A tolerância geométrica especificada pela norma nacional é dividida em duas categorias: tolerância geométrica e tolerância de posição, num total de 14 itens.
Seus nomes e símbolos são mostrados na tabela abaixo.
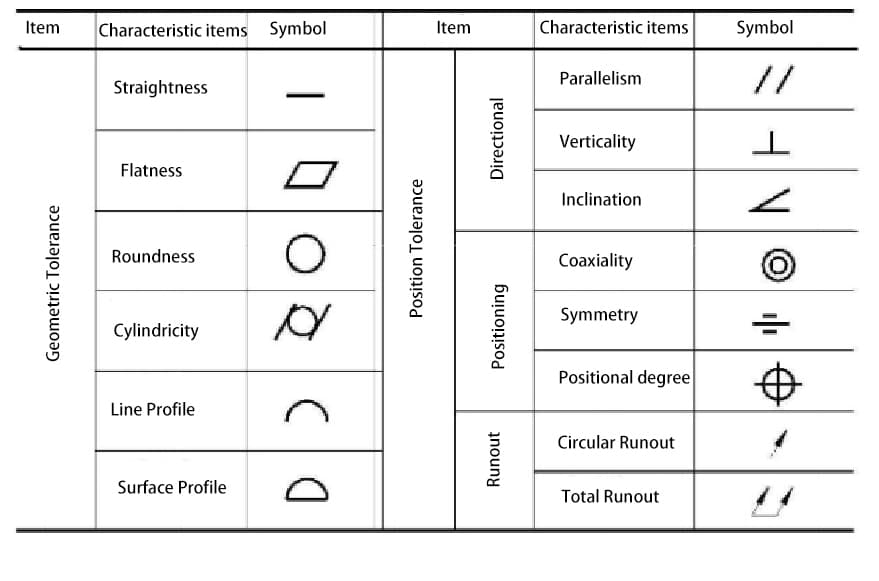
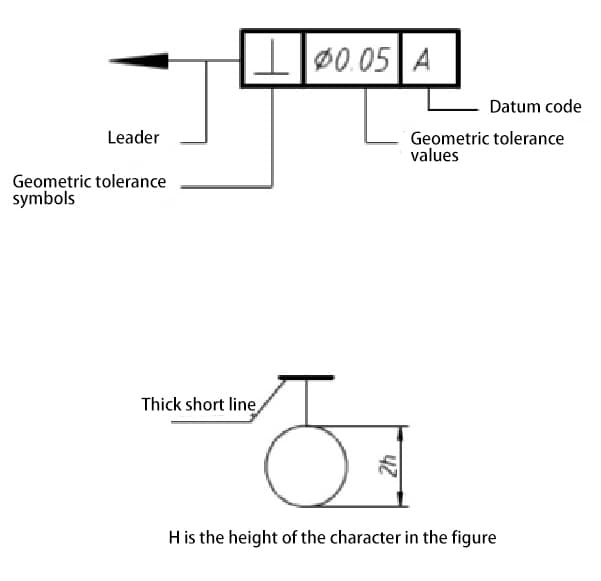
EU. Definição de tolerância de posicionamento geométrico
Retidão – Todos os pontos estão em linha reta, com tolerância especificada pela região entre duas linhas paralelas.
Planicidade – Todos os pontos de uma superfície estão em um plano, com tolerância especificada pela região entre dois planos paralelos.
Redondeza – Todos os pontos de uma superfície estão em uma circunferência, com tolerância especificada pela região entre dois círculos concêntricos.
Cilindricidade – O eixo de todos os pontos em uma superfície rotativa é equidistante de um eixo comum. A tolerância de cilindricidade define a região de tolerância formada por dois cilindros concêntricos, onde esta superfície rotativa deve cair dentro desta região.
Tolerância de perfil – Define o método de tolerância para superfícies irregulares, linhas, arcos ou planos comuns. O perfil pode ser aplicado a um único elemento de linha ou a toda a superfície de uma peça. A tolerância do perfil especifica o limite exclusivo ao longo do perfil real.
Perpendicularidade – A superfície ou eixo é perpendicular ao plano ou eixo de referência. A tolerância perpendicular especifica um dos seguintes: a região definida por dois planos perpendiculares ao plano ou eixo de referência, ou a região definida por dois planos paralelos perpendiculares ao eixo de referência.
Paralelismo – A superfície ou eixo e todos os pontos são equidistantes do plano ou eixo de referência. A tolerância de paralelismo especifica um dos seguintes: a região definida por dois planos paralelos ou linhas paralelas ao plano ou eixo de referência, ou a região de tolerância de cilindricidade onde o eixo é paralelo ao eixo de referência.
Coaxialidade – O eixo de todos os elementos combináveis que se cruzam da superfície rotativa é o eixo comum do recurso de dados. A tolerância de coaxialidade especifica a região de tolerância de cilindricidade onde o eixo é igual ao eixo de referência.
Tolerância de posição – A tolerância de posição define a área onde o eixo central ou plano central pode se desviar da posição real (teoricamente correta).
A dimensão básica estabelece a posição real entre o recurso de dados e o recurso inter-relacionado. Erro de posição é o desvio posicional total permitido entre o recurso e sua posição correta.
Para recursos cilíndricos, como furos e diâmetros externos, a tolerância de posição geralmente é o diâmetro da região de tolerância onde o eixo do recurso deve cair. Para recursos não circulares (como ranhuras e projeções curtas), a tolerância de posição é a largura total da região de tolerância onde o plano central do recurso deve cair.
Desvio circular – Fornece controle sobre elementos de superfície circulares. Quando a peça gira 360 graus, esta tolerância é aplicada independentemente em qualquer posição de medição do elemento circular e aplicada à tolerância de desvio circular construída em torno do eixo de referência, controlando a mudança acumulada na circularidade e na coaxialidade.
Quando aplicado a uma superfície construída verticalmente com o eixo de referência, controla elementos circulares de recursos de superfície plana.
Desastre total – Fornece controle composto sobre todos os elementos da superfície. Quando a peça gira 360 graus, esta tolerância é aplicada simultaneamente às operações circulares e alongadas. Quando aplicado a uma superfície construída em torno do eixo de referência, o desvio total controla a variabilidade acumulada de circularidade, cilindricidade, retilineidade, coaxialidade, ângulo, conicidade e perfil. Quando aplicado a uma superfície construída verticalmente com o eixo de referência, controla a variabilidade acumulada de perpendicularidade e retilineidade.
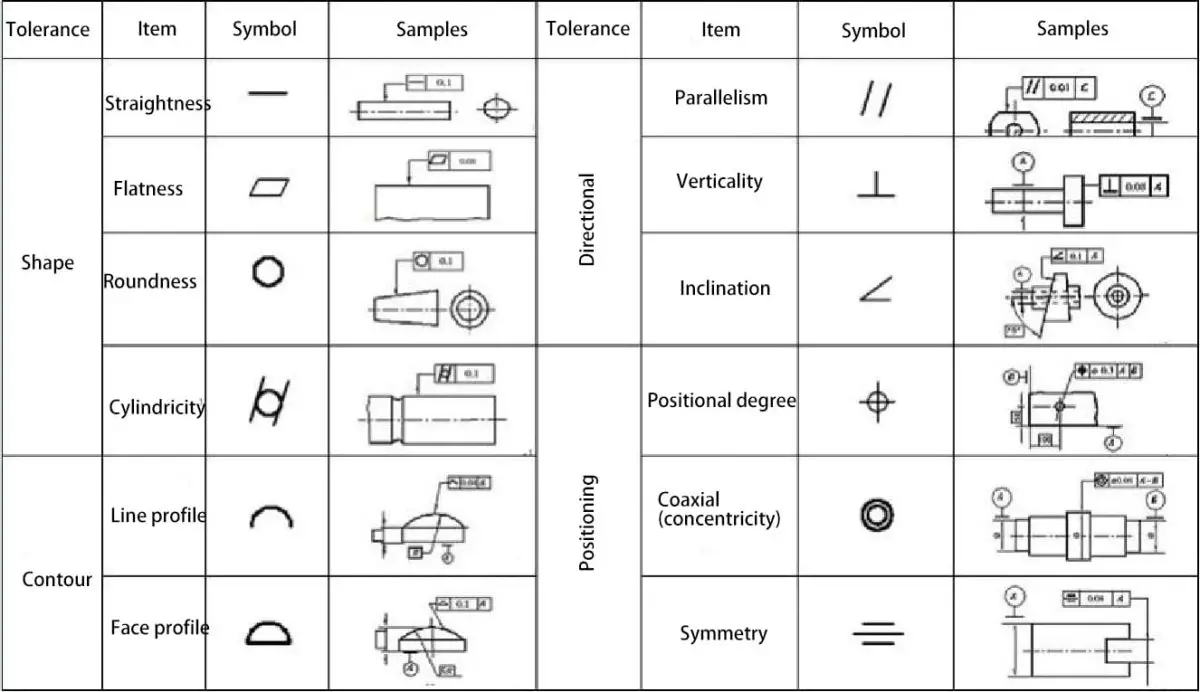
II. Terminologia Básica
Recurso – refere-se aos pontos, linhas e superfícies que constituem a geometria de um componente.
Característica ideal – uma característica com significado geométrico.
Recurso real – o recurso que realmente existe no componente, normalmente representado por um recurso medido.
Recurso de referência – um recurso usado para determinar a direção ou posição do recurso medido. Simplesmente referido como referência, serve como base para determinar a relação geométrica entre os recursos. Inclui pontos de referência, linhas de referência e superfícies de referência.
Recurso medido – o recurso que especifica a tolerância de forma ou posição.
Recurso central – pontos, linhas ou superfícies que possuem uma relação simétrica com o recurso.
Faixa de tolerância – restringe a variação da forma real ou dos recursos de posição. É uma região definida por um determinado valor máximo de erro, determinado pelo tamanho, forma, direção e posição.”
III. Classificação de tolerância
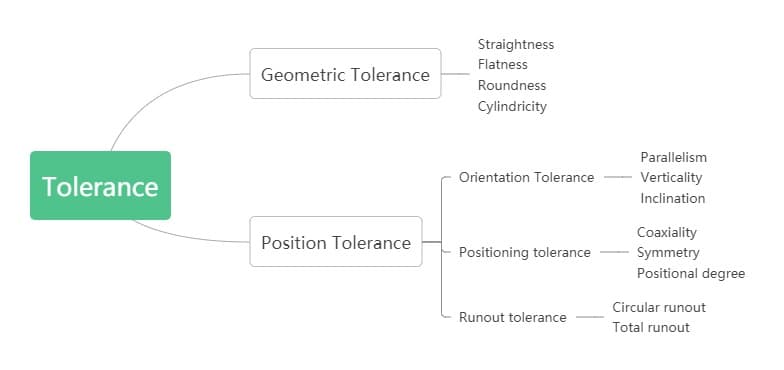
1. Retidão
A faixa de tolerância é a região entre duas linhas/planos/cilindros paralelos, etc. a uma distância do valor de tolerância t
Exemplo 1
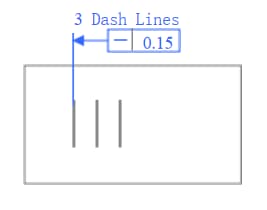
Cada linha gravada deve estar localizada entre duas linhas paralelas na superfície com um valor de tolerância de 0,015mm
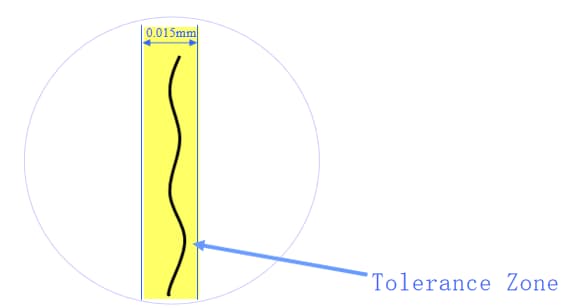
Exemplo 2
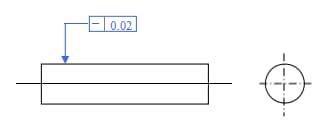
Qualquer linha de elemento na superfície cilíndrica deve estar localizada dentro do plano axial e entre duas linhas paralelas a uma distância de valor de tolerância de 0,02 mm.
Exemplo de aplicação
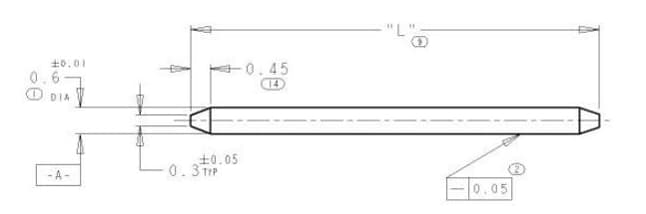
Exemplo 3
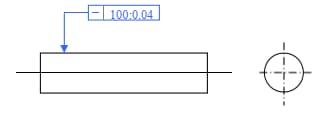
Qualquer linha de elemento na superfície cilíndrica deve estar localizada dentro do plano axial e entre duas linhas paralelas com um valor de tolerância de 0,04 mm dentro de qualquer 100 mm.
Exemplo 4
Discussão: Como devemos entender se diferentes tolerâncias de retilinidade são dadas em duas direções na mesma superfície?
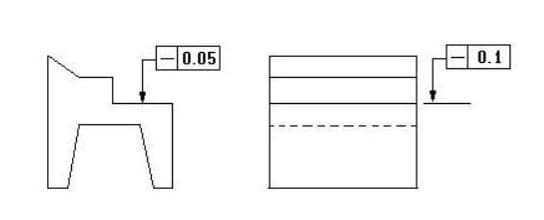
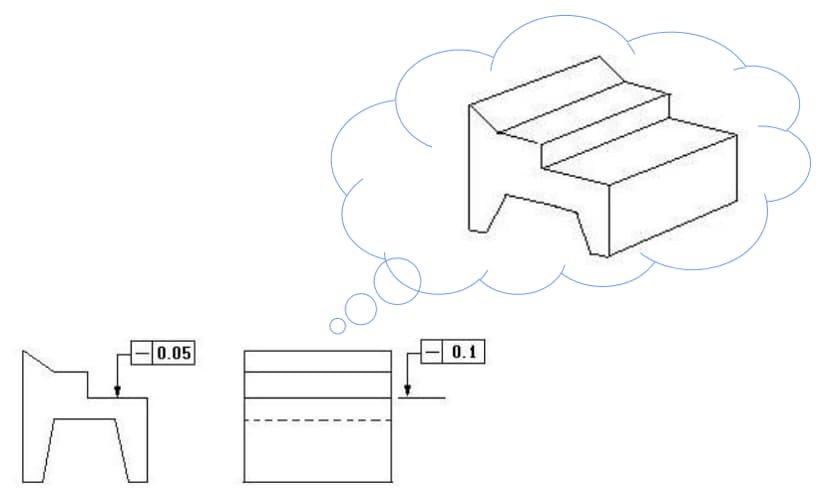
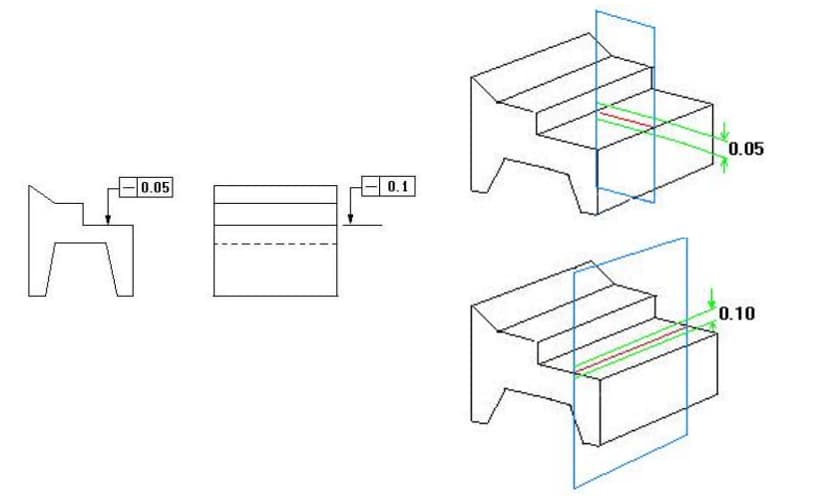
2. Planicidade
A banda de tolerância é a região entre dois planos paralelos a uma distância de valor de tolerância t.
Representa a forma real das características planas do componente, mantendo a condição plana ideal.
Exemplo 1
A superfície superior deve estar localizada dentro de dois planos paralelos com um valor de tolerância de 0,1 mm.
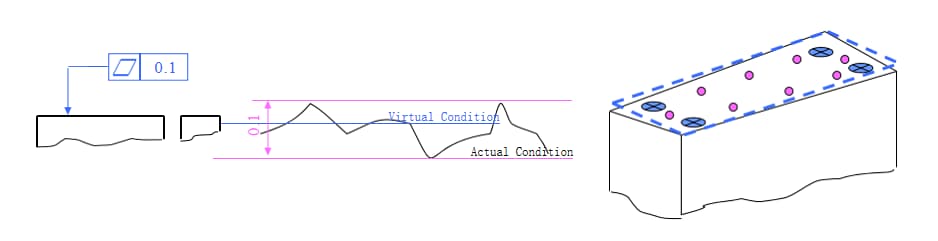
Exemplo 2
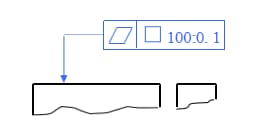
Qualquer faixa de 100×100 na superfície deve estar localizada dentro de dois planos paralelos com um valor de tolerância de 0,1 mm.
3. Redondeza
Representa a forma real do recurso circular no componente e seu centro mantendo uma distância igual.
A faixa de tolerância é a região entre dois círculos concêntricos com uma diferença de raio de valor de tolerância t na mesma seção transversal.
Exemplo 1
Em qualquer seção transversal perpendicular ao eixo, o círculo deve estar localizado entre dois círculos concêntricos com raio de tolerância de 0,02 mm.
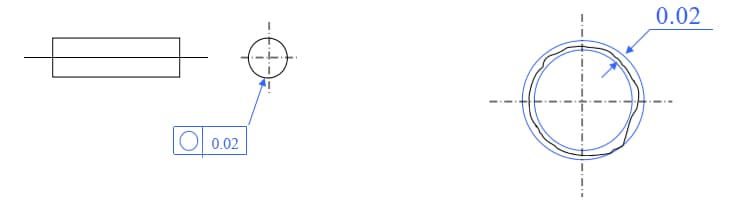
Exemplo 2
Em qualquer seção transversal perpendicular ao eixo, o círculo deve estar localizado entre dois círculos concêntricos com raio de tolerância de 0,02 mm.
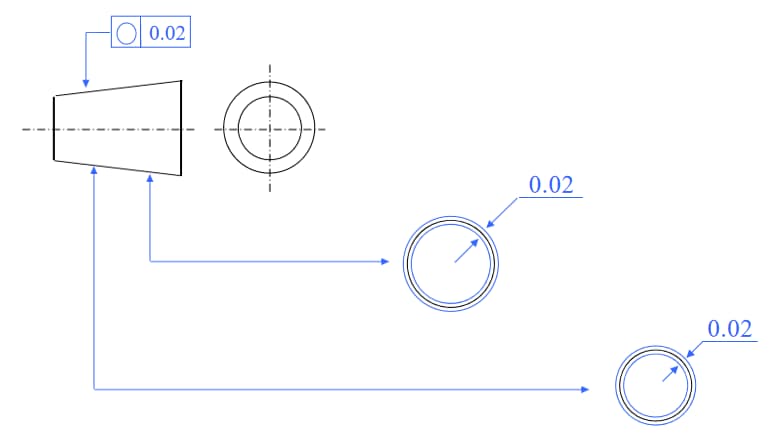
4. Cilindricidade
Representa a condição em que todos os pontos do contorno da superfície cilíndrica do componente mantêm distâncias iguais do seu eixo.
A faixa de tolerância é a região entre duas superfícies cilíndricas com uma diferença de raio de valor de tolerância t no mesmo eixo.
Exemplo 1
A superfície cilíndrica deve estar localizada entre duas superfícies cilíndricas com diferença de raio de valor de tolerância de 0,05mm no mesmo eixo.
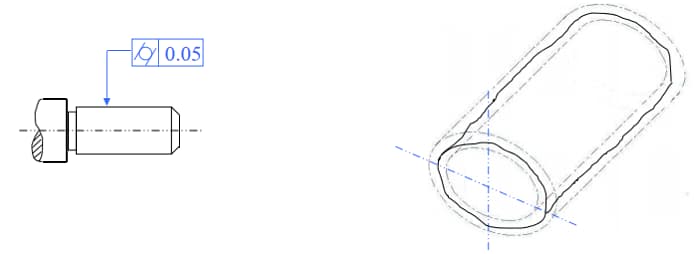
5. Paralelismo
Representa a condição em que o recurso real medido no componente mantém uma distância igual da referência.
Quando dada uma direção, a faixa de tolerância é a região entre dois planos paralelos a uma distância do valor de tolerância t e paralelo ao plano de referência (ou linha, eixo); quando dadas duas direções perpendiculares, é a região dentro de um prisma retangular com dimensões de valores de tolerância t1×t2 e paralela ao eixo de referência.
Exemplo 1
A superfície superior deve estar localizada entre dois planos paralelos a uma distância de tolerância de 0,05 mm e paralela ao plano de referência.
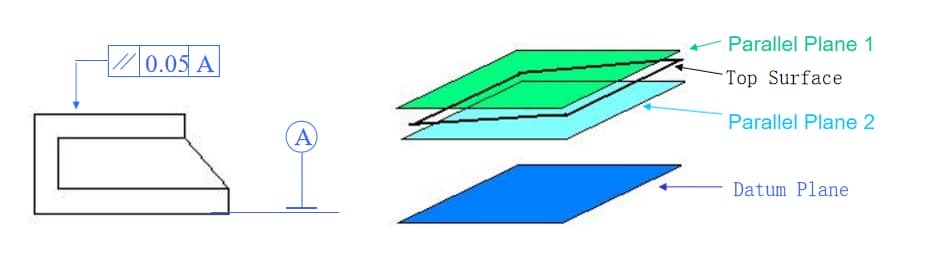
Exemplo 2
O eixo de ΦD deve estar localizado entre dois planos paralelos a uma distância de valor de tolerância 0,1 mm e verticalmente paralelo ao eixo de referência Φ.
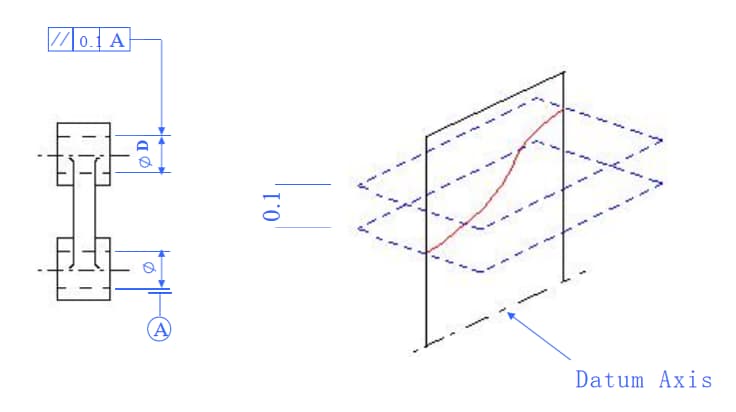
6. Verticalidade
A tolerância representa a condição em que o recurso real da peça é mantido em um ângulo correto de 90 graus em relação ao recurso de referência.
Quando dada uma direção, a zona de tolerância é a região entre dois planos (ou linhas) paralelos que são perpendiculares ao plano de referência (ou linha, eixo) e separados por uma distância igual ao valor de tolerância t.
Quando duas direções perpendiculares entre si são dadas, a zona de tolerância é a região dentro de um paralelepípedo com dimensões t1 × t2 que é perpendicular ao eixo de referência.
Exemplo 1
A superfície direita deve estar localizada entre dois planos paralelos perpendiculares ao plano de referência e ter um desvio de 0,05 mm.
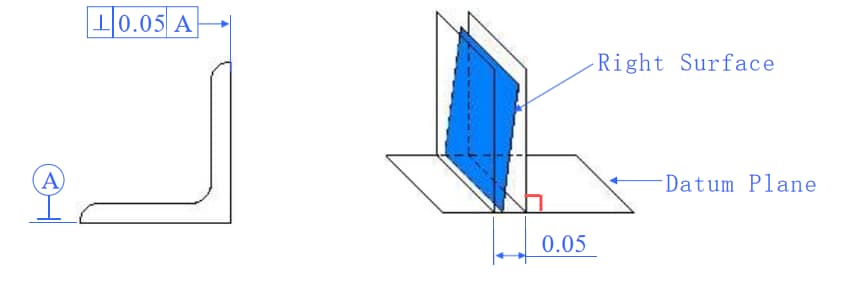
Exemplo 2
A superfície esquerda deve estar dentro de uma faixa de desvio de 0,05 mm e entre dois planos paralelos perpendiculares ao eixo de referência.
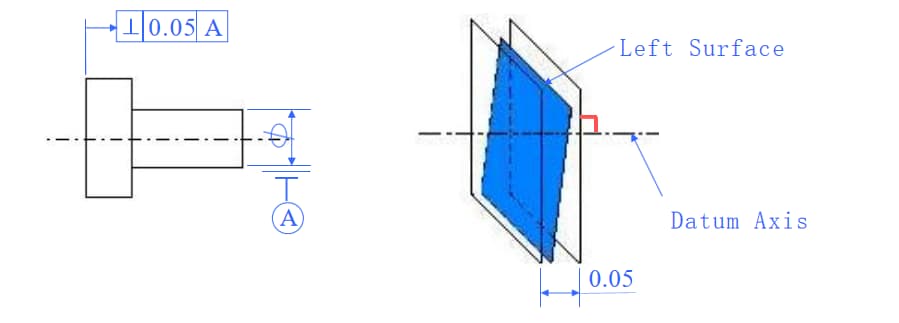
Exemplo 3
O eixo do cilindro d deve estar localizado dentro da superfície do cilindro perpendicular ao plano de referência com uma tolerância de diâmetro de 0,05 mm.
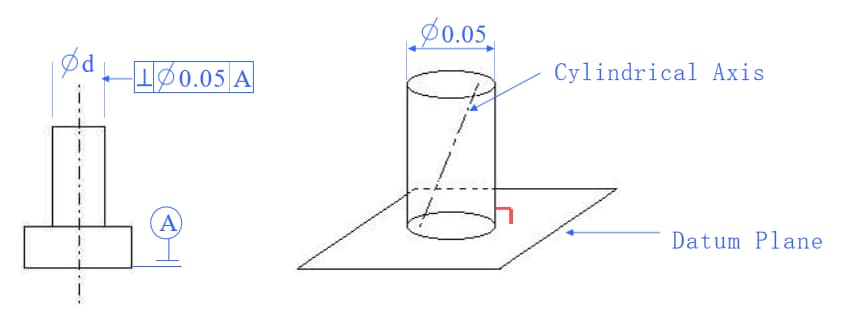
Exemplo 4
O eixo do furo circular E deve estar entre dois planos paralelos perpendiculares ao plano de referência Z, com valor de desvio de 0,06mm.
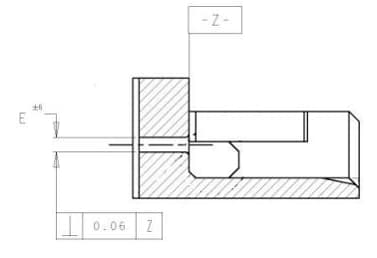
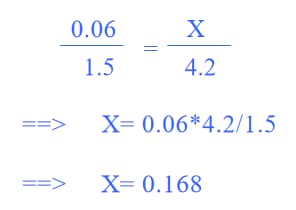
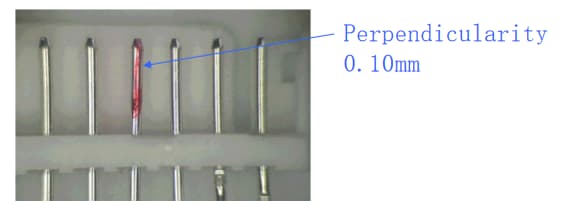
7. Grau de inclinação
Condição correta de dois elementos na peça mantendo um determinado ângulo entre suas direções relativas.
Dentro de uma direção especificada, a zona de tolerância é a área entre dois planos paralelos (ou linhas) que estão em um ângulo teórico correto em relação ao plano de referência (ou linha ou eixo) e a uma distância do valor de tolerância t dele.
Exemplo 1
A superfície inclinada deve estar localizada entre dois planos paralelos que formam um ângulo de 45 graus em relação ao plano de referência e a uma distância de 0,08 mm deste dentro da zona de tolerância.
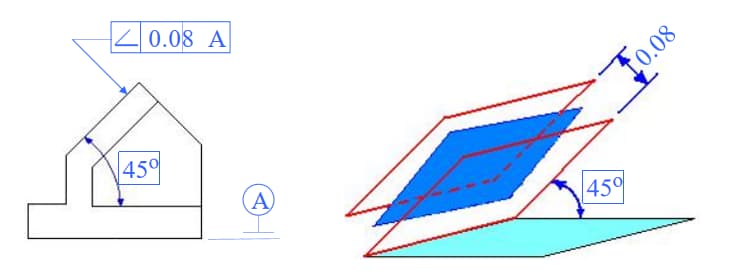
Exemplo 2
O eixo do recurso D deve estar localizado entre dois planos paralelos que formam um ângulo de 45 graus em relação ao eixo de referência e a uma distância de 0,1 mm dele dentro da zona de tolerância.
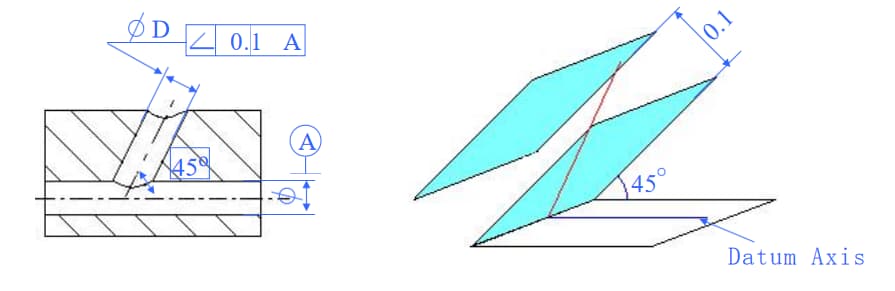
8. Concentricidade
Concentricidade é a condição em que o eixo que está sendo medido na peça mantém alinhamento com o eixo de referência ao longo da mesma linha reta.
A zona de tolerância é a área dentro de um cilindro que tem um diâmetro com o valor de tolerância t e é coaxial com o eixo de referência.
Exemplo 1
O eixo do recurso D deve estar localizado dentro de um cilindro que tenha um diâmetro de 0,1 mm e seja coaxial com o eixo de referência D dentro da zona de tolerância.

9. Simetria
Simetria é a condição em que dois pares de recursos simétricos na peça estão alinhados no mesmo plano.
A zona de tolerância é a área entre dois planos (ou linhas) paralelos que estão a uma distância do valor de tolerância t do plano central de referência (ou linha central ou eixo) e dispostos simetricamente em relação a ele.
Se forem especificadas duas direções perpendiculares entre si, a zona de tolerância é a região dentro de um prisma de quatro lados cuja seção transversal é igual aos valores de tolerância t1 x t2.
Exemplo 1
O plano central da ranhura deve estar localizado entre dois planos paralelos dispostos simetricamente em relação ao plano central de referência e a uma distância de 0,1 mm deste dentro da zona de tolerância.
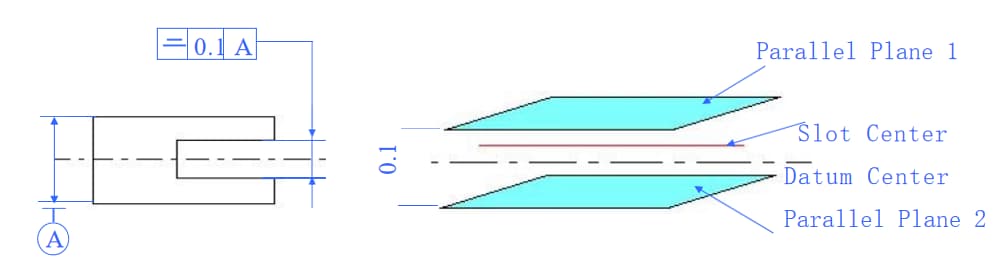
Exemplo:
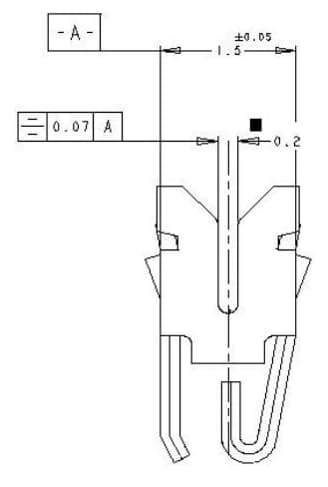
(1) O centro do terminal deve ser endireitado.
(2) O desvio máximo de um lado do centro da ranhura não pode exceder 0,035 mm.
Pergunta?
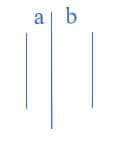
(1) Como é calculado o deslocamento T?
T=(ba)/2
(2) Qual é a tolerância de simetria?
10. Tolerância posicional.
A tolerância posicional refere-se à precisão de pontos, linhas, superfícies e outros elementos de uma peça em relação às suas localizações ideais.
Zona de tolerância:
(1) Tolerância posicional do ponto: A zona de tolerância é a área dentro de um círculo ou esfera com diâmetro do valor de tolerância t, centrada na posição ideal do ponto.
(2) Tolerância posicional da linha: Quando uma direção é dada, a zona de tolerância é a área entre dois planos (ou linhas) paralelos que estão dispostos simetricamente em torno da posição ideal da linha e a uma distância do valor de tolerância t. Se forem dadas duas direções perpendiculares, a zona de tolerância é a área dentro de um prisma de quatro lados com uma seção transversal de tamanho t1 X t2 e a linha do eixo do prisma coincide com a posição ideal da linha.
(3) Tolerância posicional da superfície: A zona de tolerância é a área entre dois planos paralelos que estão dispostos simetricamente em torno da posição ideal da superfície e a uma distância do valor de tolerância t.
Exemplo 1
O ponto deve estar localizado dentro de um círculo com diâmetro de tolerância de 0,3 mm, e o centro do círculo deve estar na posição ideal dos pontos determinados pelos dados relativos A e B.
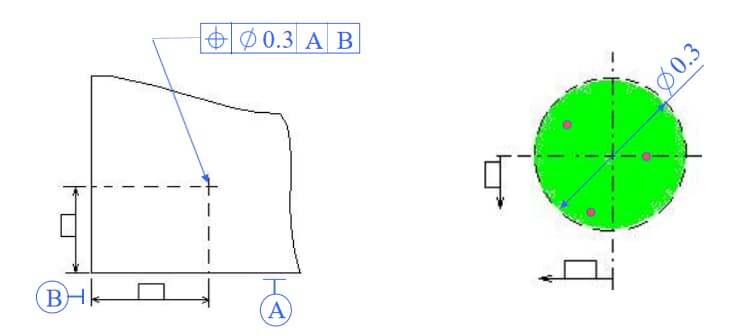
Sistema de três planos de referência:
Três planos de referência mutuamente perpendiculares A, B e C constituem um sistema de planos de referência, comumente conhecido como sistema de três planos de referência. É o ponto de partida para determinar as relações geométricas de vários elementos nas peças.
No sistema de três planos de referência, os planos de referência são ordenados por suas funções.
O mais importante é o primeiro plano de referência (A), seguido pelo segundo (B) e terceiro (C) planos de referência.
Exemplo 2
O eixo do furo deve estar localizado dentro de uma superfície cilíndrica com diâmetro de tolerância de 0,1 mm, e a linha do eixo da superfície do cilindro deve coincidir com a posição ideal dos pontos nos dados relativos A, B e C.
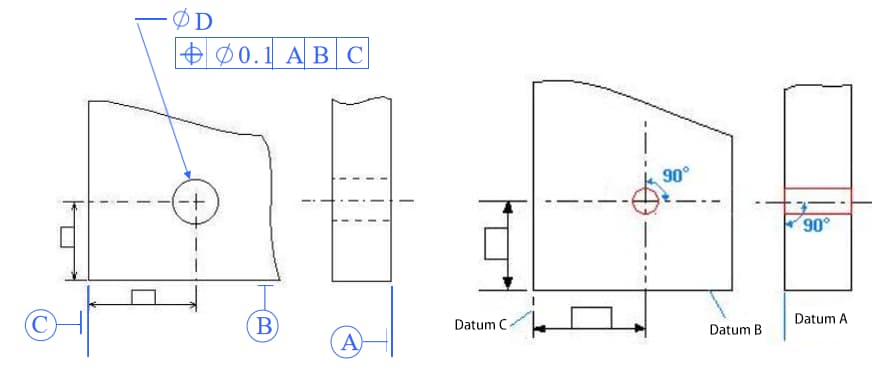
Exemplo 3
Tolerância posicional composta.
Moldura geométrica:
É um gráfico que mostra a relação geométrica correta entre um conjunto de linhas de eixos ideais ou entre elas e o ponto de referência.
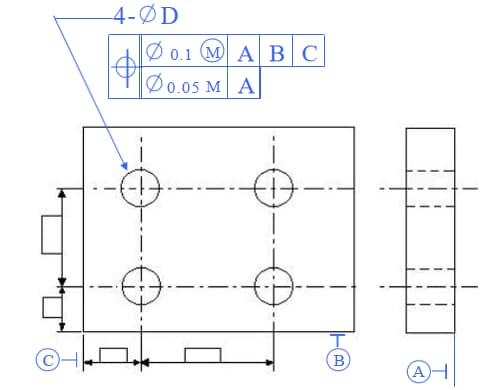
O eixo dos quatro furos D deve estar localizado dentro da seção sobreposta de duas zonas de tolerância cilíndricas, uma com valor de tolerância de diâmetro de 0,1 mm e outra com valor de tolerância de diâmetro de 0,05 mm. A moldura geométrica das quatro zonas de tolerância posicional de 0,1 mm é determinada em relação aos dados A, B e C. A moldura geométrica das quatro zonas de tolerância posicional de 0,05 mm é orientada apenas em relação ao ponto de referência A.
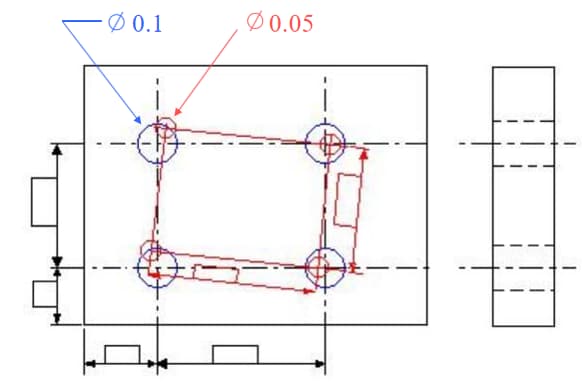
Os eixos dos quatro furos D devem estar localizados dentro da seção sobreposta de duas zonas de tolerância cilíndricas, uma com valor de tolerância de diâmetro de 0,1 mm e outra com valor de tolerância de diâmetro de 0,05 mm. A moldura geométrica das quatro zonas de tolerância posicional de 0,1 mm é determinada em relação aos dados A, B e C. A moldura geométrica das quatro zonas de tolerância posicional de 0,05 mm é orientada apenas em relação ao ponto de referência A.
Consideração: Comparar os dois tipos de precisão posicional a seguir.

11. Desvio circular
Refere-se à condição em que a superfície rotativa da peça é limitada dentro da superfície de medição e mantém sua posição especificada em relação ao eixo de referência.
(1) Excentricidade radial.
A zona de tolerância é a área entre dois círculos concêntricos com seus centros no eixo de referência, onde a diferença de raio em qualquer plano de medição perpendicular ao eixo de referência é o valor de tolerância t.
(2) Excentricidade da face final.
A zona de tolerância é a área da superfície cilíndrica ao longo da direção da geratriz com largura t no cilindro de medição em qualquer posição de diâmetro coaxial com o eixo de referência.
Exemplo 1
Excentricidade radial.
Quando a superfície cilíndrica gira em torno do eixo de referência sem qualquer movimento axial, o desvio radial em qualquer plano de medição não deve exceder o valor de tolerância de 0,05 mm.

A zona de tolerância é a área entre dois círculos concêntricos com seus centros no eixo de referência, onde a diferença de raio em qualquer plano de medição perpendicular ao eixo de referência é o valor de tolerância t.
Exemplo 2
Fim do desvio da face.
Quando a peça gira em torno do eixo de referência sem qualquer movimento axial, o desvio axial em qualquer diâmetro de medição na face final esquerda não deve exceder o valor de tolerância de 0,05 mm.
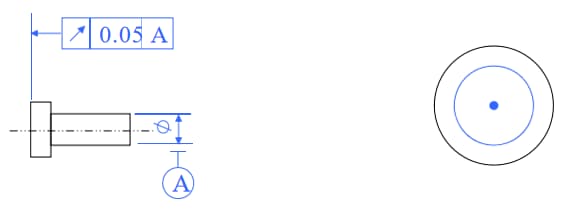
A zona de tolerância é a área da superfície cilíndrica ao longo da direção da geratriz com largura t no cilindro de medição em qualquer posição de diâmetro coaxial com o eixo de referência.
12. Desaparecimento total.
Refere-se ao desvio uniforme ao longo de toda a superfície medida da peça quando ela gira continuamente em torno do eixo de referência
(1) Excentricidade total radial.
A zona de tolerância é a área entre dois cilindros coaxiais com o eixo de referência e tendo uma diferença de raio do valor de tolerância t
(2) Excentricidade total da face final.
A zona de tolerância é a área entre dois planos paralelos perpendiculares ao eixo de referência e com uma distância do valor de tolerância t.
Exemplo 1
Excentricidade total radial.
Quando a superfície gira continuamente em torno do eixo de referência sem qualquer movimento axial, enquanto o indicador se move linearmente paralelo ao eixo de referência, o desvio ao longo de toda a superfície não deve exceder o valor de tolerância de 0,02 mm.
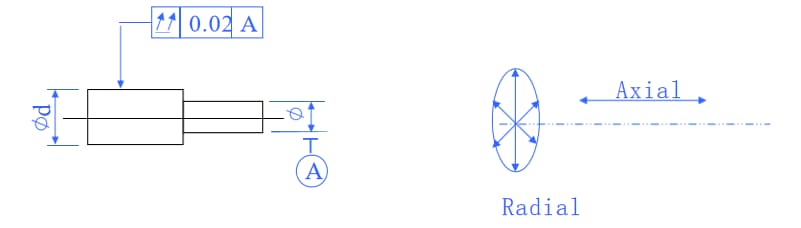
A zona de tolerância é a área entre dois cilindros coaxiais com o eixo de referência e tendo uma diferença de raio do valor de tolerância t.
Exemplo 2
Excentricidade total da face final.
Quando a face final gira continuamente em torno do eixo de referência sem qualquer movimento axial, enquanto o indicador se move linearmente perpendicular ao eixo de referência, o desvio ao longo de toda a face final não deve exceder o valor de tolerância de 0,05 mm.
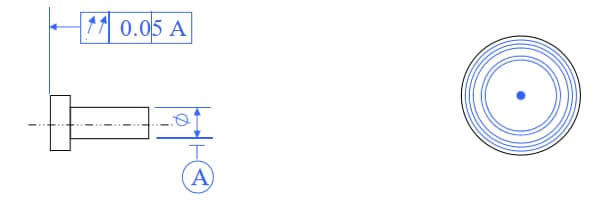
A zona de tolerância é a área entre dois planos paralelos perpendiculares ao eixo de referência e com uma distância do valor de tolerância t.