffer damage from electrical erosion will operate with increased noise, vibration, heat generation and friction. Degraded lubricant will increase wear and surface tension in the bearing and significantly reduce bearing performance and life.
One way to prevent damage from stray electrical currents passing through a bearing is to introduce an insulating coating to the bearing “from the outside”, as an alternative to using bearing materials with insulating properties such as ceramics. This can be achieved with a special protective coating on the bearing bore or outer diameter surface.
The coating's thin aluminum oxide layer provides an electrical insulation function to the bearing to form a superior barrier against arcing and damaging erosion of bearing surfaces. The coating is applied (by the manufacturer) to the bearing bore or outer diameter, depending on the bearing size, using a plasma spray technique. After application, the coating will not alter the overall dimensions of the bearing and will not require equipment modifications.
To add value, bearings with this type of protective coating are further treated with a unique sealing resin to protect them from moisture and water penetrating the coating, potentially reducing their effectiveness. This is particularly relevant for applications located in humid operating environments.
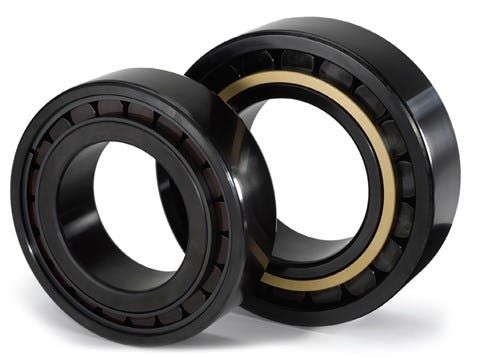
Expansion options
The world of specialty bearing surface treatment coatings continues to expand in response to the specific challenges of each application.
For example, black oxide applied to the rings and/or rolling elements of a bearing can promote greater reliability and performance in particularly heavy-duty applications such as industrial gearboxes. The treatment process, which involves a chemical reaction on the surface layer of the bearing steel, is carried out (by the manufacturer) in an alkaline aqueous saline solution at defined temperatures. Up to 15 different dipping steps create a thin, dark black surface layer of FE3O4 iron oxide that provides improved performance for a wide variety of bearing types and sizes.
This treatment can increase the uptime of machines, improving resistance to corrosion and adhesive wear (clogging); improved performance under low viscosity lubrication conditions; limit the risk of wear, microcracks and fissures; reduce potential damage caused by aggressive oil additives; and reducing the effects of friction and wear.
As another example, a zinc chromate coating for particularly corrosive environments can serve as an alternative to stainless steel bearings. Ready-to-assemble ball bearing units, often subjected to highly corrosive conditions, are prime candidates for this bearing coating treatment.
All of these solutions demonstrate that specialty coatings can be practical and cost-effective options to help maximize operational performance and bearing life, even under adverse conditions. Consulting a qualified and experienced bearing manufacturer can help you identify and choose the most suitable coating for your application challenge.