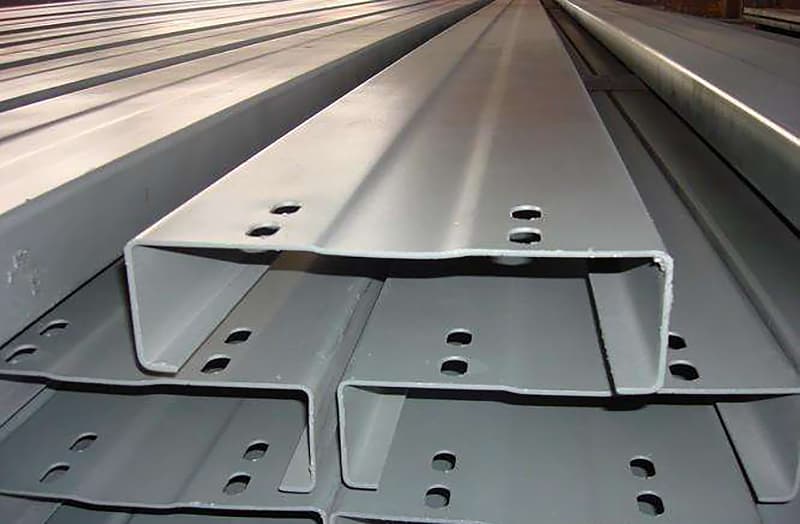
Ultra low carbon baking hardening steel for automobiles (ULC-BH steel) is a high quality automotive steel with low yield strength before stamping.
After stamping or pre-stretching deformation, the yield strength can be improved to a certain extent by baking temperature aging treatment.
For bake-hardening steel, the content of solid solution elements, especially the solid solution carbon content, is the most important factor affecting its bake-hardening property (i.e., the bake-hardening value BH2 ), therefore, it is necessary to carry out quantitative analyzes of the carbon content in solid solution.
Because the relationship between the solid solution carbon content in ultra-low carbon bake hardening steel and the processes of hot rolling, cold rolling and BH 2 values are complex, researchers such as Shi Xing and Ju Xinhua from the Institute of Technical Research of Shougang Group Co., Ltd. hope to establish the relationship between the carbon content of the solid solution and the BH 2 value of the final product using internal friction technology and thus find the best process parameters that take mechanical properties into consideration of materials and apply them to guide actual production.
The researchers mainly simulated and investigated the influence of different hot-rolling temperatures, annealing temperatures and slow cooling temperatures on the carbon content of solid solution and BH. 2 test steel value for ultra-low carbon baking hardening steel, so as to provide a theoretical basis for on-site process improvement of baking hardening steel.
1. Test materials and methods
1.1 Test materials
The test material is a hot-rolled ULC-BH steel plate with a thickness of 4.5 mm.
In the pilot-scale simulation laboratory, process simulation was carried out according to different hot winding temperatures, different annealing temperatures and slow cooling temperatures to investigate the change rule of solid solution carbon content and BH 2 value of test steel under different processes.
The specific simulation process is:
① Hot-rolled plates with the same composition are hot-rolled and wound at different winding temperatures (660, 700, 730 ℃), and then products with different hot-rolled winding temperatures are cold-rolled and then annealed at 780 ℃, with a strip speed of 200m · min -1 ;
②700℃ hot-rolled coils with the same composition are annealed at different temperatures (780, 810, 840℃) after cold rolling;
③ Test plates with the same composition after hot rolling and crimping at 700 ℃ and annealing at 780 ℃ were slowly cooled at different slow cooling temperatures (650, 680, 710 ℃).
1.2 Test method
The rectangular sample of 55 mm × 4 mm × 1 mm to be tested shall be processed with a steel carbon analyzer according to the method specified in GB/T 13665-2007 Test methods for damping power of metallic damping materials – Torsional pendulum method and bending vibration method for internal friction test.
The universal tensile testing machine is used to measure the increase value of the lowest yield strength of the pre-stressed sample with 2.0% total strain after baking at 170℃ for 20min, which is BH 2 value, relative to the resistance corresponding to 2.0% of total deformation of the sample, in accordance with the national standard GB/T 24174-2009 Determination of the baking hardening value (BH 2 ) of steel.
2. Test results and analysis
2.1 Effect of different crimping temperatures
The change curves of internal friction, solid solution carbon content and BH 2 value of test steel at different crimping temperatures are shown in Fig.
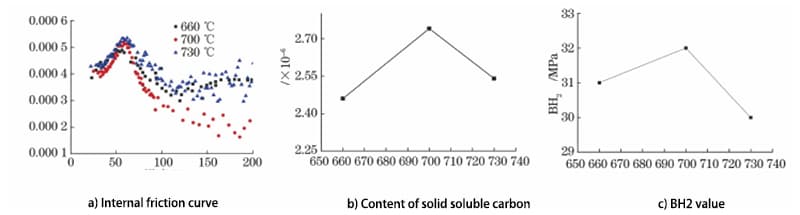
Fig. 1 Internal friction curve, carbon content in solid solution and BH 2 value of ULC-BH steel at different crimping temperatures
It can be seen from Figure 1a) that under the crimping temperature of 660, 700, 730 ℃, the internal friction test of ULC-BH test steel shows an obvious C-Snoek peak near 50 ℃, but with increasing of the crimping temperature, the height of the C-Snoek peak has little difference, about 0.00055.
Using the linear relationship between the internal friction peak caused by solid solution carbon and solid solution carbon, it can be quantitatively calculated that the corresponding solid solution carbon content (mass fraction, the same as below) to 660, 700, 730 ℃ is 2.46 × 10 -6 , 2.74 × 10 -6 , 2.54 × 10 -6 .
From the calculation results, it can be seen that the crimping temperature has little effect on the solid solution carbon content of the test steel, and the difference is 0.3 × 10 -6 as shown in Fig. 1b ).
It can also be seen from Fig. 1c) that the winding temperature has no significant effect on the BH 2 value of the final product.
2.2 Effect of annealing temperature
The change curves of internal friction, solid solution carbon content and BH 2 value of test steel at different annealing temperatures are shown in Fig.
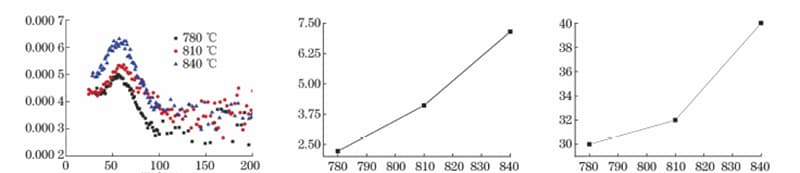
Fig. 2 Internal friction curve, solid solution carbon content and BH2 value of ULC-BH steel at different annealing temperatures
It can be seen from Figure 2 that the annealing temperature is very sensitive to the influence of the carbon content of the solid solution and the BH 2 value in ULC-BH test steel.
Under the annealing temperature of 780810840 ℃, the internal friction test of ULC-BH test steel also shows an obvious C-Snoek peak near 50 ℃;
The annealing temperature increased from 780 ℃ to 840 ℃, and the peak value of C-Snoek internal friction increased from 0.00050 to 0.00065.
Proper calculation of the C-Snoek internal friction peak at different annealing temperatures in Fig. 2a) shows that the carbon content of the solid solution corresponding to 780, 810, 840 ℃ is 2.22 × 10 -6 , 4.11 × 10 -6 ,7.15 × 10 -6 i.e., the carbon content in solid solution increases with increasing annealing temperature, with a range of 2 × 10 -6 ~3 × 10 -6 as shown in Fig. 2b).
It can be seen from Fig. 2c) that the BH 2 value of the test steel also increases with increasing annealing temperature.
2.3 Effect of slow cooling temperature
The change curves of internal friction, solid solution carbon content and BH 2 value of test steel under different slow cooling temperatures are shown in Fig.
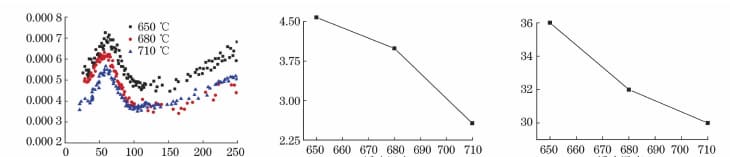
Fig. 3 Internal friction curve, carbon content in solid solution and BH 2 value of ULC-BH steel at different slow cooling temperatures
It can be seen from Figure 3 that the slow cooling temperature is also very sensitive to the influence of the carbon content of the solid solution and BH. 2 value in ULC-BH test steel.
Under different slow cooling temperatures of 650680710℃, the internal friction test of ULC-BH test steel shows an obvious C-Snoek peak near 50℃, but when the slow cooling temperature increases from 650℃ to 710℃, the peak value of C-Snoek internal friction decreases from 0.00072 to 0.00055.
Proper calculation of the C-Snoek internal friction peak at different slow cooling temperatures in Fig. 3a) shows that the carbon content of the solid solution corresponding to 650, 680, 710 ℃ is 4.58 × 10 -6 .3, 99 × 10 -6 ,2.57 × 10 -6 .
That is, when the slow cooling temperature is 650 ℃ and 680 ℃, there is little difference in the carbon content in solid solution in the steel sample, but the slow cooling temperature increases from 680 ℃ to 710 ℃, and the content of solid solution carbon decreases with increasing slow cooling temperature, with a range of about 1.5 × 10 -6 as shown in Fig. 3b).
It can be seen from Fig. 3c) that the BH 2 value of the test steel also decreases with increasing slow cooling temperature.
3. Conclusion
(1) Different process parameters have great influence on the solid solution carbon content and BH 2 value of ultra-low carbon bake hardening steel, while the crimping temperature has little influence on the solid solution carbon content and BH 2 value of the test steel.
(2) With the increase of annealing temperature, the solid solution carbon content and BH 2 value of the test steel gradually increases, and the annealing temperature increases from 780 ℃ to 840 ℃, the solid solution carbon content increases in 2 × 10 -6 ~3 × 10 -6 .
(3) With the increase of the slow cooling temperature, the carbon content of the solid solution and the BH 2 value of the test steel gradually decreases, and the slow cooling temperature increases from 650 ℃ to 710 ℃, and the carbon content carbon in the solid solution decreases by about 1.5 × 10 -6 .