Embora o alumínio e suas ligas sejam amplamente utilizados na soldagem de produtos importantes, eles apresentam dificuldades na produção real de soldagem. Alguns dos principais problemas incluem porosidade na solda, trincas a quente durante a soldagem e obtenção de resistência igual na junta.
Uma das razões para estes problemas é a forte atividade química do alumínio e suas ligas, o que torna a superfície muito propensa à formação de filmes de óxido, muitas vezes refratários. Por exemplo, o ponto de fusão do Al2O3 é 2.050 ℃ e o ponto de fusão do MgO é 2.500 ℃. Além disso, o alumínio e suas ligas possuem alta condutividade térmica, facilitando a não fusão durante a soldagem.
O filme de óxido, que possui densidade semelhante à do alumínio, pode formar inclusões no metal de solda. Além disso, o filme de óxido menos denso com MgO pode absorver mais água e é frequentemente uma causa significativa de porosidade na solda. Além disso, o alumínio e suas ligas possuem um grande coeficiente de expansão linear e alta condutividade térmica, tornando-os propensos à deformação durante a soldagem.
Finalmente, o artigo analisa as fissuras relativamente graves que ocorrem durante os testes.
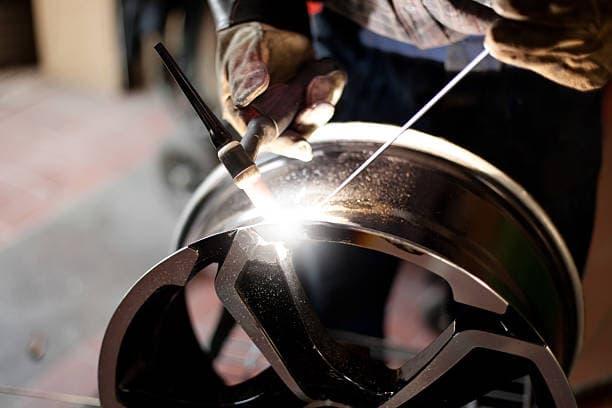
1. Fissuras em juntas soldadas de liga de alumínio e suas características
Durante o processo de soldagem da liga de alumínio, várias rachaduras podem aparecer nas juntas soldadas devido a diferenças nos tipos, propriedades e estruturas de soldagem dos materiais.
A forma e a distribuição destas fissuras podem ser bastante complexas.
Com base na sua localização, essas fissuras podem ser divididas em dois tipos:
(1) Trincas no metal de solda: fissuras longitudinais, fissuras transversais, fissuras de cratera, fissuras em forma de cabelo ou de arco, fissuras de raiz e microfissuras (especialmente na soldadura multicamadas).
(2) Rachaduras na zona afetada pelo calor: trincas de solda, trincas lamelares e micro trincas térmicas próximas à linha de fusão.
As trincas geradas durante a soldagem podem ser categorizadas em trincas a quente e trincas a frio, com base na faixa de temperatura em que ocorrem.
Trincas a quente ocorrem em altas temperaturas durante a soldagem e são causadas principalmente pela segregação de elementos de liga no contorno de grão ou pela presença de materiais de baixo ponto de fusão.
A forma, a faixa de temperatura e as principais causas das trincas a quente variam dependendo dos materiais do metal soldado.
As fissuras a quente podem ser divididas em três tipos: fissuras de cristalização, fissuras de liquefação e fissuras de poligonização.
As fissuras de cristalização ocorrem principalmente durante o processo de soldagem em altas temperaturas. Perto do solidus, o metal solidificado encolhe, causando metal líquido residual insuficiente que não consegue preencher com o tempo, levando à geração de trincas.
A trinca intergranular ocorre devido à tensão de contração de solidificação ou força externa, principalmente em aço carbono, soldas de aço de baixa liga e algumas ligas de alumínio com mais impurezas.
As fissuras de liquefação ocorrem devido à tensão de contração durante a solidificação dos contornos de grão aquecidos a altas temperaturas na zona afetada pelo calor.
Nos testes, descobriu-se que a limpeza insuficiente da superfície do material de enchimento resultou na presença de inclusões e poros na solda após a soldagem. No teste de número de três grupos, como o material de enchimento da soldagem é uma estrutura fundida e a inclusão é um material de alto ponto de fusão, ele permanece na solda após a soldagem.
A estrutura de fundição é relativamente esparsa, com muitos furos, facilitando a absorção de componentes que contenham água cristalina e óleo de qualidade. Esses fatores podem causar porosidade durante a soldagem, e inclusões e poros tornam-se peças-chave que induzem microfissuras quando a solda está sob tensão de tração.
Observações adicionais ao microscópio revelaram uma interação entre essas inclusões e microfissuras induzidas pelos poros. No entanto, é um desafio determinar se as inclusões atuam principalmente como uma fonte de concentração de tensão para induzir fissuras ou como uma fase frágil para induzir fissuras.
Além disso, acredita-se amplamente que a porosidade nas soldas de ligas de alumínio-magnésio não afeta significativamente a resistência à tração da solda. No entanto, este estudo encontrou microfissuras induzidas por inclusões e porosidade nas amostras de tração da solda simultaneamente.
Se as microfissuras induzidas pelos poros são um fenômeno secundário associado ou um dos principais fatores que causam um declínio significativo na resistência à tração das soldas, necessita de mais estudos.
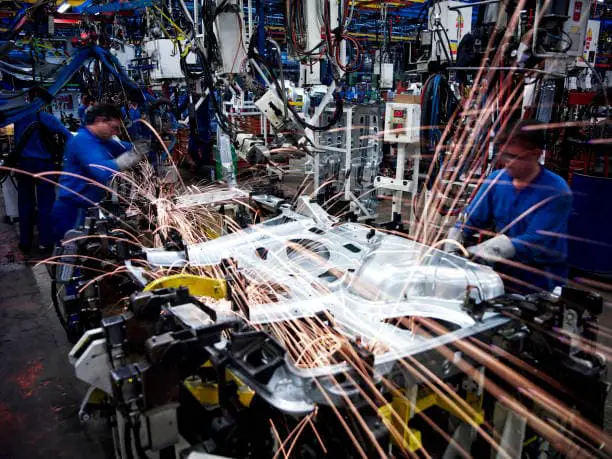
2. Processo de geração de crack a quente
Atualmente, a teoria da soldagem de trincas a quente, proposta por Prokhorov tanto nacional quanto internacionalmente, é considerada altamente refinada.
Para resumir, a teoria sugere que a geração de fissuras no cristal depende principalmente dos três fatores a seguir:
- O tamanho da faixa de temperatura frágil
- A ductilidade da liga dentro desta faixa de temperatura
- A taxa de deformação do metal quando na faixa de temperatura frágil
O tamanho da faixa de temperatura frágil e o valor de ductilidade dentro desta faixa são comumente chamados de fatores metalúrgicos que podem produzir trincas a quente na soldagem, enquanto a taxa de deformação do metal dentro da faixa de temperatura frágil é conhecida como fator mecânico.
O processo de soldagem envolve uma série de procedimentos tecnológicos desequilibrados. Esta característica está intimamente ligada aos fatores metalúrgicos e mecânicos de fratura metálica em juntas soldadas, como heterogeneidade física, química e organizacional, escórias e inclusões, elementos gasosos e vagas com concentrações supersaturadas dos produtos dos processos tecnológicos e metalúrgicos de soldagem. .
Todos esses fatores estão intimamente relacionados ao início e desenvolvimento de trincas na metalurgia.
Em termos de fatores mecânicos, o gradiente específico de temperatura e a taxa de resfriamento do ciclo térmico de soldagem podem fazer com que a junta soldada fique em um estado complexo de tensão-deformação sob certas condições de restrição, o que fornece as condições necessárias para o início e desenvolvimento de trincas.
Durante o processo de soldagem, o efeito combinado de fatores metalúrgicos e mecânicos pode fortalecer ou enfraquecer a ligação metálica de duas maneiras.
Se uma ligação forte for estabelecida no metal da junta soldada durante o resfriamento, a deformação pode permanecer obediente sob certas condições de restrição rígidas. Quando a solda e o metal próximo à costura podem suportar tensões de restrição externas e tensões residuais internas, é menos provável que ocorram trincas e a sensibilidade do metal a trincas é baixa.
Por outro lado, se a tensão não puder ser suportada, é mais provável que a ligação de resistência no metal seja interrompida, resultando em fissuras. Neste caso, a sensibilidade à fissuração do metal da junta de solda é alta.
O metal da junta de solda é resfriado à temperatura ambiente a uma certa taxa a partir da temperatura de solidificação da cristalização. Sua sensibilidade à fissuração depende da comparação da capacidade de deformação e da deformação aplicada, bem como da comparação da resistência à deformação e da tensão aplicada.
No entanto, durante o processo de resfriamento, diferentes estágios de temperatura podem resultar em diferentes resistências intergranulares e crescimento da resistência dos grãos, diferentes distribuições de deformação entre e dentro dos grãos, diferentes comportamentos de difusão induzidos por deformação, diferentes condições de concentração de tensão e fatores que levam à fragilização do metal. Estes podem causar diferentes elos fracos específicos em juntas soldadas, e o grau em que eles enfraquecem também pode variar.
A ocorrência de trincas no metal da junta soldada está intimamente relacionada a fatores metalúrgicos e mecânicos.
O gradiente de tensão em fatores mecânicos está relacionado ao gradiente de temperatura, que é determinado pelas características do ciclo térmico. A condutividade térmica do metal determina as características do ciclo térmico, que são consideradas fatores metalúrgicos. Estes incluem as características de mudança termoplástica do metal, expansão térmica e transformação estrutural.
O estado tensão-deformação do metal da junta soldada é grandemente influenciado por fatores metalúrgicos e mecânicos. Além disso, esses fatores sofrem alterações à medida que a temperatura diminui e a velocidade de resfriamento muda.
Diferentes faixas de temperatura afetam a resistência do metal da junta soldada de maneira diferente. Por exemplo, a grande faixa de temperatura de cristalização e a baixa temperatura solidus provavelmente causarão concentração de tensão no metal líquido residual de baixo ponto de fusão entre os grãos, levando a rachaduras no metal sólido. Da mesma forma, se a contração for grande, especialmente sob a condição de resfriamento rápido, é provável que ocorram rachaduras quando a taxa de deformação de contração for alta e o estado de tensão-deformação for severo.
Durante a fase posterior de solidificação e cristalização do metal de solda durante a soldagem da liga de alumínio, o eutético é comprimido no centro da intersecção do cristal para formar uma “película líquida”. Neste ponto, devido à grande retração durante o resfriamento, a retração livre não está disponível para gerar grandes tensões de tração. Como resultado, o filme líquido forma um elo fraco, que pode rachar na zona fraca sob o efeito da tensão de tração.
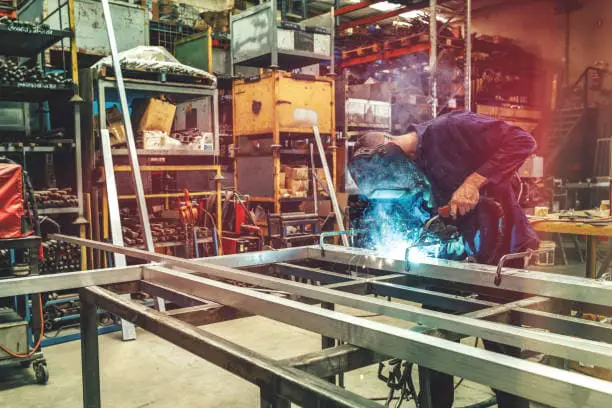
3. Mecanismo de trincas a quente
Para investigar a ocorrência de trincas a quente na soldagem de ligas de alumínio, o processo de cristalização da poça de soldagem é classificado em três etapas.
O primeiro estágio é o estágio líquido-sólido, durante o qual existe um pequeno número de núcleos de cristal à medida que a poça fundida de soldagem começa a esfriar devido à alta temperatura. À medida que a temperatura cai e o tempo de resfriamento aumenta, os núcleos cristalinos crescem gradualmente e novos surgem.
Porém, a fase líquida ainda predomina e não há contato entre os grãos adjacentes, o que permite o livre fluxo da liga líquida de alumínio que ainda não solidificou. Assim, mesmo sob tensão de tração, quaisquer lacunas abertas podem ser preenchidas prontamente pelo metal líquido que flui, tornando muito pequena a probabilidade de trincas neste estágio.
O segundo estágio é o estágio sólido-líquido. Aqui, a fase sólida na poça fundida continua a aumentar à medida que a cristalização progride, e os núcleos cristalinos previamente formados continuam a crescer.
Quando a temperatura cai até um certo ponto, os cristais de metal da liga de alumínio solidificados entram em contato uns com os outros e rolam continuamente juntos. Nesta fase, o fluxo da liga de alumínio líquida é bloqueado e a cristalização da poça fundida entra na fase sólido-líquida.
Devido à pequena quantidade de metal de liga de alumínio líquido, a deformação do próprio cristal pode ser fortemente desenvolvida nesta fase, e a fase líquida residual entre os cristais não é fácil de fluir.
As pequenas lacunas geradas sob tensão de tração não podem ser preenchidas, e mesmo uma pequena tensão de tração pode levar à possibilidade de rachaduras. Este estágio é conhecido como “zona de temperatura frágil”.
O terceiro estágio é o estágio de solidificação completa. Quando a solda formada após a solidificação completa do metal da poça fundida é submetida a tensões de tração, ela apresenta boa resistência e plasticidade, e a probabilidade de trincas neste estágio é relativamente baixa.
Portanto, quando a temperatura é superior ou inferior à zona de temperatura frágil entre ab, o metal de solda apresenta maior resistência a trincas cristalinas e menor tendência a trincas. Em geral, para metais com menos impurezas (incluindo metais básicos e materiais de soldagem), a faixa de temperatura frágil é estreita.
A tensão de tração atua nesta faixa por um curto período de tempo, de modo que a tensão total da solda é relativamente pequena, resultando em uma menor tendência ao desenvolvimento de trincas durante a soldagem.
Porém, se houver muitas impurezas na solda, a faixa de temperatura frágil é relativamente ampla, e o tempo de ação da tensão de tração nesta faixa é relativamente longo, levando a uma maior tendência à produção de trincas.
4. Medidas de prevenção para trincas de soldagem em ligas de alumínio
Para reduzir a probabilidade de trincas a quente na soldagem de ligas de alumínio, a melhoria pode ser feita através de dois aspectos: fatores metalúrgicos e fatores tecnológicos.
Em relação aos fatores metalúrgicos, a prevenção de trincas a quente intergranulares durante a soldagem envolve o ajuste do sistema de liga de solda ou a adição de modificadores ao metal de adição.
Para controlar uma quantidade apropriada de eutético fusível e estreitar a faixa de temperatura de cristalização do ponto de vista da resistência à trinca, o foco do sistema de liga de solda precisa de ajuste.
Como a liga de alumínio é uma liga eutética típica, a faixa “máxima” de temperatura de solidificação da liga corresponde à tendência máxima de trinca.
A presença de uma pequena quantidade de eutético fusível sempre aumenta a tendência de fissuras de solidificação. Para contrariar isto, o conteúdo dos principais elementos da liga é normalmente aumentado para além do componente da liga com a tendência máxima de fissuração para produzir um efeito de “cura”.
Além disso, oligoelementos como Ti, Zr, V e B são adicionados ao metal de adição como modificadores na tentativa de melhorar a plasticidade e a tenacidade, refinando os grãos e evitando trincas a quente na soldagem. Esta tentativa está em curso há algum tempo e tem produzido resultados positivos.
A Figura 3 mostra os resultados do teste de resistência à trinca do fio de soldagem Al-4,5% Mg com um modificador sob a condição de uma solda de filete sobreposta rígida. O teste incluiu a adição de 0,15% de Zr e 0,1% de Ti+B. Os resultados indicam que a adição simultânea de Ti e B melhorou significativamente a resistência à fissuração.
Ti, Zr, V, B e Ta compartilham uma característica comum: podem reagir com o alumínio para formar uma série de reações peritéticas, resultando na formação de compostos metálicos refratários como Al3Ti, Al3Zr, Al7V, AlB2, Al3Ta, etc. .
Estas pequenas partículas refratárias podem atuar como núcleos de cristal de solidificação não espontânea durante o processo de solidificação do metal líquido, facilitando assim o refinamento do grão.
Fatores de processo como especificações de soldagem, pré-aquecimento, formato da junta e sequência de soldagem são cruciais para solucionar trincas de soldagem, que são baseadas na tensão de soldagem. Os parâmetros do processo de soldagem impactam o desequilíbrio do processo de solidificação e o estado da estrutura de solidificação, bem como a taxa de crescimento de deformação durante a solidificação, influenciando assim a formação de trincas.
Os métodos de soldagem que empregam energia térmica concentrada facilitam a soldagem rápida e podem prevenir a formação de cristais colunares grossos com forte diretividade, melhorando assim a resistência à trinca.
Reduzir a velocidade de soldagem e empregar uma pequena corrente de soldagem pode diminuir o superaquecimento da poça fundida e melhorar a resistência à trinca. Aumentar a velocidade de soldagem, entretanto, aumenta a taxa de deformação das juntas soldadas e a tendência de trincas a quente. Portanto, é evidente que o aumento da velocidade e da corrente de soldagem aumenta a tendência à trinca.
Durante a montagem e soldagem de estruturas de alumínio, a solda não apresenta muita rigidez. Como tal, podem ser tomadas medidas como soldadura seccional, pré-aquecimento ou redução da velocidade de soldadura.
O pré-aquecimento pode reduzir a expansão relativa da amostra e consequentemente diminuir a tensão de soldagem, o que reduz a tensão na faixa de temperatura frágil. Soldagem de topo com ranhuras e pequenas folgas deve ser empregada tanto quanto possível, enquanto juntas cruzadas e posicionamento e sequências de soldagem inadequadas devem ser evitadas. Quando a soldagem for concluída ou interrompida, a cratera deve ser preenchida imediatamente e a fonte de calor removida, caso contrário poderão ocorrer facilmente rachaduras na cratera.
Durante a soldagem de juntas soldadas multicamadas de ligas da série 5000, microfissuras ocorrem frequentemente devido à fusão intergranular local, necessitando do controle da entrada de calor de soldagem da próxima camada do cordão de solda.
Com base nas descobertas deste artigo, a limpeza da superfície do metal base e do material de enchimento é crucial para a soldagem de ligas de alumínio. A inclusão de materiais torna-se a fonte de trincas na solda e a principal razão para o declínio do desempenho da solda.