1. What is martensitic stainless steel?
It refers to a type of stainless steel with a martensitic microstructure at room temperature and whose mechanical properties can be modified through heat treatment.
As a general description, it is a type of stainless steel that can be hardened.
Some common types of martensitic stainless steel include 1Cr13, 2Cr13, 3Cr13, 4Cr13, 3Cr13Mo, 1Cr17Ni2, 2Cr13Ni2, 9Cr18, and 9Cr18MoV.
Related Reading: Stainless Steel Grades
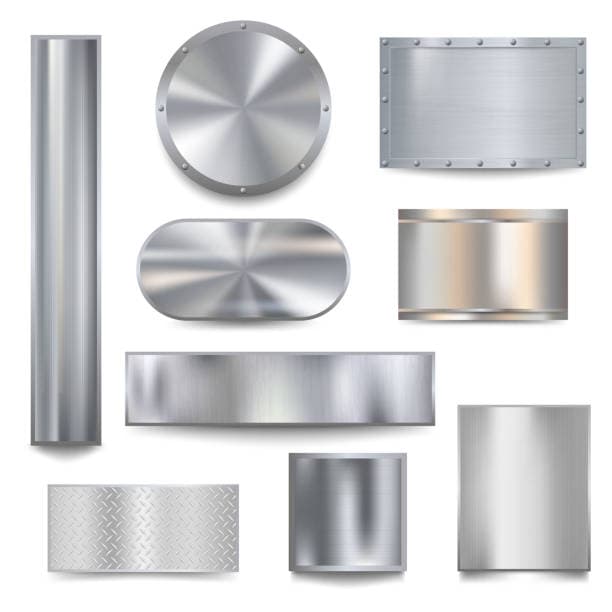
2. Common welding methods
Martensitic stainless steel can be welded using various electric arc welding techniques.
Currently, rod arc welding remains the main method, while the use of carbon dioxide gas shielded welding or mixed argon-carbon dioxide gas shielded welding can significantly reduce the amount of hydrogen in the weld, thereby reducing the risk of cold cracks in the weld.
3. Common welding materials
(1) Cr13 martensitic stainless steel electrode and wire
Generally, when higher strength is required in welding, Cr13 martensitic stainless steel welding rods and wires are used to make the chemical composition of the weld metal similar to that of the base metal, but this increases the likelihood of cold cracking.
Considerations:
The. Preheating is necessary before welding and the temperature should not exceed 450°C to avoid embrittlement at 475°C.
A post-welding heat treatment must be carried out.
Once the temperature has cooled to 150-200°C, a post-weld heat treatment must be carried out for 2 hours to allow the transformation of all parts of the austenite to martensite, followed by high temperature tempering where the temperature is elevated. to 730-790°C.
The waiting time should be 10 minutes per 1mm of plate thickness, but not less than 2 hours, and finally it should be cooled in air.
B. To avoid cracking, the S and P content in welding rods and wires should be less than 0.015%, and the Si content should not be more than 0.3%.
An increase in Si content can cause the formation of coarse primary ferrite, which decreases the plasticity of the joint.
The carbon content must normally be lower than that of the base metal, which can reduce its hardenability.
(2) Cr Ni austenitic stainless steel electrode and wire
The weld metal of Cr Ni austenitic steel has a high level of plasticity, which can alleviate the stresses produced during martensitic transformation in the heat-affected zone.
In addition, Cr Ni austenitic stainless steel type welds have high solubility for hydrogen, which can decrease the diffusion of hydrogen from the weld metal to the heat-affected zone and effectively prevent cold cracking, so preheating is not necessary.
However, the strength of the weld is relatively low and cannot be improved through post-weld heat treatment.
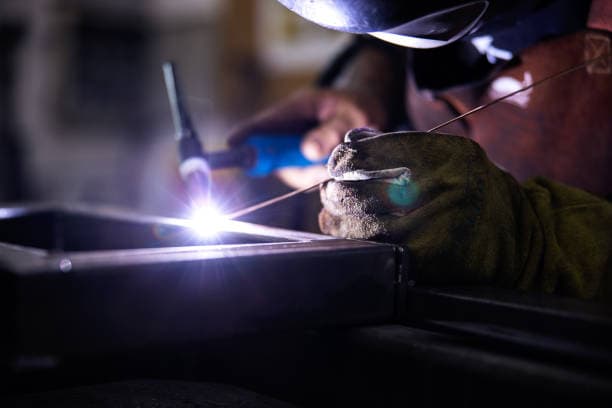
4. Common Welding Problems
(1) Cold crack welding
Martensitic stainless steel has a high chromium content, which significantly increases its hardening capacity.
Regardless of its initial state before welding, welding always results in the formation of martensite near the seam.
As the hardening tendency increases, the joint becomes more prone to cold cracking, especially when hydrogen is present. Under these conditions, martensitic stainless steel is also prone to the formation of dangerous hydrogen-induced delayed cracks.
M measurements:
- A high wire energy welding current can slow down the cooling rate.
- Different types of steel require different interpass temperatures, which must not be lower than the preheating temperature.
- A slow cooling process after welding to 150-200°C, followed by a post-weld heat treatment, is necessary to eliminate welding residual stress, remove diffusible hydrogen in the joint, and improve joint structure and properties.
(2) Fragility of the heat-affected area
Martensitic stainless steels, particularly those with higher levels of ferrite-forming elements, have a greater tendency to grain growth.
A slow cooling rate can lead to the formation of coarse ferrite and carbide in the welding heat-affected zone (HZ), while a fast cooling rate can cause hardening and the formation of coarse martensite in the HAZ.
These coarse structures reduce the plasticity and toughness of the HAZ of martensitic stainless steel, making it brittle.
Countermeasures:
- Maintain an adequate cooling rate;
- Selecting a reasonable preheating temperature. The preheating temperature should not exceed 450°C, as prolonged exposure to high temperatures above this limit may cause embrittlement at 475°C.
- Choose welding materials wisely to adjust the weld composition and minimize the presence of coarse ferrite in the weld.
5. Welding process
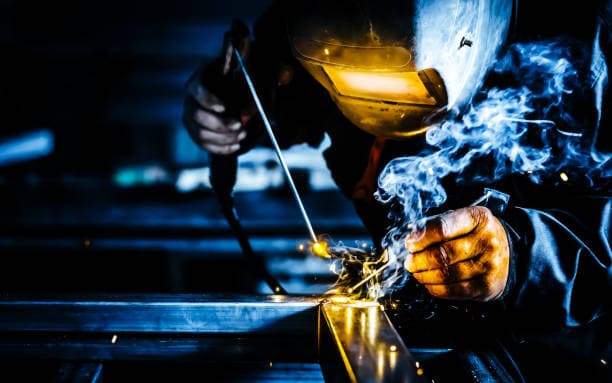
1) Preheating before welding
Preheating before welding is a crucial technique to prevent cold cracking.
For carbon content between 0.1% to 0.2%, the preheating temperature should be between 200 to 260°C, while high strength welding can be preheated to a temperature between 400 to 450°C .
2) Cooling after welding
The weldment should not be heated directly from the welding temperature for tempering treatment because the austenite may not be fully transformed during welding.
Immediate heating and tempering after welding can cause carbides to precipitate along the austenite grain boundary, resulting in the transformation of austenite to pearlite and a coarse-grained structure, which significantly reduces toughness.
Therefore, the weldment must be cooled before tempering, and the austenite in the weldment and heat-affected zone must be largely decomposed.
For low strength welds, they can be cooled to room temperature and then tempered.
For thick welds, a more complex process is required. After welding, it must be cooled to 100-150°C, kept warm for 0.5-1 hour, and then heated to the tempering temperature.
3) Post-welding heat treatment
The objective of post-welding heat treatment is to reduce the hardness of the weld and the heat-affected zone, increase its plasticity and toughness and reduce the welding residual stress.
Post-weld heat treatment may include quenching and full annealing. The tempering temperature must be between 650-750°C, with a waiting time of 1 hour followed by air cooling.
If welding requires machining after welding, full annealing may be performed to achieve minimum hardness.
The annealing temperature should be between 830-880°C, with a holding time of 2 hours followed by oven cooling to 595°C and then air cooling.
4) Welding rod selection
Electrodes for welding martensitic stainless steel are classified into two categories: chromium stainless steel electrodes and chromium-nickel austenitic stainless steel electrodes.
Common chromium stainless steel electrodes include E1-13-16 (G202) and E1-13-15 (G207).
Common chromium-nickel austenitic stainless steel electrodes include E0-19-10-16 (A102), E0-19-10-15 (A107), E0-18-12Mo2-16 (A202), and E0-18-12Mo2- 15 (A207), among others.
6. Duplex Stainless Steel Welding
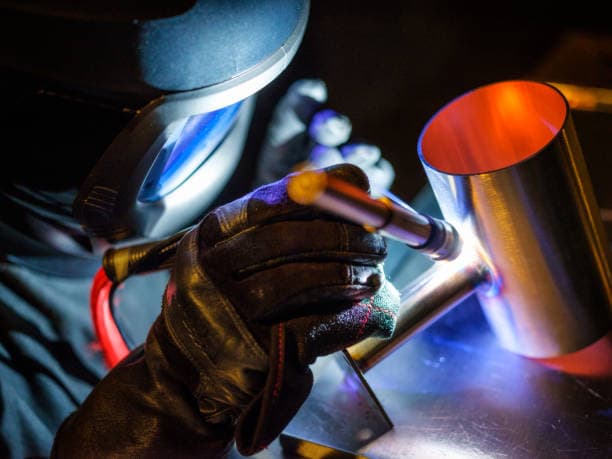
1. Weldability of duplex stainless steel
Duplex stainless steel has advantages and disadvantages of austenitic and ferritic steel and reduces their respective weaknesses.
(1) The risk of hot cracking is much lower compared to austenitic steel.
(2) The risk of cold cracking is significantly lower compared to ordinary low-alloy, high-strength steel.
(3) After cooling in the thermally affected zone, a greater amount of ferrite is retained, increasing the risk of corrosion and hydrogen-induced cracking (embrittlement).
(4) Duplex stainless steel welded joint is prone to precipitation of δ phase, an intermetallic compound of Cr and Fe.
Its forming temperature varies from 600°C to 1000°C and can vary according to the specific type of steel.
Table 1 Solution treatment temperature range, δ phase and 475℃ brittleness of duplex stainless steel
Happy | Two-phase steel 2205 and 2507, etc. | Super duplex steel 00Cr25Ni7Mo3CuN |
Solid solution temperature/℃ | 1040 | 1025~1100 |
Peeling temperature when heated in air/℃ | 1000 | 1000 |
Phase formation temperature δ/℃ | 600~1000 | 600~1000 |
Embrittlement temperature of 475°C/℃ | 300~525 | 300~525 |
2. Selection of welding methods
The welding process for duplex stainless steel first involves TIG welding, followed by stick arc welding.
When using submerged arc welding, heat input and inter-pass temperature must be closely monitored and excessive dilution must be avoided.
Observation:
When TIG welding is used, 1-2% nitrogen should be added to the shielding gas (adding more than 2% nitrogen may increase porosity and cause arc instability). The addition of nitrogen helps to absorb nitrogen from the weld metal, preventing the loss of nitrogen by diffusion into the surface area of the weld and helps to stabilize the austenite phase in the weld joint.
3. Selection of welding materials
Welding materials with higher levels of austenite-forming elements (such as Ni, N) are chosen to encourage the transformation of ferrite in the weld into austenite.
The 22.8.3L electrode or welding wire is commonly used to weld 2205 steel, while the 25.10.4L electrode or 25.10.4R electrode is often used to weld 2507 steel.
Table 2 Typical Duplex Stainless Steel FN and Welding Materials
Base metal | Welding Material | Chemical composition | Name | FN(%) | ||||||||
W | Yes | Mn | Cr | Ni | Mo | N | Ass | W | ||||
2507 | Welding Wire | 0.02 | 0.3 | 0.5 | 25 | 10 | 4 | 0.25 | – | – | 2507/P100 | 40~100 |
0.02 | 25 | 10 | 4 | 0.25 | – | – | Sandivic 25.10.4L | |||||
Welding Core | 0.03 | 0.5 | 1 | 25 | 9.5 | 3.6 | 0.22 | – | – | Avesta 2507/p100 | ||
0.04 | 25 | 10.5 | 4 | 0.25 | – | – | Sandivic 25.10.4L | |||||
Zeron100 | Welding wireWelding core | 0.04 | 1.2 | 2.5 | 25 | 10 | 4 | 0.22 | 1 | 1 | 22.9.4CuWL 22.9.4CuWLB |
40~60 |
2205 | Welding Wire | 0.02 | 0.5 | 1.6 | 22.5 | 8 | 3 | 0.14 | – | – | Sandivic 22.8.3L | 40~60 |
Welding Core | 0.03 | 1.0 | 0.8 | 22.5 | 9.5 | 3 | 0.14 | – | – | Sandivick 22.8.3R |
4. Welding points
(1) During the welding process, control of welding energy, inter-pass temperature, preheating and material thickness will affect the cooling rate and subsequently affect the structure and properties of the weld and the heat-affected zone.
To obtain ideal properties of the weld metal, it is recommended to control the maximum temperature between passes at 100°C. If post-weld heat treatment is required, inter-pass temperature restrictions may be lifted.
(2) It is preferable to avoid post-welding heat treatment for duplex stainless steel.
If post-weld heat treatment is required, the method used is water quenching. During heat treatment, heating must be rapid and the maintenance time at heat treatment temperature must be between 5-30 minutes, sufficient to restore phase balance.
Metal oxidation is a concern during heat treatment, so the use of an inert gas for protection should be considered.