A soldabilidade refere-se à capacidade de um material ser soldado em componentes que atendam aos requisitos de projeto especificados sob condições de construção definidas e que satisfaçam os requisitos de serviço predeterminados.
A soldabilidade é influenciada por quatro fatores: material, método de soldagem, tipo de componente e requisitos de uso.
EU. Liga Ferro-Carbono
1. Visão geral
A liga Ferro-Carbono é uma liga binária composta de ferro e carbono. É o tipo de material à base de ferro mais utilizado. O aço carbono e o ferro fundido são materiais da liga ferro-carbono. Ligas com menos de 0,0218% de carbono são conhecidas como ferro puro industrial. Ligas de ferro-carbono com menos de 2,11% de carbono são chamadas de aço.
Ligas com mais de 2,11% de carbono são conhecidas como ferro fundido. Além do carbono, o aço carbono e o ferro fundido contêm impurezas como silício, manganês, enxofre, fósforo, nitrogênio, hidrogênio e oxigênio; essas impurezas podem afetar as propriedades do aço.
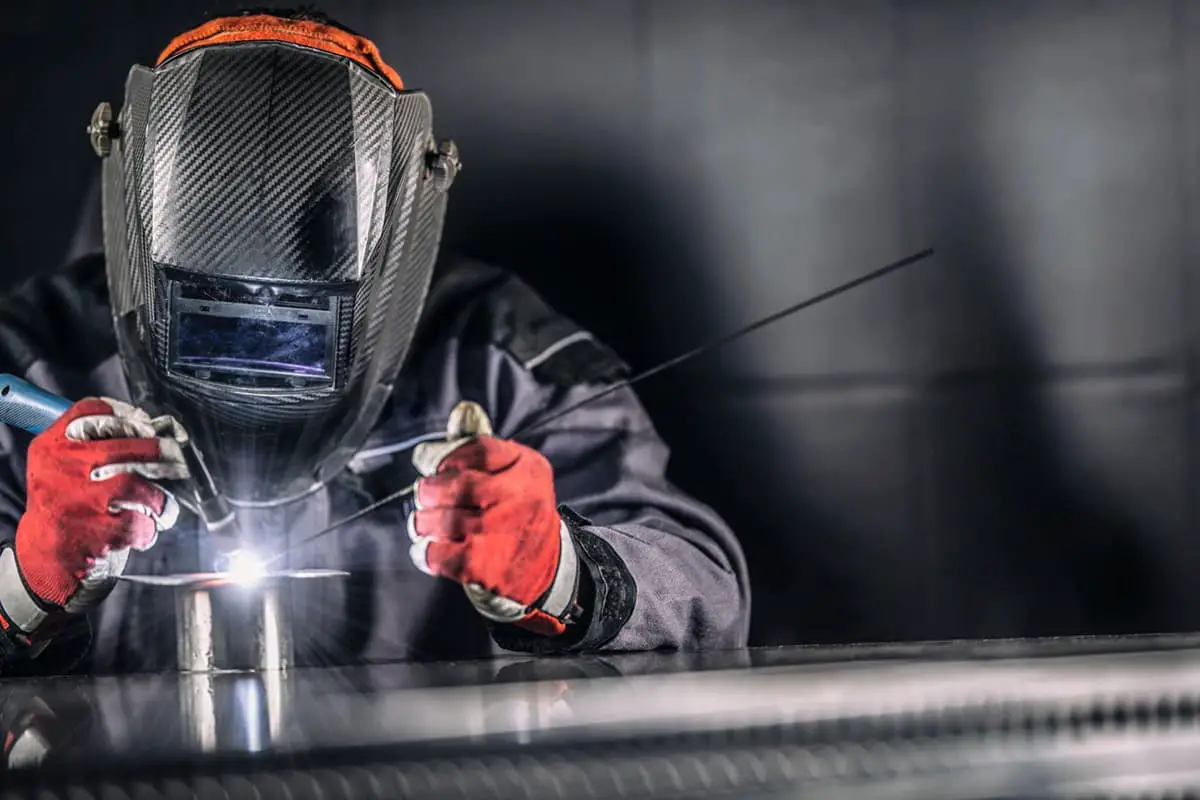
Tabela 2-1: Soldabilidade de Vários Tipos de Aço Carbono
Nome | Conteúdo de carbono | Dureza Típica | Usos típicos | Soldabilidade |
Aço de baixo carbono | ≤0,15% | HRB | Chapas especiais e chapas finas perfiladas, tiras e fios de solda | Excelente |
0,15%~0,25% | 30-35HRB | Perfis estruturais, placas e barras | Bom | |
Aço Médio Carbono | 0,25%~0,60% | 42-46HRC | Peças mecânicas e ferramentas | Médio (normalmente requer pré-aquecimento, método de soldagem com baixo teor de hidrogênio recomendado) |
Aço de alto carbono | >0,60%-1,00 | 55HRC | Molas, moldes | Fraco (requer método de soldagem com baixo teor de hidrogênio, pré-aquecimento e pós-aquecimento) |
Embora a resistência do aço carbono seja relativamente baixa, ele é fácil de fundir, tem excelente processabilidade e é barato. Possui forjabilidade, soldabilidade e desempenho de corte superiores. O aço carbono é normalmente fornecido ao mercado em diversos formatos e tamanhos, como aço redondo, aço quadrado, aço para viga I e vergalhão.
O aço de baixo carbono, com teor de carbono tão baixo quanto 0,25% ou menos, e teor mínimo de M e Si, tem baixa tendência de endurecimento, tornando-o o tipo de aço mais soldável. Além de C, M e Si, impurezas como S, P, O, N no aço carbono podem afetar suas propriedades mecânicas, trincas a frio de juntas soldadas, trincas a quente e sensibilidade à fragilidade por envelhecimento. As propriedades mecânicas do aço comum de baixo carbono são mostradas na Tabela 2-2.
Tabela 2-2 Propriedades Mecânicas do Aço de Baixo Carbono
Nota | Nível | Teste de tração (não inferior) | Teste de impacto | Teste de flexão a frio 180°, B=2a |
||||
Ponto de rendimento /MPa |
Resistência à tracção /MPa |
Taxa de alongamento | Temperatura /℃ |
Energia de absorção de impacto Charpy V-Notch (longitudinal) /J≥ | ||||
Diâmetro do núcleo de flexão d |
||||||||
Espécime Longitudinal | Espécime Transversal | |||||||
Q195 | – | 195 | 315-430 | 33 | – | – | 0 | 0,5a |
Q215 | A | 215 | 335-410 | 31 | – | – | 0,5a | a |
B | 20 | 27 | ||||||
Q235 | A | 235 | 370-500 | 26 | – | – | a | 1.5a |
B | 20 | 27 | ||||||
– | 0 | |||||||
D | -20 | |||||||
Q275 | A | 275 | 410-540 | 22 | – | – | 1.5a | 2a |
B | 20 | 27 | ||||||
C | 0 | |||||||
D | -20 | |||||||
Q245R | – | 245 | 400-520 | 25 | 0 | 31 | 1.5a | |
(20g,20R) |
Formulários:
- Q195, Q215 e Q235 apresentam boa plasticidade e podem ser laminados em placas de aço, vergalhões, tubos de aço e muito mais.
- Q255 e Q275 podem ser laminados em aço estrutural, placas de aço, etc.
Geralmente, nenhum tratamento térmico é realizado após a formação. A maioria deles é usada diretamente no estado laminado a quente.
2. Soldabilidade do Aço Carbono
O aço carbono e o aço de baixa liga são categorizados com base em suas composições químicas em três grupos: aço carbono, aço de baixa liga e aço-liga, sendo o aço carbono (comumente referido como aço carbono) o mais amplamente utilizado.
Além do carbono, que é o principal elemento de liga do aço carbono, há também o silício (Si<0,5%), o manganês (Mn<0,8%) e impurezas inevitáveis, como enxofre e fósforo.
O aço de baixa liga é derivado do aço carbono e um ou mais elementos de liga são adicionados intencionalmente para obter certas propriedades. Por exemplo, aço 16Mn.
Classificação e uso de liga de aço:
- Liga de aço estrutural
- Liga de aço para ferramentas
- Aço de Desempenho Especial
Conteúdo total do elemento de liga:
- Aço de baixa liga: <5%
- Aço de liga média: 5% – 10%
- Aço de alta liga: >10%
1. Análise de soldabilidade de aço de baixo carbono
A soldabilidade do aço carbono deteriora-se com o aumento do teor de carbono. Ao selecionar materiais de soldagem, eles não apenas devem corresponder ao material original em composição e propriedades, mas também devem ser evitados elementos nocivos como enxofre e fósforo no metal de solda.
Ao soldar aço carbono com teor de carbono superior a 0,25%, a fonte de hidrogênio deve ser minimizada.
As razões mecânicas para trincas durante a soldagem de aço carbono são tensões de restrição estrutural e tensões térmicas irregulares. Diferentes medidas tecnológicas deverão ser tomadas dependendo do teor de carbono.
Para aço de baixo carbono, atenção especial deve ser dada para evitar trincas causadas por tensões de restrição estrutural e tensões térmicas irregulares. Além de prevenir trincas causadas por essas tensões, o aço com alto teor de carbono deve evitar principalmente trincas causadas pelo endurecimento.
A soldabilidade do aço carbono depende principalmente de sua suscetibilidade a trincas a frio, trincas a quente e da tenacidade da junta. O teor de carbono do aço e do metal depositado tem o impacto mais significativo na fissuração a frio do aço carbono.
Carbono Equivalente: CE=C+Mn/6+Si/24
Para o aço carbono, o teor de silício é relativamente baixo, não ultrapassando 0,5%. Às vezes, seu impacto pode ser ignorado. À medida que o valor do Carbono Equivalente (CE) aumenta, a propensão para trincas a frio aumenta e a soldabilidade se deteriora. Normalmente, quando o valor CE excede 0,40%, a sensibilidade à fissuração a frio aumenta.
A tendência para o endurecimento da soldadura e das zonas afectadas pelo calor, e a sua susceptibilidade à fissuração a frio, não estão apenas relacionadas com a composição, mas o impacto da estrutura no desempenho é ainda mais significativo. Dada uma determinada composição, a estrutura depende da taxa de resfriamento, que pode ser determinada através de sua estrutura SHCCT (Simulated Heat Affected Zone Continuous Cooling Transformation). A Figura 2-2 apresenta o diagrama SHCCT do aço Q235 (A3).
O controle da taxa de resfriamento da área de soldagem é um método crucial para alterar o tipo de estrutura e a dureza da zona de soldagem, reduzindo assim a ocorrência de trincas a frio.
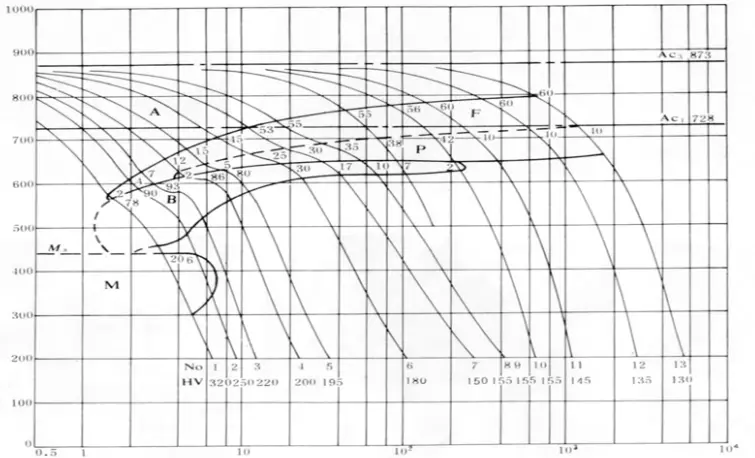
À medida que a espessura da soldagem aumenta, ou quando a temperatura ambiente é mais baixa durante a soldagem, ou a energia do fio de soldagem é menor, a dissipação de calor acelera e a velocidade de resfriamento da junta soldada aumenta, o que por sua vez aumenta a tendência de rachaduras a frio.
As juntas em T e as juntas sobrepostas têm uma área de dissipação de calor maior em comparação com as juntas de topo, acelerando assim a taxa de resfriamento na zona de soldagem e tornando-a propensa à formação de estruturas endurecidas.
O pré-aquecimento, o aumento da temperatura entre as trilhas ou camadas de soldagem ou as medidas de pós-aquecimento também podem reduzir a velocidade de resfriamento durante a soldagem.
O endurecimento do aço carbono se deve principalmente à formação de estruturas martensíticas. A martensita é uma solução supersaturada de carbono em α-Fε, e sua dureza está relacionada tanto ao teor de carbono no aço quanto à quantidade de martensita formada. A quantidade de martensita é influenciada pela taxa de resfriamento; uma velocidade de resfriamento muito rápida pode produzir 100% de martensita, alcançando assim a maior dureza.
Hidrogênio e Grau de Restrição
O hidrogênio na área de soldagem provém principalmente dos materiais de soldagem e da umidade na zona de soldagem. O hidrogênio dissolvido na solda pode ser reduzido usando materiais de soldagem com baixo teor de hidrogênio, aumentando a temperatura de secagem dos materiais de soldagem, reduzindo o teor de umidade no gás de proteção ou diminuindo a umidade na área de soldagem.
Um aumento na espessura da chapa de aço ou na rigidez da estrutura aumentará o grau de restrição, aumentando assim a sensibilidade à fissuração induzida pelo hidrogénio.
Os três principais indutores da sensibilidade à trinca a frio são a estrutura endurecida, o hidrogênio e a tensão de restrição. Quando a composição do aço é fixa, quanto maior a proporção da estrutura endurecida, menor o teor crítico de hidrogênio necessário para causar trincas a frio e menor a tensão de restrição necessária, aumentando assim a tendência para trincas a frio.
Quando a estrutura e o teor de hidrogénio são fixos, quanto maior for o grau de restrição, maior será a sensibilidade à fissuração a frio. Portanto, na tendência do aço carbono à trinca a frio, os três fatores de estrutura endurecida, hidrogênio e tensão de restrição promovem-se mutuamente e são interdependentes.
Rachadura Quente
A suscetibilidade à trinca a quente está intimamente relacionada a impurezas como enxofre (S) e fósforo (P) no aço. Durante a soldagem de aço carbono com alto teor de S e P, os compostos S e P de baixo ponto de fusão acumularam-se nos contornos dos grãos na zona afetada pelo calor, causando trincas de liquidação perto da linha de fusão da zona afetada pelo calor.
Para chapas de aço mais espessas, os sulfetos distribuídos ao longo de diferentes zonas de segregação podem levar a trincas laminares em juntas em T e outras. Quando a taxa de diluição do material de base é alta, mais S e P entram na costura de solda, o que pode facilmente causar rachaduras a quente na costura de solda.
Para evitar isso, o projeto da junta ou operação do processo deve evitar que a costura de solda tenha um formato estreito e profundo. Os cordões de solda a arco de aço de baixo carbono geralmente apresentam maior resistência à trinca a quente.
Rasgo Laminar
O aço em ebulição possui maior teor de oxigênio e uma faixa de segregação perceptível no centro da espessura da placa, o que pode causar rachaduras e porosidade durante a soldagem. Há uma certa tendência ao rompimento laminar na soldagem de chapas grossas e também apresenta um alto grau de sensibilidade ao envelhecimento. A temperatura de transição frágil da junta soldada também está no lado mais alto.
Portanto, o aço em ebulição normalmente não é usado na fabricação de estruturas sujeitas a cargas dinâmicas ou que operam em baixas temperaturas.
Mudanças no desempenho da zona afetada pelo calor durante a soldagem
A principal alteração está na ductilidade da junta, que depende da composição do aço, do estado do tratamento térmico do material base antes da soldagem e do processo térmico de soldagem. O aço carbono é entregue principalmente em estado laminado a quente, mas para alguns aços estruturais de carbono de alta qualidade e aços estruturais de carbono para fins especiais, o estado de entrega também pode ser laminação controlada, normalização, normalização + revenido ou têmpera + revenido.
Durante o processo de resfriamento do aço, uma grande deformação é aplicada a uma temperatura mais baixa antes que a austenita se decomponha, o que aumenta a taxa de nucleação da fase ferrita. Os grãos resultantes são significativamente refinados, melhorando assim drasticamente a sua resistência e ductilidade.
Certos métodos de soldagem possuem fontes de calor dispersas ou energia linear excessivamente alta, como soldagem a gás e soldagem por eletroescória. Esses métodos fazem com que os grãos na zona de grãos grossos da área afetada pelo calor da solda se tornem ainda maiores, reduzindo assim a resistência ao impacto da junta. Consequentemente, o tratamento térmico pós-soldagem é frequentemente necessário para estruturas significativas.
Concluindo, o aço com baixo teor de carbono possui baixo teor de carbono e muito baixo teor de elementos de liga. Portanto, utilizando métodos convencionais de soldagem, não haverá estruturas endurecidas ou trincas a frio nas juntas. Contanto que os materiais de soldagem sejam selecionados corretamente, juntas de soldagem satisfatórias podem ser alcançadas.
2. Métodos de soldagem
Não há requisitos específicos para a escolha de um método de soldagem para aço de baixo carbono. A seleção pode ser feita com base em variáveis como espessura do material, estrutura do produto, requisitos de desempenho e condições de produção.
Soldagem por arco metálico blindado, CO2 soldagem com proteção de gás e soldagem por arco submerso são métodos de soldagem comuns.
3. Análise de soldabilidade de aço médio carbono
Rachadura a frio
O aço de médio carbono tem um equivalente de carbono mais alto do que o aço de baixo carbono. Quando o teor de carbono excede 0,25%, a temperabilidade do aço aumenta. Durante a soldagem, se a velocidade de resfriamento for rápida (como mostrado no diagrama CCT do aço 45 na Figura 2-3, a velocidade de resfriamento excede o ponto de valor crítico c), uma estrutura martensítica se formará na zona afetada pelo calor.
A estrutura martensítica do aço de médio carbono é mais frágil e, sob a ação das tensões de soldagem, está sujeita a trincas a frio e fraturas frágeis. A zona afetada pelo calor do aço de médio carbono tem maior probabilidade de formar uma estrutura martensítica endurecida após a soldagem. Esta estrutura é mais sensível ao hidrogênio e a tensão crítica necessária para o craqueamento a frio é menor.
Portanto, é aconselhável usar eletrodos com baixo teor de hidrogênio e aumentar adequadamente a temperatura de pré-aquecimento para reduzir a tensão residual.
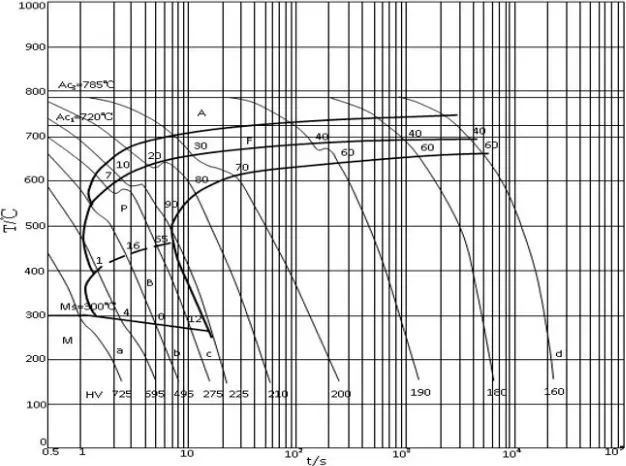
Rachaduras Quentes
Quando a fração mássica de carbono no aço excede 0,25%, a segregação do próprio carbono e sua promoção de outros elementos como enxofre (S) e fósforo (P) tornam-se significativamente proeminentes. Este é especialmente o caso quando o teor de S e P no material original é controlado próximo do limite superior do valor qualificado exigido pela norma. Sulfetos de baixo ponto de fusão podem levar a uma tendência aumentada para trincas a quente, particularmente no poço de arco.
Portanto, na soldagem de aço carbono, o controle rigoroso da fração mássica de enxofre é imprescindível.
Poros
Devido ao maior teor de carbono em comparação com o aço de baixo carbono, a quantidade de carbono que entra na poça de fusão aumenta. Isto poderia potencialmente levar à formação de poros de CO durante as reações metalúrgicas de soldagem, aumentando assim a sensibilidade à formação de poros na costura de solda.
Ao soldar aço em ebulição, é crucial garantir que o material de soldagem escolhido contenha desoxidantes adequados para evitar a formação de poros na costura de solda.
Mudanças no desempenho da zona afetada pelo calor na soldagem
A zona afetada pelo calor na soldagem sofre alterações devido ao surgimento de estruturas endurecidas, resultando em aumento de resistência, fragilidade e endurecimento, bem como maior suscetibilidade a trincas a frio. O carbono do metal original fundido entra na poça de fusão, levando a um aumento no teor de carbono do metal de solda. O desempenho varia entre os caminhos de solda devido às diferenças nas taxas de diluição.
À medida que o teor de carbono no aço de médio carbono aumenta, a sua soldabilidade deteriora-se. Os principais problemas encontrados durante a soldagem são trincas a quente, trincas a frio, porosidade e fratura frágil, e às vezes há uma diminuição na resistência na zona afetada pelo calor. Quanto mais impurezas no aço e maior a rigidez estrutural, mais graves se tornam estes problemas.
Quando trabalhos de reparo de soldagem são realizados em peças fundidas de aço de médio carbono, devem ser tomadas precauções para evitar trincas a frio durante a soldagem ou trincas devido a tensão residual excessiva na área reparada.
4. Métodos de soldagem
Normalmente, são empregados métodos de soldagem com eletrodo revestido ou soldagem com proteção de gás CO2. Ao adicionar superfícies resistentes ao desgaste ou à corrosão em aço de médio carbono, ou ao reparar superfícies desgastadas maiores em aço de médio carbono, a soldagem por arco submerso também pode ser utilizada.
5. Análise de soldabilidade de aço de alto carbono
Fraca soldabilidade
O aço de alto carbono, que inclui aço carbono estrutural, peças fundidas de aço carbono e aço carbono para ferramentas, contém mais de 0,6% de carbono. A soldabilidade desses materiais é bastante baixa e a soldagem pode resultar em martensita dura e quebradiça com alto teor de carbono. Eles têm uma alta tendência a endurecer e rachar. Dada a sua fraca soldabilidade e elevada dureza, estes tipos de aço são normalmente utilizados em componentes ou peças que requerem elevada dureza e resistência ao desgaste, em vez de na criação de estruturas soldadas.
Métodos de soldagem: Soldagem a arco de metal blindado e soldagem a gás são comumente usadas para soldagem de reparo.
II. Aço inoxidável
1. Visão Geral
O aço inoxidável refere-se a um tipo de aço que não enferruja facilmente na atmosfera; é um aço mais resistente à corrosão em condições específicas de ácido, alcalino e salino. Devido à sua excelente resistência à corrosão, conformabilidade e tenacidade em uma ampla faixa de temperatura, o aço inoxidável é amplamente utilizado em petroquímica, energia nuclear, indústria leve, têxteis, alimentos e eletrodomésticos.
1. Classificação do Aço Inoxidável
(1) Aço Inoxidável Austenítico
O aço inoxidável austenítico se distingue por suas propriedades não magnéticas, bom desempenho em baixas temperaturas, conformabilidade e soldabilidade.
(2) Aço Inoxidável Ferrítico
O aço inoxidável ferrítico é caracterizado por forte magnetismo, fácil conformabilidade, resistência à ferrugem e resistência à corrosão.
(3) Aço Inoxidável Martensítico
O aço inoxidável martensítico é conhecido por sua alta resistência e dureza, embora sua resistência à corrosão seja ligeiramente inferior à do aço inoxidável austenítico e ferrítico.
(4) Aço Inoxidável Duplex
O aço inoxidável duplex apresenta alto limite de escoamento, resistência à corrosão por pite e sob tensão e é fácil de formar e soldar.
(5) Aço inoxidável com endurecimento por precipitação
O aço inoxidável endurecido por precipitação tem um teor de cromo de cerca de 17% e, juntamente com elementos como níquel e molibdênio, não apenas possui propriedades inoxidáveis suficientes, mas também exibe resistência à corrosão comparável ao aço inoxidável austenítico.
2. Papel dos elementos de liga
Ferro: É o elemento metálico básico do aço inoxidável.
Cromo: É o principal elemento formador de ferrita. Quando combinado com o oxigênio, o cromo forma uma película passiva de Cr2O3 resistente à corrosão, tornando-o o elemento essencial para manter a resistência à corrosão do aço inoxidável.
Carbono: É um forte elemento formador de austenita que pode aumentar notavelmente a resistência do aço. No entanto, o carbono também pode afetar negativamente a resistência à corrosão.
Níquel: É o principal elemento formador de austenita. O níquel pode retardar a corrosão do aço e o aumento dos grãos durante o aquecimento.
Molibdênio: É um elemento que forma carbonetos. Os carbonetos que ele forma são extremamente estáveis, evitando o crescimento de grãos durante o aquecimento da austenita e reduzindo a sensibilidade do aço ao superaquecimento.
Nióbio, Titânio: São elementos formadores de carboneto fortes que aumentam a resistência do aço à corrosão intergranular.
Nitrogênio: É um forte elemento formador de austenita que aumenta significativamente a resistência do aço.
Fósforo, Enxofre: Esses elementos nocivos do aço inoxidável afetam negativamente sua resistência à corrosão e propriedades de estampagem.
3. Propriedades físicas gerais do aço inoxidável
(1) Condução de calor: A taxa de transferência de calor do aço inoxidável é relativamente lenta.
(2) Expansão Térmica: Comparado ao aço carbono, o coeficiente de expansão linear do aço grau 304 é maior.
(3) Resistência Elétrica: Geralmente, a resistência elétrica das ligas é superior à dos metais puros, e o mesmo se aplica ao aço inoxidável.
(4) Propriedades Magnéticas do Aço Inoxidável
Tabela 3: Propriedades Magnéticas de Vários Materiais
Materiais | Propriedades magneticas | Permeabilidade Magnética: μ(H=50e) |
SUS430 | Magnetismo Forte | – |
Ferro | Magnetismo Forte | – |
Não | Magnetismo Forte | – |
SUS304 | Não magnético (exibe magnetismo durante trabalho a frio) | 1,5(65% Processamento) |
SUS301 | Não magnético (exibe magnetismo durante trabalho a frio) | 14,8(55% Processamento) |
SUS305 | Não magnético | – |
2. Soldabilidade
1. Soldabilidade do aço inoxidável
A resistência elétrica do aço inoxidável é significativamente maior que a do aço de baixo carbono. Durante a soldagem, tanto a haste de soldagem quanto o material base na área de soldagem são propensos a aquecer e derreter. Isso pode causar superaquecimento do material de base circundante, resultando em deformação irregular na área de soldagem e grãos grossos.
O aço inoxidável tem um alto coeficiente de expansão linear e um baixo coeficiente de condutividade térmica, dificultando a dissipação do calor. Durante a soldagem, a profundidade de penetração é alta e o aquecimento da soldagem faz com que a estrutura se expanda. Durante o resfriamento, ocorrem deformações de contração e tensões de tração significativas, o que pode facilmente levar a fissuras térmicas.
A zona afetada pelo calor (ZTA) na soldagem pode facilmente levar à corrosão intergranular. Isso ocorre porque, dentro da ZTA, o metal base fica empobrecido em cromo na faixa de temperatura de sensibilização (450°C a 850°C), dificultando a passivação.
Como resultado, a sua resistência à corrosão diminui significativamente e, portanto, é preferencialmente corroído no ambiente corrosivo correspondente, alargando os limites dos grãos do aço. Neste ponto, a plasticidade e a resistência da área corroída foram severamente comprometidas, levando a rachaduras e fraturas frágeis durante a flexão a frio e a um som não metálico quando o local corroído atinge o solo.
O aço inoxidável é um tipo de aço relativamente resistente à corrosão, mas não é totalmente à prova de ferrugem. Até o momento, não foi inventado nenhum aço que não corroa sob quaisquer condições. Portanto, tipos específicos de aço são projetados para uso em determinados ambientes.
A resistência à corrosão do aço aumenta com o teor de cromo. Quando o teor de cromo atinge ou excede 12%, a resistência à corrosão do aço muda drasticamente, passando de propenso à ferrugem para resistente à ferrugem, e de não resistente à corrosão para resistente à corrosão. Portanto, o aço inoxidável é comumente referido como uma liga à base de ferro com um teor de cromo superior a 12%.
III. Aço resistente ao calor
1. Visão Geral
A capacidade do aço de manter a sua estabilidade química (resistência à corrosão e incrustações) a altas temperaturas é referida como estabilidade térmica; a propriedade do aço de ter resistência suficiente em altas temperaturas é chamada de resistência térmica. O aço que possui estabilidade térmica e resistência térmica é conhecido como aço resistente ao calor.
1. Classificação do Aço Resistente ao Calor
(1) No aço perlítico resistente ao calor, os elementos de liga primários são cromo, molibdênio e vanádio, com seu conteúdo combinado normalmente inferior a 5%. Este tipo também é conhecido como aço resistente ao calor de baixa liga.
(2) O aço martensítico resistente ao calor não apenas apresenta resistência a altas temperaturas, mas também apresenta notável resistência à corrosão. Os aços 1Cr13 e 2Cr13 podem servir como aços resistentes ao calor, bem como aços inoxidáveis.
(3) Aço Ferrítico Resistente ao Calor
Este tipo de aço tem excelente resistência à oxidação e corrosão em alta temperatura, mas tem baixa resistência ao calor e é propenso à fragilidade.
(4) Aço Austenítico Resistente ao Calor
Este tipo de aço não apenas possui alta resistência ao calor, mas também apresenta considerável plasticidade, tenacidade e excelentes propriedades de soldagem. Devido à sua estrutura austenítica monofásica, também apresenta resistência superior à corrosão.
2. Soldabilidade
1. Soldabilidade do aço perlítico resistente ao calor
O elemento principal do aço perlítico resistente ao calor é o carbono e contém uma certa quantidade de cromo e molibdênio. Algumas variedades também contêm elementos como vanádio, tungstênio, silício, titânio e boro. A presença destes elementos de liga torna a solda e a zona afetada pelo calor propensas ao endurecimento.
Após a soldagem, o resfriamento ao ar pode facilmente produzir martensita dura e quebradiça, o que não apenas afeta as propriedades mecânicas da junta soldada, mas também gera tensões internas significativas. Combinado com uma alta concentração de difusão de hidrogênio, a costura de solda e a zona afetada pelo calor são propensas a trincas a frio.
Além disso, como o aço perlítico resistente ao calor contém carbonetos fortes como nióbio, molibdênio e cromo, e é normalmente usado em altas temperaturas, ele é suscetível a rachaduras por reaquecimento.
2. Soldabilidade do aço martensítico resistente ao calor
O aço martensítico resistente ao calor inclui principalmente aço com alto teor de cromo com composições simples, como Cr13 e 2Cr13, bem como aço que adiciona elementos de liga como Mo, V, W, Nb, etc., à base de cromo 12. Esses tipos de aço tendem a sofrer têmpera ao ar, resultando em baixa soldabilidade. Após a soldagem, eles geralmente formam martensita de alta dureza e uma pequena quantidade de estruturas bainíticas, levando à trinca a frio.
3. Soldabilidade do aço ferrítico resistente ao calor
A maior parte do aço ferrítico resistente ao calor é composto de aço com alto teor de cromo com w(Cr)>17% e uma porção de aço tipo Cr13. Esses tipos de aço não sofrem transformação de fase α→Y durante a soldagem, não apresentando tendência ao endurecimento. No entanto, os grãos próximos à linha de fusão aumentarão rapidamente, levando à fragilidade da junta soldada.
Quanto maior o teor de cromo e maior o tempo de permanência em altas temperaturas, mais severa se torna a fragilidade. Essa fragilidade não pode ser refinada por meio de tratamento térmico, tornando-a propensa a trincas durante a soldagem de estruturas rígidas.
4. Soldabilidade do aço austenítico resistente ao calor
O aço austenítico resistente ao calor tem uma microestrutura austenítica como matriz. Este tipo de aço contém quantidades significativas de níquel, manganês e nitrogênio, que são elementos formadores de austenita. Possui excelente resistência a altas temperaturas e estabilidade estrutural acima de 600 ℃, combinada com bom desempenho de soldagem. Portanto, é o tipo de aço resistente ao calor mais utilizado em aplicações que variam de 600 a 1200 ℃.