Shot peening is a forming technique that uses high-speed shot flow to strike the surface of a metal sheet, causing plastic deformation of the impacted surface and the underlying metal material, gradually causing the sheet to bend toward the hammered surface, achieving the desired shape.
Shot Peening Diagram:

The main advantages of shot peening are:
(1) The process requires simple equipment, without the need for a molding die, which keeps the manufacturing cost of the parts low and provides great adaptability to the size of the parts.
(2) Since shot peening forms residual compressive stress on the upper and lower surfaces of the part along the thickness direction, it can improve the fatigue resistance of the part during the forming process.
(3) It can form parts with complex single or double curvatures.
In recent years, with the increasing demands on the overall aerodynamic performance of modern and advanced aircraft and the rapid development of computer technology, the research and development of shot peening technology has been greatly promoted.
This has led to the emergence of prestressed shot peening technology, digital shot peening technology and new shot peening reinforcement technology, greatly expanding the processing capacity and application range of shot peening technology.
I. Prestressed shot peening technology
Normally, the parts are completely free before shot peening. The deformation caused by shot peening is related to the shot peening resistance, the shot coverage and the thickness of the part.
The factors affecting shot peening strength mainly include shot peening-related parameters, such as shot peening material, heat treatment state and diameter, as well as shot peening equipment-related parameters, including shot peening speed and spray angle. .
Factors that affect shot peening coverage mainly include shot peening time and the material properties of the part being shot peening.
Therefore, for a certain shot peening and shot peening equipment, when using maximum coverage shot peening to form specific materials and thick parts, the deformation obtained is certain. This deformation reflects the limit of shot peening formation under the corresponding conditions.
The supercritical wing is an important feature of modern and advanced aircraft.
As one of the important parts constituting the shape of the wing, the integral wall panel has complex saddle and twist shapes on the outside and integral reinforcement protrusions, mouth moldings, holes and sinks on the inside.
The application of integral rib structure is also increasing.
For these parts, due to the small forming limit of free shot peening, it is difficult to meet the deformation required for the part shape. As a result, prestressed shot peening technology emerged.
Prestressed shot peening main diagram:

Before shot peening of the parts, a predetermined load is applied to the parts using specific jigs and accessories, causing the parts to undergo an initial elastic deformation. Next, the stressed surface is sandblasted. Under the same peening intensity and coating conditions, the formation limit of prestressed shot peening is 2 to 3 times greater than that of free shot peening.
At the same time, prestress shot peening can effectively control the additional bending deformation along the shot peening direction.
Currently, prestressed shot peening technology has been applied in the manufacture of integral wing panels for supercritical aircraft.
AR Company of Canada uses prestressed shot peening technology to avoid the negative impact on fatigue life caused by mechanical bending of such parts when manufacturing integral wing panels for Israel's 5B8BZU aircraft.
Of course, to apply prestress to parts, it is necessary to design and manufacture specific prestressing accessories. These accessories must be simple, light, easy to operate and must be compatible with the shot peening equipment used.
Therefore, the development trend of prestressed shot peening technology will be further research into simple and feasible prestress loading methods, as well as the use of finite element analysis to accurately determine the size of the applied prestress, ensuring that the parts are completely within the elastic deformation range under prestress.
II. Digital shot peening forming technology
Digital shot peening forming technology uses digital technology to digitally analyze the geometric information of parts, select and optimize the parameters of the shot peening forming process, simulate and control the shot peening forming process, digitally inspect the shape of parts formed and digitally manage shot peening formation process files and part programs.
This advanced forming technology aims to describe the parts and their shot peening forming process in the form of digital quantities and unify the data generated at each stage.
In terms of digital shot peening forming technology, a successful application example is the automated shot peening forming technology proposed by P/ Company of Germany.
In addition, as an essential part of digital technology, the numerical simulation technology of the shot peening forming process has also achieved significant development.
The implementation of automated shot peening forming technology is divided into three stages: conceptual design and analysis phase, pre-production development phase and production phase.
During the conceptual design and analysis phase, the 2+O numerical model of the parts is analyzed and evaluated mainly for shot peening formability, and the initial shot peening forming process plan and forming process parameters are formulated, taking into consideration the user's equipment and personal situation.
In the pre-production stage, the process is optimized through shot peening tests on specimens, generating relevant process control files and programs, and necessary updates and adjustments are made to the user's equipment. Furthermore, at this stage, changes and improvements to the part design can be made simultaneously.
In the production phase, the automation of shot peening forming can be carried out by invoking pre-established control programs for the parts, at the same time as carrying out technical training for the relevant personnel.
After establishing an automated shot peening forming technology system at the user's premises during this phase, the development of new products in the future only requires offline programming, and then the relevant data and programs can be transferred to the user's equipment for testing and production.
Automated shot peening technology mainly includes hardware and software aspects. The hardware aspect requires a numerically controlled multicoordinate shot peening device with programmable control.
The software aspect requires shot peening forming process database technology, simulation analysis technology, digital measurement technology, virtual visualization technology and extensive practical experience to quickly formulate a reasonable and correct process route.
The advantages of automated shot peening technology are very obvious. Users do not need to do any programming or testing; The operator simply presses the start button and the equipment will automatically complete the other tasks predefined in the parts program.
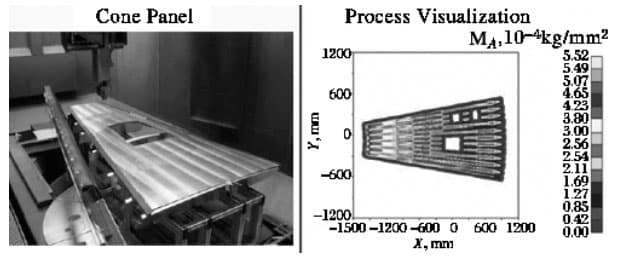
In recent years, some new shot peening methods have emerged that differ from traditional shot peening techniques. Among them, the development and application of double-sided shot peening, laser shot peening, ultrasonic shot peening and high-pressure water shot peening have received widespread attention and concern.
III. Double Sided Shot Peening Technique
The double-sided shot peening technique was first proposed in 2002 by R.KOPP of the Aachen University of Technology in Germany. The basic principle involves using projectiles of different sizes to simultaneously blast the top and bottom surfaces of a part at different speeds, thereby improving shot peening capacity and efficiency.
As shown in the figure below:

The method makes it possible to achieve a bending radius as small as 1000 mm. Double-sided shot peening forming technology has high requirements for shot peening equipment. It not only needs to have the function of simultaneously spraying shots of different sizes, but also requires strong matching and control of the speed and flow of two sizes of shots to achieve the expected results.
4. Laser peening forming technology
Laser shot peening technology was first proposed around 1965. The basic principle is to use high-frequency, high-power, short-pulse laser beams to impact the surface of the part coated with a semitransparent ablation material placed in laminar water. .
The laser pulse passes through the laminar water and is absorbed by the ablation layer, creating a plasma cloud in the laminar water. Within 10ns ~ 100ns, the plasma rapidly expands on the surface of the workpiece, generating a pressure of 1Gp ~ 10Gp and forming a planar shock wave, thereby causing plastic deformation on the surface of the workpiece.
Compared with traditional shot peening, laser shot peening generates larger residual stress values, and the residual stress distribution area is 3 to 5 times deeper than that of traditional shot peening.
Therefore, laser shot peening is used for surface strengthening of metal parts. Laser shock hardening can greatly improve the fatigue and stress corrosion resistance of parts. When used to form thin-walled parts, it can achieve greater deformation capacity than traditional shot peening.
V. Ultrasonic shot peening forming technology
Ultrasonic shot peening mainly uses ultrasonic waves to induce mechanical vibrations in the shots, thereby driving the shots to carry out shot peening treatment on the workpiece.
The basic principle is as follows:

Ultrasonic shot peening uses not only steel shot as the peening medium, but also spray needles with different radii of curvature at their ends.
The advantage of ultrasonic shot peening is that it can reach a deeper residual stress layer than traditional shot peening, and the residual stress value is also higher, while the surface roughness is better than that of traditional shot peening.
SONATS, a French company, began researching this technology in 1996 and has now developed a set of ultrasonic shot peening technology and corresponding ultrasonic shot peening equipment, which is widely used in the aerospace, shipbuilding and automotive industries.
SAW. Shot Peening Technology Development
Shot peening formation also has obvious limitations, such as the tendency of spherical deformation, limited deformation, strict constraint conditions and numerous influencing factors.
However, the excellent characteristics of shot peening forming make people constantly seek new ways and methods to break through its limitations, continuously explore the inherent potential of shot peening forming technology, and continuously meet the special forming and performance requirements of components that are becoming increasingly demanding. , represented by integral panels of complex metallic wings of large and medium-sized aircraft.