I. What are the differences between copper core cables and aluminum core cables?
(1) Low resistivity: The resistivity of aluminum core cables is about 1.68 times that of copper core cables.
(2) Good ductility: Copper alloys have ductility of 20-40%, while electrical copper is more than 30%, but aluminum alloy is only 18%.
(3) High strength: Under normal temperatures, the allowable stress of copper is 7-28% higher than that of aluminum. This difference is particularly significant at high temperatures.
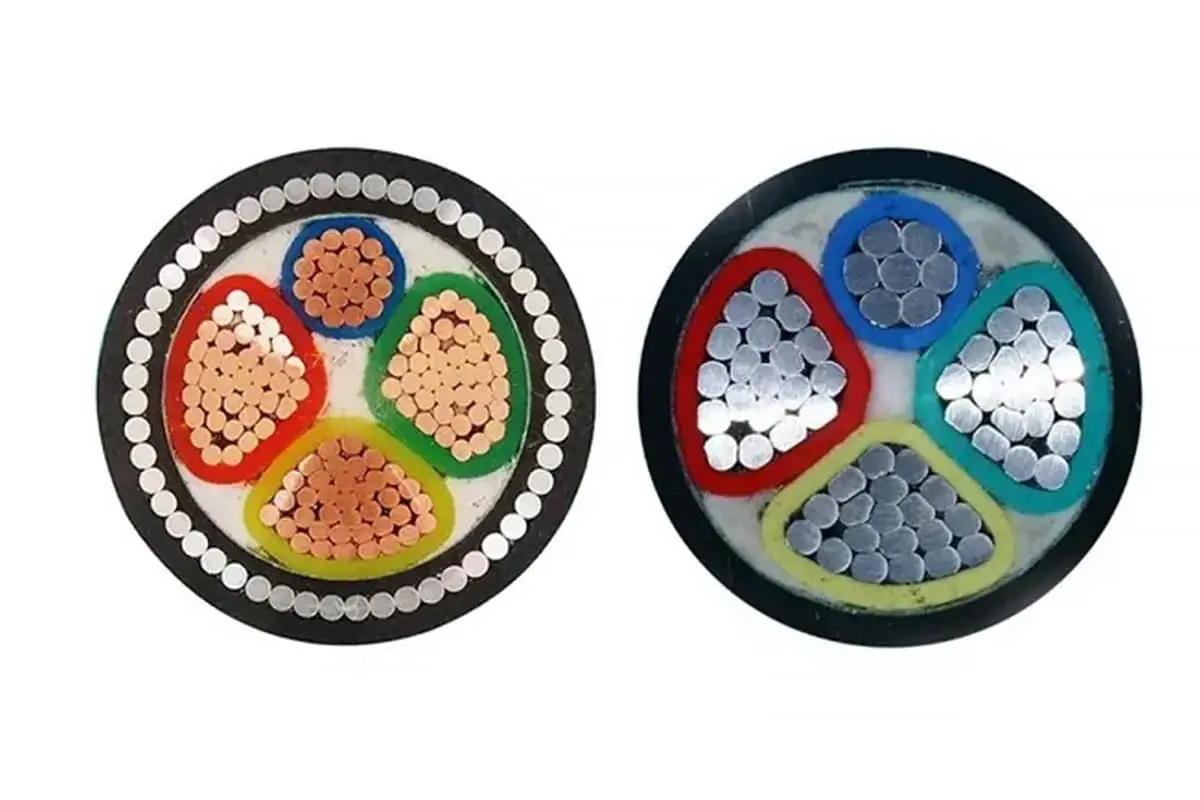
(4) Fatigue resistant: Aluminum tends to fracture after repeated bending, while copper does not. In terms of elasticity index, copper is about 1.7-1.8 times higher than aluminum.
(5) Good stability and corrosion resistance: Copper cores are resistant to oxidation and corrosion, while aluminum cores are prone to oxidation and corrosion.
(6) Large current-carrying capacity: Due to low resistivity, the current-carrying capacity (maximum current it can carry) of copper core cables of the same cross section is about 30% higher than that of cables with aluminum core.
(7) Low heat generation: Under the same current, the heat generated by copper core cables of the same cross section is significantly lower than that of aluminum core cables, making the operation safer.
(8) Low power consumption: Due to the low resistivity of copper, the power loss in copper cables is lower than that in aluminum cables. This is obvious and beneficial to improve the utilization of power generation and protect the environment.
(9) Oxidation resistant, corrosion resistant: Copper core cable connections are stable and will not cause accidents due to oxidation. Aluminum core cable connections are unstable, and increased contact resistance due to oxidation can often cause heating and accidents. Therefore, the accident rate is much higher than that of copper core cables.
(10) Convenient for construction: Copper cores are flexible with a small bending radius allowed, making bending and threading easy; copper cores are fatigue resistant and will not break easily after repeated bending, making wiring easier; The mechanical resistance of the copper cores is high, capable of withstanding greater mechanical stress, which greatly facilitates construction and laying and creates conditions for mechanized construction.
(11) Small voltage loss: Due to the low resistivity of copper core cables, when the same current flows through the same cross section, the voltage drop of copper core cables is small. The same transmission distance can ensure higher voltage quality; Under permitted voltage drop, copper core cables can reach long distances, that is, the coverage area of the power supply is large, which favors network planning and reduces the number of power points.
In conclusion, copper core cables have the advantages of low resistivity, good ductility, high strength, fatigue resistance, good stability and large current-carrying capacity. They have remarkable advantages in the field of cable power supply, especially underground cable power supply.
Aluminum core cables are cheaper than copper core cables, lighter and easier to transport, which makes them essential materials for high voltage, large cross-section and long-range overhead transmission.
Therefore, I want to remind you to choose the suitable cable according to the different applications and characteristics of products made of different materials.
II. What are the advantages of copper core cables compared to aluminum core cables?
We often use copper core cables and aluminum core cables, but many users don't know whether to choose copper core cables or aluminum core cables.
To make a clear judgment between the two, I will introduce the advantages of copper core cables over aluminum core cables.
(1) Strong conductivity: The resistivity of aluminum core cables is about 1.68 times that of copper core cables. Due to the lower resistivity of copper core cables, copper core cables of the same cross section have a higher current carrying capacity than aluminum core cables, therefore the conductivity of copper core cables is generally greater than that of aluminum core cables.
(2) Good ductility: Metals have good ductility, such as gold, platinum, copper, silver, tungsten and aluminum, which are rich in ductility. Among them, the ductility of copper alloys is 20 to 40%, and the ductility of electrical copper is more than 30%.
(3) Good elasticity: Copper cables are not easily broken when repeatedly bent by hand and have strong fatigue resistance, while aluminum is very prone to breakage. In terms of elasticity index, copper is about 1.7-1.8 times higher than aluminum.
(4) Good anti-oxidation: The aluminum core cable joint is unstable and will react with the oxidation in the air, causing the resistance of the cable conductor to increase, causing the conductor to heat up and accidents. However, the copper core cable joint is more stable and will not cause accidents due to oxidation. Therefore, the stability of copper core cables is much higher than that of aluminum core cables.
(5) Low voltage loss: Due to the lower resistivity of copper core cables, when the same current flows through the same cross section, the voltage drop of copper core cables is smaller. At the same transmission distance, copper core cables can guarantee higher voltage quality.
Under allowable voltage drop conditions, copper core cable transmission can reach a greater distance, which means a larger power supply coverage area, which benefits network planning and reduces the number of source points feed. The resistivity of aluminum core cables is higher and their performance is much lower than that of copper core cables.
(6) Easy construction: Because the elasticity of copper core cables is much higher than that of aluminum core cables, they are not easily broken with repeated bending and their flexibility is better with a smaller allowable bending radius.
Therefore, it is easier to bend during the laying process and more convenient for threading. Furthermore, the mechanical strength of copper core cables is high and can withstand more damage from external forces, providing greater convenience during construction.
From the above, copper core cables have the advantages of low resistivity, good ductility, high elasticity, good anti-oxidation and large current-carrying capacity. They have notable advantages over cable power supply.
III. The differences, advantages and disadvantages of aluminum core cables and copper core cables
Many people often cannot distinguish the advantages of aluminum core cables and copper core cables, or where they are applied. Therefore, I have compiled the differences, advantages and disadvantages of the two.
1) The basic differences between aluminum wire and copper wire:
1. The current carrying capacity of copper wire and aluminum wire is different.
2. Aluminum wire is relatively cheaper.
3. Aluminum wire is lighter.
4. Aluminum wire has lower mechanical strength.
5. Aluminum wire is prone to oxidation at the connection point, and after the connection point is oxidized, a temperature rise will occur.
6. Copper wire has lower internal resistance. Although aluminum wire has greater internal resistance than copper wire, it dissipates heat more quickly. The main differences are the different current conduction capabilities and mechanical resistance.
The resistivity of copper is 0.017 and that of aluminum is 0.029. Therefore, the current carrying capacity of aluminum is about 80% of that of copper. The mechanical resistance of copper is also much better.
2) Comparison of advantages and disadvantages of copper core cables and aluminum cables:
1. Copper core cable has lower resistivity: the resistivity of aluminum core cables is about 1.68 times that of copper core cables.
2. Copper core cable has good ductility.
3. Copper core cable has high strength: the allowable voltage at room temperature can reach 20 for copper, while for aluminum it is 15.6kgt/ mm2 .
4. Copper core cable is fatigue resistant: aluminum material is prone to breaking with repeated bending, while copper is not.
5. Copper core cable is stable and corrosion resistant: copper cores are resistant to oxidation and corrosion, while aluminum cores are prone to oxidation and corrosion.
4. Application comparison of aluminum alloy and copper cables
1 . Overview
In the past, pure aluminum cables were gradually replaced by copper cables due to high resistivity, joint heating due to oxidation, poor fatigue resistance, electrochemical corrosion and creep.
However, with the improvement of the properties of aluminum alloy materials, aluminum alloy cables produced with AA-8000 series aluminum alloy conductors have emerged using advanced technologies such as special crimping processes and annealing treatments.
This type of aluminum alloy power cable makes up for the shortcomings of previous pure aluminum cables, solves the problems of electrochemical corrosion and creep of pure aluminum conductors, and improves the bending performance, fatigue resistance, creep resistance and weathering resistance. corrosion of aluminum alloy cables.
This ensures that the cable maintains stable performance during long periods of overload and overheating. As a result, there are a growing number of manufacturers and cables are being used in related areas.
two . Basic performance comparison
The differences in physical properties between aluminum and copper alloys are shown in Table 1.
Copper cable | Aluminum Alloy Handle | Comparative Statement | |
Density (g/ mm3 ) |
8.89 | 2.7 | The weight of an aluminum alloy cable of the same diameter is one third of that of a copper cable. |
Electric conductivity
% IACS (68°F) |
100 | 61.8 | The conductivity of an aluminum alloy cable of the same diameter is 61.8% of that of a copper cable, while its current-carrying capacity is 79% of that of copper. |
Under identical electrical performance requirements, traditional aluminum alloy cables have a much larger diameter than their copper counterparts. In recent years, cable manufacturers have developed new production techniques, specifically advanced compression methods.
By maximizing compression, these techniques compensate for the lack of volumetric conductivity in aluminum alloys, allowing aluminum alloy cables to have a cross-section 1.1-1.25 times that of traditional copper cables while weighing only half as much.
3 . App Comparison
After analyzing relevant information, carrying out technical exchanges with manufacturers and considering the actual conditions on site, the application requirements for aluminum alloy cables and copper cables are compared as follows:
Copper Electrical Cable | Aluminum Alloy Handle | |
Construction | Crimping is simple | Specialized tools are required for crimping, requiring high precision. |
Demands on construction personnel are low. | Construction personnel must be highly qualified. | |
The object is heavy, making installation inconvenient. | Lightweight and easy to install, some situations allow the omission of cable trays. | |
Connector cable | Affordable price | In situations where the cost is high and there are many cable sections, the proportion of expense attributed to cable joints is significant. |
Universal Standards | This is typically a product designated by the cable manufacturer. | |
The copper connector is short | The copper-aluminum joint is long, making its use challenging in certain situations – for example, a custom order is required for motor junction boxes. | |
Cable price | Dear | Providing equivalent electrical performance, the cost of aluminum alloy cables is 20% to 40% less than traditional copper core cables. |
4. Application Status
Since 1968, Southern Cable Company in the United States began developing and producing alloy power cables, which have since been progressively introduced and used in countries such as the United States, Canada and Mexico.
They are mainly used in construction projects of airports, military bases, office buildings, residential areas, hotels, supermarkets, educational institutions, sports stadiums, hospitals and factory buildings.
5. Considerations
It is clear that the use of aluminum alloy cables is expanding and manufacturers claim that, under the premise of meeting equivalent electrical performance, the price of these cables is 20%-40% lower than that of traditional aluminum core cables. copper.
However, after analyzing materials and technical exchanges with manufacturers, the following points need to be observed when using aluminum alloy cables:
1. At present, the national standard “Rare Earth High Speed Aluminum Alloy Conductor” has not yet been introduced. Different production units are using enterprise standards, leading to strong individualization of products from different companies and uneven product quality.
2. Because the bending properties, fatigue resistance, anti-creep and corrosion resistance of aluminum alloy cables are strongly related to the material properties of the alloy, the material requirements are significantly higher than those of copper cables.
On the other hand, the construction requirements for stable operation are much higher than those for copper cables, making acceptance checks more challenging. If the quality of material and construction cannot be guaranteed, there may be substantial hidden risks in the future.
3. At present, it is generally believed that aluminum alloy cables are not suitable for high temperature and high vibration areas, nor for use in mobile equipment.
4. If there are many cable breaks and the cable is short, the number of copper-aluminum joints used in aluminum alloy cables is large. The cost advantage is not apparent and construction requirements are high, increasing the workload.
5. As copper-aluminum gaskets are longer than copper gaskets, economic feasibility needs to be carefully considered for their use in some situations. For example, customization may be required for motor junction boxes; and the number of switches arranged within some electrical cabinets may need to be reduced, necessitating an increase in the number of electrical cabinets.
6. The use of aluminum alloy cables in the power supply of metallurgical enterprises is limited and the usage time is short, so the service life is unknown. The service life of copper cables is generally more than 30 years, and it is not known whether aluminum alloy cables can reach this limit. Otherwise, the cost advantage is not apparent.
6. Application suggestions
Based on the above circumstances, it is suggested to initially try to use these cables in lighting, maintenance power supply and temporary power lines.
For other power transmission and distribution systems, additional investigations and verifications are required due to the lack of relevant data for application in the metallurgical industry.
V. How to choose electrical wires and cables
Selection of types of electrical wires and cables:
- When choosing electrical wires and cables, consider the purpose, installation conditions and safety. For example, based on different purposes, you can choose power cables, overhead insulated cables, control cables, etc.
- Based on different installation conditions, you can choose general plastic insulated cables, steel tape armored cables, steel wire armored cables, anti-corrosion cables, etc.
- Based on safety requirements, you can choose non-flammable cables, flame retardant cables, halogen-free flame retardant cables, fire resistant cables, etc.
Selection of electrical wire and cable specifications:
- When determining the usage specifications (conductor cross-section) of electrical wires and cables, generally consider conditions such as heating, voltage loss, economical current density, and mechanical strength.
- Based on experience, as the charging current of low voltage power lines is larger, the cross section is generally chosen first according to the heating condition, and then the voltage loss is calculated.
- Mechanical strength: For low voltage lighting wires, because they require a higher voltage level, the cross section can be chosen first according to the allowable voltage loss condition, and then the heating condition and mechanical strength are calculated.
- Although aluminum core cables are cheaper, copper cables have notable advantages in cable power supply, especially in the field of underground cable power supply. The use of copper core cables for underground power supply has features such as low accident rates, corrosion resistance, high reliability, and convenient construction and maintenance.