Currently, the manufacturing industry is experiencing an increase in automation and intelligence, with the rapid development of industrial robots leading to greater maturity in their application in the processing and production fields.
It should be noted that these are not the only applications of industrial robots.
The possibilities for industrial robots are limited only by the imagination.
Arc welding
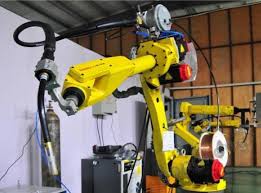
Arc welding robots are categorized into two main types: melting electrode welding and non-melting electrode welding. These robots have unique characteristics such as the ability to perform long-term welding operations, high productivity and consistent high quality and stability in welding processes.
Spot welding
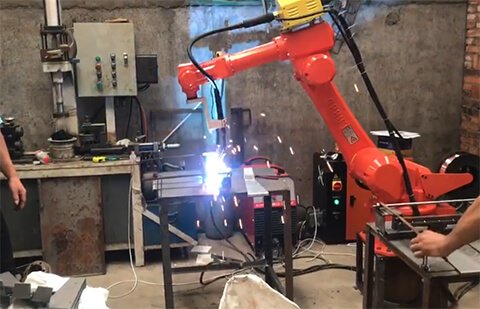
The spot welding robot operates following the actions, sequences and parameters described in its programmed instructions. The entire process is fully automated and includes a communication interface with external devices.
This interface allows the robot to receive control commands from a master computer or higher-level management system, allowing it to perform its work.
laser welding
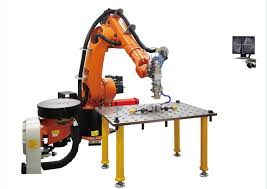
Laser welding is known to cause minimal deformation in the part being welded, resulting in virtually no gaps in the joint and a high weld depth to width ratio. This results in a higher quality weld compared to traditional welding methods.
Laser cut
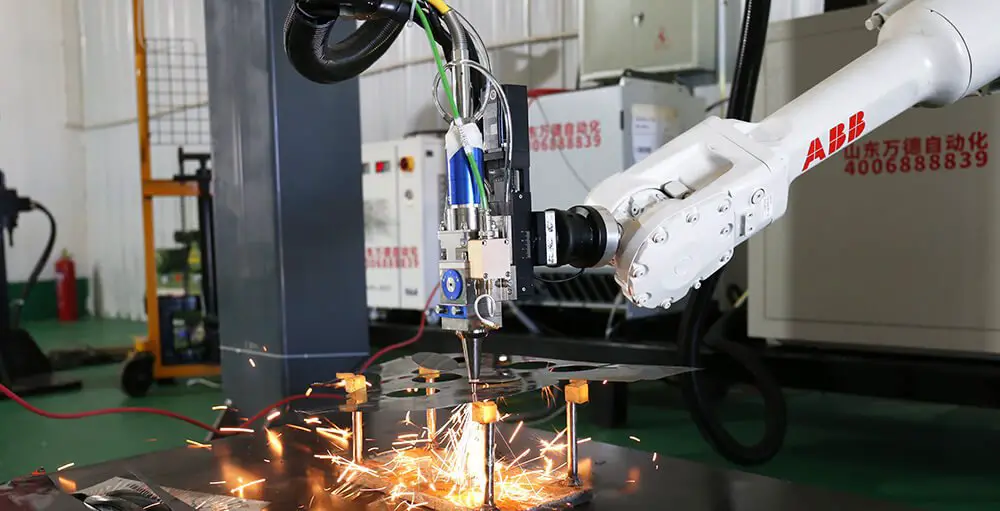
Robotic laser cutting systems are characterized by two main features: the ability of industrial robots to freely and flexibly perform complex 3D curve processing trajectories and the use of flexible, long-distance transmission laser fibers as the transmission medium , which does not limit the range of movement of the robot.
Loading and unloading the machine
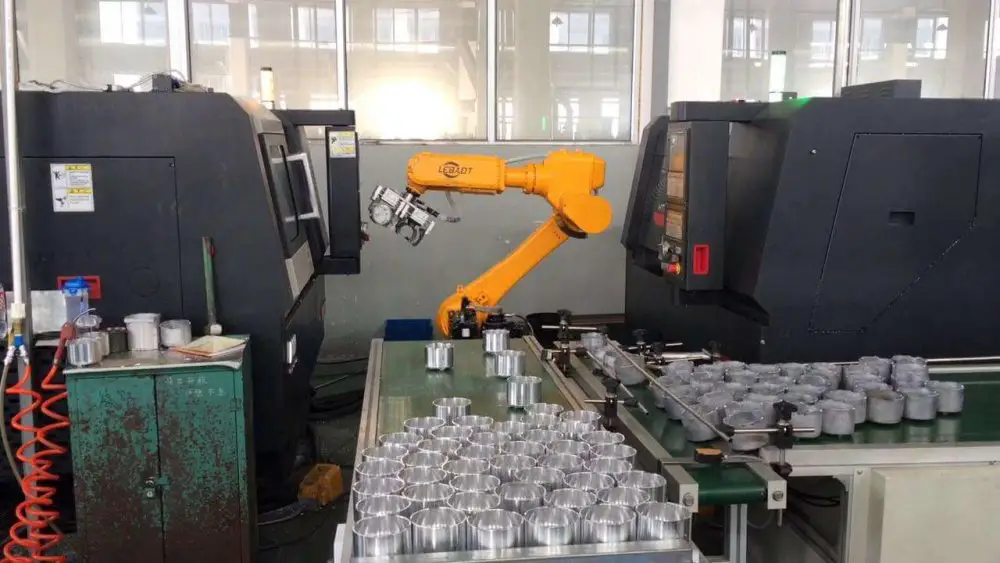
Robotic loading and unloading systems are known for their high efficiency, stability, simplicity and ease of maintenance. They can be used for a wide range of products, allowing users to quickly adjust product structures and expand production capacity. This results in a significant reduction in the work intensity of industrial workers.
Forging
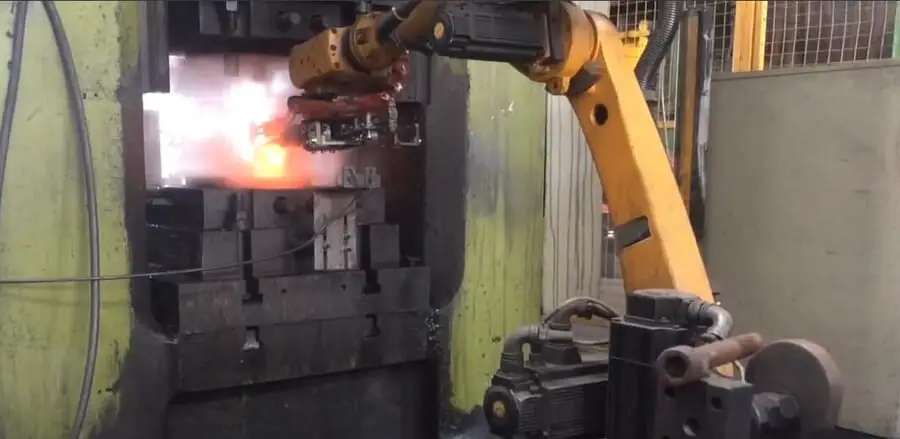
The forging robot is automated through the use of advanced computer control and programming. It is capable of completely replacing manual labor in the continuous and repetitive tasks of loading, turning and unloading in the forging production process. This leads to a reduction in the intensity and dangerousness of work, as well as an increase in the degree of automation and efficiency of the production process.
Deburring
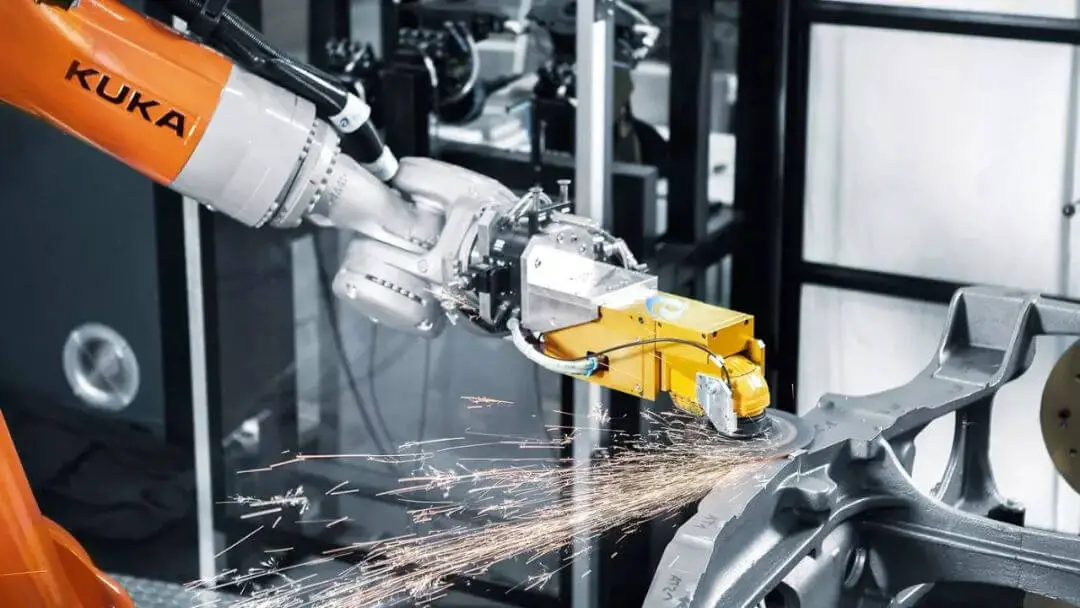
The deburring robot is the result of a combination of several disciplines, including mechanical and precision machines, microelectronics and computers, automatic control and drive, sensors and information processing, and artificial intelligence. It represents the latest advances in these fields.
Stamping
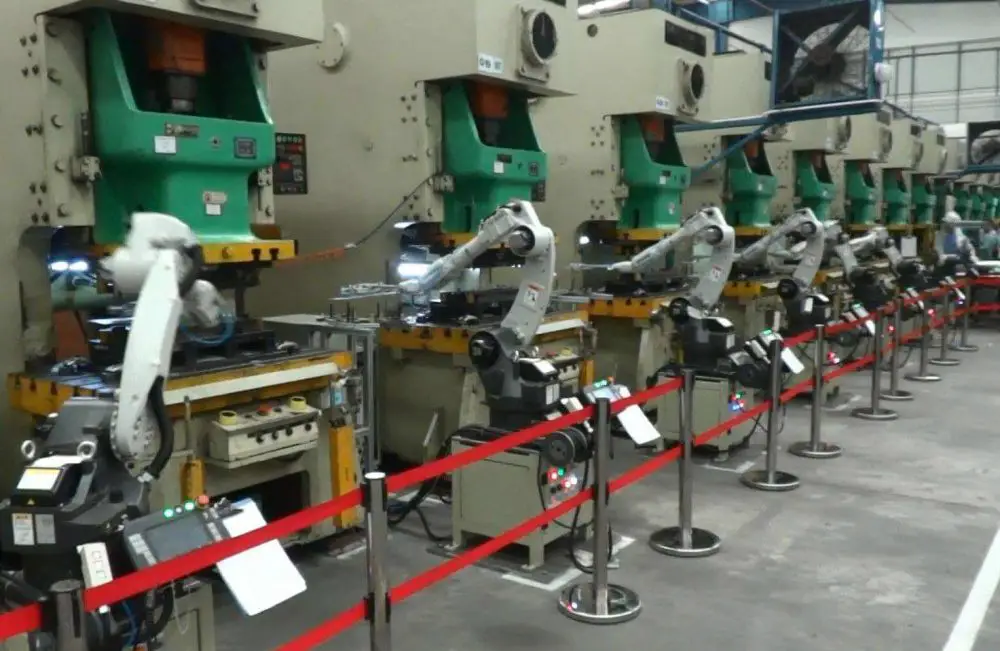
Stamping robots, used in manipulators, improve automation in transferring materials, loading and unloading parts, changing tools and assembling machines. This results in increased labor productivity, reduced production costs and a faster pace of mechanization and automation of industrial production.
Glue
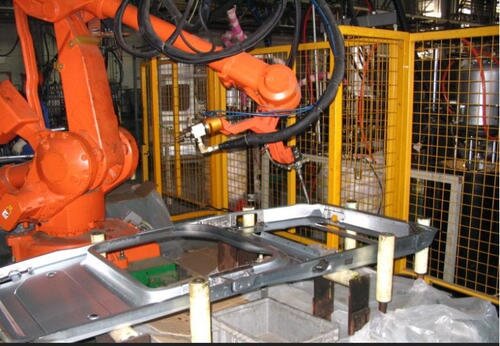
The use of robots in gluing and distribution has significantly improved efficiency, saving a considerable amount of labor and reducing labor costs. The investment in this technology will typically be recouped within a year of operation, and the robot will continue to function for at least ten years with proper maintenance.
As fully automated, high-volume gluing lines become more prevalent, the market outlook and development potential for gluing systems is expected to grow.
Assembly
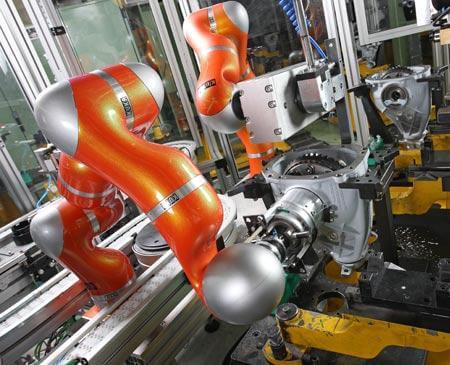
Assembly robots are a crucial component of flexible automated assembly systems and consist of a robot operator, controller, end effector and sensing system. Operator structures come in several types, including horizontal joint, right-angle coordinate, multijoint, and cylindrical coordinate.
Controllers typically utilize multi-CPU or multi-stage computer systems to control motion and perform motion programming. End effectors are designed to adapt to different mounting objects such as grippers and wrists.
The sensing system collects information about the interaction between the assembly robot, its environment and the assembly object.
Robots ' vision
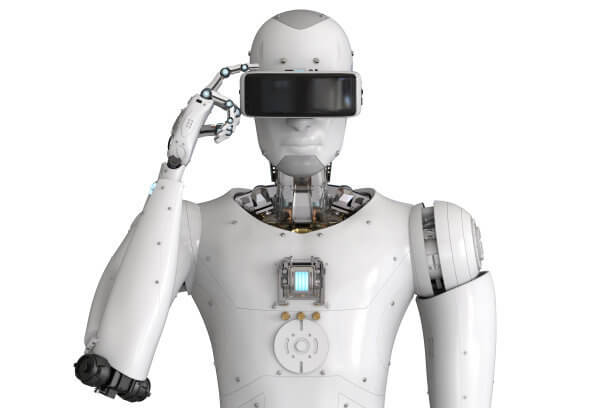
Robotic vision is a crucial aspect of any robotic system. It allows robots to acquire two-dimensional images of their environment through the use of vision sensors, which are then analyzed and interpreted by vision processors. The processed information is then translated into symbols, allowing the robot to recognize objects and determine their location.
Pulverization
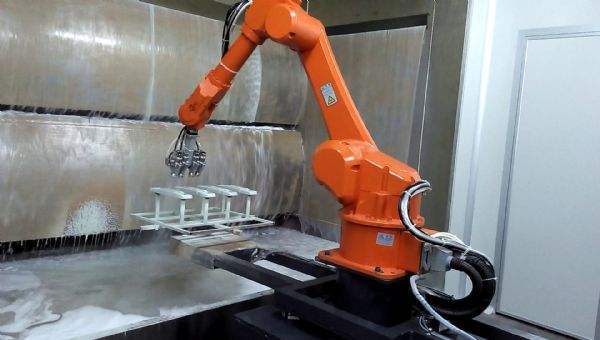
Spraying robots, also known as spray painting robots, are industrial robots that can automate the process of spray painting or applying other coatings.
Key benefits of using spray painting robots include:
(1) Exceptional flexibility and a wide range of work capabilities.
(2) Better spray quality and material utilization.
(3) Easy operation and maintenance, with offline programming capabilities that significantly reduce field commissioning time.
(4) High equipment utilization rate, with spray robots typically having a utilization rate of 90% to 95%.
Ordering
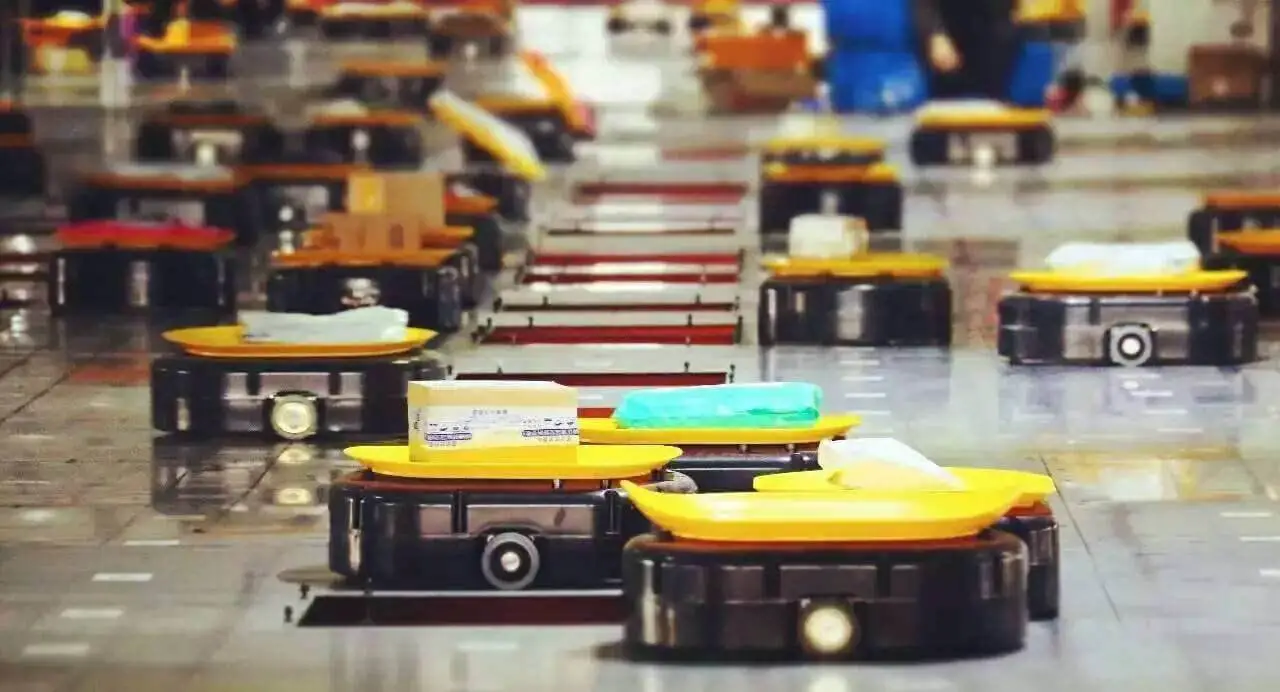
A sorting robot is a robot that uses sensors, objective mirrors, and electronic optical systems to efficiently sort goods.
Automatic sorting robots have become widely used. For example, Japan has developed an automatic apple dispenser that can separate up to 540 apples per minute based on color, brightness and size, and distribute them into different containers.