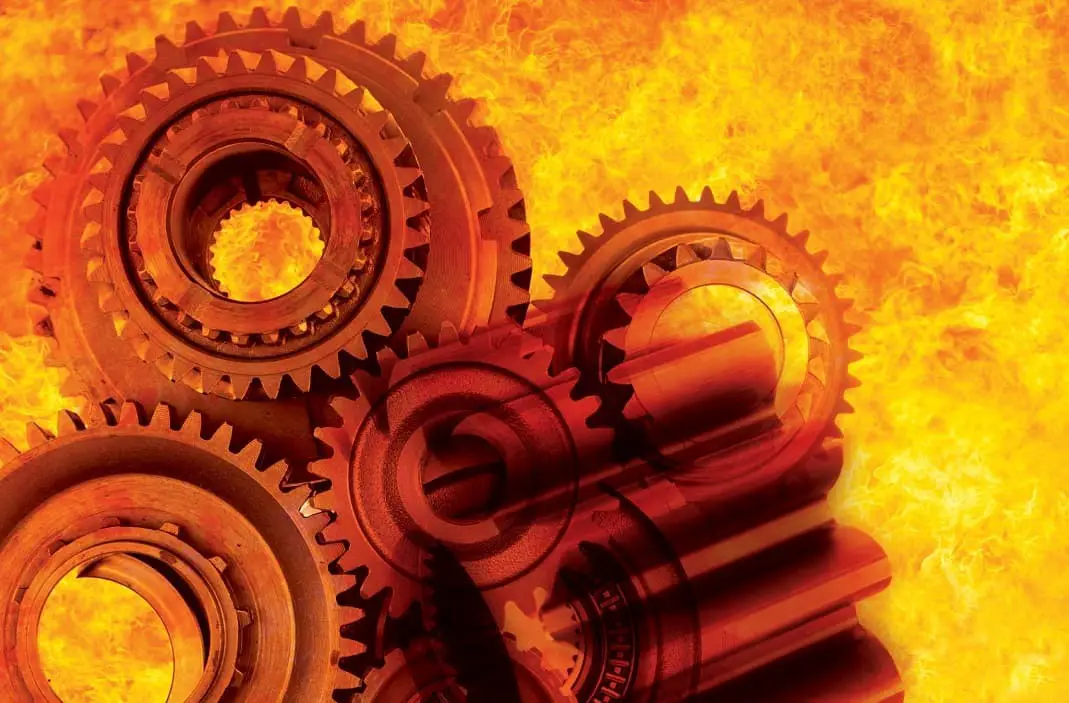
1. Carbon content in steel
The carbon content has the greatest influence on the warpage distortion and volume distortion of gears during quenching.
2. Alloying elements in steel
Alloying elements in steel have a significant impact on gear distortion, with certain elements such as C, Mn, Ni, Cr and Mo increasing hardenability and tendency to distortion. On the other hand, other elements such as Cr, Mn, Mo, Si, Ni and Ti can help reduce distortion.
3. Hardenability of steel
The greater the hardenability of the steel, the more pronounced the distortion during tempering; whereas, with lower hardenability, the tempering distortion is less significant.
4. Gear shape and section size
The gear design has low symmetry in its shape and irregular sections.
The spokes in the gear design lack rigidity.
The positioning of the process hole in the gear design is inappropriate, leading to increased heat treatment distortion of the gear.
5. Original steel structure
1)The non-uniformity of steel microstructure significantly affects the heat treatment distortion. This is due to coarse structures, large segregation and network structures that exacerbate distortion after quenching.
2) Defects such as banded structures and segregation have become critical factors leading to gear distortion.
3)Macrosegregation in steel ingots often results in square segregation in the cross-section of the steel material, leading to uneven quenching distortion of disc gears.
4) The distortion of gears during heat treatment is uniform in gears produced by continuous casting square billets. However, the heat treatment distortion of gears produced by continuous casting rectangular billets has significant directionality that affects gear distortion.
5) The finer the grain size, the less distortion occurs after quenching.
6) Non-uniform normalization treatment of gear blanks leads to heat treatment distortion in gears.
6. Forge
1)Proper forging techniques can help reduce distortion in metals.
In particular, creating a streamlined metal structure through forging can minimize distortion during heat treatment. Furthermore, careful forging can reduce segregation, promote uniformity in the metal structure, improve banding, and further reduce heat treatment distortion.
2)If the mold cavity is not completely filled with metal, the final heat treatment may be inconsistent and cause distortion.
3) Forging of gear blanks may lead to increased distortion during heat treatment due to high temperature heating, uneven deformation and high final forging temperatures.
7. Preliminary heat treatment of the blank
1)Performing preliminary heat treatment on gear blanks can help minimize distortion during the final heat treatment process. It has been observed that when using normalization techniques, the distortion is more pronounced compared to isothermal normalization.
2) Gear blanks undergo quenching and tempering before the final quenching process. After extinction, the distortion tends to exhibit a predictable pattern and the overall magnitude of the distortion is reduced.
8. Residual stress
The gear machining process can induce stress, leading to metal distortion.
During the gear heating process, thermal stress not only contributes to distortion, but the release of internal stress can also cause it.
9. Quenching Heating Process
1)The maximum voltage that can be produced under heating temperature is higher in gears with larger diameter or thickness, resulting in greater distortion.
2)In many production conditions where gears are fixed, there is a significant temperature difference in each part during the initial stage of entering the furnace. The resulting thermal stress is sufficient to cause plastic deformation in the part that first reaches the high temperature, leading to local distortion.
3) The warping distortion of slender shaft teeth and thin plate gears is greatly influenced by uneven heating, including rapid heating.
4)Generally, when heating is uneven, such as with direct heating elements, the side of the gear with higher internal temperature tends to become concave and produce bending distortion after cooling.
5)Heating speed directly affects the formation of thermal stress during the heating process and may cause gear distortion.
10. Cooling
1) Quench cooling rate and quench cooling medium
The greater the cooling capacity, the stronger the quenching intensity (H), and the greater the temperature difference between the inside and outside of the gear (or in different thicknesses), the greater the voltage generated.
Distortion is related to the type of quenching cooling medium, its cooling performance and hardenability.
2) Uneven cooling
Distortion can be caused by several factors, such as gear structure, gear fixation, and quenching cooling medium characteristics.
3) Quenching cooling medium temperature
Generally, increasing the temperature of the quenching cooling medium such as quenching oil can reduce the heat treatment distortion of gears.
11. Quenching operation
1) Gear fixing and support mode
Gear distortion is greatly influenced by fixing and hanging methods, slings and their support methods when loading the gear into the furnace. This is especially true for thin-walled ring gears with large inner and outer diameters. In addition to the expansion and contraction of the inner and outer diameters, it can often cause the roundness to be out of tolerance.
Improper furnace loading can easily produce large creep at high temperature, which can affect the flow of quenching cooling medium and the cooling uniformity of gears during quenching. As a result, the uniformity of distortion and distortion is affected.
2) Extinguishing heating temperature and heating uniformity
The impact of extinction temperature on warpage distortion is significantly greater than that on volume distortion.
In general, increasing the quenching temperature results in greater gear distortion.
Distortion is caused by uneven heating.
3) Repeated tempering
If gears fall out of tolerance due to poor heat treatment quality, repeating the quenching process during repair may result in increased distortion due to additional quenching cycles.
4) Effect of quenching cooling
The gear cools at high speed, which causes volume expansion simultaneously. If cooling is not uniform, it may result in greater distortion.
In double medium quenching or step quenching, the residence time in the first medium is long.
The high fluidity and impact of the quenching cooling medium on the gear have a significant influence on the distortion of the gear during heat treatment.
5) Operational factors
This problem is often linked to violation of process regulations during operation.
For example, during the threading process, gears may collide with each other. Additionally, impact between the gear and the oven, oven body, oven door or other hard objects may result in gear distortion.
When the gear is quenched outside the furnace, unstable operation and significant shaking can further intensify gear distortion, especially when dealing with slender gear shafts and thin plate gears.
12. Quenching, cold treatment and aging
1) Temperament
Changes in the size of hardened gears are mainly caused by transformations in their microstructure.
2) Cold treatment
For gears with a high content of alloying elements or requiring high precision, a cold treatment is often carried out at sub-zero temperatures to further transform the retained austenite into martensite, which leads to a higher level of distortion.
Furthermore, it should be noted that the size of the expansion tends to increase with higher quenching temperatures.
3) Aging treatment
The main cause of aging distortion in the hardened gear structure is the amount of retained austenite.
During natural aging, stress relaxation occurs due to hydrogen escape. This relaxation and release of stresses can cause a transformation of a small amount of retained austenite.