Technical requirements for fastening in the process of installing equipment and pipeline flanges
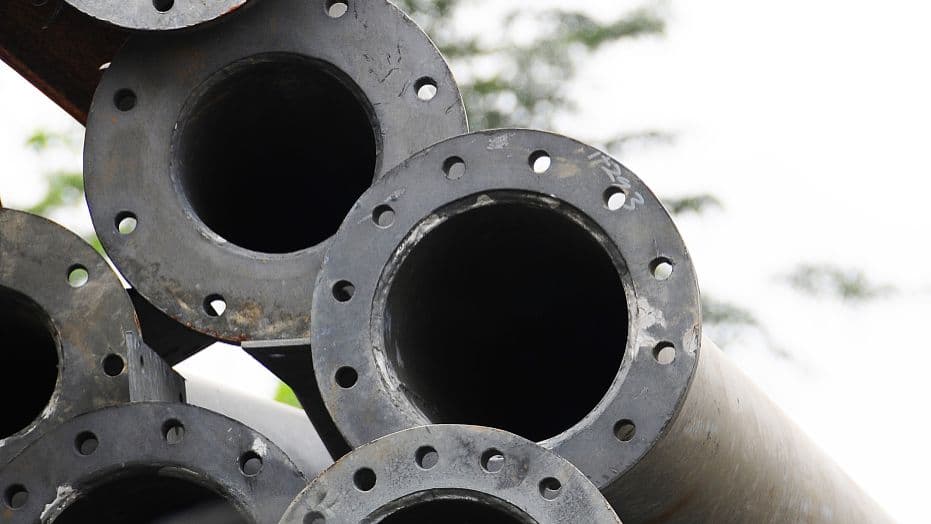
(1) Inspection of flange fasteners
● Gasket: When installing, make sure the gasket is new and clean, and check the gasket for defects or damage.
Old gaskets cannot be reused. Before installation, confirm that the size and class of the gasket used are consistent with the flange identification.
● Table: Check the flange surface for damage before installation, such as scratches, inscriptions, mud, corrosion and burrs.
When the depth of dents or scratches passing through the watermark line of the radial sealing surface of the flange exceeds 0.2 mm and the covering surface exceeds half the width of the gasket sealing surface, the flange shall be replaced or the sealing surface will need to be re-machined and repaired.
The position of the supporting surface of the flange rear nut should be parallel and smooth. Check whether the flange is centered and the inspection method must follow the piping installation requirements in SH3501-2011.
● Bolts and nuts: Check whether bolts and nuts are used correctly according to the requirements of the equipment and pipeline design.
The threads and contact surfaces must not contain external substances such as dirt, rust, thick skin, inscriptions, burrs, debris and others that affect the torque during tightening.
Welding or machining methods are not permitted to repair screws. After the flange is installed and tightened, at least two threads should be exposed outside the nut.
Bolts and nuts should be lubricated before use to reduce the coefficient of friction when tightening bolts and to improve the anti-slip and anti-corrosion properties of bolts and nuts.
Stud threads, nut threads and mating surfaces must be degreased and dried before using lubricating oil.
Bolt threads, nut threads, nut bearing surfaces, washers, and nut bearing surfaces on flanges must use the same lubricating oil appropriately. High temperature anti-seize agents should be used as needed.
(2) Screw fixing method
● Non-torque wrench or impact wrench: Suitable for general equipment and pipe flange tightening. Select according to bolt size and flange pressure level.
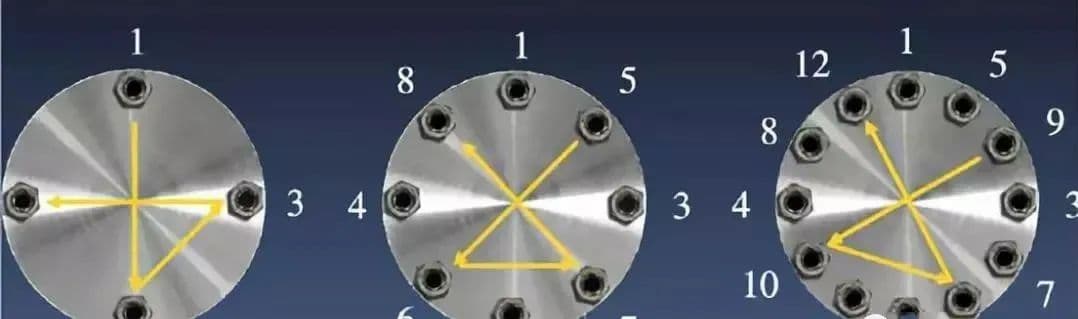
Fixture requirements are as follows:
- The maintenance unit formulates a clamping plan and tightens the flange symmetrically, numbering the tightening sequence and referring to Figures 1 and 2.
- To position in positions 1, 2, 3 and 4, use 4 screws as gaskets to ensure the center of the rolled gasket is within the edge of the boss.
- Tighten the positioning screws by hand, then insert other screws and balance the load by hand. Make sure at least two nut threads are exposed on each end.
- According to the equipment and flange on site, calculate a tightening cycle as a single time, and reasonably formulate the tightening times (at least 3 times) and hammering load (force) for each tightening. The hammering load (force) must be tightened in sequence from small to large (such as 50%, 80%, 100%) to prevent the joint from losing its seal due to too fast or too large a load.
- The order of each tightening of the non-torque wrench or impact wrench:
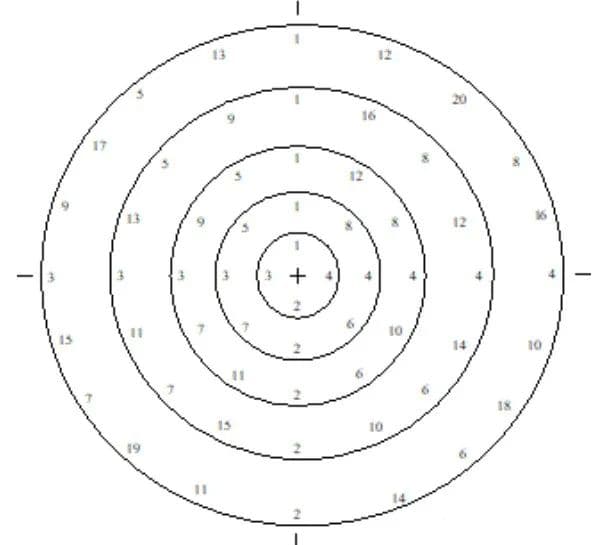
Tighten the two screws that are radially opposite to the predetermined hammering load of the screws.
Tighten another pair of screws that are about 90 degrees from the previous two screws along the circumference.
Continue tightening until all remaining screws are tightened to the predetermined hammering load.
- Finally, tighten all screws clockwise or counterclockwise according to 100% hammering load.
● Torque wrench: Suitable for important equipment and pipeline flanges with high temperature, high pressure, flammable and explosive properties, etc.
Fixture requirements are as follows:
- The maintenance unit needs to formulate a fastening plan, determine the appropriate torque, design and check it according to parameters such as bolt strength, initial seal compression ratio and working seal compression ratio of the gasket and medium pressure to avoid bolt fracture and loss of gasket elasticity due to excessive clamping force, leading to seal failure.
- Tighten the flange symmetrically, numbering the tightening sequence and referring to Figures 1 and 2.
- To position in positions 1, 2, 3 and 4, use 4 screws as gaskets to ensure the center of the rolled gasket is within the edge of the boss.
- Tighten the positioning screws by hand, then insert other screws and balance the load by hand. Make sure at least two nut threads are exposed on each end.
- Calculate a single tightening cycle according to the equipment and flange on site, reasonably formulate the tightening times (at least 3 times) and tightening torque for each time. The tightening torque is tightened in sequence from small to large (such as 50%, 80% and 100%) to prevent the gasket from losing its seal due to too fast or too large a load.
- The order of each tightening of the torque wrench:
Tighten the two screws that are radially opposite to the predetermined screw torque.
Tighten another pair of screws that are about 90 degrees from the previous two screws along the circumference.
Continue tightening until all remaining screws are tightened to the predetermined torque.
- Finally, tighten all screws clockwise or counterclockwise to 100% torque value.
- Record the torque value as a reference for future maintenance.
● Screw tensioner: Suitable for important equipment and pipeline flanges with high temperature, high pressure, flammable and explosive properties, etc.
Fixture requirements are as follows:
- The maintenance unit formulates a fastening plan, determines the appropriate tensile force, and designs and checks it according to parameters such as bolt strength, initial sealing compression ratio and working sealing compression ratio of the joint and medium pressure to prevent screw fracture and the gasket lose elasticity due to excessive clamping force, leading to seal failure.
- When a single screw (step) is tightened by the screw tensioner, it should be performed according to the principle of uniform screw tightening, referring to the tightening sequence of the torque wrench.
- During the bolt tensioning process, reasonably formulate the tightening times, gradually increase the pressure evenly from small to large (such as 50%, 80% and 100%), and stabilize the pressure before increasing the pressure to avoid pulling force of excessive impact on screws, affecting the pre-tightening effect of the screws.
- Record the pressure value as a reference for future maintenance.
Requirements for thermal tightness when heating equipment and pipelines during the construction period.
(1) Perform heat tightening according to the temperature in Table 1.
Table 1: Temperature for thermal and cold tightening of equipment and pipelines, unit: ℃
Work temperature | Primary hot and cold clamping temperature | Secondary hot and cold clamping temperature |
250~350 | Work temperature | / |
>350 | 350 | Work temperature |
-70~-29 | Work temperature | / |
<-70 | -70 | Work temperature |
Note: Hot and cold tightening cannot be performed for working temperatures between -29~250°C.
(2) Hot or cold tightening must be carried out after the temperature of the equipment and piping has stabilized. Use explosion-proof tools and do not perform operations such as heating and pressurizing during tightening.
(3) For tightening, it is recommended to start with the largest gap between the flanges and tighten symmetrically. If there is a leak, first tighten the leak.
(4) During the process of increasing the temperature of equipment and pipeline, it is necessary to carry out quality inspection for tightness. Use a torque wrench according to the torque value of 100% or use an explosion-proof hammer to check whether the nut is loose in the tightening direction.