A soldagem a laser é altamente vantajosa devido à sua velocidade rápida, deformação mínima, soldas esteticamente agradáveis e alta resistência. É amplamente utilizado em áreas como aviação, automóveis e medicina.
Especificamente, a soldagem por fusão a laser é um processo de soldagem sem contato que cria uma variedade de formatos de costura de soldagem com excelente consistência de costura. Tem um enorme potencial na fabricação de chapas metálicas.
Este artigo enfoca a aplicação do projeto de chapa metálica na soldagem a laser de estruturas de alojamento com juntas flangeadas chanfradas de 45°.
Projeto de chapa metálica na estrutura da caixa de soldagem a laser
O corpo da caixa é feito de aço inoxidável 304 com 1,5 mm de espessura e tem dimensões de 200 mm × 200 mm × 115 mm. A caixa é dobrada em ângulos de 90°, 90° e 80° de baixo para cima.
A estrutura da caixa está ilustrada na Figura 1.
A Tabela 1 exibe os parâmetros de soldagem a laser.
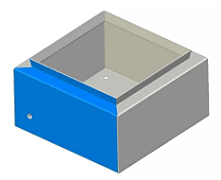
Figura 1 Diagrama esquemático da estrutura da caixa
Processo de soldagem | Soldagem por condução térmica a laser |
---|---|
Potência (W) | 3.000 |
Velocidade (m/min) | 1,8 |
Desfocar (mm) | 10 |
Tabela 1 Parâmetros de soldagem a laser
No processo tradicional de soldagem de estruturas em caixa de aço inoxidável, é comum a realização de tratamentos de retificação e polimento após a soldagem, a fim de obter um produto final esteticamente mais agradável. No entanto, estes procedimentos subsequentes podem ser complicados e demorados, e também podem resultar em deformação e penetração da soldadura.
A soldagem a laser, por outro lado, oferece vantagens significativas na soldagem de chapas metálicas, como velocidades de soldagem rápidas, deformação mínima e costuras de soldagem visualmente atraentes. Como tal, encontrar maneiras de aplicar os benefícios da soldagem a laser, incluindo sua estreita zona afetada pelo calor e alta precisão, à soldagem de estruturas em caixa tornou-se uma questão urgente a ser abordada.
Projeto de sobreposição da estrutura da caixa de soldagem a laser
Em estruturas de caixa de aço inoxidável soldadas, a solda de ângulo da caixa constitui uma parte significativa do processo geral de soldagem.
Para obter uma costura de soldagem a laser redonda, otimizamos a quantidade de sobreposição nas técnicas de soldagem tradicionais, conforme ilustrado nas Figuras 2 e 3. Nessas figuras, t representa a espessura da placa, a é a quantidade de sobreposição, b é a posição de o centro do laser na seção transversal da placa e α denota o ângulo de inclinação do laser.
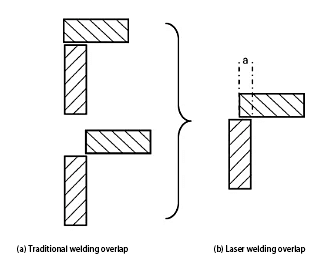
Figura 2 Melhoria da sobreposição da costura de solda em ângulo
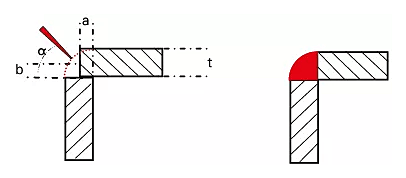
Figura 3 Sobreposição de soldagem a laser
A quantidade otimizada de sobreposição é soldada usando soldagem por condução térmica a laser. A distância de desfocagem é definida com precisão em 10,00 mm e a precisão de focagem é mantida em 0,01 mm através da utilização de um sistema de focagem automático.
Com o auxílio de uma câmera CCD de alta ampliação, o valor b pode ser posicionado com precisão, resultando em uma solda a laser redonda sem a necessidade de fio de enchimento, conforme ilustrado na Figura 4b.
Este método de otimização para a quantidade de sobreposição é mais adequado para placas com espessura de 3 mm ou menos, em que os valores de a, b e α são determinados pelo valor de t.

Figura 4 Diagrama esquemático da otimização da quantidade de sobreposição e do efeito real da soldagem a laser
Projeto da ranhura de liberação de canto da estrutura da caixa de soldagem a laser
Em estruturas de caixa de aço inoxidável soldadas, a otimização da ranhura de alívio dos cantos é crucial, pois impacta diretamente a eficácia da estrutura inferior da caixa.
Nos processos de soldagem tradicionais, ranhuras de alívio de canto retangulares ou arredondadas são comumente utilizadas. No entanto, tais ranhuras de alívio de canto podem facilmente resultar em soldadura ou soldadura insuficiente quando se utilizam técnicas de soldadura a laser.
O diagrama esquemático da ranhura de alívio de canto é ilustrado na Figura 5.
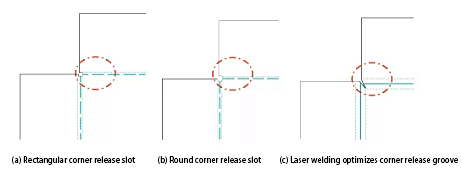
Figura 5 Diagrama esquemático do slot de liberação de canto
Ao utilizar o bloco de processo de ranhura de alívio de canto para soldagem a laser, a estrutura do produto pode ser otimizada.
Com a soldagem a laser, é possível obter um efeito de soldagem completo e arredondado, quase sem necessidade de tratamento secundário e reduzindo bastante o tempo de processamento subsequente, conforme demonstrado nas Figuras 6 e 7.
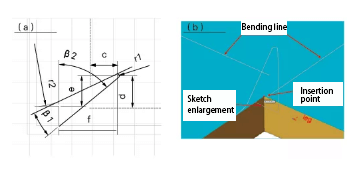
Fig. 6 Diagrama esquemático do projeto de soldagem a laser da ranhura de liberação de canto
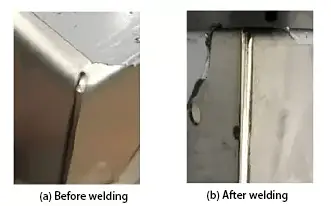
Figura 7 Efeito real da soldagem a laser da ranhura de liberação do canto
Projeto de interface chanfrada de 45 ° para flangeamento de estrutura de caixa de soldagem a laser
Na estrutura em caixa feita de aço inoxidável soldado, a interface chanfrada de 45° do flange tem dificuldade de fechar firmemente devido à quantidade de deformação por flexão, conforme ilustrado em A na Figura 8. Esta questão representa um desafio significativo para a soldagem a laser.
Conseqüentemente, o design da interface impacta diretamente a qualidade da soldagem da estrutura da caixa. Além disso, existirá uma lacuna considerável em B, dificultando o gerenciamento da soldagem direta a laser.
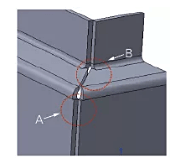
Figura 8 Diagrama esquemático antes da otimização
Para resolver esse problema, otimizamos a estrutura do gabinete. No processo de projeto, uma porção do metal da superfície do degrau foi removida e duas superfícies de degrau menores foram estendidas, conforme ilustrado na Figura 9a.
Durante o desdobramento, a porção previamente cortada é compensada usando a superfície final como referência, conforme mostrado nas Figuras 9b e 9c.
Em B na Figura 8, duas superfícies escalonadas são estendidas alternativamente para aumentar a quantidade de compensação metálica, o que compensa a lacuna criada nessa área. Esta solução é ilustrada na Figura 9d.
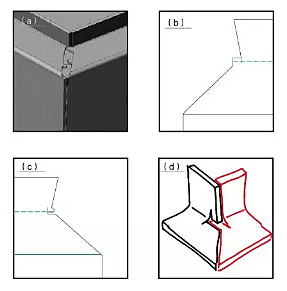
Figura 9 Diagrama esquemático do projeto de chapa metálica da interface do flange chanfrado de 45°
A Figura 10 demonstra o resultado do processo de soldagem a laser.
Conforme mostrado na Figura 10a, a interface é hermeticamente vedada, atendendo aos requisitos do processo de soldagem a laser. A superfície da costura de soldagem é lisa e esteticamente agradável, com uma transição natural e sem afundamentos ou defeitos de soldagem visíveis.
Além disso, conforme mostrado na Figura 8, a lacuna em B também está bem preenchida, demonstrando a eficácia da solução de otimização implementada.
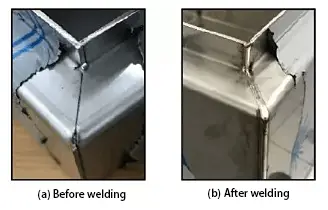
Figura 10 Efeito de soldagem a laser da interface chanfrada de 45° do flange
Conclusões
À medida que o processo de soldagem continua a evoluir, os esquemas tradicionais de projeto de chapa metálica ficarão gradualmente desatualizados. Da mesma forma, à medida que a soldagem a laser ganha maior adoção na indústria de chapas metálicas, haverá necessidade de novas soluções de projeto de chapas metálicas para soldagem a laser. É imperativo desenvolver e introduzir projetos inovadores que sejam mais adequados às capacidades e limitações do processo de soldagem a laser.