
Sheet metal processing technology has continually advanced, particularly in applications such as precision bending of stainless steel, bending of stainless steel decorative parts, bending of aluminum alloys, bending of aircraft parts, and bending of copper plates, which have increasingly stringent requirements for the surface quality of the formed. work piece.
The conventional bending process, however, tends to cause damage to the surface of the part, leaving noticeable marks or scratches on the surface that comes into contact with the mold. This negatively impacts the appearance of the final product and reduces its perceived value by the user.
Reasons for Crease Marks
In this article, we will use the example of bending a V-shaped part to discuss the process.
Sheet metal bending is the process of forming a sheet of metal under pressure from a punch or press brake machine. The sheet undergoes elastic deformation followed by plastic deformation.
At the beginning of the plastic bending, the sheet is free to bend. With the pressure of the punch or die, the sheet and the inner surface of the V-groove of the die gradually approach each other, and the bending radius and bending force arm decrease. The process continues until the end of the stroke, at which point the die and sheet are in full contact at three points, and the V-shaped bend is complete.
During bending, the sheet metal is elastically deformed by the pressure of the bending die, causing the contact point between the sheet metal and the die to slide as bending progresses. Sheet metal undergoes two stages of deformation: elastic and plastic.
After the bending process is complete, three indentation lines will remain, due to the holding pressure applied during the bending process. These indentation lines are commonly known as “shoulder marks” and are generated by the die V-groove plate and shoulder, as shown in Figures 1 and 2.
The formation of marks on the shoulders can be attributed to several factors, which can be broadly classified below.
Bending method
The shoulder marks are related to the contact between the plate and the V-groove shoulder of the die. During the bending process, the gap between the punch and the die affects the compressive stress in the sheet, resulting in differences in the probability and severity of indentation, as shown in Figure 3.
Under the same V-groove conditions, the greater the bending angle of the workpiece, the greater the deformation of the sheet metal and the greater the friction distance at the shoulder of the V-groove. In addition, a larger bending angle also results in a longer retention time for the punch to apply bending force to the sheet, exacerbating marks caused by the combination of these factors.
The V-groove structure of the die
When bending sheet metal of varying thicknesses, the V-groove widths chosen also differ.
Under the same conditions for the punch, a larger V-groove size for the die leads to a larger indentation width. On the other hand, less friction between the metal sheet and the V-groove shoulder of the die reduces the indentation depth.
Thinner plates result in narrower V-grooves, causing more visible marks.
Another factor to consider in terms of friction is the coefficient of friction. Different radii of the die's V-groove shoulder result in varying levels of friction on the sheet during the bending process.
In terms of the pressure exerted on the sheet by the die V-groove, a larger radius of the die V-groove reduces the pressure between the sheet and the shoulder of the die V-groove, leading to fewer bend marks.
Lubrication degree of die V-groove
Previously, we noted that the V-groove surface of the die can cause friction when it comes into contact with the sheet material.
As the mold wears, the contact between the V-groove and the sheet becomes rougher and the coefficient of friction increases. Sliding of the sheet on the surface of the V-groove results in contact between numerous rough protrusions and the surface, causing increased pressure on the sheet surface and more visible indentations.
Furthermore, if the V-groove is not cleaned before bending the workpiece, residual debris in the V-groove may cause obvious indentations due to the pressure it exerts on the sheet metal. This is a common problem when bending parts such as galvanized sheets and carbon steel sheets.
Application of Mark Free Bending technology
Since the main cause of bending marks is the friction between the plate and the V-groove shoulder of the die, we can use processing technology to reduce this friction.
The formula for the friction force, F=μ×Fn, shows that the factors that affect the friction force are the coefficient of friction (μ) and the pressure (Fn), both of which are proportional to the friction force.
Therefore, the following four solutions can be used to achieve a mark-free push-up:
1. The non-metallic material used in the V-groove shoulder of the die
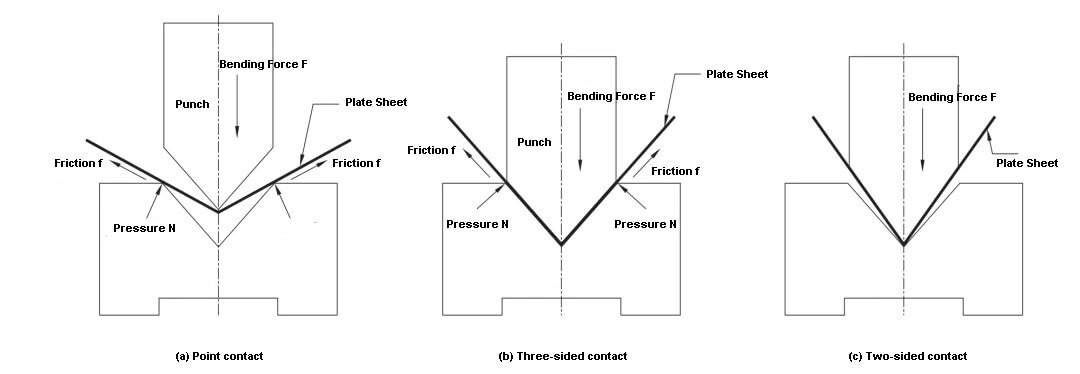
Figure 3 Type of flexion
The traditional approach of simply increasing the radius of the V-groove shoulder is not a reliable solution for reducing bending recoils.
To reduce the pressure on the friction pair, it is possible to use a softer, non-metallic material for the shoulder of the V-groove, such as nylon or urethane (PU elastomer), as long as the required extrusion effect is maintained. However, these materials have the disadvantage of being prone to wear and tear and requiring frequent replacement.
Currently, there are several V-groove structures that use these materials.
2. Change V-groove shoulder from die to ball and roller
Furthermore, in order to reduce the friction coefficient between the plate and the V-groove, the sliding friction couple between the plate and the shoulder of the V-groove can be transformed into a rolling friction pair, thus significantly reducing the frictional force acting on the sheet.
This can effectively prevent bending recoil.
Currently, this method is widely used in the mold industry, and the bending mold without ball marks (Figure 5) is a common application example.
To avoid rigid friction between the bent mold roll without ball marks and the V-groove, and to facilitate the rotation and lubrication of the roll, balls are added to reduce the pressure and friction coefficient.
As a result, parts processed by spherical markless bending mold generally have no visible marks, but the markless bending effect is not ideal for soft materials such as aluminum and copper.
From a financial perspective, the structure of the bending mold without ball marks is more complicated than previous mold designs, resulting in higher processing costs and maintenance difficulties. These factors must be taken into consideration by business managers when choosing tools.
3. Change the die V-groove shoulder to a flip structure
Currently, there is another type of mold in the industry that uses the principle of pivot rotation to achieve the bending of the part by rotating the die shoulder.
This mold design departs from the traditional V-groove structure by transforming the inclined surfaces on both sides of the V-groove into a reversible structure.
During pressing of the sheet by the punch, the rotating mechanism on both sides of the punch is activated by the pressure of the punch, causing the sheet to bend and form, as illustrated in Figure 6.
Under this operating condition, there is minimal sliding friction between the sheet and the die, and the sheet moves closer to the punch apex near the turning plane to avoid marking the parts.
The structure of this type of mold is more complex than previous designs, with a tension spring structure and hinged plate, resulting in higher maintenance and processing costs.
4. Insulation between die V-groove and sheet
The methods discussed above aim to obtain a mark-free bend by modifying the bending dies.
From a commercial standpoint, it may not be viable to develop and purchase a new set of dies to bend individual parts without marks.
From the perspective of frictional contact, as long as the mold is separated from the sheet, friction does not occur.
Therefore, without changing the bending die, mark-free bending can be achieved by using a soft film to avoid contact between the V-groove and the sheet.
This soft film, also known as non-marking flexible film, is commonly made from materials such as rubber, PVC (polyvinyl chloride), PE (polyethylene) and PU (polyurethane).
Rubber and PVC have lower raw material costs, but lack pressure resistance, poor protective performance and short service life.
PE and PU, on the other hand, are excellent engineering materials. The mark-free bending and pressing film made with them as substrate has good tear resistance and a long service life, providing good protection.
The bending protection film works as a buffer between the workpiece and the mold shoulder, relieving the pressure between the mold and the sheet and thus preventing the workpiece from being scratched during bending.
When in use, the foldable film can be placed on the die, offering low cost and easy use.
At present, the thickness of commercially available unmarked folding film is typically 0.5mm, and the size can be customized according to needs.
Under the pressure condition of 2t, the non-marking bending film can generally achieve a service life of about 200 bending cycles, and has strong abrasion resistance, excellent tear resistance, superior bending performance, high tensile strength and elongation , resistance to lubricants, and resistance to aliphatic hydrocarbon solvents.
This article has described several methods for achieving mark-free flexure, and Table 1 provides a comparison of these methods.
Table 1 Mark-free bending process comparison
Contrast item | V type nylon groove | Urethane V-groove | V roller groove | Flip type groove | Mark the Free Fold Sheet |
---|---|---|---|---|---|
Bending angle | Multiple angles | Bow | Multiple angles | Commonly used at right angles | Multiple angles |
Applicable sheet | Various dishes | Various dishes | Aluminum-free copper and other soft plates | Various dishes | Various dishes |
Length limitation | ≥50mm | ≥200mm | 100mm | / | / |
Service life | 15~200,000 times | 10~150,000 times | / | / | 200 times |
Replacement maintenance | Replace nylon | Replacing the PU block | Replace the roller | Full replacement or replacement of accessories such as extension springs | Full replacement |
Cost | Low | Low | Dear | Dear | Low |
Advantage | Low cost and suitable for mark-free bending of a wide range of sheets, using the same bottom die approach as a standard press brake. | Low cost, suitable for mark-free bending of various boards | Long life | Suitable for mark-free bending of multiple boards | Low cost, using the same method as the standard matrix |
Limitation | Shorter service life than standard molds, segment size is limited above 50mm | Currently, it is only applicable to the unmarked bending of arc-shaped products. | This method is expensive and its non-marking bending effect on soft materials such as aluminum and copper is not ideal. The friction and deformation of the balls are difficult to control, leading to possible marks on other rigid plates, and have more restrictive length and groove requirements. | Expensive and small scope, limited length and V-shaped opening | It has a shorter shelf life compared to other solutions, frequent replacement reduces production efficiency, and the cost increases significantly when used in large quantities. |
Final thoughts
Competition in the sheet metal processing industry is intense, and to remain competitive, companies need to constantly improve their processing technology. They must not only consider the functionality of the product, but also its processability, appearance and economics of processing. By using more efficient and cost-effective processing methods, companies can make their products easier to process, more economical and more attractive.