In the mid-19th century, due to the very backward aluminum smelting technology in France, princes' ministers could only use silver cutlery at banquets, and only Napoleon II used an aluminum bowl.
With the application of aluminum electrolytic technology, aluminum has become increasingly integrated into public life. The development of aluminum alloy surface treatment technology has made aluminum not only have high practical value but also aesthetic value.
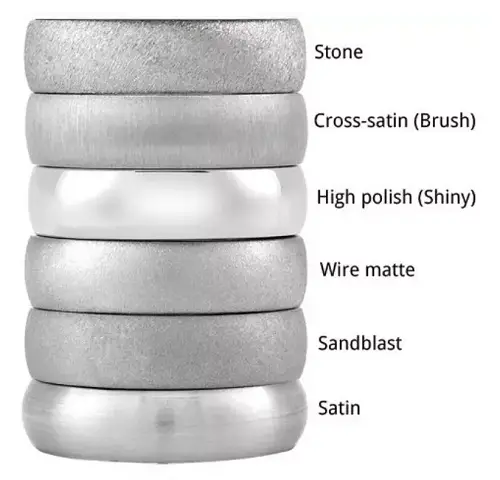
Metal materials are increasingly being used in existing products because they can better reflect product quality and highlight brand value. Among many metal materials, aluminum is the first choice of many manufacturers because of its easy processing, good visual effect and rich surface treatment methods.
I. What is surface treatment?
Surface Treatment: This process involves applying a protective layer to the surface of a product, using mechanical and chemical methods. This protective layer maintains stability in the natural environment, increasing corrosion resistance, the aesthetics of the product and therefore its value.
The choice of the type of surface treatment must mainly consider factors such as operational conditions, useful life, aesthetic appreciation and, of course, economic value.
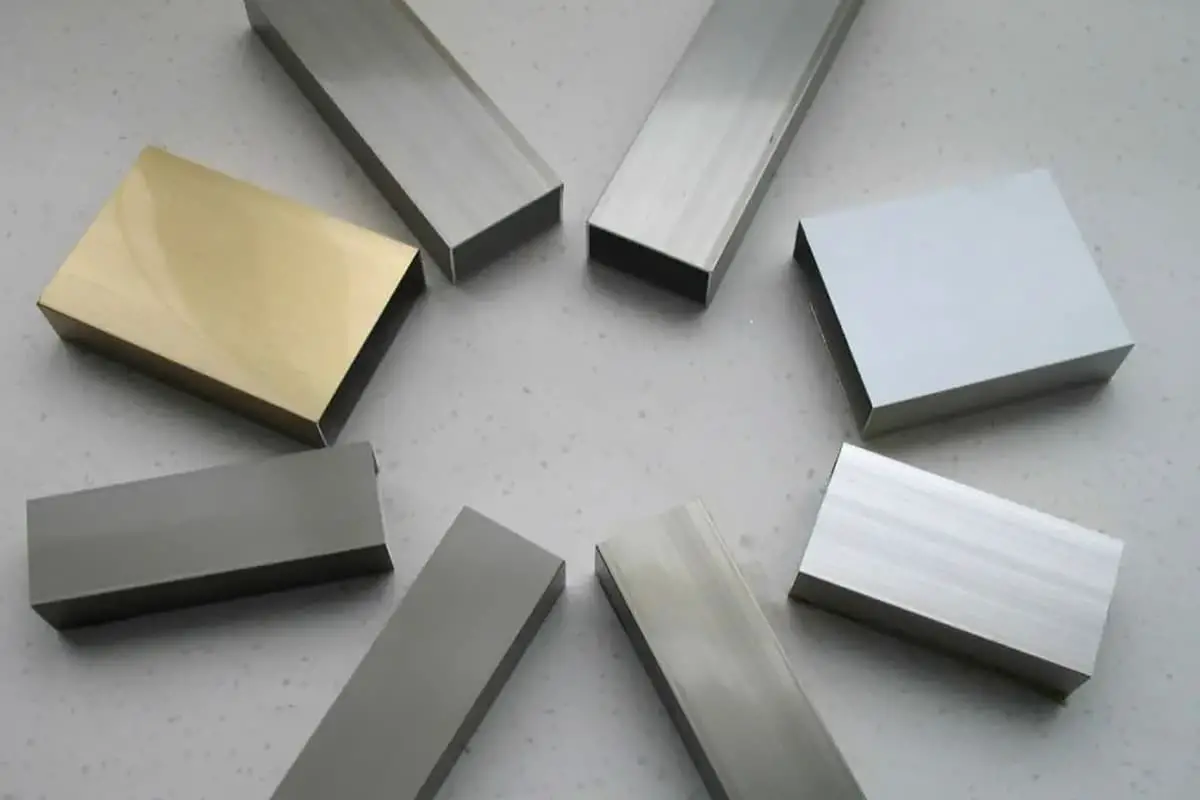
The surface treatment process consists of pre-treatment, film formation, post-film treatment, packaging, storage and shipping. Pretreatment includes mechanical and chemical processes.
Mechanical processes include sand blasting, blasting, grinding, polishing and waxing. They aim to eliminate irregular surfaces and correct any adverse aspects.
The chemical treatment helps to remove oil and rust from the surface of the product, at the same time as it forms a layer that allows a better bond with film-forming substances, transforming it into a reactive metallic body. This ensures that the coating has a stable state, improving the bond strength of the protective layer and consequently protecting the product.
Common surface treatment methods for aluminum materials include chromium (Ge) treatment, painting, electroplating, anodizing, electrophoresis and other chemical treatment processes. Mechanical treatments consist of drawing, polishing, sandblasting, grinding and more.
Aluminum alloy sheets can be categorized into unpainted and painted products according to their surface treatment methods.
1. Unpainted products:
(1) Can be subdivided into hammer pattern aluminum sheets (with irregular patterns), embossed sheets (with regular patterns) and pre-matte and anodized aluminum surface treatment sheets.
(2) These products do not undergo painting treatment on their surface, so their appearance requirements are not high and they are comparatively cheaper.
2. Painted products:
(1) Classification:
Depending on the painting process, they can be classified into spray-painted and pre-laminated sheets;
According to the type of paint used, they can be classified into polyester, polyurethane, polyamide, modified silicone, epoxy resin, fluorocarbon, among others.
(2) Among the various coatings, the main difference in performance lies in their resistance to the sun's UV rays. The most commonly used front coating is fluorocarbon paint (PVDF), which has strong resistance to UV rays; on the back, you can choose polyester or epoxy resin coating as protective paint.
II. Aluminum alloy surface treatment methods
Let's take a look at the surface finishing process of aluminum and aluminum alloys in our daily products.
1. Drawing
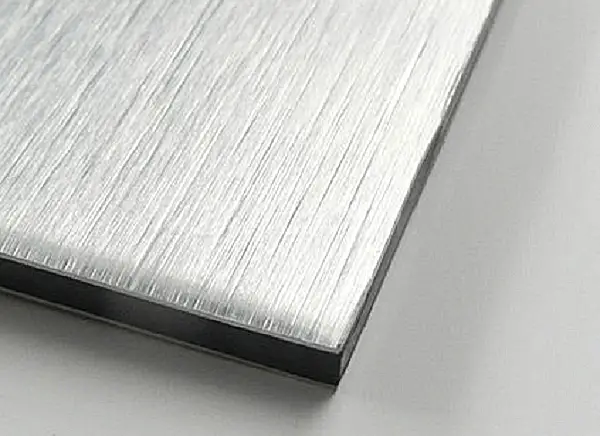
Metal drawing is a manufacturing process in which sandpaper is used to repeatedly scrape the surface of the material to produce a series of fine lines.
Drawing can be divided into straight drawing, random drawing, spiral drawing and line drawing.
The metal wire drawing process can create fine lines on the surface of the material, producing a silky, matte finish. The resulting product combines style and technology.
2. Diameter cutting
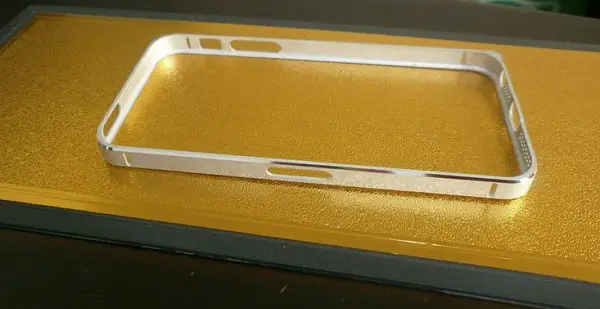
The diamond knife is mounted on the shaft of a high-speed engraving machine (typically 20,000 rpm) to carve the parts, creating a highlighted area on the surface of the product.
The brightness of the highlighted area is affected by the speed of the milling bit. The faster the speed, the brighter the light, while the slower the speed, the darker the light and it is easy to produce knife marks.
High-gloss and high-brightness cutting is especially used in mobile phones such as iPhone 5. In recent years, some high-end metal TV frames have adopted high-gloss milling technology, combined with anodizing and wire drawing technology, making the TV look stylish and technologically advanced.
3. Two-color anodizing
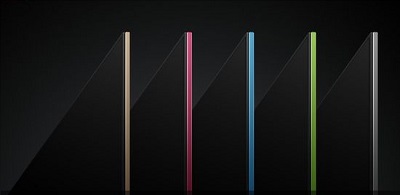
Two-color anodizing refers to the process of anodizing a product and imparting a different color to a specific area.
The two-tone anodizing process is complicated and expensive; However, the contrast between the two colors can better reflect the exclusive and sophisticated appearance of the product.
4. Anodizing
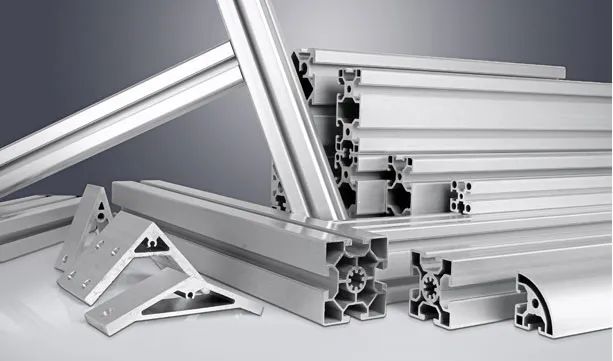
Anodizing refers to the electrochemical oxidation of a metal or alloy. It is the process of forming an oxide film on the surface of an aluminum article (anode) and its alloy under corresponding electrolyte and specific process conditions due to the application of current.
Anodizing can not only solve the defects of aluminum's surface hardness and wear resistance, but also extend the service life of aluminum and improve its appearance. It has become an indispensable part of aluminum surface treatment and is the most widely used and successful process.
Mainly, anodizing is applied to aluminum, taking advantage of electrochemical principles to create a film of Al2O3 (aluminum oxide) on the surface of aluminum and its alloys. This oxide film has special attributes such as protection, decoration, insulation and abrasion resistance.
Process: Single or gradient color: Polishing/Blasting/Drawing → Degreasing → Anodizing → Neutralizing → Dyeing → Sealing → Drying
5. Electrophoresis
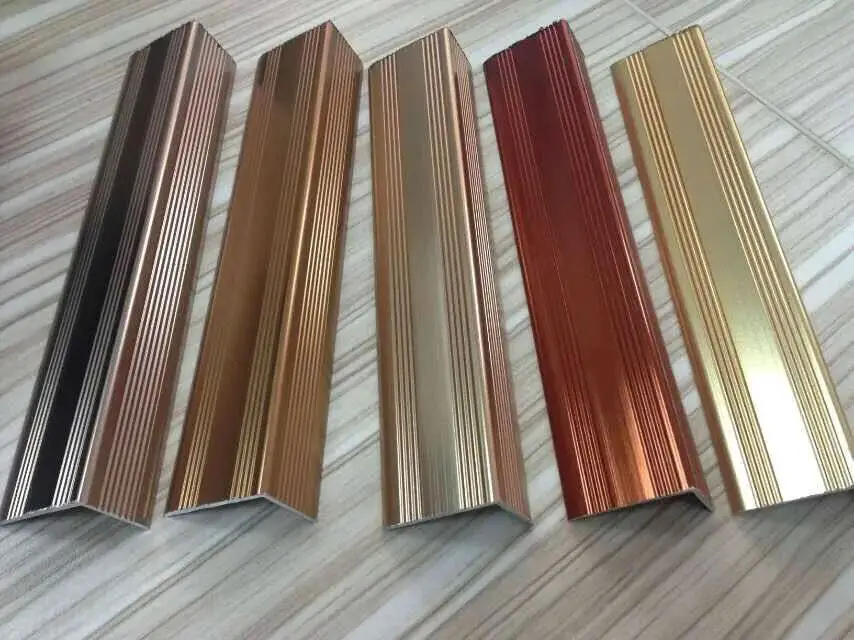
Applicable to stainless steel, aluminum alloys, etc., electrophoresis imparts different colors to the product while preserving the metallic shine. At the same time, it improves surface properties and has good anti-corrosion performance.
Process: Pretreatment → Electrophoresis → Drying
Technical characteristics:
Benefits:
- Rich color options;
- No metallic touch, suitable for sandblasting, polishing, wire drawing, etc.;
- Processing in a liquid environment, enabling surface treatment of complex structures;
- Mature technology, suitable for mass production.
Disadvantages:
Moderate defect coverage capacity; castings require high pretreatment for electrophoresis.
6. Microarc Oxidation (MAO)
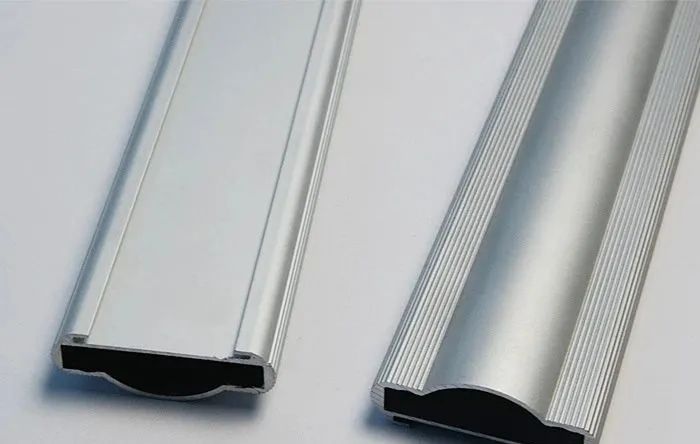
This is a process that forms a ceramic surface film layer by applying high voltage to an electrolyte solution (usually a weak alkaline solution). It is the result of physical discharge and electrochemical oxidation.
Process: Pre-treatment → Hot water washing → MAO → Drying
Technical characteristics:
Benefits:
- Ceramic texture, matte appearance without high gloss products, delicate touch, fingerprint resistant;
- Broad-based materials: Al, Ti, Zn, Zr, Mg, Nb and their alloys;
- Simple pretreatment, excellent corrosion resistance, weather resistance and heat dissipation performance.
Disadvantages:
Currently, color options are limited, with only mature black, gray, etc.; Vibrant colors are difficult to achieve. The cost is mainly affected by high electricity consumption, making it one of the most expensive surface treatments.
7. PVD vacuum coating
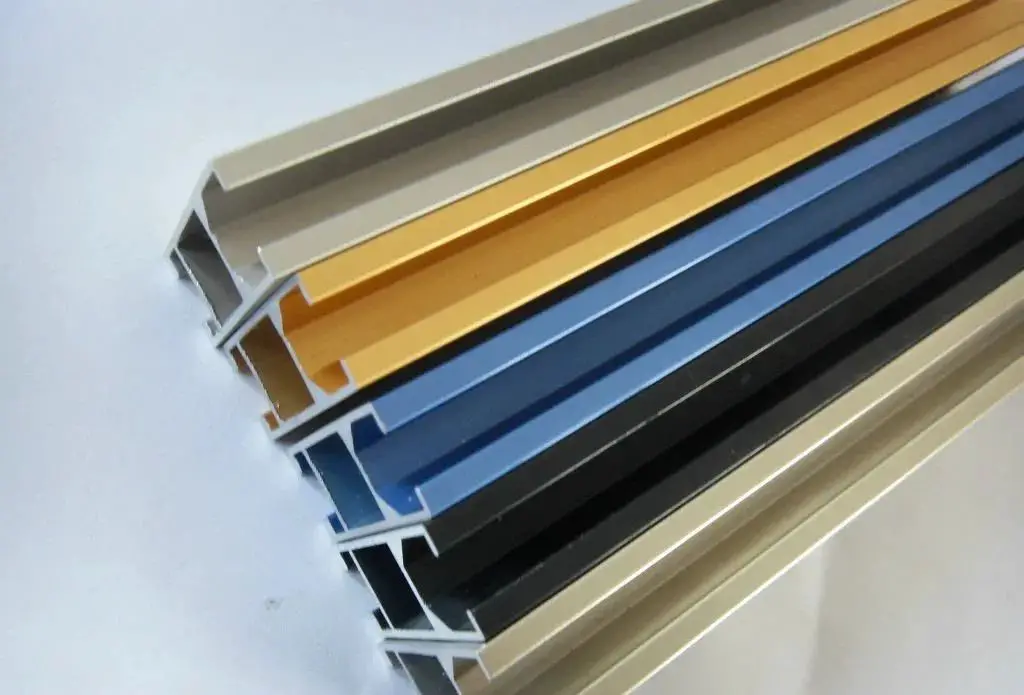
Physical Vapor Deposition (PVD) is an industrial manufacturing process, a technique primarily used to deposit thin films through physical processes.
Process: Pre-cleaning for PVD → Vacuum furnace loading → Target cleaning and ion cleaning → Coating → End of coating, cooling and unloading → Post-processing (polishing, AFP)
Technical characteristics:
PVD (Physical Vapor Deposition) can deposit high hardness and high wear resistance metal ceramic decorative coating on the metal surface.
8. Electroplating
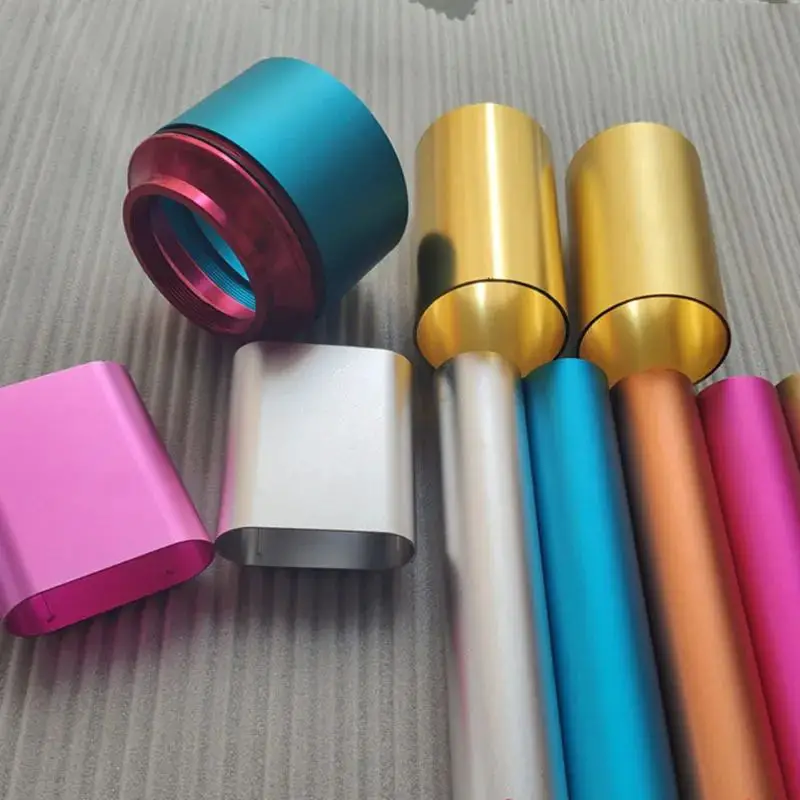
Electroplating is a technique that uses electrolysis to coat the surface of a metal with a thin layer of metallic film, thus providing protection against corrosion and increasing wear resistance, electrical conductivity, reflectivity and aesthetics.
Process flow: Pretreatment → Cyanide-free alkaline copper → Cyanide-free white tin copper → Chrome plating
Technical characteristics:
Benefits:
- High gloss of the coating layer, high quality metallic appearance.
- Substrates can be SUS, Al, Zn, Mg, etc.; relatively lower cost than PVD.
Disadvantages:
Poor environmental protection, high risk of environmental pollution.
9. Powder Coating
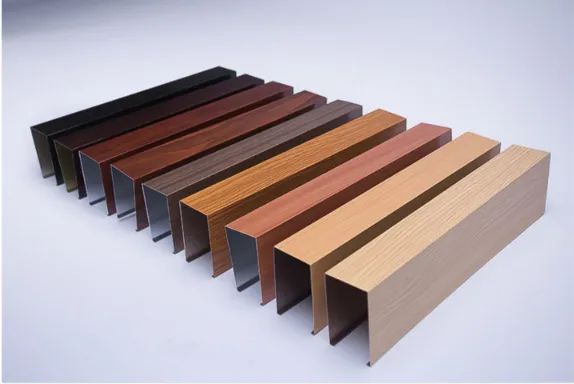
Powder coating is a process in which a powder coating device (electrostatic powder sprayer) sprays powder coating onto the surface of the workpiece. Under electrostatic action, the powder adheres uniformly to the surface of the part, forming a powdery coating. After leveling and baking at high temperature, the powder coating transforms into a final coating with varying effects depending on the type of powder coating used.
Process flow: Part assembly → Electrostatic dust removal → Coating → Low temperature leveling → Baking
Technical characteristics:
- Rich color selection, choose between high gloss and matte finish.
- Lower cost, suitable for housing construction furniture and heat sinks.
- High utilization rate, 100% utilization, environmentally friendly.
- Strong defect protection ability.
- It can imitate the effect of wood grain.
10. Drawing
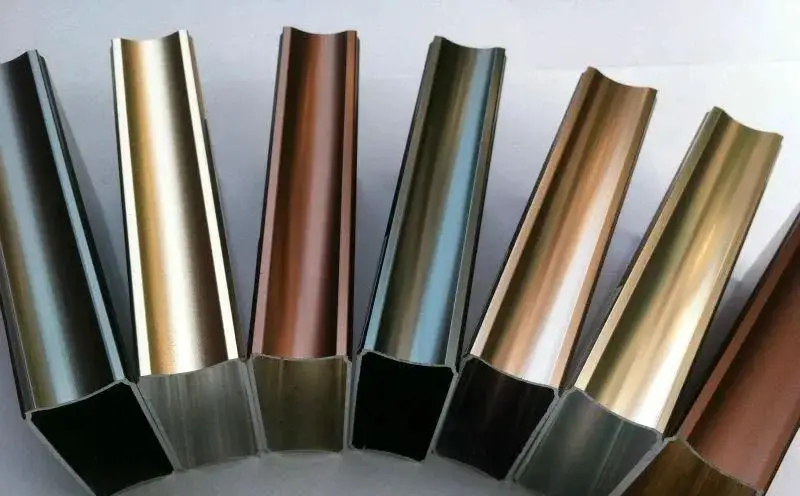
Wire drawing is a surface treatment method that forms linear striations on the surface of a product through grinding, creating a decorative effect. Depending on the pattern of the flutes after drawing, it can be divided into: straight line design, random line design, wave pattern and spiral pattern.
Technical features: Wire drawing treatment can give the metal surface a non-mirror metallic luster, while eliminating small defects on the metal surface.
11. Sand Blasting
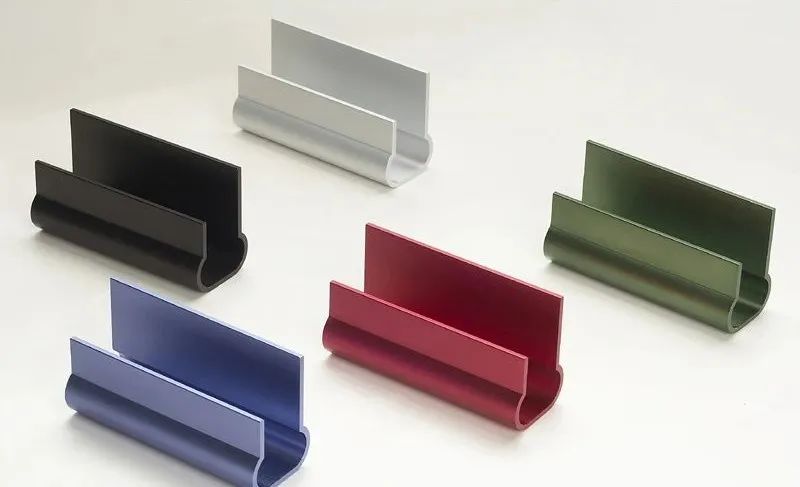
Sand blasting is a process that uses compressed air as force to form a high-speed jet, which blows the blasted material at high speed onto the surface of the part to be processed, causing changes to the external surface or shape of the part and achieving a certain level of cleanliness and different levels of roughness.
The process involves cleaning and roughening the metal surface using high-speed sand flow.
This aluminum surface treatment method can achieve a certain degree of cleanliness and different levels of roughness on the surface of the part, which improves the mechanical properties of the surface of the part.
As a result, the fatigue resistance of the part is improved, the adhesion of the coating is increased, the durability of the coating film is prolonged, and the leveling and decoration of the coating is also facilitated.
This process is often seen in various Apple products and is increasingly used in the manufacture of TV sets or middle frames.
Technical characteristics:
- It can achieve different levels of reflection or matte finish.
- It can clean small burrs on the surface of the workpiece, making the surface smoother, eliminating the risk of burrs and improving the quality of the workpiece.
- It can remove the residual dirt left during pretreatment, improve the smoothness of the workpiece, and reveal a uniform and consistent natural metallic color, making the workpiece more aesthetically pleasing.
12. Polishing
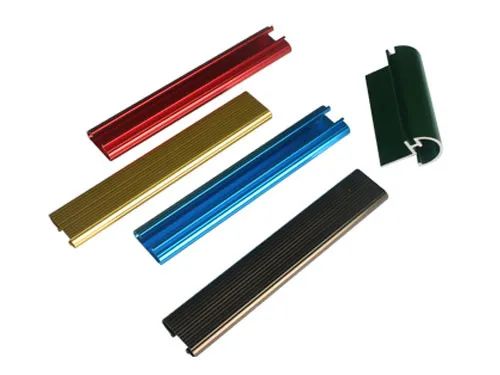
Polishing is a modification process performed on the surface of the part using a flexible polishing tool and abrasive particles or other polishing media.
Depending on the polishing process: rough polishing (basic polishing process), medium polishing (fine machining process) and fine polishing (gloss process), selecting the appropriate polishing wheel can achieve the best polishing effect and increase the polishing efficiency. polishing.
It improves the dimensional or geometric accuracy of the workpiece, achieves a smooth surface or mirror-like shine, and can also remove shine.
Mechanical, chemical or electrochemical methods are used to reduce the surface roughness of the workpiece to obtain a flat and shiny surface.
The polishing process is mainly divided into mechanical polishing, chemical polishing and electrolytic polishing.
Aluminum parts can be mechanically polished and electrolytically polished to achieve a mirror effect close to that of stainless steel, giving people a sense of high-level simplicity and modern future. Of course, this surface finish is subject to fingerprints and requires more care.
13. Engraving
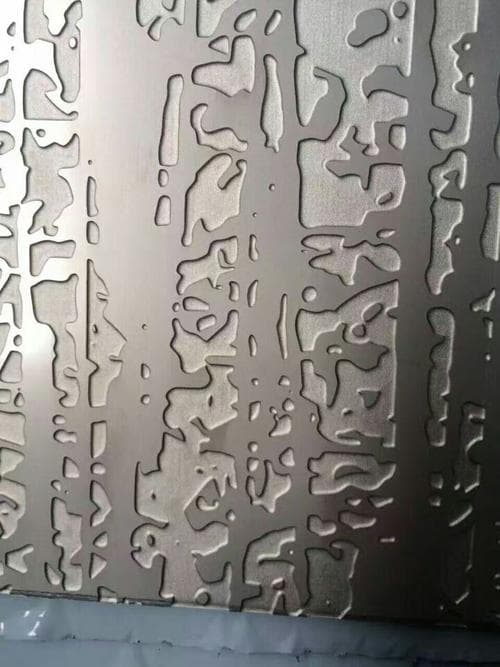
Engraving, often referred to as photochemical engraving, involves removing the protective film from the area to be engraved after exposure and developing, making contact with a chemical solution during engraving, to dissolve and corrode, forming embossed or hollow modeling effects. .
Process flow:
Exposure method: The engineer opens the size of the material according to the charts – Material preparation – Material cleaning – Drying → Film gluing or coating → Drying → Exposure → Developing → Drying – Etching → Film removal → OK
Screen printing method: Material cutting → Plate cleaning (stainless steel and other metal materials) → Screen printing → Etching → Film removal → OK
Technical characteristics:
Benefits:
- It can perform fine processing on metal surfaces.
- Gives special effects to the metal surface.
Disadvantages:
The corrosive liquid used during engraving (acid, alkali, etc.) is mainly harmful to the environment.