Common Types of Level Gauges
- Magnetic Level Gauge
- Floating Ball Level Gauge
- Steel Tape Level Gauge
- Radar Level Meter
- Magnetostrictive Level Gauge
- RF Intake Level Meter
- Tuning fork level gauge
- Glass Plate/Glass Tube Level Gauge
- Hydrostatic Level Gauge
- Pressure Level Transmitter
- Capacitive Level Meter
- Smart Electric Float Level Meter
- Buoyancy Level Meter
- Floating Level Transmitter
- Electrical Contact Level Meter
- Magnetic Bicolor Electronic Level Gauge
- External Measurement Level Gauge
- Hydrostatic Level Gauge
- Ultrasonic Level Meter
- Differential Pressure Level Gauge (Double Flange Level Gauge)
Working Principles of Common Level Gauges
1. Magnetic Plate Level Meter
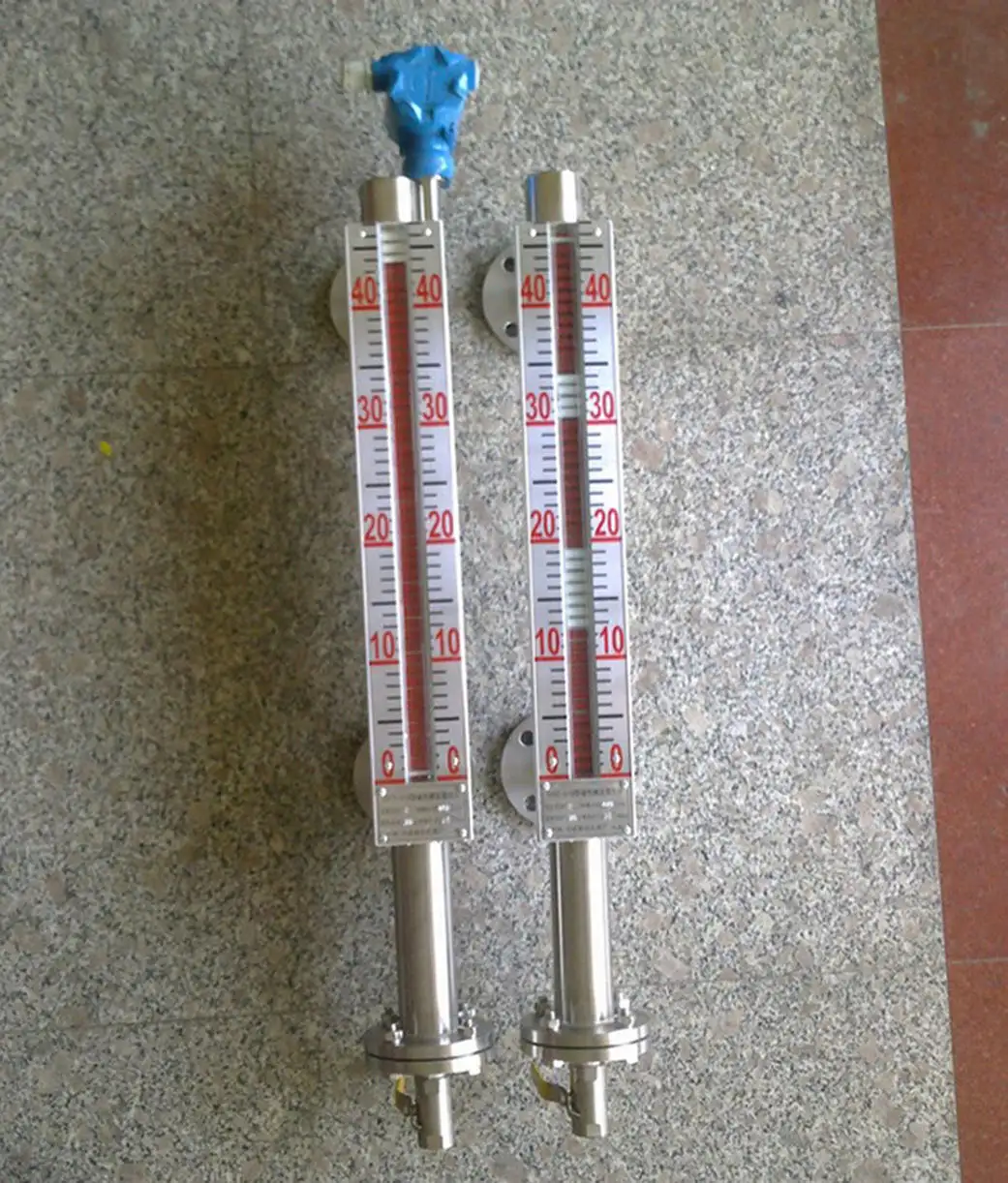
Also known as magnetic float level meter or magnetic column level meter.
This meter operates on the principle of a communicating vessel, developed based on the principles of buoyancy and magnetic coupling.
As the liquid level in the container being measured increases or decreases, the permanent magnetic steel inside the float transmits to the magnetic column indicator panel through the magnetic coupling, causing the red and white column to rotate 180°.
When the liquid level rises, the column changes from white to red, and when the liquid level drops, it changes from red to white. The intersection of red and white on the panel indicates the actual height of the liquid level in the container, thus displaying the liquid level.
2. Floating level gauge
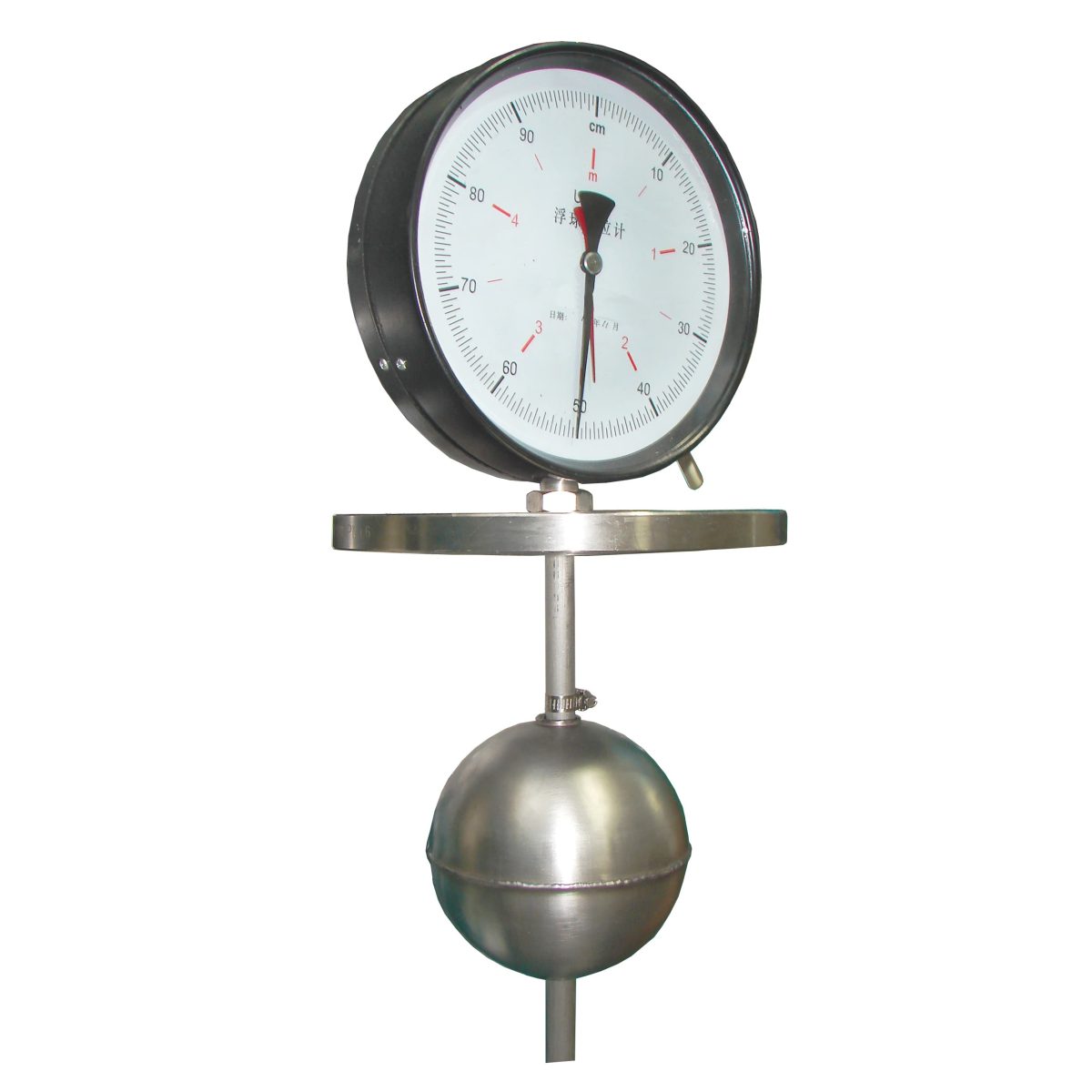
Floating level gauge mainly operates based on buoyancy and static magnetic field principles.
The location of the float containing a magnet (hereinafter referred to as the float) within the medium being measured is influenced by buoyancy: changes in the liquid level lead to changes in the position of the magnetic float.
The magnet inside the float interacts with a sensor (magnetic reed switch), causing the number of components (such as fixed resistors) connected in the circuit to vary, subsequently changing the electrical quantities within the instrumentation circuit system.
Essentially, changes in the position of the magnetic buoy trigger variations in electrical quantities. The state of the liquid level within the container is reflected by detecting these changes in electrical quantity.
3. Tape Level Gauge
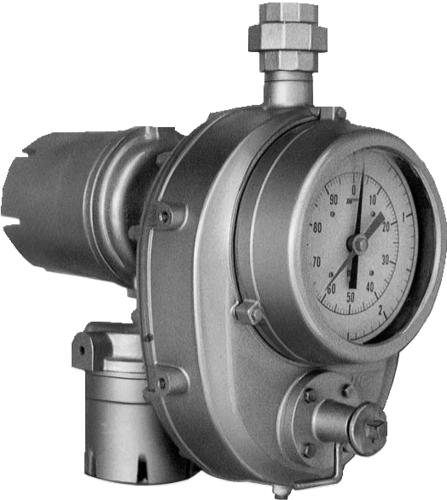
The tape level gauge is designed and manufactured based on the principle of mechanical balance.
When the liquid level changes, the original mechanical balance is disturbed by the buoyancy affecting the float, reaching a new balance through the movement of the steel ribbon.
The liquid level detection device (float), based on the state of the liquid level, triggers the movement of the steel tape. This displacement drives the rotation of the transmission shaft through the movement of the steel ribbon, which in turn acts on the counter to display the liquid level.
4. Radar Level Meter
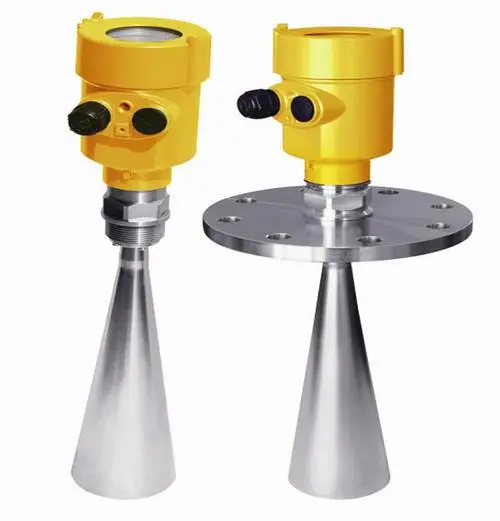
The radar level gauge is a measuring instrument based on the principle of time of flight. Radar waves travel at the speed of light and their travel time can be converted into a level signal by electronic components.
The probe emits high-frequency pulses that propagate along a cable-type probe.
When these pulses encounter the surface of the material, they are reflected back and received by the receiver inside the instrument, which then converts the distance signal into a level signal.
5. Magnetostrictive level gauge
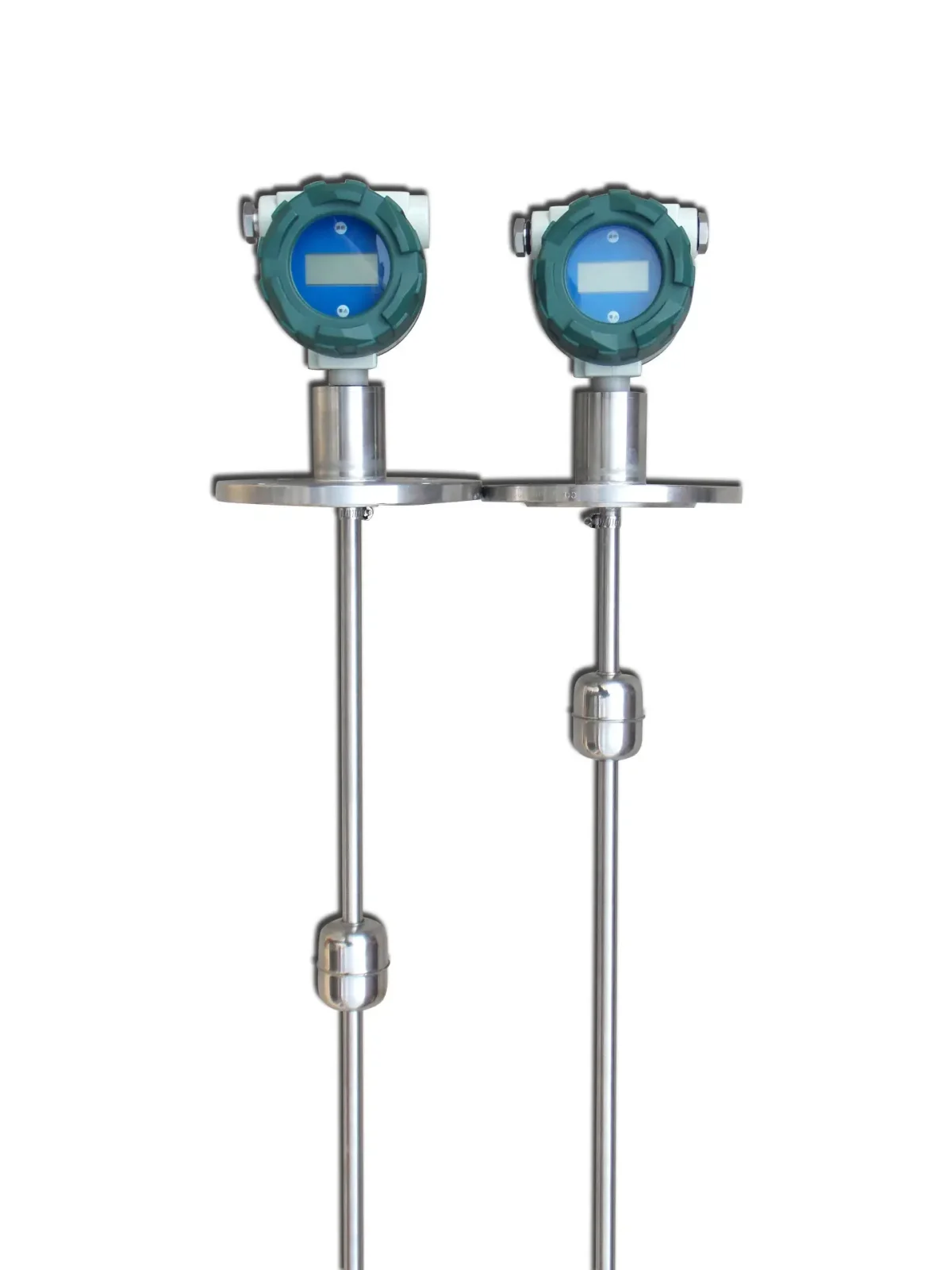
During operation of the magnetostrictive level gauge sensor, the circuitry within the sensor induces a pulse current in the waveguide wire.
This current, when propagating along the wire, generates a magnetic field of pulsed current around it.
The level gauge sensor probe is equipped with a float, which moves up and down with changes in the liquid level along the probe. Inside the float is a set of permanent magnetic rings.
When the magnetic field of the pulse current meets the magnetic field of the float's magnetic rings, the magnetic field around the float changes, causing a twisting wave pulse at the position of the float on the waveguide wire made of magnetostrictive material.
This pulse is transmitted back along the waveguide wire at a fixed speed and detected by the sensing mechanism. By measuring the time difference between the pulse current and the torsional wave, the precise location of the float, and therefore the position of the liquid level, can be accurately determined.
6. Radio Frequency Admittance Level Meter
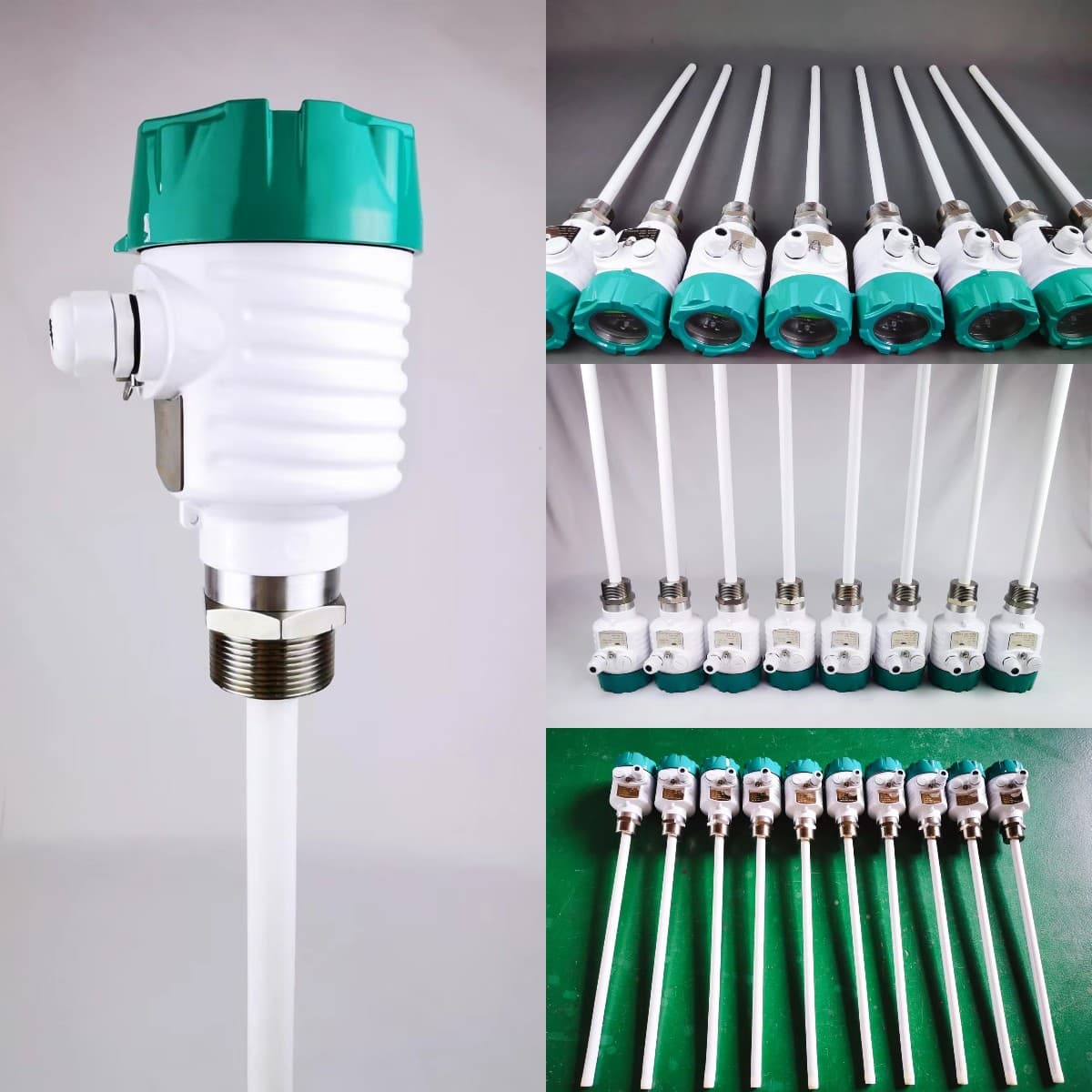
The radio frequency admittance level meter consists of a sensor and a control instrument.
The sensor, which can be rod, coaxial or probe-cable type, is installed in the upper part of the silo. The pulse card inside the sensor converts level changes into pulse signals sent to the control instrument.
The control instrument, after computer processing, converts these signals into displayed engineering units, thus carrying out continuous level measurement.
7. Tuning fork level gauge
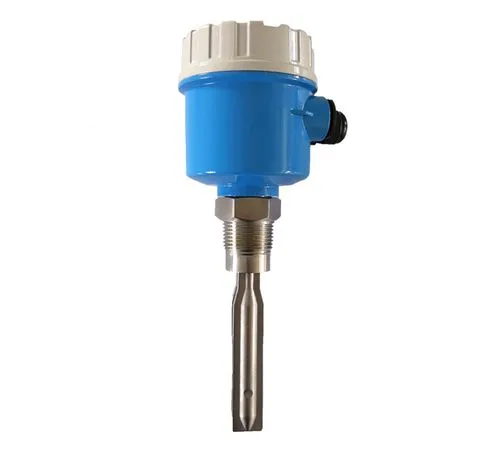
The working principle of the tuning fork level controller involves a pair of piezoelectric crystals mounted on the base of the tuning fork, causing the tuning fork to vibrate at a certain resonant frequency.
When the tuning fork comes into contact with the medium being measured, its frequency and amplitude change.
These modifications are detected and processed by an intelligent circuit, which converts them into a switching signal.
8. Glass plate level meter (glass tube level meter)
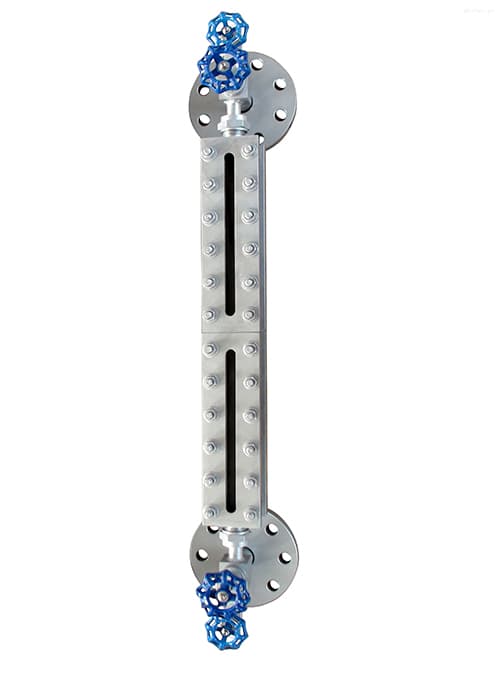
The Glass Plate Level Gauge is a device that establishes a connection with the vessel through a flange, allowing immediate reading of the height of the liquid level inside the vessel through the glass plate.
9. Pressure Level Transmitter
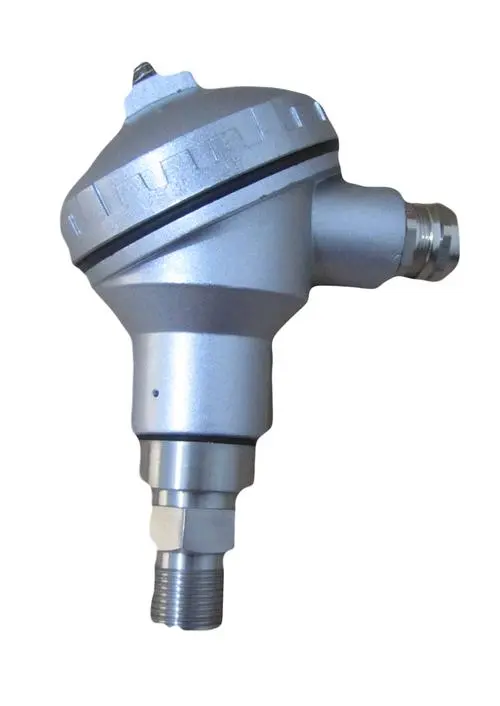
The pressure type level gauge employs the principle of static pressure measurement.
As the level transmitter is immersed in a specific depth of the liquid under inspection, the sensor faces the pressure exerted by the fluid. This pressure is then introduced into the sensor's positive pressure chamber via a stainless steel gas guide.
At the same time, the atmospheric pressure Po above the fluid surface is connected to the negative pressure chamber of the sensor to compensate the Po at the back of the sensor. This allows the sensor to measure pressure as: ρ.gH By measuring pressure P, the depth of the fluid can be determined.
10. Capacitive Liquid Level Meter
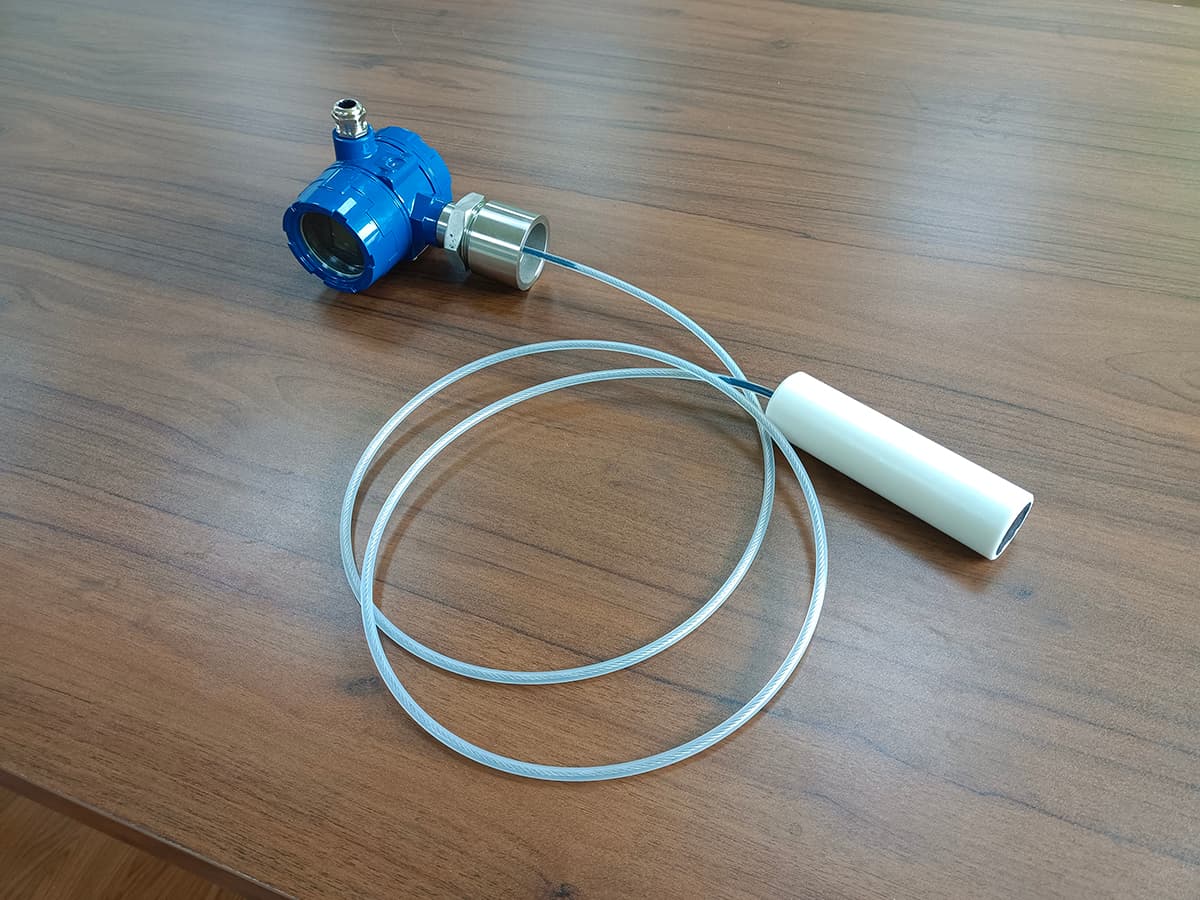
The capacitive liquid level gauge measures the height of liquid surfaces by detecting changes in capacitance. It incorporates a metal rod inserted into a liquid-filled container, where the rod functions as one pole of the capacitor and the container wall as the other.
The dielectric between the two poles consists of the liquid and the gas above it. Given the different dielectric constants ε1 for the liquid and ε2 for the gas above (where ε1 > ε2), the overall dielectric constant – and therefore the capacitance – increases as the liquid level increases.
Conversely, when the liquid level drops, both the dielectric constant and capacitance decrease.
Thus, the Capacitive Liquid Level Meter can measure the height of liquid levels by observing changes in the capacitance between its two poles.
11. Smart Electric Float Level Meter
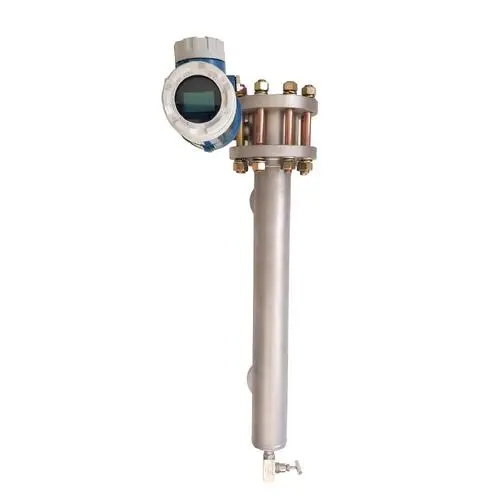
Smart Electric Float Level Gauge is a liquid level measuring instrument designed based on Archimedes principle and magnetic coupling principle.
The instrument can be used to measure liquid levels, interface levels and densities, being responsible for outputting upper and lower limit alarm signals.
12. Floating Level Gauge
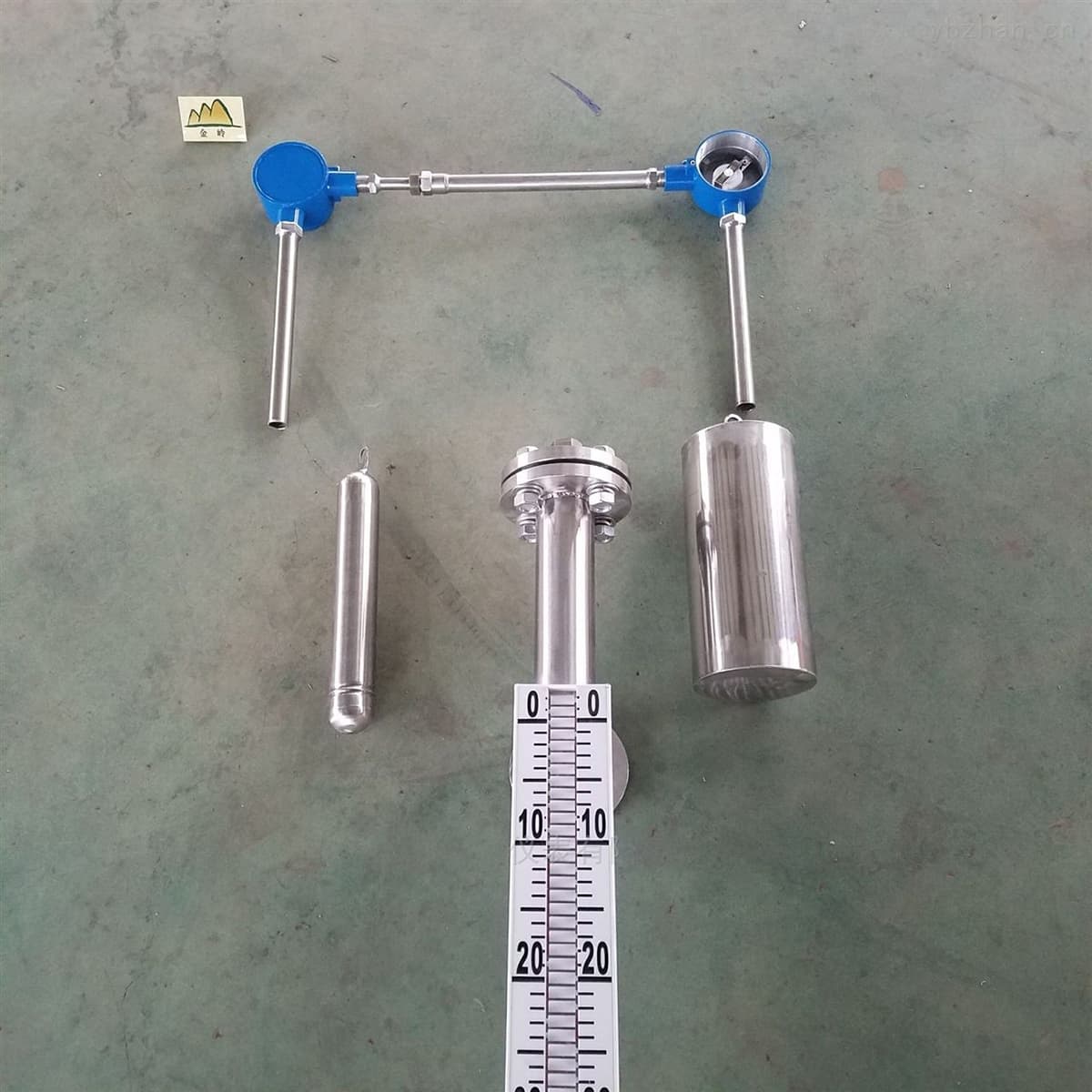
This is designed and manufactured using the principle of mechanical balance. When the liquid level changes, the original mechanical balance is disturbed by the buoyancy acting on the float, reaching a new balance through the movement of the steel ribbon (rope).
The liquid level detection device (float) moves the steel tape (rope) according to the liquid level status, and the displacement transmission system drives the indicator in place through the movement of the steel tape (rope ), thereby displaying the liquid level status on the display device.
13. Floating Level Transmitter
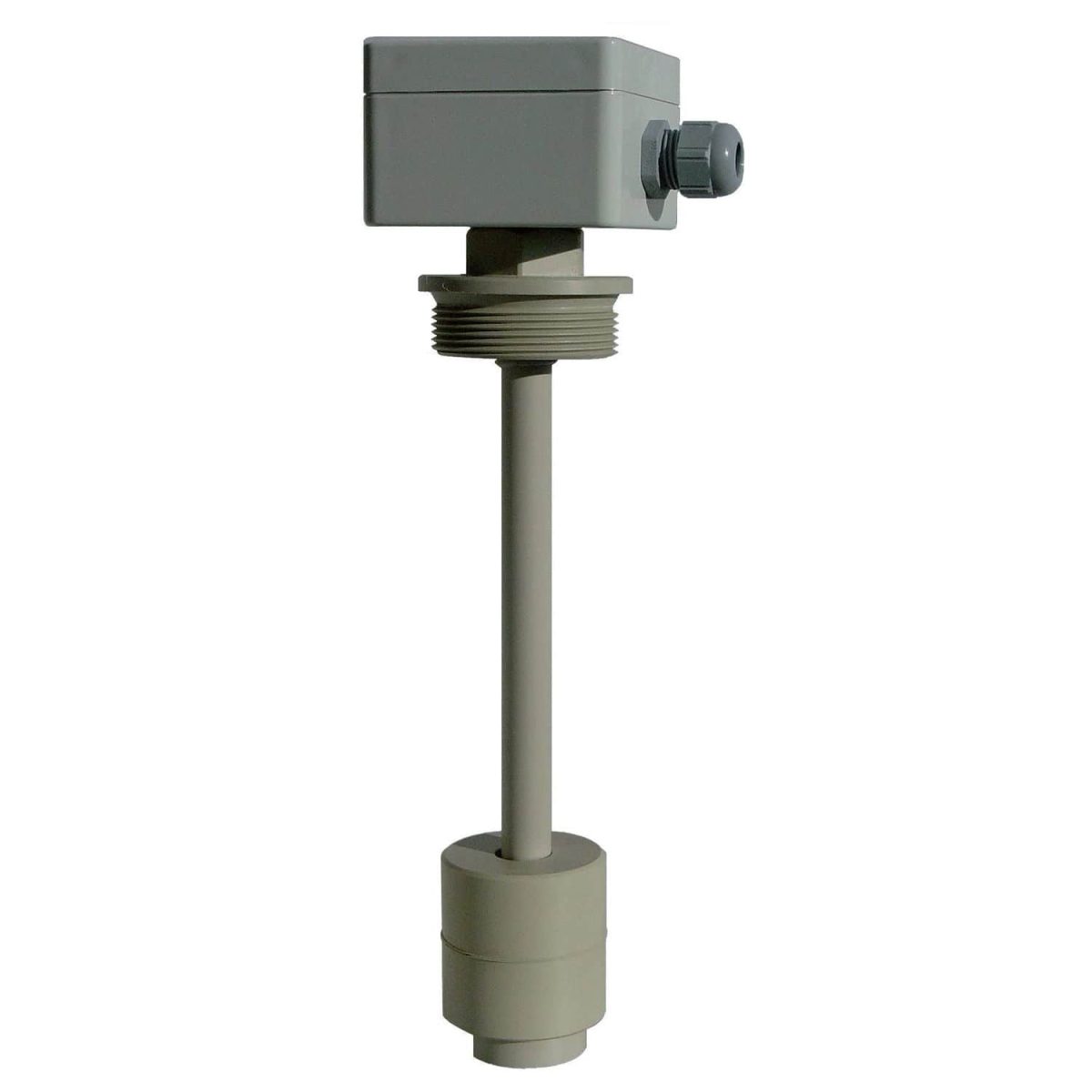
The float is submerged in the fluid inside the float chamber, rigidly connected to the torque tube system. The force supported by the torque tube system is the net weight of the float minus the buoyancy it receives. Under this combined force, the torque tube rotates to a certain extent.
Variations in the position, density or level of the liquid within the float chamber cause changes in the buoyancy experienced by the submerged float, thus altering the angle of rotation of the torque tube.
This change is transmitted to the sensor rigidly connected to the torque tube, causing a variation in the output voltage, which is then amplified by electronic components and converted into a current output of 4-20mA.
The floating level transmitter uses a microcontroller and associated electronic circuitry to measure process variables, provide current output, drive LCD displays, and provide HART communication capabilities.
14. Electrical contact level meter
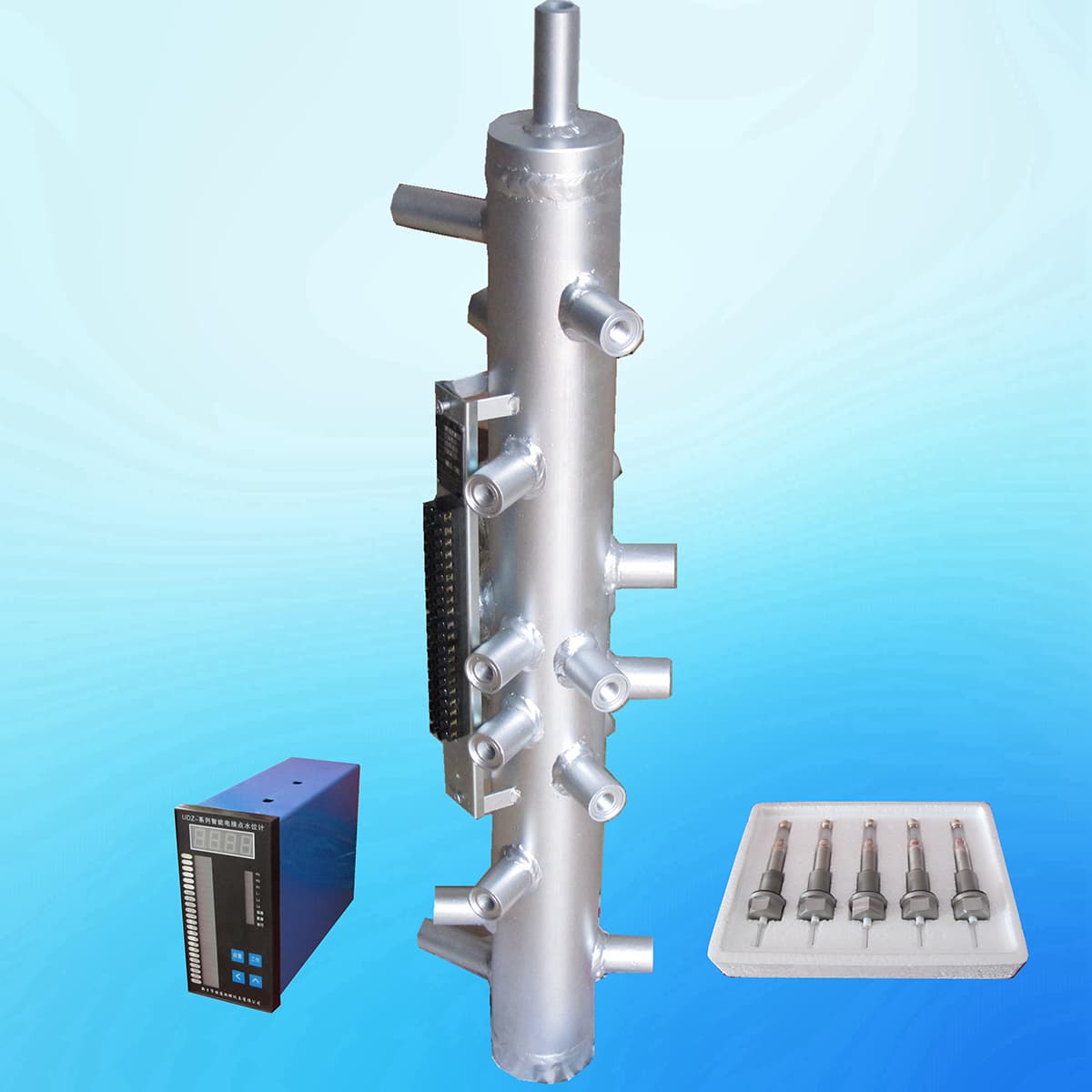
The electrical contact level meter is designed based on the different resistivities of water and steam.
The impedance of the electrode to the body of the measuring tube is lower in water and higher in steam.
As the water level changes, the number of electrodes in the water varies, resulting in a change in the resistance value.
This information is transmitted to the secondary instrument, thus enabling functions such as water level display, alarms and protective interlocks.
15. Magnetic Bicolor Electronic Liquid Level Gauge
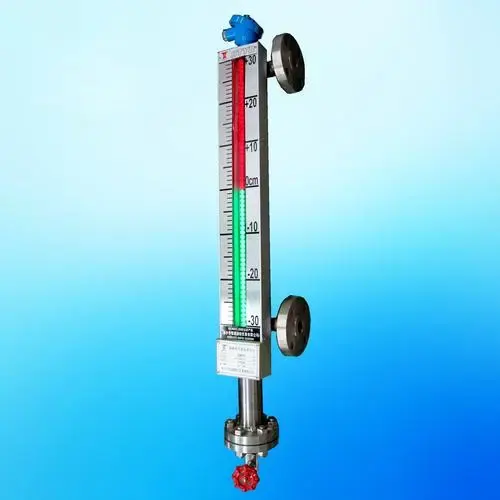
The magnetic two-color electronic liquid level gauge is made of high-quality stainless steel and imported electronic components.
The display section uses high-brightness bi-color LED light-emitting diodes to form a columnar screen.
Through the red and green changes of the LED light column, it can achieve upper and lower limit alarms and control of liquid levels.
16. External level gauge
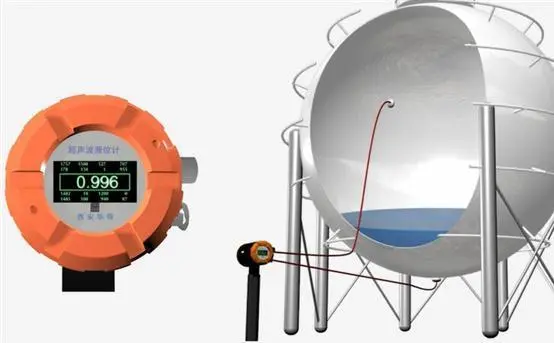
The external level gauge is an instrument that uses sonar ranging principles and “microvibration analysis” technology to measure the liquid level outside the container.
Two compact ultrasonic external level gauge sensors are installed, one at the bottom of the tank and the other on the side wall to compensate for density variation.
The signal from the level gauge's external sensor is transformed by a microprocessor and sent to a local display or user control system, allowing calculation of the height and volume of the liquid inside the tank.
17. Hydrostatic level gauge
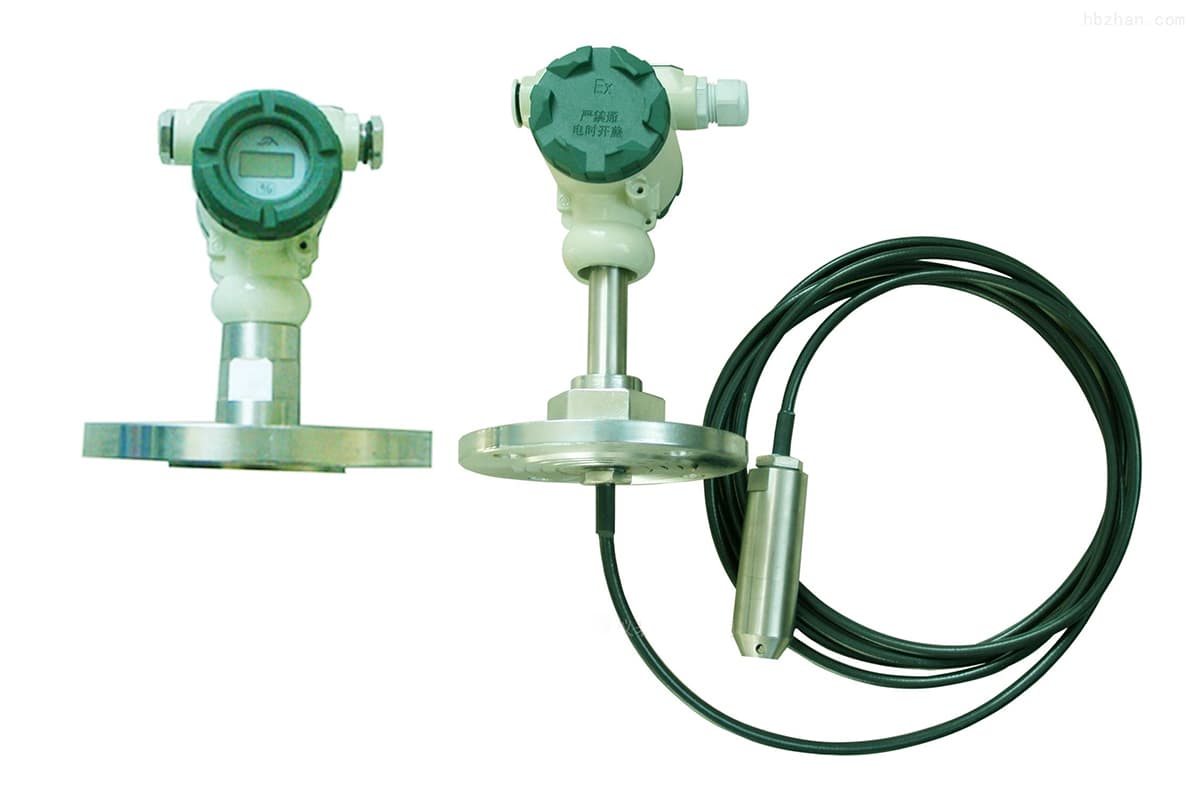
The hydrostatic level transmitter, encapsulating a diffuse core filled with silicon oil within a stainless steel housing, has a protective cap on the front end to protect the sensor diaphragm while ensuring that the fluid makes smooth contact with the diaphragm.
Waterproof wiring is sealed to the outer casing and a vent tube inside the cable maintains connection to the outside environment, all within an internal structure designed for anti-condensation.
18. Ultrasonic Liquid Level Meter
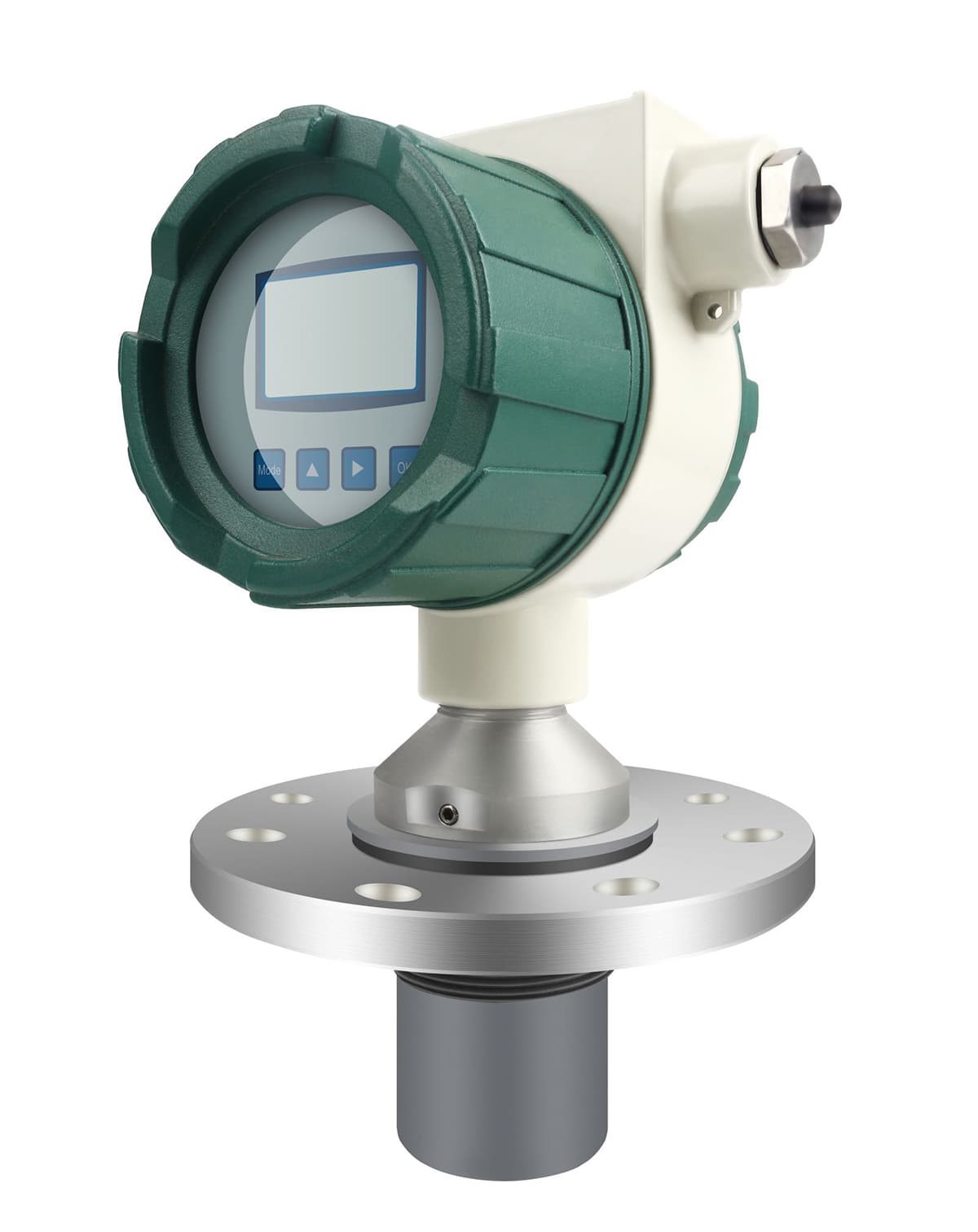
The ultrasonic liquid level/position meter comprises a complete ultrasonic sensor and control circuit.
The ultrasonic waves emitted by the sensor are reflected off the surface of the liquid, and the time required for these waves to return is measured and used for calculations.
Adjustments are made for the influence of temperature on the process of transmitting ultrasonic waves through a temperature sensor, which is then converted into the distance between the liquid surface and the ultrasonic sensor.
This information is displayed on an LCD and outputs a 4mA-20mADC analog signal, allowing remote reading of the instrument on site.
19. Differential pressure liquid level gauge (double flange level gauge)
A differential pressure liquid level transmitter operates by measuring the pressure difference between two points and then converting this data into an electrical signal that is relayed to electrical components in the control room.
This type of gauge is primarily used to measure liquid levels in sealed pressure vessels. The magnitude of the differential pressure corresponds to the height of the liquid level.
The level is determined by measuring the differential pressure between the gas and liquid phases using a differential pressure gauge.