There are more than 100 types of materials that can be used for mold processing, including metals, plastics, inorganic non-metals and wax.
Related Reading: Metal Type
However, each material has its specific purpose and requirements based on actual needs.
Today, we will discuss the 24 most frequently used metal materials in mold processing.
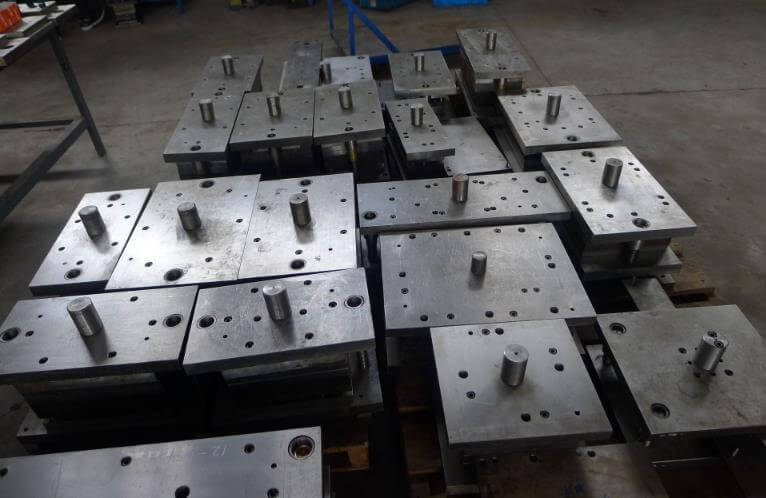
1. # 45 – high-quality carbon structural steel, which is the most commonly used medium-carbon quenched and tempered steel
Main Features:
The most widely used medium-carbon quenched and tempered steel has favorable overall mechanical properties, but is susceptible to poor hardenability and cracking during water quenching. Small components must be quenched and tempered, while larger components must be normalized.
Forms:
This steel is mainly used to produce high-strength moving parts such as turbine impellers, compressor pistons, shafts, gears, racks and worm screws. It is important to preheat before welding and annealing to relieve stress after welding.
2. Q235A (A3 steel) – the most commonly used carbon structural steel
Main Features:
This material has high plasticity, toughness, weldability, cold stamping ability, moderate strength and good cold bending performance.
Forms:
It is widely used in welded components and structures with general requirements, such as tie rods, connecting rods, pins, shafts, screws, nuts, ferrules, brackets, bases, building structures and bridges with minimum force.
3. 40Cr – one of the most used steels, is an alloy structural steel
Main Features:
This material has good overall mechanical properties, impact toughness at low temperatures and low notch sensitivity after quenching and tempering. It has good hardenability and high fatigue resistance can be achieved with oil cooling, although parts with complex shapes are prone to cracking during water cooling.
The material has medium cold bending plasticity and good machinability after tempering or quenching and tempering, but weldability is poor and cracking is likely to occur. Preheating to 100-150°C is required before welding. It is typically used in the quenched and tempered state and can also undergo carbonitriding and high-frequency surface quenching.
Forms:
- After quenching and tempering, it is used to manufacture medium speed and medium load components such as machine tool gears, shafts, worms, spline shafts and thimble sleeves.
- After quenching and tempering and high-frequency surface quenching, it is used to produce parts with high surface hardness and wear resistance, such as gears, shafts, main shafts, crankshafts, spindles, sleeves, pins, connecting rods, screw nuts and inlet valves.
- After quenching and tempering at medium temperature, it is used in the manufacture of parts with heavy loads and impact at medium speed, such as oil pump rotors, sliding blocks, gears, main shafts and collars.
- After quenching and tempering at low temperature, it is used to produce heavy, low-impact and wear-resistant parts such as worms, spindles, shafts and collars.
- After carbonitriding treatment, it is used to produce large, low-temperature impact-resistant large transmission parts such as shafts and gears.
4. HT150 – Gray Cast Iron
Forms:
This material is commonly used in gearboxes, machine bases, boxes, hydraulic cylinders, pump bodies, valve bodies, flywheels, cylinder heads, pulleys and bearing covers, among others.
5.35 – common materials of various parts and standard fasteners
Main Features:
This material has adequate strength, good plasticity, high cold plasticity and acceptable weldability. It can undergo local upsetting and cold drawing, has low hardenability and is used after normalization or quenching and tempering.
Forms:
It is suitable for the production of parts with small cross-sections that can withstand high loads, such as crankshafts, levers, connecting rods, shackles, various standard parts and fasteners.
6. 65Mn – common spring steel
Forms:
This material can be used to manufacture various flat and round springs in small sizes, including buffer springs and spring springs. It can also be used to make spring rings, valve springs, clutch springs, brake springs, cold coil springs and pressure springs.
7. 0Cr18Ni9 — the most commonly used stainless steel (American steel 304, Japanese steel SUS304)
Characteristics:
This material is a type of heat-resistant stainless steel, widely used in various applications, such as food equipment and chemical equipment in general.
Forms:
It is commonly used in the manufacture of food equipment and chemical equipment in general due to its heat resistant properties.
8. Cr12 – common cold work die steel (American steel D3, Japanese steel SKD 1)
Characteristics:
Cr12 steel is a commonly used cold working die steel which belongs to ledeburite steel with high carbon and chromium content. It is known for its good hardenability and wear resistance.
Forms:
However, due to its high carbon content (2.3%), it has low impact toughness, making it susceptible to embrittlement and the formation of irregular eutectic carbides. Despite this, Cr12 steel is widely used in manufacturing high wear resistance cold stamping dies, punches, stamping dies, cold upsetting dies, punches, concave cold extrusion dies, punching sleeves, gauges, drawing dies, stamping dies, wire friction plates, deep drawing dies and cold stamping dies for powder metallurgy.
9. DC53 – common cold work die steel imported from Japan
Characteristics:
This is a high strength and toughness cold working die steel produced by special (deformation) steel manufacturer Datong in Japan. After high temperature tempering, it has high hardness, high toughness and good wire cutting performance.
Forms:
It is commonly used in the manufacture of precision cold stamping dies, drawing dies, thread rolling dies, cold stamping dies and punches.
10. Dccr12mov – wear-resistant chrome steel
Domestic steel has lower carbon content compared to Cr12 steel and its carbide uniformity is improved with the addition of Mo and V. Mo helps reduce carbide segregation and increases hardenability, while V refines the grain structure and increases tenacity.
This steel has high hardenability and can be fully hardened when the section size is less than 400 mm, maintaining good hardness and wear resistance at 300 to 400 degrees Celsius. It has greater toughness compared to Cr12, with minimal volume change during quenching.
Furthermore, it has high wear resistance and good overall mechanical properties. This makes it suitable for manufacturing various molds with large sections, complex shapes and large impacts, such as drawing dies, punching dies, slitting dies, slitting dies, sharpening dies, drawing dies, cold extrusion dies , cold cutting shears, circular saws, standard tools and measuring tools.
11. SKD11 – ductile chromium steel
Hitachi type is a type of production originating from Japan. The steel casting structure is improved and the grain is refined, which results in an improvement in toughness and wear resistance compared with Cr12MoV. This leads to extended die life.
12. D2 – high carbon, high chromium cold work steel
Made in the United States, D2 steel is a commonly used air-hardening tool steel. It has high hardenability, hardness and wear resistance, as well as good high temperature oxidation resistance and corrosion resistance after quenching and polishing.
The heat treatment deformation of D2 steel is minimal, making it suitable for manufacturing various cold working dies, cutting tools and measuring tools that require high precision and long service life, such as drawing dies, extrusion dies cold and cold shear knives.
13. SKD11 (SLD) – high chromium steel with non-deformation toughness
Hitachi type produced in Japan.
This type of steel is made with a greater amount of Mo and V, which improves the steel's casting structure and refines the grain. This results in better carbide morphology and greater strength and toughness compared to other steels such as SKD1 and D2. Wear resistance and hardening resistance are also increased, leading to longer die life.
It is commonly used to manufacture high-demand molds such as wire drawing molds and impact grinding wheel blade molds.
14. DC53 – high tenacity, high chromium steel
DC53 is a high performance cold working die steel produced by the Datong strain in Japan.
It has a higher hardness after heat treatment compared to SKD11, with a hardness of 62-63 HRC achievable after high temperature tempering.
DC53 has better strength and wear resistance than SKD11, and its toughness is also twice that of SKD11.
The toughness of DC53 results in less cracking and less deformation during cold work die manufacturing, which greatly improves its service life.
The DC53 also has low residual voltage, which is reduced upon return at high temperature.
Furthermore, its machinability and abrasiveness are superior to those of SKD11 due to the reduction of cracks and deformations after cutting the wire.
It is commonly used for precision stamping dies, cold forging and deep drawing dies.
15. SKH-9 – general high speed steel with high wear resistance and toughness
The steel is produced by Hitachi in Japan and is commonly used to manufacture cold forging dies, cutting blades, drills, reamers and punches. It has high strength, toughness and wear resistance, making it ideal for these types of tools and applications.
16. Asp-23 – high speed steel for powder metallurgy
Swedish-made powder metallurgy high-speed steel known for its uniform carbide distribution, high wear resistance, excellent toughness, ease of processing and stability during heat treatment. It is commonly used for a wide range of cutting tools that require long service life, such as punches, deep drawing dies, drilling dies, milling cutters and shear blades.
17. P20 – general requirements plastic molds
It is a pre-hardened steel that can be processed by electrical discharge machining (EDM). The steel has a hardness of HB270 to 300 before being quenched and a hardness of HRC52 after quenching. This steel is often used in the manufacture of cutting tools and other products that require high hardness and toughness.
18. 718 – large and small plastic molds with high requirements
Swedish-made material that can be processed by electrical engraving. It is pre-hardened to a hardness of HB290 to 330 and tempered to a hardness of 52 on the Rockwell C scale.
19. Nak80 – high mirror, high precision plastic mold
Datong in Japan produces a pre-hardened steel with hardness of HB370~400 and quenched hardness of HRC52.
20. S136 – corrosion-resistant, mirror-polished plastic mold
Made in Sweden. Pre-hardening HB < 215 and quenching hardness HRC52.
21. H13 – common die casting die
Used for die casting of aluminum, zinc, magnesium and alloys, hot stamping die, aluminum extrusion die, etc.
22. SKD61 – Advanced Casting Die
It is produced by Hitachi in Japan and uses electroslag remelting technology. This technology results in a significant increase in service life compared to H13. It is commonly used for hot stamping dies and aluminum extrusion dies.
23. 8407 – advanced die casting die
Made in Sweden. Used for hot stamping dies and aluminum extrusion dies.
24. FDAC – sulfur is added to increase its chipping
The pre-hardening hardness of this material is HRC38 to 42, and it can be carved directly without undergoing quenching and tempering. This material is often used for small batch molds, simple molds and various resin products, as well as slip parts and mold parts that require a short lead time. Examples include zipper molds, eyeglass frame molds, and more.