In the welding process, the use of mixed gas instead of a single gas as shielding gas can effectively refine the droplet, reduce spatter, improve formation, control penetration, prevent defects and reduce porosity productivity, significantly improving the welding quality. .
Commonly used welding shielding gas mixtures include binary gas mixture, ternary gas mixture and quaternary gas mixture.
Binary gas mixtures include Ar He, Ar-N 2 Ar-H 2 Ar-O 2 Ar-CO 2 CO 2 -O 2 N 2 -H 2 etc;
Ternary gas mixtures include Ar-He-CO 2 Ar-He-N 2 Ar-HeO 2 Ar-O 2 -CO 2 etc;
The quaternion gas mixture is less used and is mainly composed of Ar, He, N 2 Ó 2 H 2 CO 2 etc.
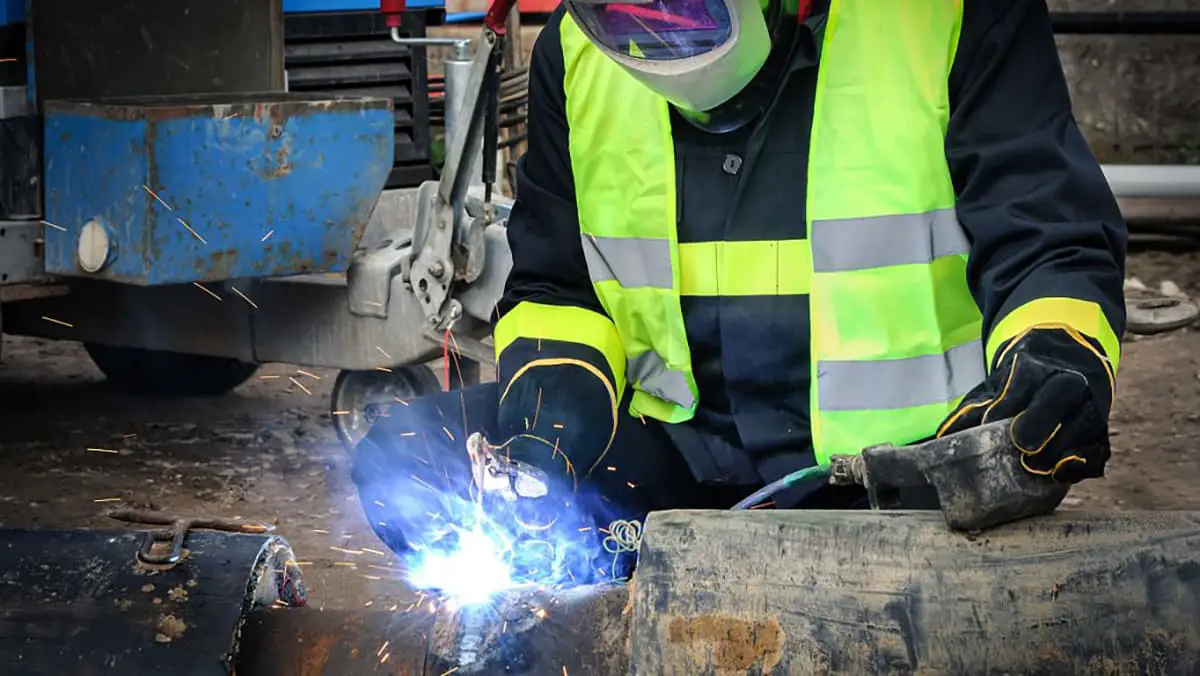
The proportion of each component in various mixed gases can vary in a wide range, which is mainly determined by the welding process, welding material, welding wire model and many other factors.
In general, the higher the welding quality requirements, the higher the purity requirements of the single gas used to prepare the mixture.
1. Binary gas mixture
(1) Argon-oxygen
Adding a small amount of oxygen to argon for MIG welding can improve arc stability, improve the refinement rate of molten droplets, reduce spray transfer current, improve wettability and weld bead formation.
Related Reading: MIG vs TIG Welding
For example, Ar+(1% – 2%) O 2 is commonly used for spray arc welding of carbon steel, low alloy steel and stainless steel.
Appropriately increase the oxidizability of the arc atmosphere to increase the temperature of molten metal in the molten pool and improve fluidity.
The molten metal can fully flow to the weld tip, reducing the undercutting tendency and making the weld bead flat.
For example, Ar+(5% – 10%) O 2 can be used for welding carbon steel to improve welding speed.
Sometimes a small amount of oxygen is added to weld non-ferrous metals.
For example, when welding very clean aluminum plates, adding 1% oxygen in the volume fraction can make the arc stable.
(2) Argon carbon dioxide
This type of gas mixture is mainly used for welding carbon and low alloy steel and has limited application for welding stainless steel.
Ar-CO 2 has less spatter than pure CO 2 and reduces the burning loss of alloying elements, which is helpful in improving the strength and impact resistance of the weld.
A small amount of CO 2 is added to the Air as a small amount of O 2 is added to produce an arc jet.
The biggest difference is that the critical current of the Ar-CO 2 mixture is greater than that of the Ar-O 2 mixture.
Ar-CO 2 is the most widely used binary welding gas mixture in China.
In order to meet market demand and standardize quality requirements, the chemical industry standard HG/T3728-2004 Argon Carbon Dioxide Welding Gas Mixture was formulated, which specifies the purity of the feed gas used to prepare Ar- CO 2 gas mixture, technical requirements, test methods, inspection rules, etc. for gas mixture products.
The Ar-CO 2 ratio of the mixed gas can be almost any ratio.
For example, it is common to add 5% CO2 to the gas mixture for all-position pulsed MAG welding of thick low-alloy steel plates.
Generally, compared with the addition of 2% O 2 , weld oxidation is lower, penetration is improved and porosity is lower;
Air+(10% – 20%) CO 2 is used for narrow gap welding of carbon steel and low alloy steel, all position welding of thin plates and high speed MAG welding;
Air+(21% – 25%) CO 2 is commonly used for short-circuit transfer welding of low carbon steel;
Air+50% CO 2 is used for deep penetration welding with high heat input;
Air+70% CO 2 is used to weld thick-walled pipes.
(3) Argon helium
The Ar He mixture is used for welding non-ferrous metals, such as aluminum, copper, nickel alloys and active metals, regardless of their proportion.
These gases use different combinations to improve the arc voltage and heat of TIG and MIG welding while maintaining the favorable characteristics of argon, which is particularly suitable for occasions where weld quality is highly demanded.
The helium content must be at least 20% to produce and maintain stable spray arc effect.
(4) Argon nitrogen
When welding duplex stainless steel, 2% – 3% N 2 can be added to the mixed gas to improve the pitting corrosion and stress corrosion cracking resistance of the joint.
(5) Argon helium
H 2 is a diatomic molecule with high thermal conductivity.
When Ar-H 2 mixture is used, the arc temperature can be increased, the penetration ability can be increased, the welding speed can be improved, and undercutting can be avoided.
In addition, hydrogen has a reducing effect, which can prevent the formation of CO pores.
Ar-H 2 mixed gas is mainly used for welding nickel-based alloys, nickel-copper alloys, stainless steel, etc.
The hydrogen content must be controlled below 6%.
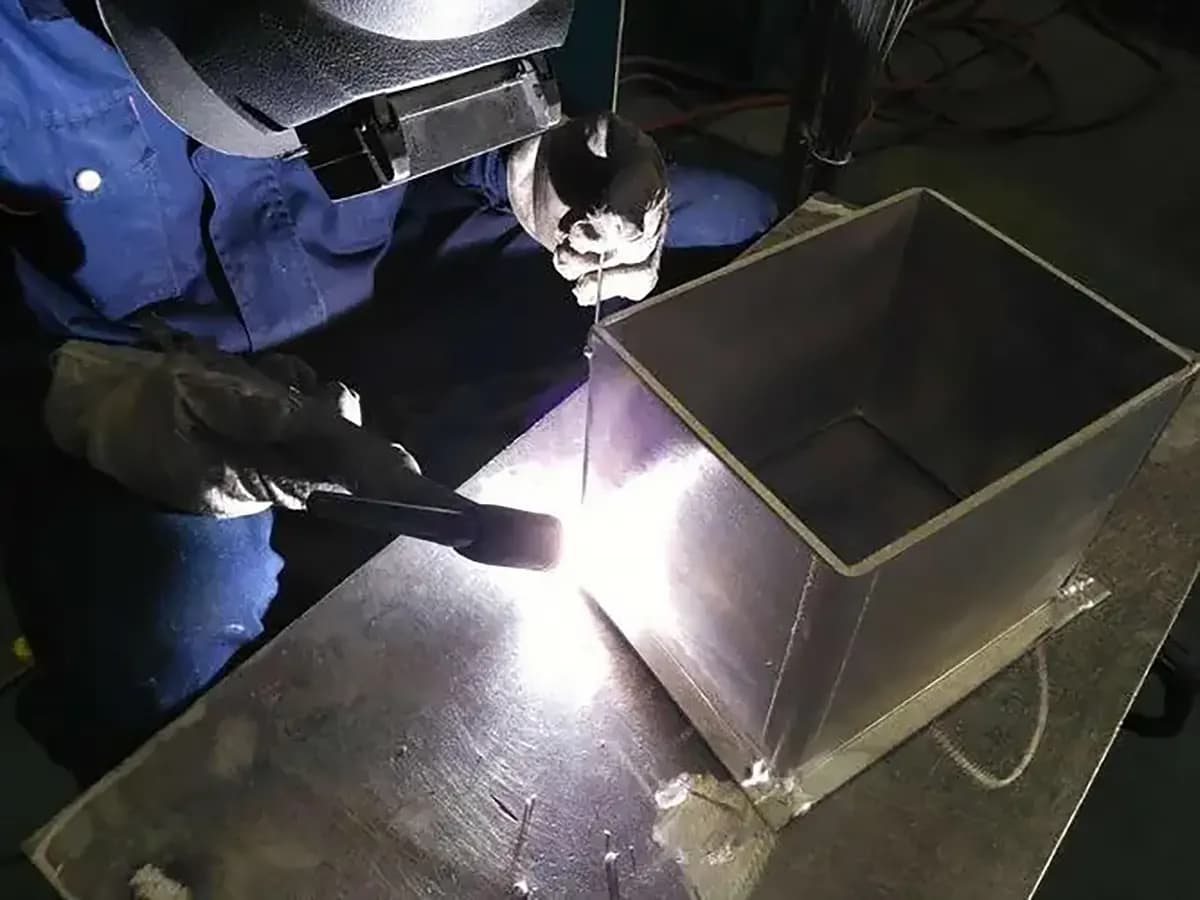
2. Ternary mixture of gases
(1) Argon, carbon dioxide, oxygen
The mixed gas containing these three components generally has CO 2 below 20% and O 2 below 5%.
The main advantage is that it can weld carbon steel, low alloy steel and stainless steel of different thicknesses. It doesn't matter which form of transition is appropriate.
(2) Argon, carbon dioxide, hydrogen
A small amount of H 2 (volume fraction 1% – 2%) is added to stainless steel during pulsed MIG welding, which improves weld wetting and makes the arc stable.
Therefore, CO 2 should also be lower (the volume fraction is 1% to 3%) to reduce the amount of carburizing and maintain good arch stability.
This gas is not recommended for low alloy steels, as it causes high hydrogen content in the weld metal, poor mechanical properties and cracking.
(3) Argon, helium, carbon dioxide
The addition of He and CO2 into Ar can increase the heat input of the weld and improve the stability of the arc, and the wetting and formation of the weld bead are better.
When welding carbon steel and low alloy steel, it is added to increase heat input and improve the fluidity of the molten pool.
It is also inert, which does not affect the loss due to burning of the weld metal oxidation alloy.
For example, Ar+(10% – 30%) He+(5% – 15%) CO 2 is used for pulsed jet arc welding of carbon steel and low alloy steel;
(60% – 70%) He+(20% – 35%) Ar+5% CO 2 is used for high-strength steel, especially short-circuit transfer welding in all positions;
90% He+7.5% Ar+2.5% CO 2 is widely used for all position short circuit arc welding of stainless steel.