Both steel and iron are iron-carbon alloys that contain a small amount of alloying elements and impurities. According to the different carbon contents, they can be divided into:
- Pig iron – containing 2.0% to 4.5% carbon
- Steel – containing 0.05% to 2.0% carbon
- Wrought iron – containing less than 0.05% carbon
Related Reading: Pig Iron vs Wrought Iron
Cast iron
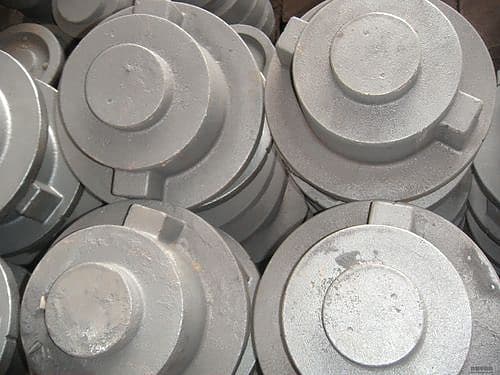
What is cast iron?
Cast iron is an iron-carbon alloy with a carbon content greater than 2%. The carbon in cast iron usually exists in the form of graphite and sometimes in the form of carbides.
In addition to carbon, cast iron also contains 1% to 3% silicon, as well as manganese, phosphorus, sulfur and other elements.
Alloy cast iron also contains elements such as nickel, chromium, molybdenum, aluminum, copper, boron and vanadium.
Carbon and silicon are the main elements that affect the microstructure and properties of cast iron.
Types of cast iron
Cast iron can be divided into:
1. Gray cast iron:
With high carbon content (2.7% to 4.0%), the carbon mainly exists in the form of flaky graphite and the fracture surface is gray. It has a low melting point (1145°C to 1250°C), small solidification shrinkage, compressive strength and hardness similar to carbon steel and good shock absorption.
It is used to manufacture structural components such as machine tool bases, cylinders, and housings.
2. White Cast Iron:
Low in carbon and silicon, carbon mainly exists in the form of carbides, and the fracture surface is silvery white.
During solidification, it presents great shrinkage and is subject to holes and cracks. It has high hardness and fragility and does not withstand impact loads. It is mainly used as blanks for malleable cast iron and to make wear-resistant parts.
3. Malleable Cast Iron:
Obtained by annealing white cast iron, graphite is distributed in a grouped form, commonly called ductile iron. Its microstructure and properties are uniform, wear-resistant and have good plasticity and toughness.
It is used to manufacture parts with complex shapes and capable of withstanding strong dynamic loads.
4. Ductile Cast Iron:
Obtained by the spheroidization of ferric water from gray cast iron. Precipitated graphite is spherical in shape, commonly called nodular cast iron.
It has higher strength, better toughness and plasticity than common gray cast iron. It is used in the manufacture of parts for internal combustion engines, automotive components, agricultural machinery, etc.
5. Compacted graphite iron:
Obtained by the compaction and spheroidization of ferric water in gray cast iron, the precipitated graphite is worm-shaped.
Its mechanical properties are similar to those of nodular cast iron, and its casting properties are between gray cast iron and nodular cast iron. It is used in the manufacture of automotive parts.
6. Cast Iron Alloy:
Ordinary cast iron with a suitable amount of alloying elements (such as silicon, manganese, phosphorus, nickel, chromium, molybdenum, copper, aluminum, boron, vanadium, tin, etc.) added.
Alloying elements change the structure of the cast iron matrix, having corresponding characteristics such as heat resistance, wear resistance, corrosion resistance, low temperature resistance or non-magnetism.
It is used in the manufacture of parts for mining, chemical machines, instruments and meters.
Cast steel
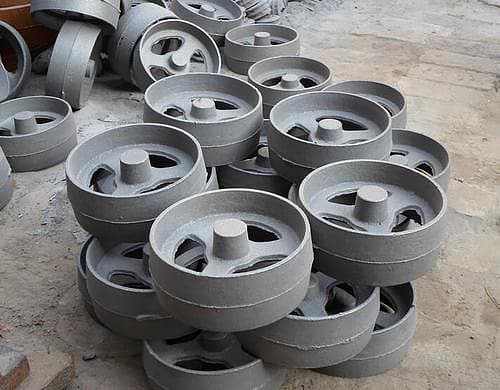
What is cast steel?
Steel used for casting. It is a cast alloy that can be divided into three types: carbon cast steel, low alloy cast steel and special cast steel.
Types of Cast Steel
1. Carbon Cast Steel:
Cast steel in which carbon is the main alloying element and contains a small amount of other elements. Low carbon cast steel contains less than 0.2% carbon, medium carbon cast steel contains 0.2% to 0.5% carbon, and high carbon cast steel contains more than 0.5% carbon .
As the carbon content increases, the strength and hardness of carbon cast steel increases. Carbon cast steel has high strength, plasticity and toughness, lower cost.
It is used in heavy machines to manufacture parts that support large loads, such as rolling mill structures, hydraulic press bases; and used in railway vehicles to manufacture parts subject to large forces and impacts, such as rocker pads, side structures, wheels and couplers.
2. Low alloy cast steel:
Casting of steel containing alloying elements such as manganese, chromium and copper. The total amount of alloying elements is generally less than 5%, which has higher impact toughness and can obtain better mechanical properties through heat treatment.
Low alloy cast steel performs better than carbon steel, reduces part weight and extends service life.
3. Special Cast Steel:
Cast steel alloy refined to meet special needs. There are many varieties, usually containing one or more high alloying elements to obtain certain special properties.
For example, high manganese steel containing 11% to 14% manganese can resist impact wear and is mainly used in wear-resistant parts of mining machinery and engineering machinery; various stainless steels based on chromium or chromium-nickel, used in parts that work under corrosive conditions or high temperatures above 650°C, such as valve bodies, pumps, containers for the chemical industry or turbine casings for power plants. large capacity.
ASTM D-5S standard austenitic nodular iron requires a carbon content of less than 2.0%.