The fit between bearings, shafts and bearing housings is a critical aspect in bearing applications and is a topic of great interest to bearing users. In practical work, the principle of pattern selection for adjustment can satisfy application needs.
However, many engineers are curious about how this tuning selection principle is calculated, and some even prefer to do the calculations themselves.
In fact, the basic calculation method for selecting the fit between bearings, shafts and bearing housings can be accomplished by recombining prior knowledge from the perspective of how the fit impacts bearing operation.
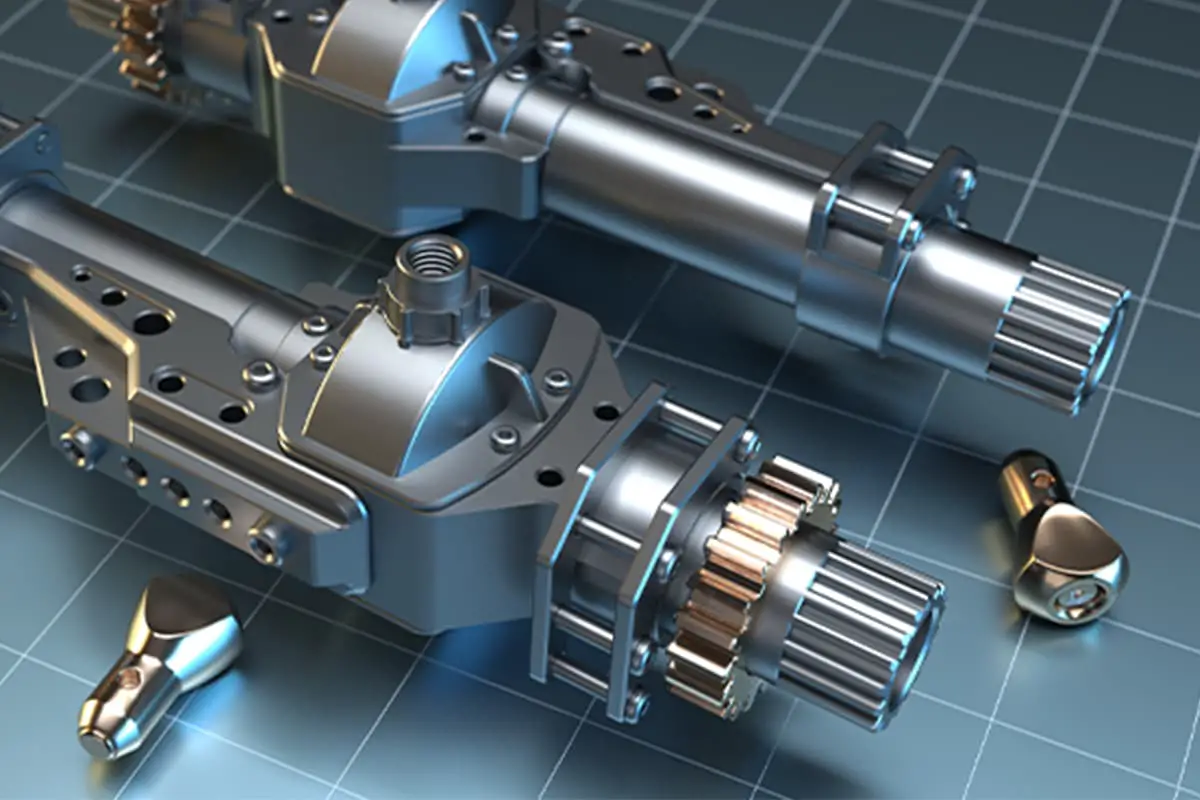
I. Boundary conditions for bearing, shaft and bearing housing adjustment calculation
Before performing the calculation to select the fit between bearings, shafts and housings, it is crucial to understand the real purpose of this calculation, which provides a clear definition of the calculation method and boundary conditions.
Purpose of adjustment
The general purpose of the fit between the bearing inner ring and the shaft, and the bearing outer ring and the bearing housing, is to ensure that there is no relative movement between the bearing and the shaft, and between the bearing housing. and the bearing outer ring.
Relative movement in the circumferential and axial directions must be avoided. It is important to understand that it is challenging to prevent relative movement by adjustment alone, so other external design elements must be used to ensure this.
For example, shaft shoulders and bearing housing steps are used to limit axial movement; designs using locking grooves or sealing rings to stop relative movement in the circumferential direction. These methods usually serve as a complement when adjustment alone cannot fulfill its function, avoiding relative movements and guaranteeing a certain degree of reliability.
Adjustment Limits
From the above discussion, we know that there is a minimum limit in assembling bearings and related components. If the fitting force is too small, it will cause relative movement between the bearing and the fitting surface, ceasing to fulfill its fixing function. This situation increases the likelihood of bearing displacement.
From the point of view of mechanical parts design theory: the tighter the fit, the greater the fit force and, consequently, the more significant the “clamping” effect. However, there is a certain degree of “loose” and “tight” fit.
If the fit is too tight, although it can ensure the relative fixation of the mating surface, other dimensions within the bearing and the steel material of the bearing itself will be affected. Therefore, fixation cannot be achieved by simply increasing the adjustment.
On the other hand, in some applications, the “fitting force” generated between the two mutually fitted surfaces will vary (e.g. in some vibration situations). Therefore, when the tendency for relative movement of the mating surface occurs during the above-mentioned force fluctuations, the required “fitting force” needs to be greater.
Why should it be bigger? Because we need to ensure that during the “strong” and “weak” stages of relative motion, this mating force will not cause relative movement of the mating surfaces. For example, if we select the “adjustment force” according to the “strong” stage of relative motion, when the vibration changes to the “weak” stage, this “adjustment force” will appear very large.
On the other hand, if we choose the “adjustment force” according to the “weak” stage, then when it vibrates to the “strong” stage, we will find that this force is insufficient and relative movement of the adjustment surfaces has occurred. Therefore, to meet the peak, a larger adjustment force is inevitably used.
This is why in vibration conditions it is generally recommended to employ a tighter fit for the related bearing.
This is what we need to discuss: there is an upper limit to the assembly of bearings and related components. If the adjusting force is too large, it will cause changes to other properties of the bearing, causing problems.
In conclusion, the ultimate goal in selecting bearing tolerance fits is the fit force between the bearing fit surfaces. If this mounting force is too small, it can easily lead to relative movement (displacement) between the bearing and the mounting components; If the mounting force is too large, it may affect the internal performance of the bearing (clearance too small, preload increased).
This is the basic limit and calculation direction for selecting tolerance fits of the bearing shaft and bearing housing.
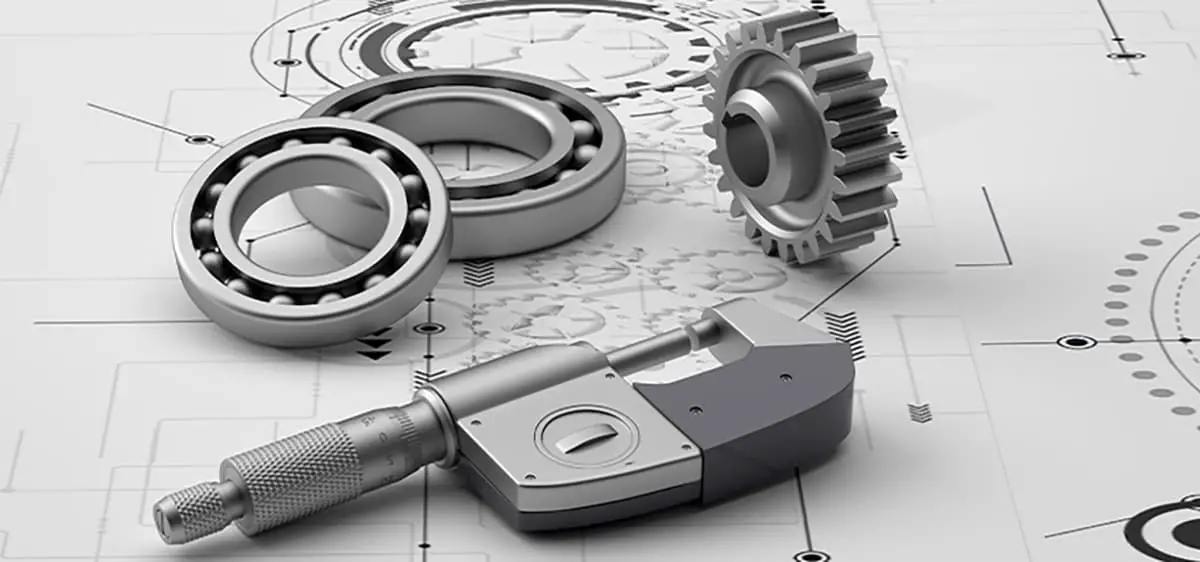
II. Minimum fitting force between bearing, shaft and bearing housing
Example: General bearing of horizontal internal rotation motor.
The shaft system of a common horizontal internal rotation motor has the simplest bearing configuration. Other types of axis systems can be inferred based on this model.
When a horizontal internal rotation motor is running, the rotating shaft of the motor will rotate with the inner ring of the bearing. Thus, “rotation” is transmitted from the motor rotor to the bearing inner ring, implying that the bearing inner ring rotates passively. This being the case, a significant amount of driving force is required.
This driving force encompasses the force required for the bearing's inner ring, together with the rolling element and cage, to rotate. Therefore, the most demanding operating condition to trigger bearing inner ring rotation is during starting or speed changes. At this point, the minimum driving force is the centrifugal acceleration multiplied by the mass of the bearing's inner ring.
The situation is slightly different when the bearing rotates at a uniform speed.

When a bearing moves at a constant speed, the driving force required is minimal, mainly to overcome the friction between the internal rolling elements and the raceways. Therefore, the required “fitting force” is much simpler than the above-mentioned scenario.
Looking at two different applications, engines that frequently change speed or start require much more “tuning force” than those that run at a constant speed. This explains why the previously recommended tuning charts often require a tighter fit for variable speeds or frequent startup situations.
So far, we have discussed the “spinning ring” – the inner ring. But what about the outer ring? In horizontal internal rotor motors, the bearing outer ring is normally stationary and the bearing housing is also fixed.
The only force that tends to rotate the bearing outer ring is the rolling of the bearing rollers within the outer ring. Under normal circumstances, there is generally only rolling friction between the bearing rollers and the outer ring, so this adjusting force only needs to exceed this rolling friction to overcome the rotation tendency of the bearing outer ring.
In addition, because the rolling friction is very small, the mounting force required by the bearing to overcome the rolling friction is also very small. However, there is sliding friction between the bearing housing and the bearing outer ring.
At the same time, the radial load between the bearing outer ring and the bearing housing can be considered equal to the internal radial load of the bearing. Furthermore, there is a lubricant inside the bearing race to reduce friction, while there is no lubricant between the bearing outer ring and the bearing housing.
In conclusion, by safely positioning the bearing outer race within the bearing housing, the tendency for relative movement can be overcome through sliding friction. Therefore, it is easy to understand why the outer bearing race in a horizontal internal rotation motor is often loosely adjusted.
Returning to the main topic, it is quite simple to calculate the friction force exerted on the outer race of a bearing by rolling elements. Of course, my personal engineering experience suggests that such calculations are generally not necessary in practice, as standard fit selection tables are usually sufficient. Engineers curious to learn, however, may want to give it a try.
Here are some additional questions engineers should consider (the thought process was outlined above, just follow it):
1. Why does the fit need to be tightened under vibration conditions and the outer race needs to be tightened?
2. How should the tolerance setting be selected for a vertical motor?
3. How should the tolerance setting be selected for an externally rotating motor?
The above content did not provide answers to the above questions. Everyone is encouraged to think about this for themselves and I believe everyone can get the answers. (A little tip: consider elasticity.)
Under uniform motion, would the aforementioned outer race adjustment result in orbit?
III. Maximum interference fit between bearing, shaft and bearing housing.
We mentioned the maximum interference fit limit. If the interference is too great, it may cause changes in the performance of other bearings.
First of all, the most important factor is the change in the dimensions of the bearing itself. When the bearing is well adjusted, the internal clearance of the bearing will decrease. When the bearing clearance is too small, the bearing may seize. Therefore, the first requirement for tighter bearing fit is to satisfy the bearing residual clearance requirement.
These methods are commonly used in certain fields such as gearbox bearing application.
Secondly, the factors affected by tight fit are bearing materials such as inner ring cracking. This situation actually occurred in practical applications. However, generally, the bearing material impact occurs after the backlash effect.
II. Conclusion
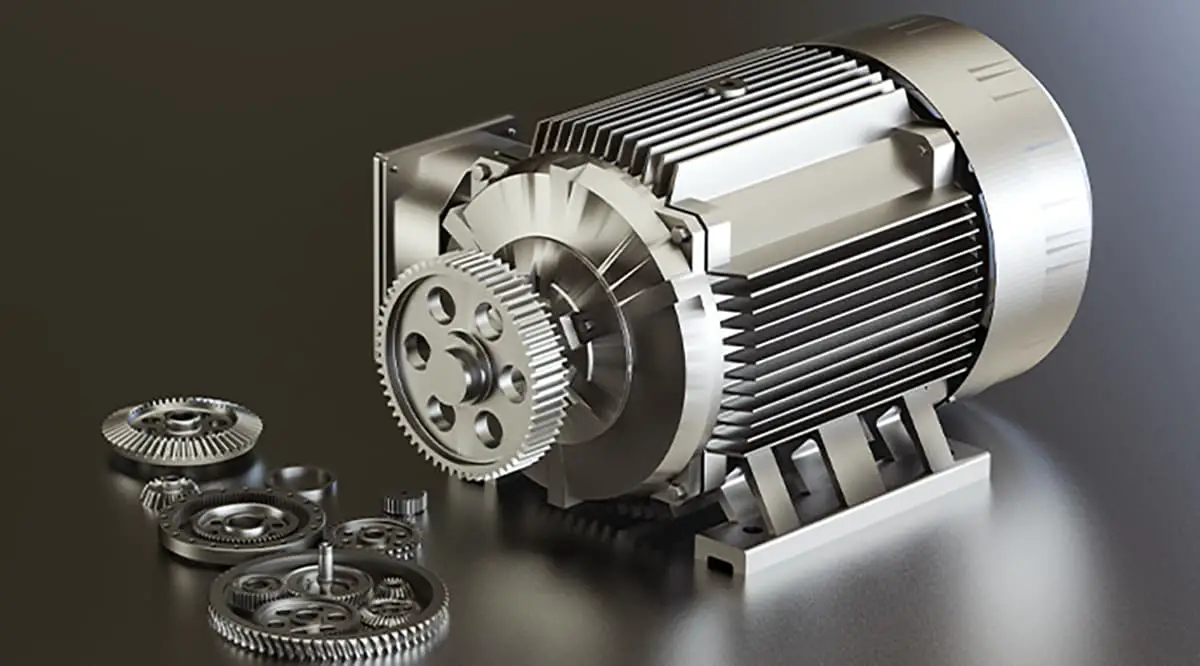
This article mainly discusses the basic adjustment calculation methods of bearings and related components.
However, it is crucial to understand that for engine bearing systems, these complex calculations are typically unnecessary. This is because the daily recommended tolerance adjustment tables have already considered the above-mentioned factors. Direct selection based on these principles is generally sufficient. We wrote this content to inform you how these benchmark results that we use daily are obtained.
Unless it is a very specific application or you are particularly passionate about understanding the theoretical process, we do not recommend that each adjustment selection undergoes such complex consideration.
Of course, for gearbox engineers, especially when calculating the preload of tapered roller bearings and angular contact ball bearings, such considerations become unavoidable and require careful understanding.