1. Preface
This article discusses the impact of surface carbon concentration on the heat treatment properties of 20CrMo steel.
To ensure the desired carbon content in the furnace atmosphere during the entire carburizing process and the required carbon concentration on the part surface after carburizing, the carbon concentration in the carburizing process must be meticulously regulated. Furthermore, optimizing the quenching process can help achieve better quenching hardness, resulting in good wear resistance.
20CrMo steel is a low-alloy carbon structural steel widely used in the production of a variety of workpieces such as gears, shafts and high-strength fasteners. For example, in the production of a company, this material is used in the construction of the hydraulic cylinder of the hydraulic crusher in construction machines.
In order for the hydraulic cylinder to meet the high hardness and wear resistance required by post-carburizing heat treatment, as well as good plasticity and toughness (i.e. excellent comprehensive mechanical properties), targeted research was required.
However, during initial production of the hydraulic cylinder, the surface hardness of the part was low, and this problem persisted despite efforts to correct it by adjusting process conditions. As a result, a focused study was conducted on the workpiece.
2. Heat treatment process, technical requirements and problems of hydraulic cylinder
This type of hydraulic cylinder has a large volume, with a unit weight of approximately 365kg and an effective thickness of 150-200mm.
See Figure 1 for a visual representation of the actual workpiece.
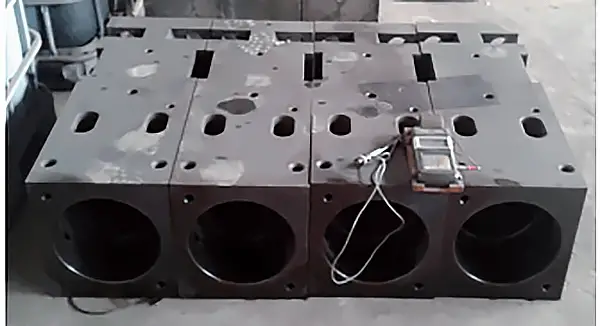
After undergoing heat treatment, carburizing and quenching, the workpiece should have a carburizing layer depth of 1.0-1.4mm and an overall hardness of 58-62HRC.
See Table 1 for chemical composition specifications of 20CrMo steel in GB/T 3077-1999 alloy structural steel.
Table 1 Chemical composition of 20CrMo steel (mass fraction) (%)
W | Mn | Yes | Cr | Mo | P | s |
0.17~0.24 | 0.4~0.7 | 0.17~0.37 | 0.80~1.10 | 0.15~0.25 | ≤0.035 | ≤0.035 |
Various process methods are used for treatment during actual production. However, the results indicate that the surface hardness is below 50HRC, making it unqualified. Adjusting the carburizing temperature and increasing the quenching temperature cannot meet the technical requirements.
For specific details on the heat treatment process, see Table 2.
Table 2 heat treatment process
NO. | Process parameters | Part surface hardness (HRC) |
1 | Strong permeability: 920℃×330min, carbon potential 1.1%; Diffusion: 920℃x130min, carbon potential 0.85%; Insulation quenching: 830℃×30min, carbon potential 0.85%. |
45~47 |
two | Strong permeability: 920℃×350min, carbon potential 1.1%; Diffusion: 920℃×140min, carbon potential 0.9%; Quenching and heat preservation: 840℃x30min, carbon potential 0.9%. |
46~47 |
3 | Strong permeability: 930℃×330min, carbon potential 1.2%; Diffusion: 930℃ x 30min, carbon potential 0.9%; Insulation quenching: 860 ℃ × 40 min, carbon potential 0.9%. |
49~50 |
4 | Strong penetration: 930℃x450min, carbon potential 1.2%; Diffusion: 930℃×250min, carbon potential 0.9%; Quenching and heat preservation: 860℃x30min, carbon potential 0.9%. |
46~48 |
3. Cause analysis of low surface hardness of hydraulic cylinder
(1) Carburizing temperature
Carburizing temperature is a crucial technological parameter in the carburizing process and significantly affects the ability of austenite to dissolve carbon.
As the temperature increases, the solubility of carbon in austenite also increases.
According to the iron-carbon phase diagram, the saturated solubility of carbon in austenite is 1.0% at 850°C and 1.25% at 930°C.
The accuracy of the carburizing temperature directly affects the quenching quality of the part.
After performing a 9-point temperature detection of the equipment, we found no deviation in temperature, the oven temperature is normal, and no significant temperature difference is present.
Therefore, we can exclude the influence of temperature on the surface hardness of the part.
(2) Effect of carbon concentration
During process execution, a furnace test block measuring 25mm x 25mm is used for each process number.
The hardness test results of the test block are better than those of the workpiece body.
See Table 3 for the hardness test results of the case-hardened test block performed according to process 3, both on the end face and in the longitudinal direction of the part.
Table 3 Part hardness test results (HRC)
Surface |
Essential |
|||||
Final face |
59 |
60 |
58.5 |
59.6 |
20 |
21 |
Portrait |
56.6 |
57.5 |
55.2 |
56 |
According to the hardness method specified in GB/T 9450-2005 to determine and check the effective depth of the carburizing and quenching hardened layer of iron and steel, the hardness gradient of the carburizing layer is tested in the furnace test block after the heat treatment process.
The results are shown in Table 4.
Table 4 Results of the hardness gradient test of the part penetration layer
Carburizing layer depth / mm | HV1 hardness |
0.1 | 622.9 |
0.2 | 747.7 |
0.3 | 714.4 |
0.4 | 720 |
0.5 | 685.8 |
0.6 | 662.7 |
0.7 | 635.9 |
0.8 | 635.9 |
0.9 | 599.9 |
1 | 568.8 |
1.1 | 540 |
The case-hardened layer of the test block is examined using the metallographic analysis method to verify that the carbon concentration meets the required specifications.
Figure 2 illustrates the metallographic structure of the surface layer and the effective depth of the hardened layer of the part.
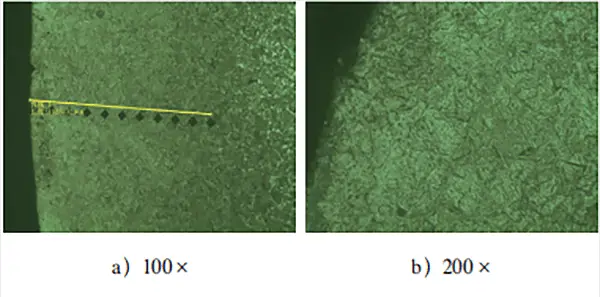
After observing the metallographic structure of the carburized layer of the test block in Fig. 2, it was found that the surface layer mainly comprises needle-shaped martensite and residual austenite. No significant carbide composition was detected.
Furthermore, effective detection of the depth of the hardened layer revealed that the test block showed a clear “head up” phenomenon after carburizing treatment. This suggests that there was a noticeable oxidation atmosphere in the carburized layer, resulting in low surface hardness and increased step hardness.
To better examine the microstructure of the infiltrated layer of the test block of the part, the test block was annealed. The annealing process involved cooling the test block from 860℃×30min to 500℃ using the oven, followed by air cooling.
Metallographic samples were prepared and examined to observe the balance of the metallographic structure of the carburized 20CrMo steel parts, as shown in Figure 3.
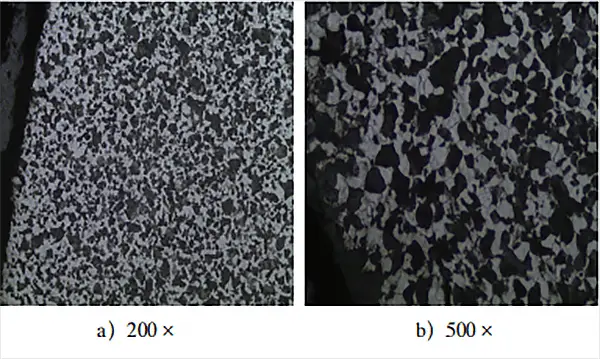
Based on the observation of the equilibrium metallographic structure in Fig. 3, the microstructure morphology of the carburizing layer in low-carbon steel after slow cooling is significantly different from that of normal low-carbon steel. The hypereutectoid layer, eutectoid layer and transition layer in the carburizing layer cannot be distinguished clearly and effectively.
The microstructure of low carbon steel after carburizing and slow cooling must comprise a surface layer of pearlite and liquid cementite, a eutectoid structure inside, a subeutectoid structure transition zone and the original structure.
As for the equilibrium structure in Fig. 3, its morphology and structure are most similar to the equilibrium structure obtained after annealing ordinary medium-carbon steel, which has a uniformly distributed pearlite and ferrite structure. No obvious cementite was found, indicating that the carbon potential of the carburizing atmosphere in the furnace is insufficient to ensure sufficient carbon concentration on the surface of the part.
Therefore, to obtain a suitable carbon concentration on the surface of the part and form an effective carbon concentration gradient, it is necessary to increase the carbon potential when the carburizing temperature is normal.
4. Improvement of process methods and conditions
The diffusion of carbon atoms from the surface to the center is necessary for carburizing and to reach a certain depth of the carburizing layer.
The driving force behind diffusion is the carbon concentration gradient between the surface and the core.
To improve the carburizing effect, it is crucial to absorb the activated carbon atoms in time to ensure the uniform circulation of the furnace atmosphere. The rate of carbon atoms supplied (decomposition rate) must match the absorption rate to avoid insufficient supply and carbon deposition.
Through the analysis of the original process bonds and test blocks, it was found that the low hardness of the real part was mainly due to the low carbon concentration on the surface of the carburizing layer caused by insufficient atmosphere in the furnace. This resulted in an ineffective carburizing treatment, preventing the formation of an ideal carburizing layer structure and achieving sufficient hardness.
To resolve this, targeted rectification measures were taken to overhaul the equipment, replace the carbon potential monitoring equipment, check the tightness of the furnace body, and re-perform the carbon determination treatment in the furnace atmosphere to ensure uniformity and accuracy of the furnace atmosphere.
After reevaluating the furnace conditions and redefining the parameters of the carburizing and tempering process, production can continue.
See Table 5 for adjusted heat treatment process.
Table 5 adjusted heat treatment process
NO. | Process parameters | Part surface hardness (HRC) |
1 | Strong penetration: 930℃x450min, carbon potential 1.3%; Diffusion: 930℃ x 30min, carbon potential 1.0%; Insulation quenching: 850℃×30min, carbon potential 1.0%; Quenching: 150℃x240min |
62.6, 623, 62.1, 62.4, 62.9, 62.8 |
two | Strong permeability: 920 ℃ × 450 min, carbon potential 1.3%; Diffusion: 920℃x30min, carbon potential 1.0%; Quenching and heat preservation: 840℃x30min, carbon potential 1.0%; Quenching: 180℃x240min |
59.4, 613, 60.1, 59.4, 60.9, 60.1 |
The metallographic structure of the infiltrated layer of the test block treated by the adjusted heat treatment process is shown in Figure 4.
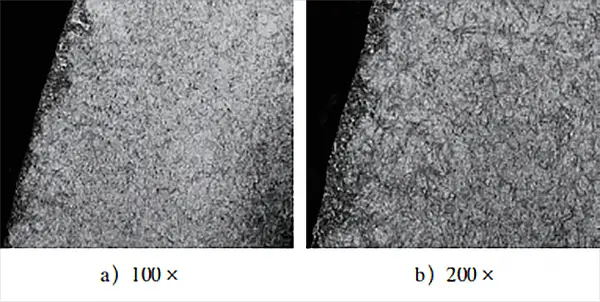
Figure 4 illustrates that the metallographic structure consists mainly of fine tempered martensite, fine-grained carbide, and a small amount of residual austenite, which aligns with the normal carburizing and quenching structure. This ensures an effective surface hardness and an overall surface hardness of the part that meets the range required by the technical conditions.
To obtain a better understanding of the microstructural changes before and after specific adjustments to the heat treatment process, the test block is subjected to annealing with the same process.
The annealing process involves heating the block to 860℃ for 30 minutes, cooling it to 500℃ in the furnace, and finally cooling it in air.
Metallographic samples were prepared to observe the equilibrium structure of carburized 20CrMo steel parts.
Figure 5 demonstrates the annealed structure after the heat treatment of the tuning process.
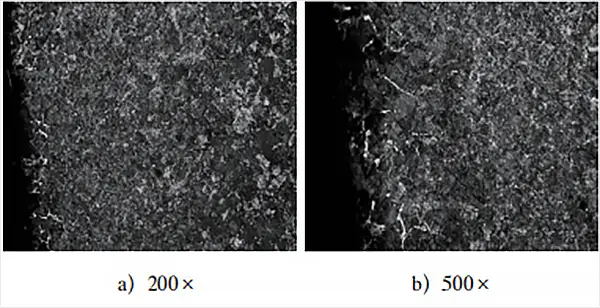
Figure 5 clearly shows the presence of pearlite and cross-linked cementite, and a comparison of the surface layer structure in Figure 3 highlights the difference between them.
The structure depicted in Fig. 3 resembles the equilibrium structure of common medium-carbon steel after annealing, with a carbon content (mass fraction) of around 0.5%.
In contrast, the equilibrium structure in Fig. 5 displays the pearlite + cementite network structure that results from normal carburizing annealing.
This change in structure suggests that there was a significant problem with the furnace atmosphere under the original process conditions. As a result, the carburizing conditions of the parts did not meet the defined requirements, causing the parts to fall short of the specified technical requirements after the process treatment.
5. Conclusion
- The slowly cooling solid phase transformation structure of low-alloy carbon structural steel after carburizing and quenching can be used to determine the carbon content in the final carburized layer. This, in turn, helps determine whether the furnace atmosphere meets the required standards.
- Although increasing the carbon potential can enhance the carburizing effect to a certain extent, the limited saturated solubility of carbon in austenite necessitates a flexible setting of the carbon potential based on actual conditions to avoid the possibility of carbon deposition.
- The precision of the carburizing treatment equipment will have a direct impact on the final heat treatment results.