Cast aluminum” generally refers to aluminum castings made through the casting process, while “cast aluminum” refers to aluminum castings made through high-pressure die casting. The main difference between the two is the casting process used.
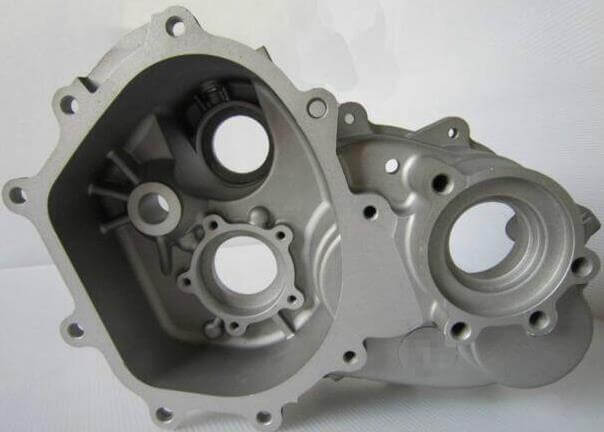
In the casting process, methods such as sand casting, dewaxing casting, gravity casting, low pressure casting, ceramic mold casting and plaster mold casting are used. The die casting process, on the other hand, is a type of pressure casting produced in a cold chamber die casting machine.
The aluminum grades used in the two processes are different, with ZL representing cast aluminum alloys in China's GB national standard and YL representing cast aluminum alloys.
Cast aluminum castings can typically be strengthened through heat treatment, with T6 heat treatment being the most common method. However, castings are not suitable for T6 heat treatment due to the large amount of densely distributed gas within them. This is because the T6 heat treatment temperature is close to the melting point of aluminum alloys, and the gas in pressure casting will expand and be forced out of the surface of the casting, causing damage to the surface and rendering the casting unusable.
Due to the point protrusion after the gas runs out, the appearance of the casting is seriously damaged and cannot be used.
Aluminum alloy gravity casting and aluminum alloy low pressure casting belong to the metal mold casting process and are used to produce aluminum castings. The molds are made of hot work steel such as H13.
These casting processes can produce the same brand of cast aluminum alloy, with similar pouring temperature and mold opening time, as well as compactness, strength and other mechanical properties of aluminum castings.
However, there are still differences between aluminum alloy gravity casting and aluminum alloy low pressure casting in terms of forming principle, aluminum casting structure, labor intensity, batch number, development time, etc., as shown in the figure below.
Formation principle | Aluminum die-casting structure | work intensity | Minimum lot | Development time | Mold cost | |
---|---|---|---|---|---|---|
Aluminum alloy gravity casting | Using gravity | Complex and diverse | high | 100 | short | any less |
Aluminum alloy low pressure casting | Using air pressure | single | commonly | 500 | far away | Higher |
According to the comparison shown above, aluminum alloy gravity casting is ideal for producing products with multiple varieties, small batches, short development cycles and high quality requirements, while aluminum alloy low pressure casting It is ideal for products with large batches, thin walls and structures suitable for the low pressure casting process.
The long development cycle of the latter benefits the improvement of production technology throughout the manufacturing process.
A typical product produced by low pressure casting in aluminum alloy is the rim of an automobile wheel. Its structure is suitable for the low pressure casting process and the high production volume allows enough time to improve the production technology.
In contrast, typical products produced by aluminum alloy gravity casting are industrial robot castings. These aluminum castings require small production batches, high quality products and a short development cycle. The aim is to produce high-quality aluminum castings, without pores or sand holes, in a very short time.
Aluminum Die Casting: An Overview
Aluminum die casting is a widely used manufacturing process that offers several advantages in creating parts and components for various industries. This process involves forcing molten aluminum into a mold cavity under high pressure to create complex shapes that can be difficult to produce through other methods such as extrusion or machining.
There are different aluminum alloys used in pressure casting, the most common being 383 and 413. These aluminum alloys have characteristics such as high operating temperatures, corrosion resistance and lightweight properties. Additionally, they provide excellent rigidity, strength-to-weight ratio, and effective EMI and RFI shielding capabilities.
The pressure casting process itself comprises several steps. First, the mold cavity, also known as the die, is prepared with a release agent to facilitate removal of the part after solidification. Next, molten aluminum is injected into the mold cavity under extreme pressure. After the aluminum solidifies, the die opens and the aluminum casting is ejected. The process allows for efficient, high-volume production of aluminum parts, leading to cost savings compared to other manufacturing techniques.
Some essential factors to consider during your aluminum casting project include:
- Part complexity: Die casting allows the creation of highly complex shapes and intricate designs that may not be possible with other methods.
- Dimensional Accuracy: The process offers high accuracy for complex geometries, contributing to tight tolerances and consistent repeatability across numerous castings.
- Surface Finish: Aluminum castings can be given various surface finishes to improve aesthetics, durability or other performance parameters.
In conclusion, aluminum casting is an efficient manufacturing process suitable for producing complex and intricate parts. With its multiple benefits and versatile applications, it remains a popular choice in industries ranging from automotive and aerospace to consumer electronics and more.
The pressure casting process
Pressure paper
In aluminum casting, high pressure plays a significant role in creating precise, high-quality parts. Molten aluminum is forced into the mold cavity using high pressure, ensuring the material completely fills the mold and reaches every detail of the complex shape. This pressure helps produce a part with tight tolerances and a smooth surface finish.
Solidification and Cavities
Once the molten aluminum fills the mold cavity, it begins to solidify and take the shape of the desired part. During this solidification process, it is essential to avoid the formation of cavities and voids that could compromise the structural integrity and performance of the part. To ensure perfect casting, adequate temperature control, ventilation and pressurization are important factors in preventing cavities and unwanted defects.
Draft and parting line considerations
Draft and parting lines are two critical aspects of the die casting process that influence the quality of the final product. Draft refers to the angle or taper applied to the side walls of the mold to facilitate ejection of the solidified part. Proper draft ensures smooth removal of the part without causing damage or distortion.
Parting lines, on the other hand, are the lines where two halves of the mold meet. Proper positioning and design of parting lines is essential to minimize burrs (excess material) and obtain a clean, accurate final product.
Creating complex shapes
Aluminum die casting is known for its ability to create complex shapes with intricate details. Features such as holes and windows, protrusions and ribs can be easily achieved by incorporating them into the mold design. This versatility enables the production of lightweight, high-strength components used in a variety of industries, including automotive, aerospace and electronics. Careful design and planning, combined with the efficient use of high pressure and solidification control, enable the production of aluminum die castings with complex geometries and excellent performance.
Characteristics of cast aluminum parts
Mechanical properties
Cast aluminum parts are known for their light weight, which makes them an excellent choice for many applications. They have a good strength/weight ratio, ensuring a balance between durability and ease of use. The hardness of cast aluminum parts varies depending on the specific alloy used. However, most aluminum molds have considerable tensile strength, providing resistance to deformation and breakage under load.
Thermal and Electrical Characteristics
Aluminum molds exhibit high operating temperatures, making them suitable for applications requiring heat resistance. Its thermal conductivity is also remarkable, allowing for efficient heat transfer and rapid cooling when needed. Additionally, cast aluminum parts provide excellent electrical conductivity, acting as effective shields against electromagnetic interference (EMI) and radio frequency interference (RFI) in electronic devices.
Corrosion and wear resistance
One of the main benefits of using cast aluminum parts is their exceptional corrosion resistance. This makes them suitable for use in harsh environments where they may be exposed to moisture or corrosive substances. Additionally, aluminum molds are wear-resistant, ensuring longevity and reducing the need for frequent maintenance or replacement.
Efficiency and Volume
Aluminum pressure casting is an efficient process, as it allows the large volume production of parts with complex geometries. Tolerances of ±0.002″ to ±0.004″ can generally be achieved for aluminum casting, providing accurate and consistent results. This efficiency makes it an ideal choice for industries that require large quantities of precision components, such as automotive and aerospace.
Cast Aluminum Applications and Uses
Cast aluminum is a versatile material, finding applications in a wide range of industries due to its favorable mechanical properties and ease of fabrication. In this section, we will explore the uses of cast aluminum in various sectors, including automotive, industrial, and electronics.
Automotive industry: The automotive sector benefits significantly from cast aluminum parts as they contribute to weight reduction and improve fuel efficiency. Aluminum's lightweight and durable properties make it an ideal material for automotive components such as engine blocks, transmission cases, and structural parts of a vehicle's chassis. Additionally, aluminum alloys can withstand high temperatures, making them suitable for automotive applications where heat dissipation is crucial.
Industrial applications: In the industrial sector, die-cast aluminum plays an essential role in the manufacture of equipment and machines. Due to its high strength-to-weight ratio, corrosion resistance and ability to withstand varying temperatures, aluminum die castings are used in diverse applications such as heavy machinery, pumps, valves and industrial tools. These properties allow manufacturers to reduce material costs, improve performance and extend the life of their equipment.
Electronic Connectors and Housings: Aluminum die casting is widely used in the electronics industry to produce complex shapes and designs for connectors and housings. The material's excellent thermal and electrical conductivity, along with its low cost, make it ideal for producing parts used in RF filter housings, heat dissipation and networking equipment. Die-cast aluminum housings also provide excellent EMI shielding, ensuring electronic devices operate efficiently and reliably.
In summary, cast aluminum offers numerous advantages across multiple industries, including automotive, industrial and electronics. Its impressive properties such as light weight, high strength-to-weight ratio, corrosion resistance and conductivity make it an ideal choice for manufacturing durable, efficient and cost-effective components.