Currently, aluminum is the most used material for electronic heat sinks. Its characteristics are very suitable for manufacturing heat sinks due to its good thermal conductivity, low cost and high resistance to atmospheric corrosion.
The following are the properties of pure aluminum and aluminum alloys used in the heat sink industry, providing a deeper understanding of aluminum and aluminum alloys.
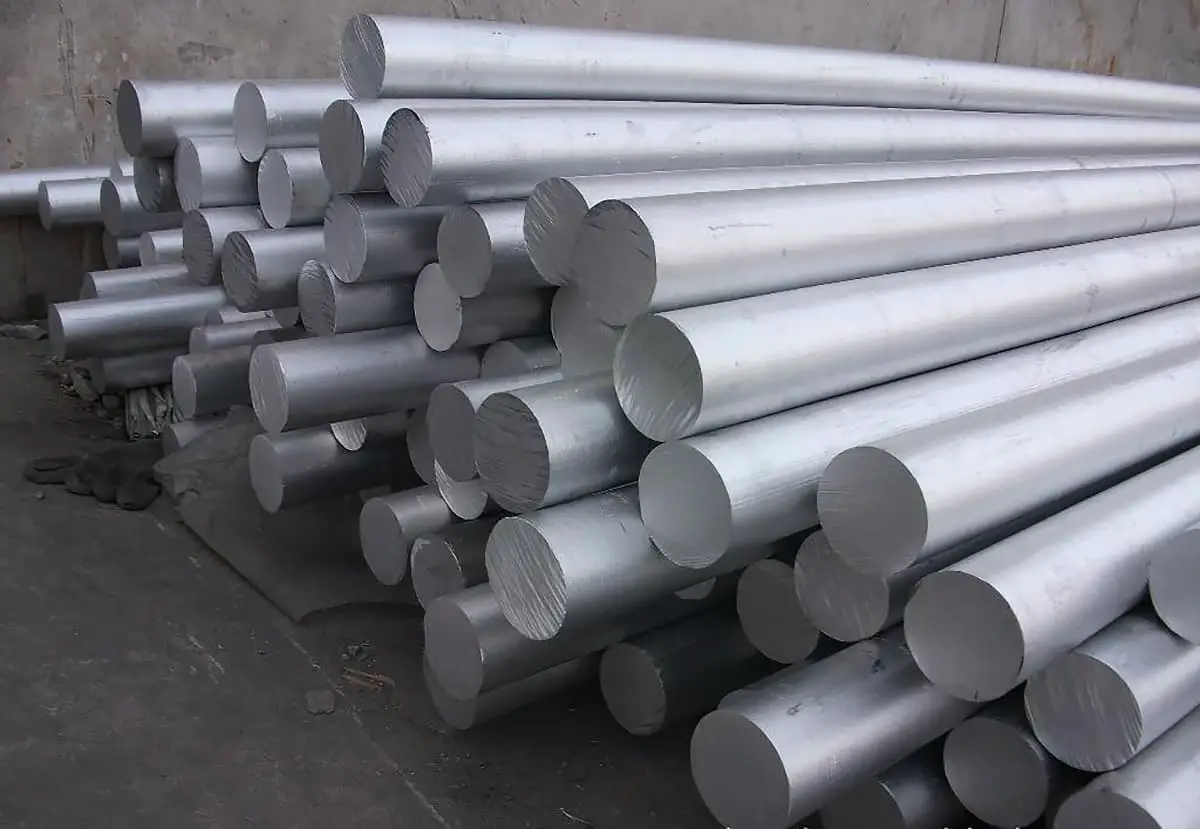
1. Pure Aluminum
Density:
Aluminum is a very light metal, with a density of 2.72 g/cm³, about a third of the density of pure copper.
Electrical and Thermal Conductivity:
Aluminum has excellent electrical and thermal conductivity. When the cross-sectional area and length of aluminum are the same as those of copper, the electrical conductivity of aluminum is about 61% of that of copper.
If the weight of aluminum is the same as that of copper, but the cross-sectional area is different (with equal length), the electrical conductivity of aluminum is 200% of that of copper.
Chemical properties:
It has good resistance to atmospheric corrosion due to the formation of a dense aluminum oxide film on its surface, which prevents further oxidation of the internal metal. Aluminum does not react with concentrated nitric acid, organic acids or foods.
Structure:
Aluminum has a face-centered cubic structure. Industrial pure aluminum has extremely high plasticity (ψ = 80%) and can easily withstand various forming processes.
However, its strength is very low (σb is about 69 MPa), so pure aluminum can only be used as a structural material after being strengthened by cold deformation or alloying.
Other properties:
Aluminum is a non-magnetic, non-sparking material and has good reflective properties. It can reflect visible light and ultraviolet light.
Impurities in aluminum include silicon and iron. The higher the impurity content, the lower the electrical conductivity, corrosion resistance and plasticity.
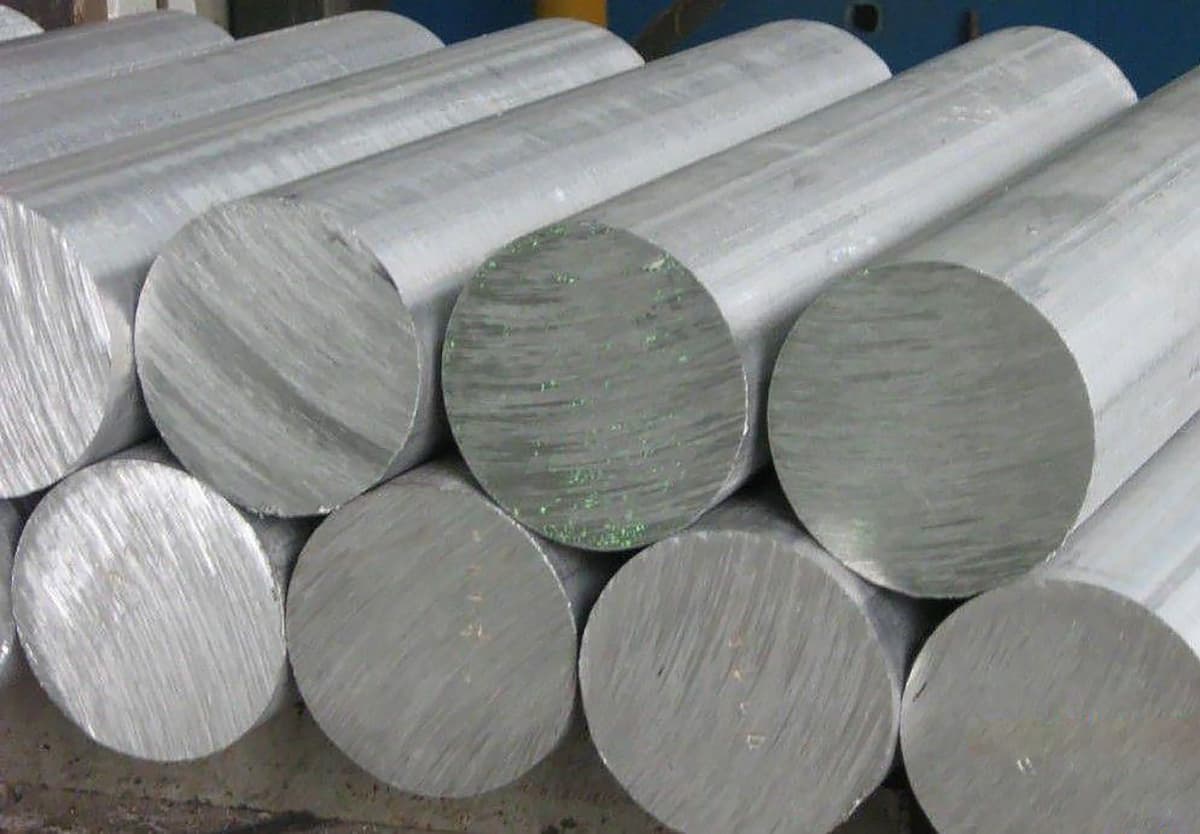
2. Aluminum alloys
By adding appropriate alloying elements to aluminum and then cold working or heat treating it, certain properties can be greatly improved.
The most commonly used alloying elements in aluminum are copper, magnesium, silicon, manganese and zinc.
Sometimes these elements are added alone or in combination, and sometimes traces of titanium, boron, chromium and other elements are also added.
According to the composition and characteristics of the production process of aluminum alloys, they can be divided into two categories: cast aluminum alloys and forged aluminum alloys.
Forged aluminum alloys: This type of aluminum alloy is generally processed through hot or cold pressing, such as rolling, extrusion, etc., to produce sheets, tubes, rebars and various profiles. This type of alloy requires relatively high plasticity, so the alloy content is relatively low.
Cast aluminum alloys are poured directly into sand molds to make complexly shaped parts. This type of alloy requires good castability, that is, good fluidity. When the alloy content is low, it is suitable for making wrought aluminum alloy, and when the alloy content is high, it is suitable for making cast aluminum alloy.
The elastic modulus of aluminum alloys is small, only about 1/3 of that of steel, that is, under the same load and cross section, the elastic deformation of aluminum alloys is three times that of steel. Although their resistance is not high, they have good seismic performance.
The hardness range of aluminum alloys (including annealed and age hardening states) is 20-120 HB. The harder aluminum alloy is softer than steel.
The maximum tensile strength of aluminum alloys ranges from 90 MPa (pure aluminum) to 600 MPa (superhard aluminum), which is significantly lower than that of steel.
The melting point of aluminum alloys is lower (generally around 600°C, while that of steel is around 1450°C).
Aluminum alloys have excellent plasticity at both room temperature and high temperature and can be used to produce structural parts with extremely complex cross-sectional shapes, thin walls and high dimensional accuracy using extrusion methods.
In addition to adequate mechanical properties, aluminum alloys also exhibit excellent corrosion resistance, thermal and electrical conductivity and reflectivity.
3. Glossary:
σb: Tensile strength (endurance limit) is the maximum stress equivalent to the maximum load that the sample can withstand divided by the original cross-sectional area before failure.
ψ: Area reduction is the relative shrinkage value of the cross-sectional area of the sample after fracture, equal to the absolute shrinkage of the cross-sectional area divided by the original area of the sample.
Plasticity: The ability of a metal to undergo plastic deformation (i.e. residual strain) before breaking.
4. International naming system for aluminum and aluminum alloys:
1. Pure aluminum (aluminum content not less than 99.00%): 1XXX
2. Alloy groups are divided according to the following main alloy elements:
- Cu (copper): 2XXX
- Mn (manganese): 3XXX
- Si (silicon): 4XXX
- Mg (magnesium): 5XXX
- Mg+Si (magnesium + silicon): 6XXX
- Zn (zinc): 7XXX
- Other elements: 8XXX
- Reserved: 9XXX
Group 1XXX represents pure aluminum (with an aluminum content of not less than 99.00%), and the last two digits represent the minimum percentage of aluminum, with decimal places following the two digits.
The second digit in the alloy designation indicates the control status of the limits of impurities or alloying elements. If the second digit is 0, it means there is no special control for the impurity limit. If it is 1-9, it means that there is a special control for one or more individual impurities or alloying element limits.
The last two digits in the designations 2XXX-8XXX have no special meaning and are only used to distinguish different alloys within the same group. The second digit represents temperament status. If the second digit is 0, it means the original league. If it is 1-9, it means the modified league.
6063-T5 Aluminum Composition Standard Content Table:
Note: Content is shown in percentage (%).
Component | Yes | Faith | Ass | Mn | mg | Zn | Cr | You |
Default content | 0.2~0.6 | ≤0.35 | ≤0.1 | ≤0.1 | 0.45~0.9 | ≤0.1 | ≤0.1 | ≤0.1 |
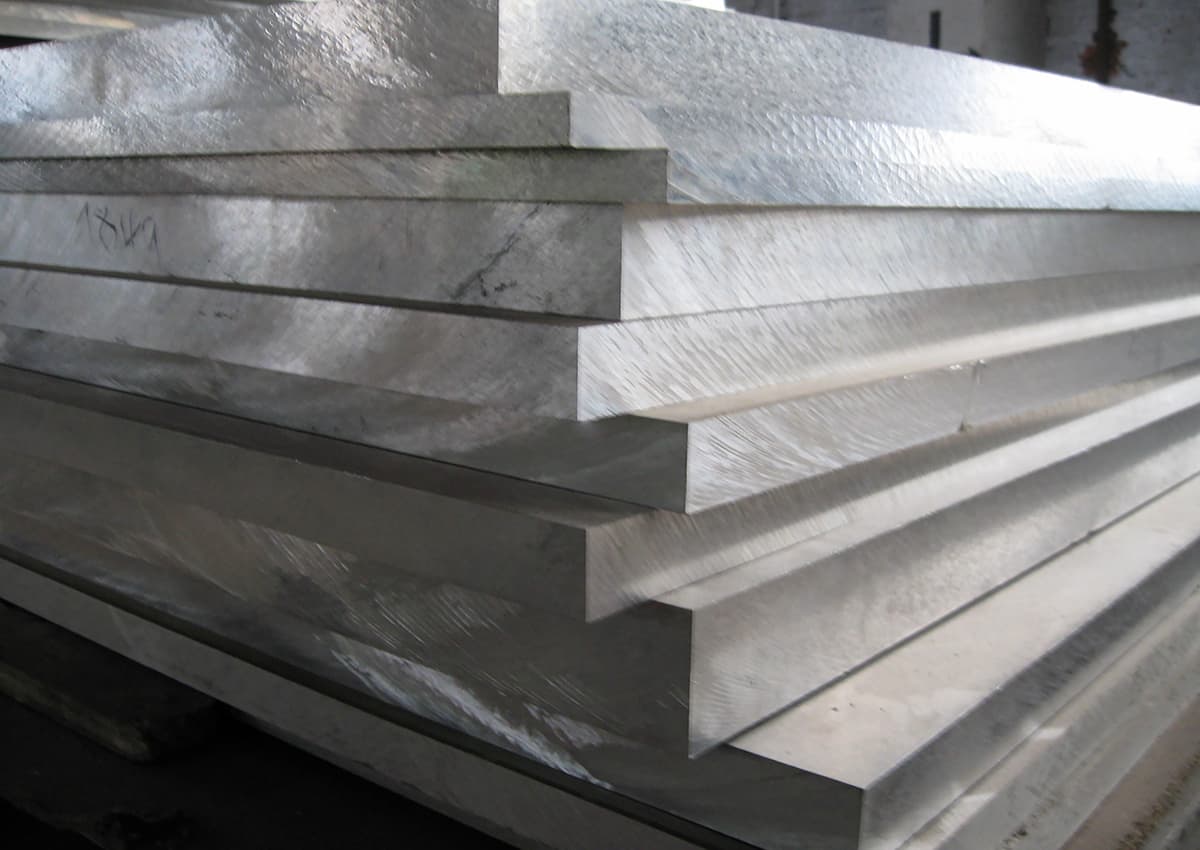
5. The meaning of codes for aluminum alloys in China:
- L: Aluminum
- LF: Anti-rust aluminum alloy (Al-Mg, Al-Mn)
- LY: Hard aluminum alloy (Al-Cu-Mg)
- LC: Superhard aluminum alloy (Al-Cu-Mg-Zn)
- LD: Forged aluminum alloy (Al-Mg-Si and Cu-Mg-Si)
- LT: Special aluminum alloy
6. Practical applications:
Currently, the following aluminum alloys are mainly used in the radiator industry:
1.Al6063/Al6061: Excellent plasticity makes it suitable for the extrusion process for manufacturing profile radiators. It can produce almost any shape of radiator, with mature technology, low price and high machinability.
2. Die-cast aluminum: Mainly used for large irregular-shaped radiators and integrated radiators for equipment cabinets.
3. LF/LY Series: Mainly used in radiators of electronic devices under special operating conditions. The operating environment has certain hardness and corrosion resistance requirements. LY12 is currently widely used.
7. Heat treatment process for aluminum alloys:
Heat treatment principles for aluminum alloys
Heat treatment for aluminum alloy castings involves selecting a specific heat treatment specification, controlling the heating rate to reach a certain temperature, maintaining it for a certain period of time, and then cooling it to a certain fee to change the league structure.
Its main objective is to improve the mechanical properties of the alloy, increase its corrosion resistance, improve its processing performance and achieve dimensional stability.
7.1.1 Features of heat treatment of aluminum alloys
As we all know, high carbon steel immediately obtains high hardness after quenching, but its plasticity is very low.
However, this is not the case with aluminum alloys. After quenching, the strength and hardness of aluminum alloys do not increase immediately and their plasticity increases rather than decreasing.
However, the strength and hardness of the quenched alloy will increase significantly, while the plasticity will decrease after being left for a period (such as 4-6 days).
This phenomenon in which the strength and hardness of quenched aluminum alloys increase significantly over time is called aging.
Aging can occur at room temperature, which is called natural aging, or it can occur within a certain temperature range above room temperature (such as 100-200℃), which is called artificial aging.
7.1.2 Age hardening principles for aluminum alloys
Age hardening of aluminum alloys is a complex process, which not only depends on the alloy composition and aging process, but also on any defects caused by shrinkage during production, especially the number and distribution of voids and dislocations. . It is generally believed that age hardening is the result of the aggregation of solute atoms to form a hardening zone.
When aluminum alloys are quenched and heated, voids form in the alloy. During quenching, these voids do not have enough time to escape due to rapid cooling, so they become “fixed” in the crystal.
Most of these vacancies in the supersaturated solid solution combine with solute atoms. Since the supersaturated solid solution is in an unstable state, it will inevitably shift toward equilibrium.
The existence of voids accelerates the rate of diffusion of solute atoms, thus accelerating the aggregation of solute atoms.
The size and number of hardening zones depend on the quenching temperature and quench cooling rate.
The higher the quenching temperature, the greater the concentration of voids, the more hardening zones and the smaller their size.
The faster the quenching cooling rate, the more fixed voids in the solid solution, which is beneficial to increase the number of hardening zones and reduce their size.
A fundamental characteristic of precipitation hardening alloy systems is the equilibrium solubility that changes with temperature, i.e., solubility increases as the temperature increases.
Most aluminum alloys that can be heat treated for strengthening meet this condition.
The solubility-temperature relationship required for precipitation hardening can be explained by the Al-4Cu alloy of the aluminum-copper system.
Figure 3-1 shows the binary phase diagram of the aluminum-rich part of the aluminum-copper system. The eutectic transformation L→α+θ (Al2Cu) occurs at 548℃.
The maximum solubility of copper in the α phase is 5.65% (548°C), and the solubility decreases drastically with decreasing temperature, to about 0.05% at room temperature.
During the aging heat treatment process, the alloy undergoes several changes in its structure, including the following:
7.1.2.1 Formation of solute atom aggregation zones – G•(Ⅰ) zones
In the recently quenched supersaturated solid solution, the distribution of copper atoms in the aluminum lattice is random and disordered.
In the early stage of aging, that is, when the aging temperature is low or the aging time is short, copper atoms aggregate on certain crystalline faces of the aluminum matrix to form solute atom aggregation zones called G zones. •(Ⅰ).
The G•(Ⅰ) zones maintain a coherent relationship with the α matrix, and these aggregates constitute coherent deformation regions that improve resistance to deformation, thus increasing the strength and hardness of the alloy.
7.1.2.2 Orderly arrangement of G• zones – formation of G•(Ⅱ) zones
As the aging temperature increases or the aging time extends, the copper atoms continue to aggregate and become ordered, forming G•P(Ⅱ) zones.
These zones still maintain a coherent relationship with the α matrix, but are larger than the G•P(Ⅰ) zones.
They can be considered intermediate transition phases and are often represented by θ”.
They have greater distortion than the surrounding G•P(Ⅰ) zones, which further impedes the movement of dislocations, making the strengthening effect of aging stronger.
The precipitation of the θ” phase is the phase in which the alloy reaches its maximum strengthening.
7.1.2.3 Formation of the transition phase θ′
As the aging process develops, copper atoms continue to aggregate in the G•P(Ⅱ) zones, forming the transition phase θ′ when the ratio of copper atoms to aluminum atoms becomes 1:2.
As the lattice constant of θ′ changes greatly, its coherent relationship with the matrix begins to disintegrate as it forms, i.e., it changes from complete coherence to partial coherence with the matrix.
Therefore, the coherent distortion around the θ′ phase weakens and the hindering effect on the movement of dislocations also decreases, resulting in a decrease in the hardness of the alloy.
It can be seen that the existence of coherent distortion is an important factor that causes the aging of strengthening in alloys.
7.1.2.4 Formation of stable θ phase
The transition phase completely precipitates from the aluminum-based solid solution, forming an independent stable Al2Cu phase with a clear interface with the matrix, called the θ phase.
At this time, the coherent relationship between the θ phase and the matrix is completely broken, and it has its own independent network, and its distortion disappears.
With increasing aging temperature or extending aging time, the θ phase particles aggregate and grow more, and the strength and hardness of the alloy further decrease. The alloy softens and becomes “aged”. The θ phase aggregates and becomes thicker.
The aging principles and general rules of aluminum-copper binary alloys also apply to other industrial aluminum alloys.
However, the types of alloys, the G•P zones formed, the transition phases, and the stable phases finally precipitated are all different, leading to different aging strengthening effects.
Even for the same alloy, the aging process may not entirely follow each stage sequentially, for example, some alloys stop in the G•P(Ⅰ) to G•P(Ⅱ) zones during natural aging.
During artificial aging, if the aging temperature is too high, the alloy may directly precipitate the supersaturated solid solution transition phase without passing through the G•P zone. The degree of aging directly affects the structure and properties of the alloy after aging.
7.1.3 Factors affecting aging
7.1.3.1 The influence of time between tempering and artificial aging
Studies have found that some aluminum alloys, such as Al-Mg-Si alloys, cannot reach their maximum strength after artificial aging if they remain at room temperature before artificial aging. Instead, its ductility increases.
For example, for cast aluminum alloy ZL101, if it is left at room temperature for a day after quenching and then artificially aged, the ultimate strength will be 10-20 Mpa lower than when aged immediately after quenching, but its ductility will increase in comparison to the latter.
7.1.3.2 The influence of the chemical composition of the alloy
Whether an alloy can be strengthened by aging depends first on whether the elements that make up the alloy can dissolve in solid solution and to what extent the solid's solubility changes with temperature.
For example, the solid solubility of silicon and manganese in aluminum is relatively small and does not vary much with temperature, while magnesium and zinc have a relatively large solid solubility in aluminum-based solid solution, but the structures of the compounds that they form with aluminum are not much different from matrix, resulting in minimal reinforcing effects.
Therefore, aluminum-silicon, aluminum-manganese, aluminum-magnesium and aluminum-zinc binary alloys are generally not subjected to aging strengthening treatment.
Some binary alloys, such as aluminum-copper alloys and ternary or multicomponent alloys, such as aluminum-magnesium-silicon alloys and aluminum-copper-magnesium-silicon alloys, have solubility and solid-state phase transitions during heat treatment and can be reinforced through heat treatment.
7.1.3.3 The influence of alloy solid solution processing technology
To obtain good aging strengthening effects, under conditions of avoiding overheating, burning and grain growth, higher quenching heating temperatures and longer retention times are favorable for obtaining a uniformly supersaturated solid solution with maximum supersaturation .
Furthermore, when extinguished, cooling should not result in precipitation of the second phase; otherwise, during subsequent aging treatments, the already precipitated phase will act as the nucleus, causing non-uniform local precipitation and reducing the aging strengthening effect.
8. Pure Aluminum
Pure aluminum is mainly used in environments that require high thermal conductivity, but overall it is not widely used. AL6061 aluminum alloy has several states: O, T4, T6, T451, T651, T6510, T6511.
Typical applications include industrial structural components that require a certain level of strength, high weldability and corrosion resistance. These components are used in the manufacture of trucks, towers, ships, trams, railway vehicles, furniture, bars, tubes and profiles with good anodizing properties.
AL6063 aluminum alloy has several states: O, T4, T83, T1, T5, T6. It is typically used as an extruded material for building profiles, irrigation pipes, vehicle frames, furniture, elevators, fences and decorative components of different colors for aircraft, ships, light industry and buildings.
In terms of extruded materials, 6063 is without a doubt the best choice. It has better polishing and anodizing properties than 6061 after extrusion.
6061 is a material with similar properties to 6063, but it belongs to a structural component material. Its characteristics include good weldability, corrosion resistance and structural strength, but there are still slight differences between 6061 and 6063. Its extrusion performance is lower than that of 6063.