1. Introduction
According to the principle of three-point rounding, the sheet metal bending machine uses the rotary movement and relative position change of the work roll to achieve continuous elastic-plastic bending. This results in sheet metal bent into predetermined shapes, such as cylinders and arcs, as well as precision workpieces.
Plate bending machine is widely used in various industries, including boiler manufacturing, shipbuilding, petrochemical, metal structure and sheet metal forming machines.
Based on the number of rolls, plate calender can be classified into two-roll, three-roll and four-roll types, each with its unique characteristics.
Compared with the traditional two-roll type, the four-roll sheet metal bending machine has several advantages, including easier centering, a smaller residual straight edge, higher circular straightening accuracy and higher production efficiency.
Furthermore, the four-roll sheet metal calender is capable of performing final sheet preplexing and rolling of parts without the need for turning, making it increasingly important in sheet metal forming.
The machine is composed of an upper roller, a lower roller and two side rollers at the front and back. The upper roller rotates in a fixed position while the steel plate is fed by friction. The process of fixing, pre-plexing and rolling the steel plate is controlled by adjusting the position of the bottom roller and the two side rollers.
To increase the rolling accuracy of the steel plate, it is crucial to study the precise positions of the bottom roller and the two side rollers. Currently, the position control of these components is determined by the operator through repeated adjustments based on experience, and the rolling accuracy is monitored through continuous comparison and model checking, resulting in low accuracy and efficiency.
This paper proposes a calculation formula for the springback radius of curvature based on the springback theory and studies the position requirements of the bottom roll and the two side rolls in the steel plate rolling process. A mathematical model is established to calculate the positions of these components during alignment, preplexing and bending.
The study accurately determines the displacement of the bottom roller and front and rear side rollers during steel sheet rolling, providing accurate feeding data for digital control. The results of this method, verified through production practice, show consistency with practical applications, leading to better rolling precision and efficiency.
1. Process Flow of Four Roll Plate Bending Machine
1.1 Structure and working principle of four-roll plate bending machine
The four-roll sheet metal bending machine is composed of several main components, including the upper roller device, lower roller device, side roller device, tipping device, low rack, base, high rack and hydraulic pump station.
The upper roller serves as the driving roller and is rotated by a servo motor through a transmission device, with a fixed position. The bottom roller and side roller are driven rollers, whose rotation is driven by friction with the steel plate.
The lower roller is fixed on its bearing seat, which can move vertically in a sliding guide groove in the frame to accommodate different plate thicknesses. Side rollers are installed on side roller bearing seats.
To form the desired bending radius of the cylinder, the side roller bearing seat moves up and down in an inclined direction within the sliding guide groove, with a certain angle to the vertical direction.
The tipping and reset of the lower roller, side roller and upper roller are controlled by a hydraulic cylinder. The general structure of the equipment is represented in Figure 1.
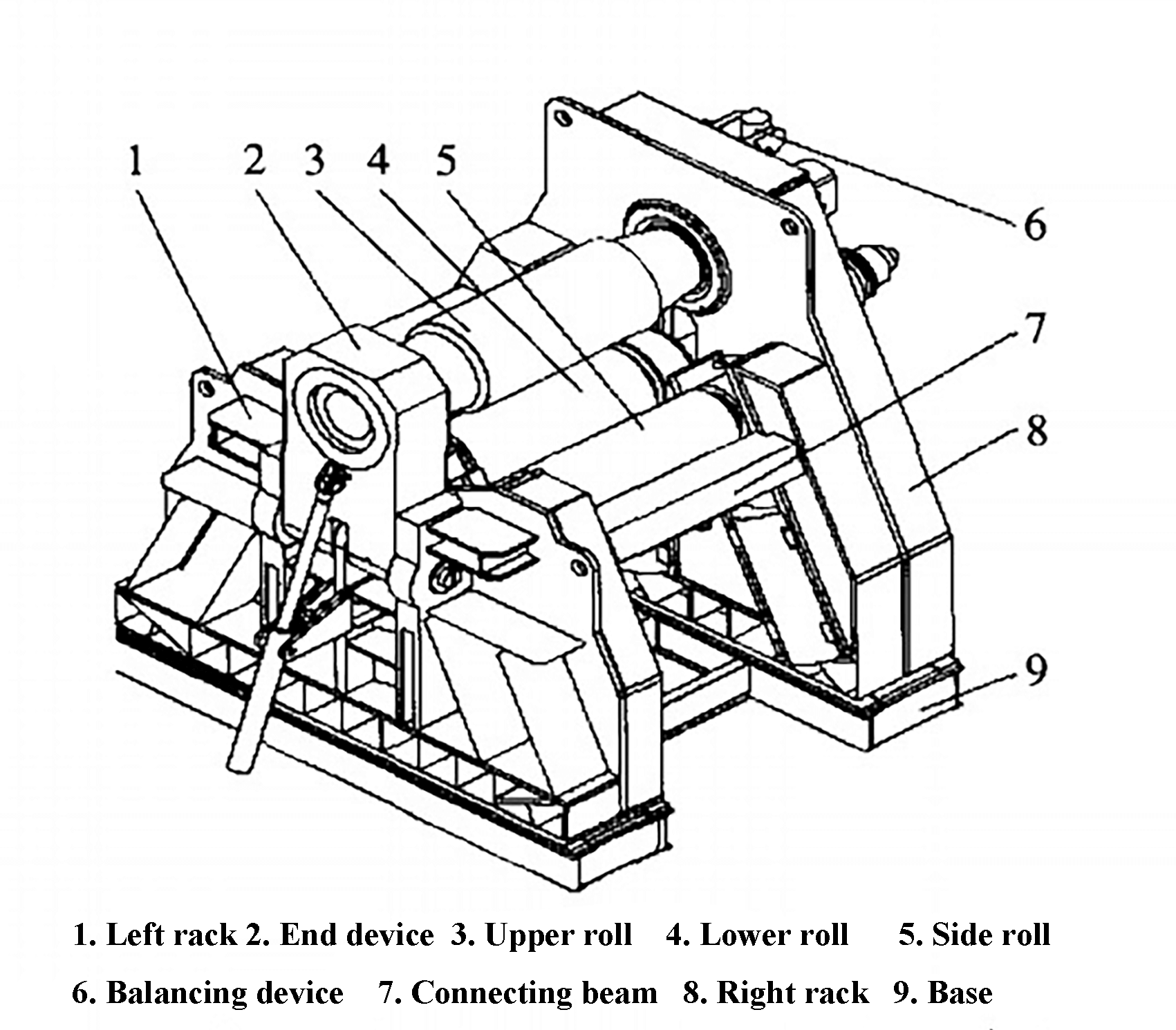
Fig. 1 Structure of four-roll sheet metal bending machine
1 .2 Process flow of four-roll sheet metal bending machine
The steel sheet rolling process typically consists of six steps, including preparation, feeding, pre-bending, other side pre-bending, rolling and arc correction. This process is represented in Figure 2.
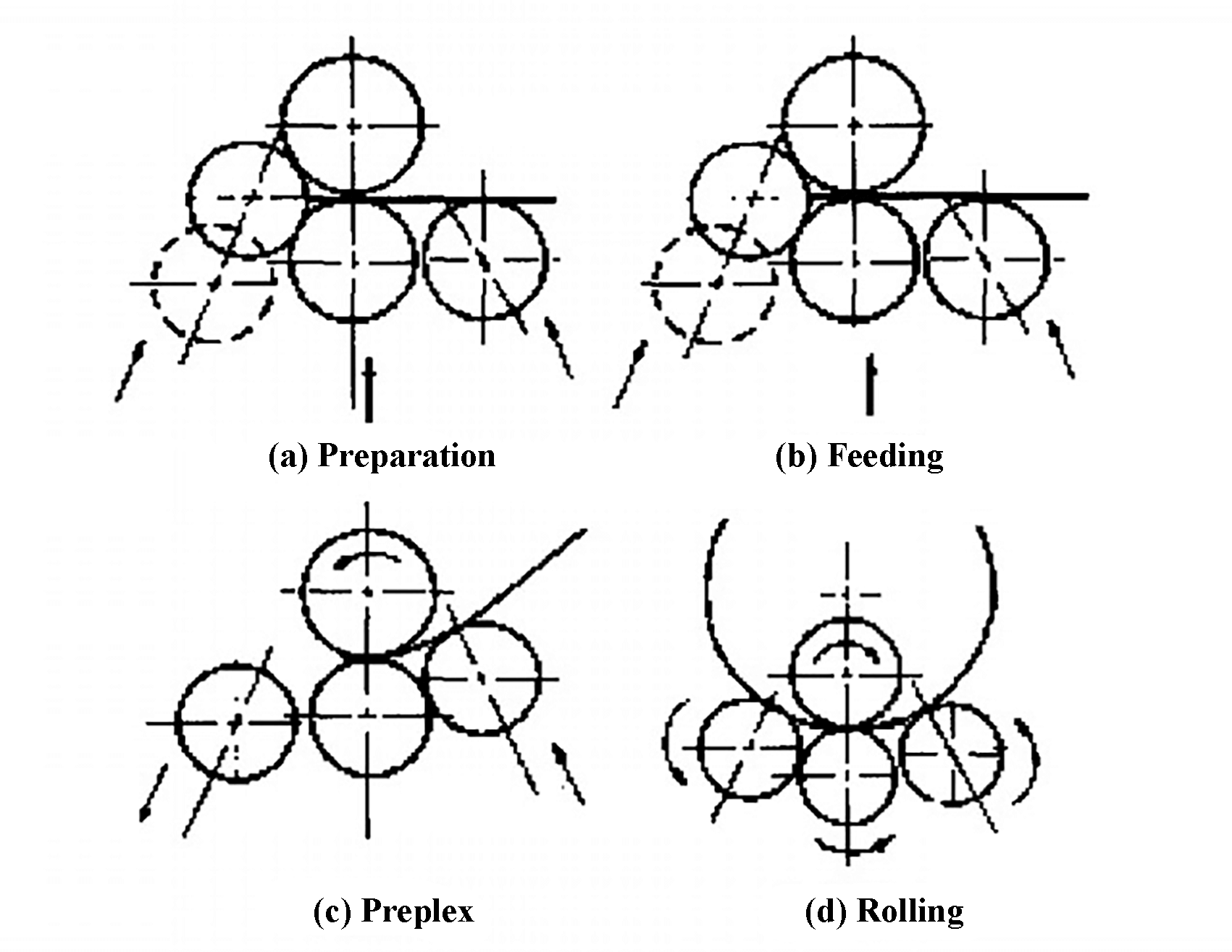
Fig. 2 Technological process of four-roll sheet metal bending machine
1.2.1 Preparation and feeding
The lower roller is raised to a position where the distance between the upper generating line and the lower generating line of the upper roller is slightly greater than the thickness of the workpiece.
The rear side roller is raised to a position where the upper generatrix and the upper generatrix of the lower roller are in the same horizontal plane, and then the front side roller is raised to a position where its center line is located between the upper roller and the lower rollers (as shown in Figure 2a).
The workpiece is fed horizontally between the upper and lower rollers, with the front end pressed against the front roller. The lower roller is then raised to secure the steel plate (as shown in Figure 2b).
Once these steps are complete, the preparation and eating process is complete.
1.2.2 Pre-flexion
The front side roller is returned to its original position and the rear side roller is raised to the process height for pre-bending bending of the steel plate (as shown in Figure 2c).
The upper roller rotates counterclockwise to drive the steel plate forward. When the end of the steel plate reaches half the distance between the two rollers, it must be measured to ensure that it reaches the required curvature.
The process for pre-bending the other end is similar to that described above.
1.2.3 Roll folding
The front side roller is raised to the process height for the required curvature, while the rear side roller is lowered so that the front and rear side rollers are at the same level.
The upper roller rotates counterclockwise to drive forward movement of the steel plate, causing it to curl. At the same time, the curvature of the protruding steel plate is measured using a template, and the process height is adjusted as needed to achieve the desired radian (as shown in Figure 2d).
The arc correction process is similar to the roll bending process.
3 . Calculation of springback radius during bending of steel sheet
Currently, most coils are produced by cold rolling. The springback phenomenon is quite pronounced in this process, therefore, an adequate amount of overcoiling is required to compensate for it.
Normally, the springback radius should be smaller than the desired radius of the parts (pre-bending radius).
Based on elastic-plastic mechanics, springback in sheet metal processing is influenced by factors such as modulus of elasticity, reinforced modulus of elasticity, yield strength, pre-coiling radius and sheet thickness.
Through theoretical derivation, the formula for calculating the radius of curvature before recovery can be determined as follows:
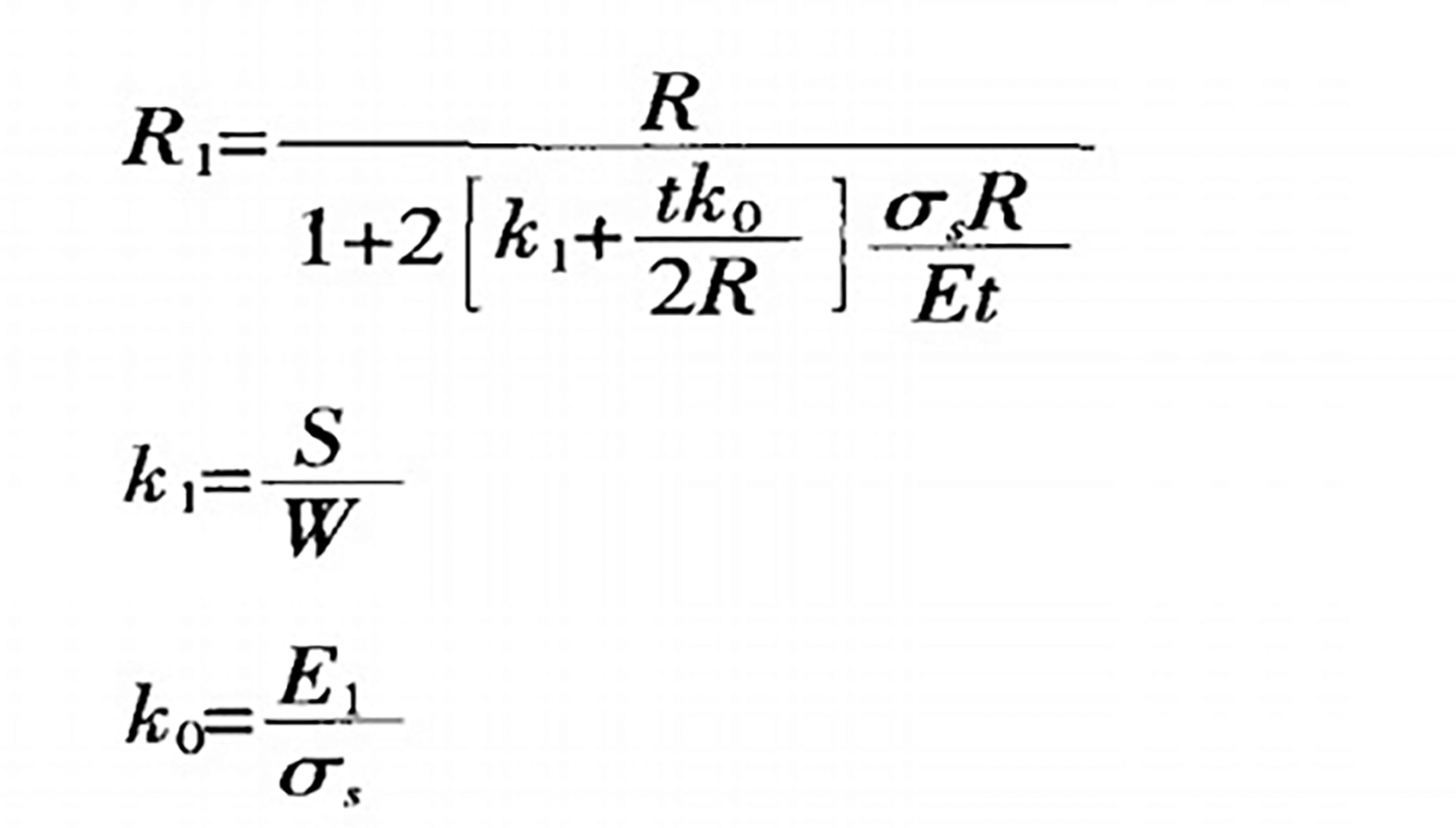
In the formula:
- R – Pre-winding radius, mm;
- E – Elastic modulus of the material, MPa;
- t – Thickness of the steel plate, mm;
- σ is – Plate yield limit, MPa;
- S – Static moment of the section, mm;
- W – Flexural section modulus, mm;
- E 1 – Reinforced modulus of elasticity of the steel sheet material, MPa;
- k 0 – Relative reinforcement coefficient of the material;
- k 1 – Section coefficient, 1.5 is considered for the rectangular section.
4. Calculation of side roller working displacement
Analysis of the steel plate rolling process reveals that the position of the upper roll remains unchanged during rolling and that rolling is mainly carried out through the vertical movement of the lower roll and the angular feed of the two side rolls.
Therefore, precise steel plate rolling can be achieved by precisely controlling the position of each roll during the process.
It then focuses on mathematical modeling and calculation of the process positions of the bottom roll and side rolls during key processes such as forward movement, pre-bending and winding.
The calculation takes into account factors such as the geometric parameters of the rolling mill, the material and thickness of the rolled steel sheet and the rolling radius.
The following symbols are typically used to derive the displacement formula for the rear roller and both sides of the plate bending machine:
- R is the radius of curvature before springback (i.e. the radius to be curled), mm;
- A is the center of the press brake, which is located at the intersection of the inclination angles of the rollers on both sides;
- α is the angle of inclination of the rollers on both sides, °;
- L 1 is the distance from point a to the center of the upper roller, mm;
- L 2 is the distance from point a to the center of the lower roller, mm;
- L 3 is the distance from point a to the center of the side roller, mm;
- D 1 is the diameter of the upper roller, mm;
- D 2 is the diameter of the lower roller, mm;
- D 3 is the diameter of the side roller, mm;
- S 1 is the lower displacement of the roller, mm;
- S 2 is the displacement of the rear side roller, mm;
- S 3 is the displacement of the front side roller, mm.
4.1. Calculation of displacement of the side roller and bottom roller of the sheet metal bending machine
During the plate calender alignment process, as illustrated in Figure 2, the lower roller and both side rollers undergo corresponding displacement. The process position of each roll during alignment is shown in Figure 3.
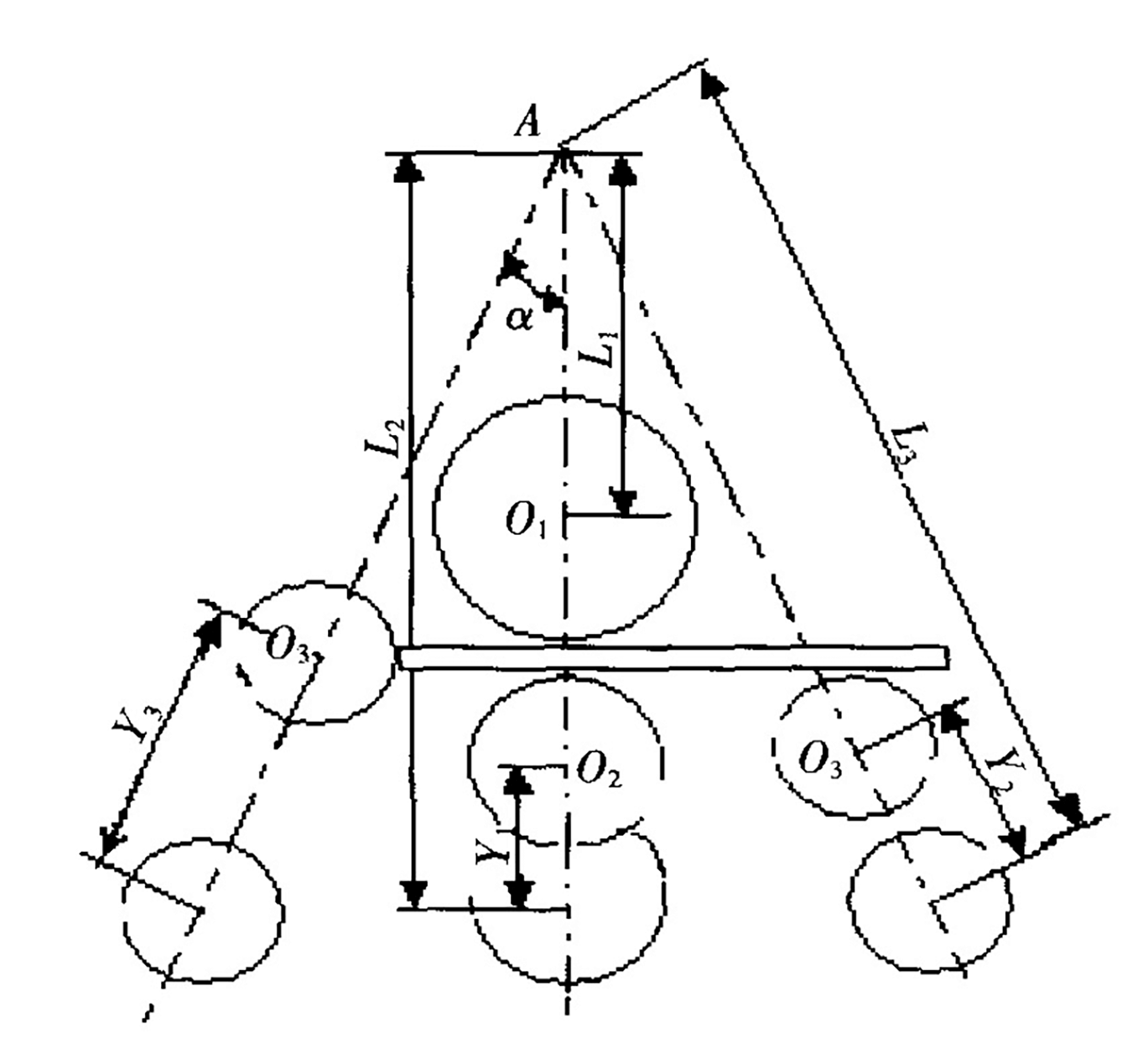
Fig. 3 Process position of the alignment rollers
The displacement of the two side rollers and the bottom roller can be calculated based on the geometric relationship as follows:
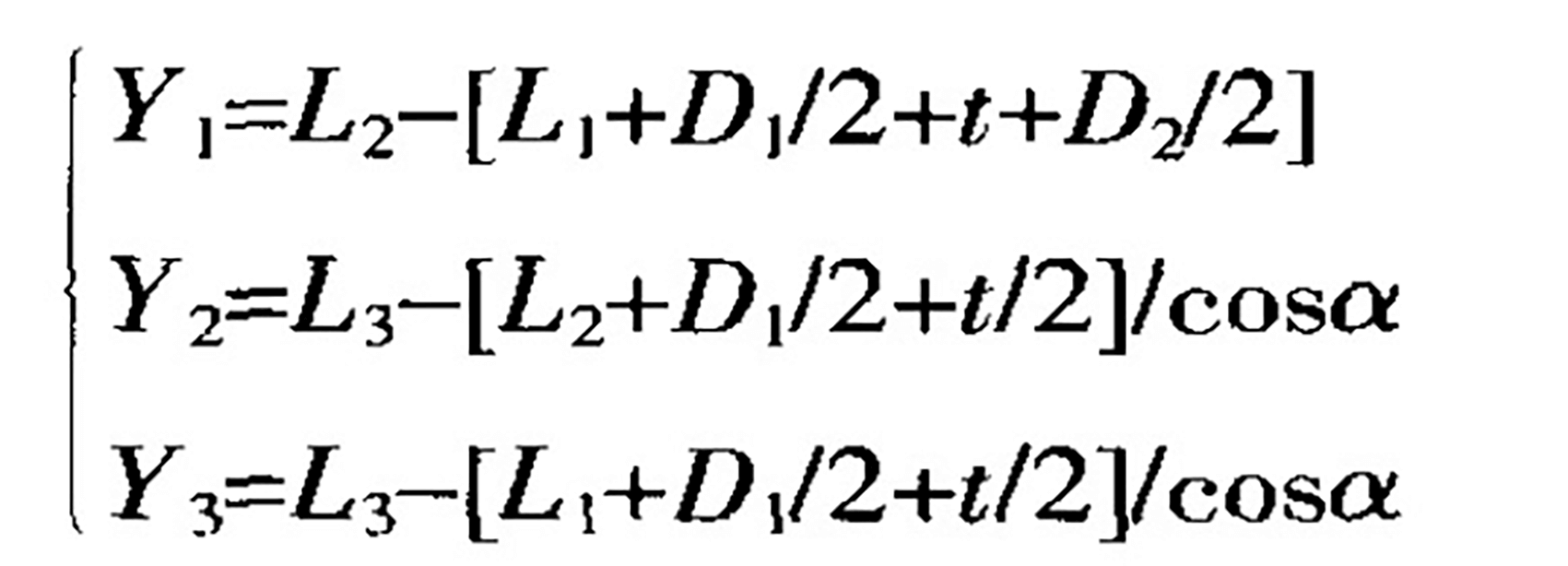
4.2 Calculation of lateral roll displacement during pre- bending
During the pre-bending process of the press brake, as shown in Figure 2, the lower roller and the front and rear rollers undergo corresponding displacement.
To meet the requirements of the pre-bending process, the process position of each roll during left pre-bending is shown in Figure 4. During right pre-bending, the positions of the front and rear rolls are simply switched, while the position of the lower roller remains unchanged.
The value of the geometric parameter B can be calculated using the calculation formula for the asymmetric three-roll plate calender. In this article, B is considered equal to 2t.
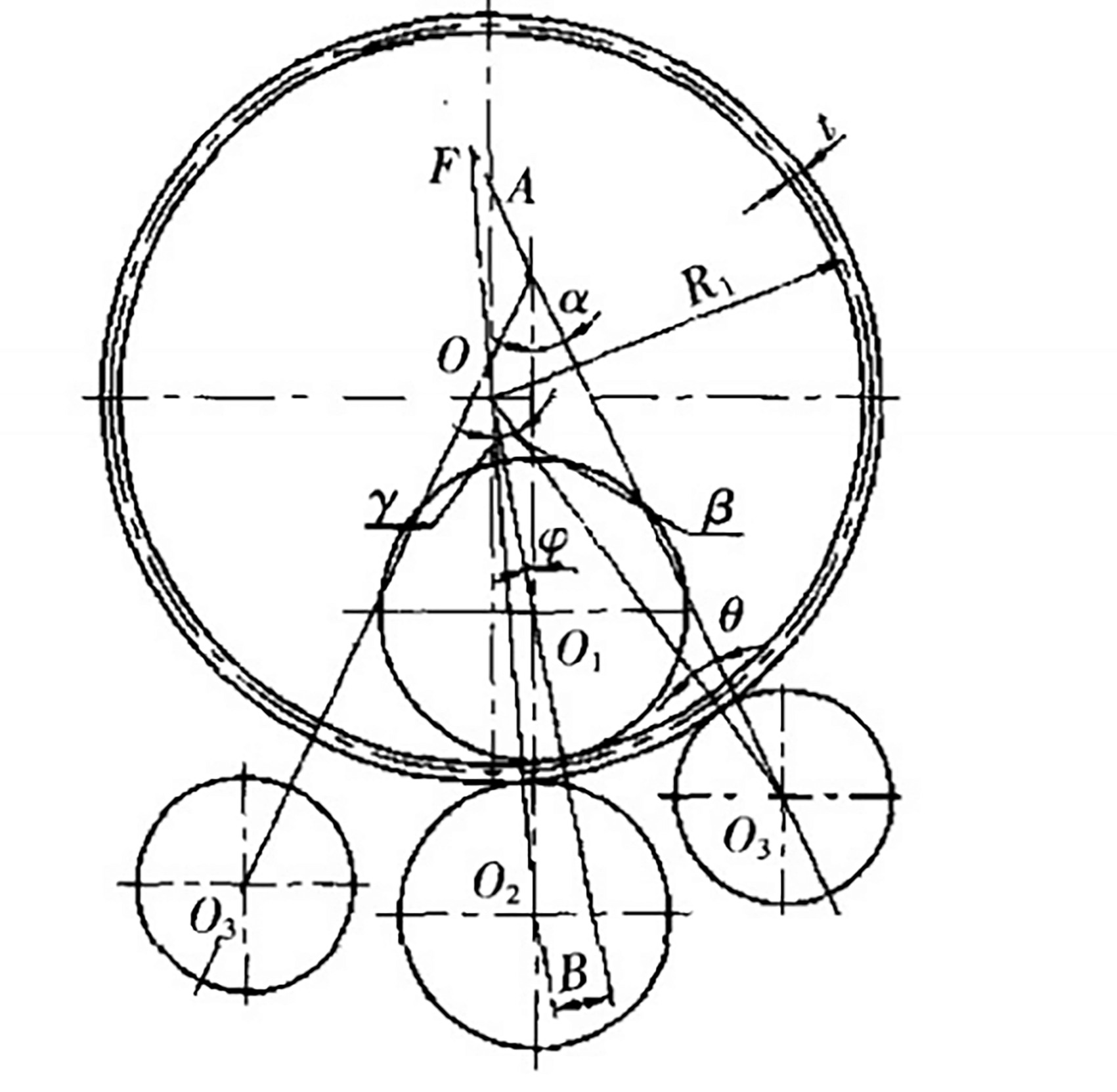
Fig. 4 Process position of each roll during pre-bending
Suppose “O” is the center of curvature before springback, “y” represents the angle between the upper roll center and the bending center line “OO 1 ” and the angle between the lower roll center and the center line “OO 2. ”
The angle “φ” represents the angle between the line “O 1 Ó 2 ” between the center of the upper roll and the center of the lower roll, and the line between the center of the upper roll and the bending center.
The angle “θ” represents the angle between the line “AO 3 ” between the center of the bending machine and the center of the side roller, and the line “OO 3 ” between the center of the side roller and the bending center.
Based on these geometric relationships, the following conclusion can be drawn:
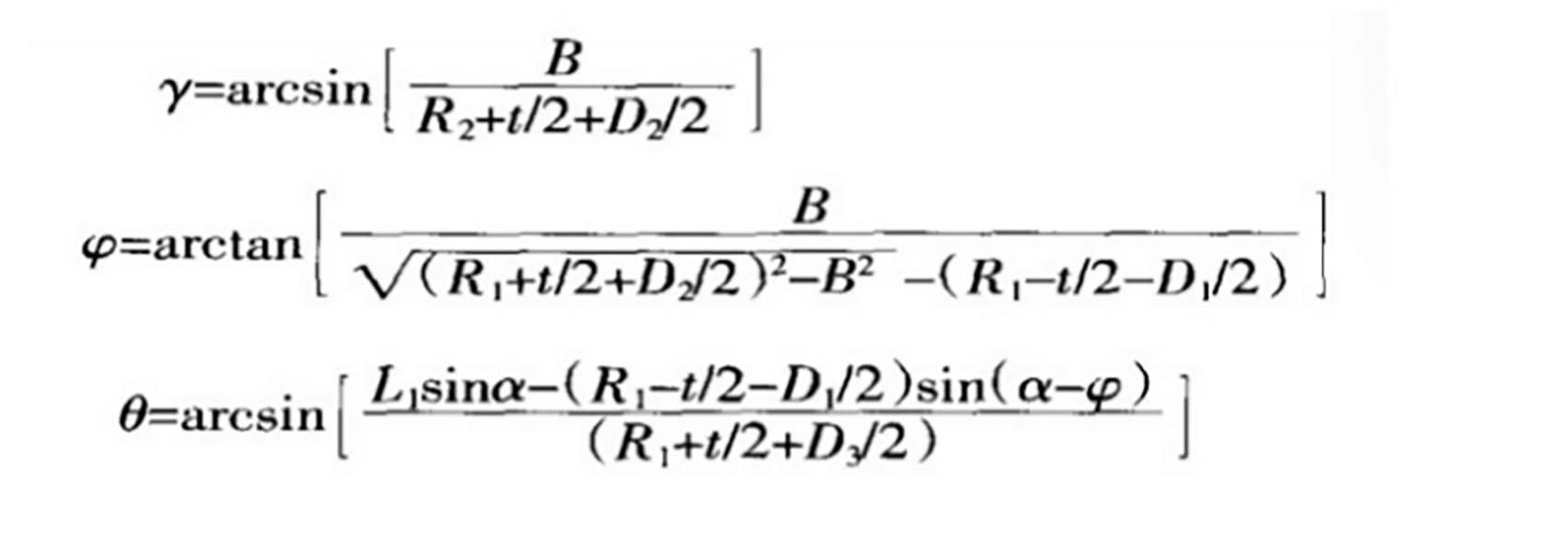
In the formula, the geometric parameter B is the value from the center of the lower roll O 2 to OO 1 which can be calculated according to the formula of the three-roll asymmetric press brake.
In this article, B = 2t and other parameters are the same as above.
Suppose F is the intersection of OO 2 and AO 3 and β is the angle between F and the midline of the upper and lower rolls.

In △ AFO 2 according to the sine theorem:
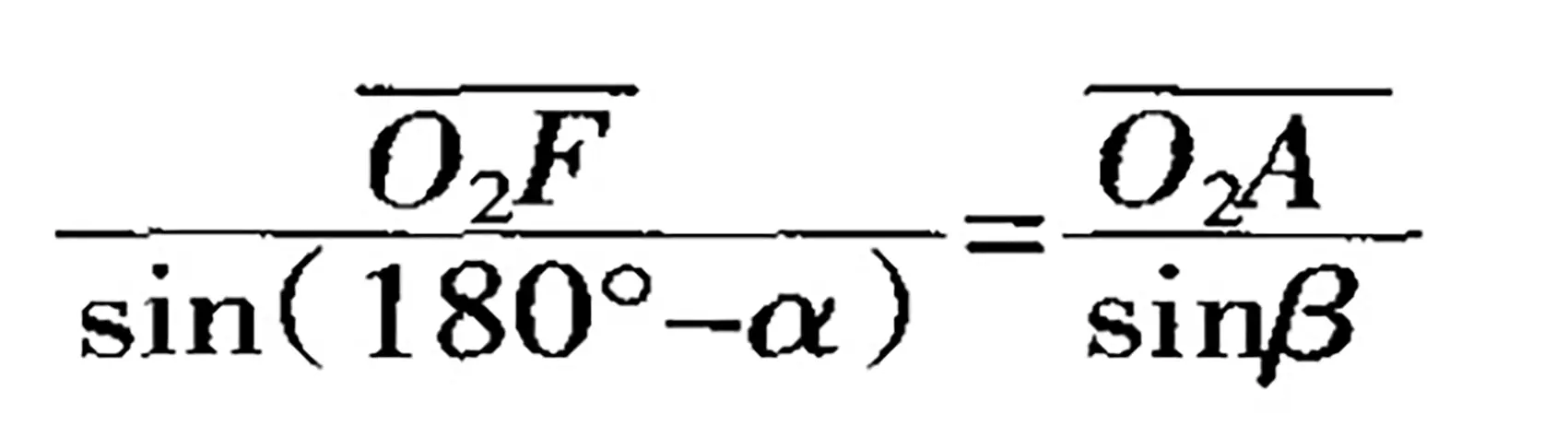
That's why:

Likewise, in △AFO 2 :
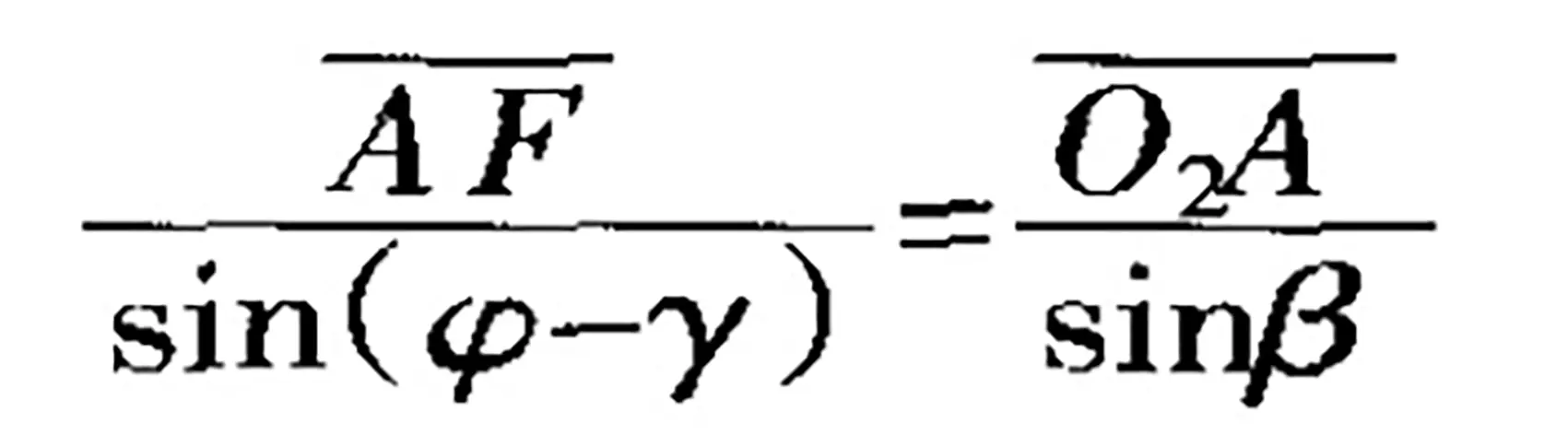
That's why:

In △AFO 2 :

That's why:

That is:

Therefore, the displacement between the two side rollers and the bottom roller is:
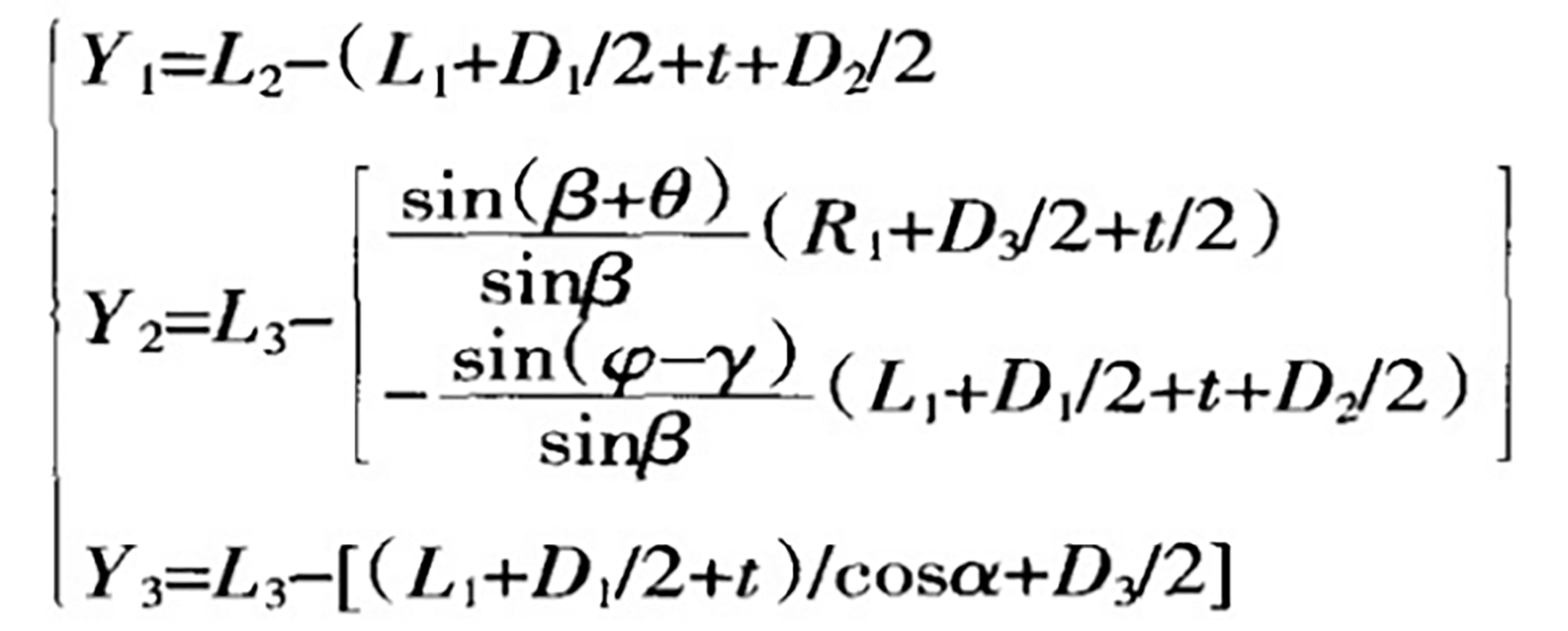
When the right side is pre-flexed, Y 1 remains unchanged, Y 2 and U 3 can be switched.
4.3 Calculation of lateral roll displacement during continuous bending
In the continuous bending process of the plate bending machine shown in Figure 2, the two side rollers are positioned symmetrically, and the bottom roller and the front and rear side rollers have corresponding displacements.
To meet the requirements of the continuous bending process, the position of each roll during the process is shown in Figure 5.

Fig. 5 Process position of each roll during continuous bending
According to the geometric relationship, in △OAO 3 of the sine theorem:
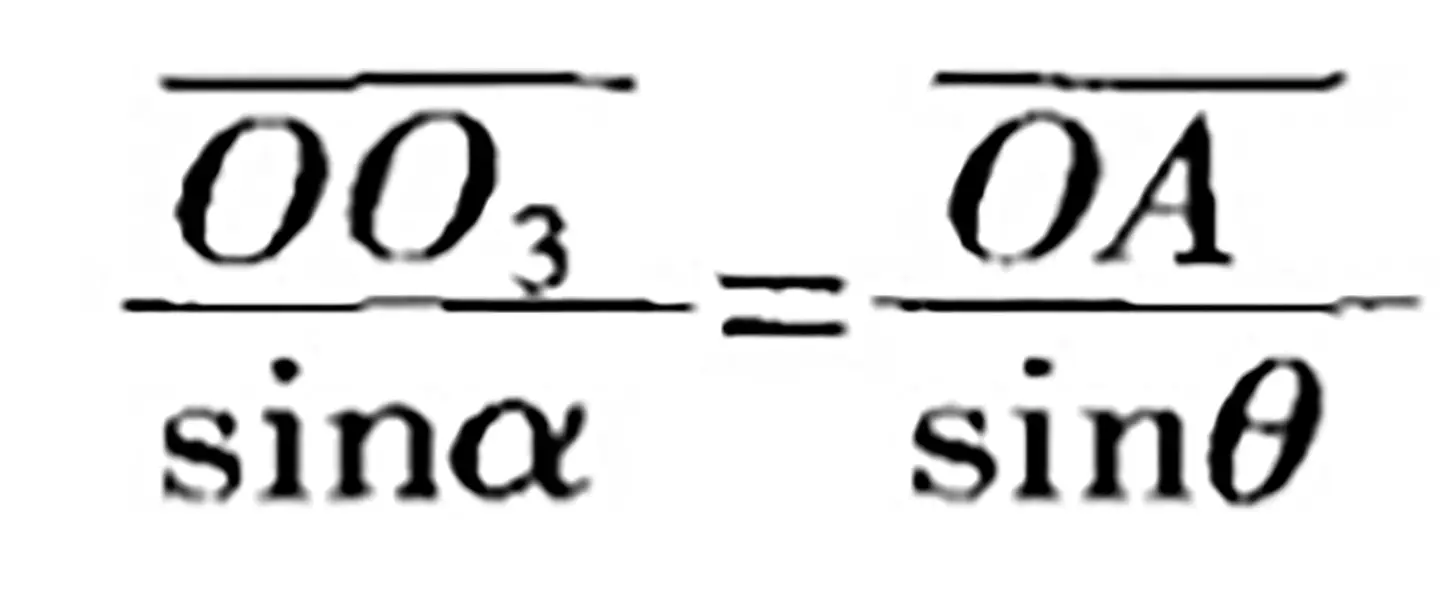
That's why:

Suppose that O is the center of curvature before springback, λ is the angle between OO 2 and OO 3 then:
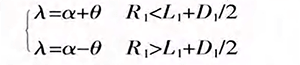
In △OAO 3 :
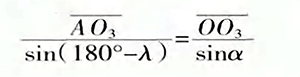
That's why:

If U 1 remains unchanged, Y 2 =S 3 =L 3 -AO 3 then the displacement of the rollers on both sides and the bottom roller is:
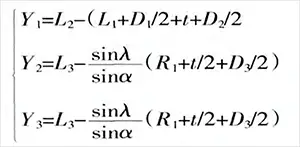
5. Actual verification results
An experimental study was carried out using a W1220 x 2500 sheet rolling machine, with a 10 mm thick Q235 sheet material and a rolling radius of 700 mm.
The results of the experiment showed that there was an absolute error of 4.8 mm between the actual circle radius and the required circle radius, resulting in a relative error of 0.68%. Based on these results, it was determined that the correction was sufficient to meet the accuracy requirements.
When analyzing test data from multiple attempts to adjust the springback radius, it was discovered that the main cause of the error was the assumption that the plate was undergoing pure bending during the springback radius calculation, and not taking into account Consideration the impact of extrusion force and friction.
However, the technical analysis showed that the displacement calculation was accurate and met the process requirements.
6. Conclusion
This article presents an analysis of the rolling process of a four-roll thick plate rolling mill. Combining the springback radius calculation formula with mathematical and mechanical methods, the article analyzes the position of each roller during the machine's working process.
The calculation results were tested on a four-roll sheet metal bending machine.
The experiment results showed that this method can significantly reduce the number of tests and improve the accuracy and efficiency of the rolling process.