Introdução
A soldagem é um processo primário na fabricação de chapas metálicas, caracterizado por alta intensidade de trabalho e condições de trabalho adversas. Como tal, alta proficiência é essencial.
A automação na soldagem e o desenvolvimento de métodos de união inovadores têm sido pontos focais consistentes para profissionais da tecnologia de soldagem.
Um aspecto fundamental da automação da soldagem é o controle da qualidade e eficiência da soldagem. Durante o processo, desafios como alinhamento do arco e da costura de solda, uniformidade das folgas dos componentes, penetração da solda e controle da distorção da soldagem devem ser abordados.
Com os rápidos avanços na tecnologia de soldagem a laser, ela deu um salto significativo e amadureceu em sua aplicação em vários setores, incluindo eletrodomésticos, eletrônicos de alta tecnologia, fabricação automotiva, produção de trens de alta velocidade e usinagem de precisão.
Os benefícios da soldagem a laser podem ser compreendidos comparando-a com a soldagem a arco tradicional. Esta postagem irá se aprofundar no processo de soldagem a laser e explorar como obter melhores resultados.
Para avaliar a qualidade de uma solda a laser, a relação profundidade/largura e a morfologia da superfície são levadas em consideração. Esta postagem examinará os parâmetros do processo que impactam esses índices.
Experimentos de soldagem a laser foram realizados em placas de aço inoxidável, alumínio e aço carbono. Os resultados fornecem insights práticos que podem ser utilizados na produção de soldagem.
A soldagem a laser é uma técnica de produção de ponta que utiliza um laser com alta densidade de energia como fonte de calor para soldagem. É amplamente utilizado na indústria de fabricação de chapas metálicas devido às suas vantagens, incluindo alta densidade de energia, rápida velocidade de soldagem, respeito ao meio ambiente, deformação mínima da placa e muito mais.
A soldagem a laser, com base nas características da formação da costura de solda, pode ser dividida em soldagem por condução e soldagem por penetração profunda. A soldagem por condução utiliza baixa potência do laser, resultando em tempos de formação de poças de fusão mais longos e profundidades de fusão rasas.
É usado principalmente para soldar pequenos componentes.
Em contraste, a soldagem de penetração profunda possui alta densidade de potência, onde o metal na área de irradiação do laser derrete rapidamente.
Esta fusão é acompanhada por intensa vaporização, conseguindo cordões de solda com profundidade significativa e relação largura-profundidade de até 10:1.
Componentes de chapa fina podem ser unidos usando vários métodos de soldagem, incluindo soldagem a laser, brasagem, soldagem por hidrogênio atômico, soldagem por resistência, soldagem por arco de plasma e soldagem por feixe de elétrons.
Ao comparar a soldagem a laser com outras técnicas de soldagem comuns, ela oferece vantagens significativas em termos de zona afetada pelo calor, deformação térmica, qualidade da costura de solda, necessidade de material de enchimento e ambiente de soldagem.
A comparação entre a soldagem a laser e outros métodos de soldagem pode ser encontrada na Tabela 1.
Tabela 1 Comparação entre soldagem a laser e outros métodos de soldagem
Soldagem a laser | menos | menos | preferencialmente | não | nenhum requesito especial |
Brasagem | comumente | comumente | comumente | sim | Aquecimento geral |
Soldagem a arco de argônio | mais | mais | comumente | sim | Eletrodo necessário |
Soldagem por resistência | mais | mais | comumente | não | Eletrodo necessário |
Soldagem a arco plasma | comumente | comumente | comumente | sim | Eletrodo necessário |
Soldagem por feixe de elétrons | menos | menos | preferencialmente | não | vácuo |
Características da soldagem a laser
A soldagem a laser utiliza um laser que canaliza um feixe de laser de alta energia para uma fibra óptica. Após a transmissão, ela é colimada em luz paralela usando uma lente colimadora e então focada na peça de trabalho.
Isso resulta em uma fonte de calor de energia extremamente alta que derrete o material na junta. O metal fundido esfria rapidamente para formar uma solda de alta qualidade. A aparência de uma peça de chapa metálica soldada a laser é mostrada na figura abaixo.
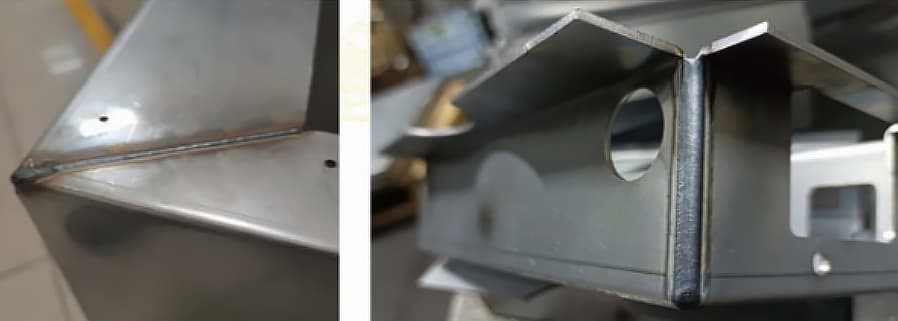
Operação fácil:
As máquinas de solda a laser são fáceis de usar. A operação é simples, fácil de aprender e fácil de usar. O nível de especialização exigido para os operadores é relativamente baixo, o que se traduz em poupanças nos custos laborais.
Alta flexibilidade:
Os soldadores a laser podem soldar de qualquer ângulo e são hábeis em acessar áreas de difícil acesso. Eles podem lidar com componentes de soldagem complexos e peças grandes de formato irregular, oferecendo flexibilidade incomparável na soldagem em qualquer orientação.
Segurança aprimorada:
O bico de soldagem de alta segurança é ativado somente em contato com o metal, apresentando um interruptor de toque com sensor de temperatura corporal. Padrões de segurança específicos devem ser respeitados ao operar o gerador de laser especializado, incluindo o uso de óculos de proteção para minimizar possíveis danos aos olhos.
Qualidade superior do feixe de laser:
Uma vez focado, o laser atinge uma alta densidade de potência. Com foco a laser de alta potência e modo baixo, o diâmetro do ponto resultante é minúsculo, promovendo significativamente a automação na soldagem de chapas finas.
Velocidade de soldagem rápida com penetração profunda e distorção mínima:
Devido à alta densidade de potência da soldagem a laser, pequenos poros se formam no metal durante o processo. A energia do laser penetra profundamente no material através desses poros com propagação lateral mínima. A profundidade da fusão do material é considerável e a velocidade de soldagem é rápida, cobrindo uma grande área em pouco tempo.
Custos trabalhistas reduzidos:
Devido à entrada mínima de calor durante a soldagem a laser, a distorção pós-soldagem é menor. Isto resulta em um acabamento de solda visualmente atraente, levando à redução do processamento pós-soldagem, o que por sua vez reduz significativamente ou até mesmo elimina os custos de mão de obra associados ao alisamento e nivelamento.
Capacidade de soldar materiais difíceis:
A soldagem a laser não é apenas adequada para unir uma variedade de metais diferentes, mas também para soldar metais e ligas como titânio, níquel, zinco, cobre, alumínio, cromo, ouro, prata, aço e ligas de corte. Ele atende bem às necessidades de desenvolvimento de novos materiais em eletrodomésticos.
Particularmente adequado para soldagem de chapas finas e componentes estéticos não revestidos:
Dada a sua alta relação de aspecto na soldagem, baixo aporte de calor, zona mínima afetada pelo calor e distorção reduzida, a soldagem a laser é especialmente adequada para soldagem de chapas finas, componentes estéticos não revestidos, peças de precisão e componentes termicamente sensíveis. Isto pode minimizar ainda mais as correções pós-soldagem e o processamento secundário.
Comparação entre soldagem a laser e soldagem a arco tradicional
Introdução à soldagem a arco
A soldagem a arco tradicional pode ser amplamente categorizada em vários tipos, incluindo soldagem a arco com eletrodo, soldagem com gás inerte de tungstênio (TIG), soldagem com gás inerte de metal (MIG) e soldagem a arco submerso.
A soldagem a arco com eletrodo envolve a formação de um arco entre o eletrodo e a peça de trabalho, gerando calor que derrete o metal no ponto de contato entre o eletrodo e a peça de trabalho. Isso cria uma poça de metal fundido. O eletrodo é então movido em uma direção específica, criando novas poças de metal fundido e solidificando as poças anteriores, resultando na formação de uma solda.
Um diagrama do processo de soldagem é mostrado na Figura 1.
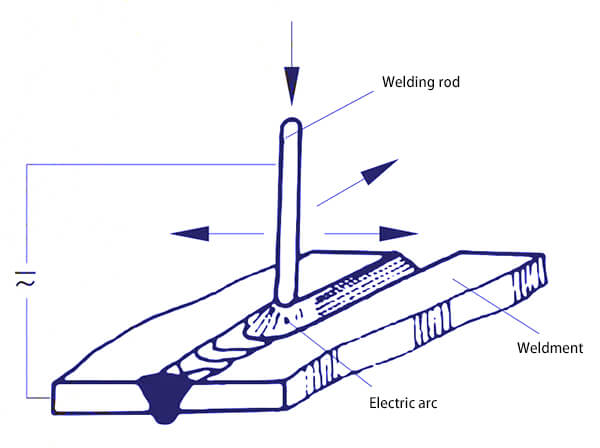
Fig. 1 Diagrama esquemático da soldagem a arco de eletrodo
A soldagem com gás inerte de tungstênio (TIG) usa um eletrodo de tungstênio como eletrodo de descarga, que não é consumido durante o processo. A área de soldagem é protegida por um gás inerte, normalmente argônio, e o calor gerado pelo arco é usado para derreter tanto o metal base quanto o material de soldagem. O resultado é uma superfície de soldagem lisa com poucos ou nenhum respingo.
Soldagem por arco de metal a gás (GMAW) é um processo onde um arco é gerado entre o fio de soldagem e o metal base, fazendo com que o fio e o metal base derretam. O material derretido solidifica, formando uma solda.
Embora a soldagem a arco ainda detenha uma posição dominante na indústria de soldagem, as crescentes demandas por soldagem eficiente e de alta qualidade levaram a limitações em sua aplicação em alguns campos de fabricação de chapas metálicas de alta qualidade. Algumas das desvantagens da soldagem a arco tradicional incluem:
- A necessidade de argônio de alta pureza como gás de proteção, que pode ser caro.
- Um alto nível de habilidade e certificação é necessário para uma operação adequada, tornando-o inacessível para muitos.
- A corrente de alta densidade e o calor gerado durante o processo de soldagem podem impactar negativamente a soldagem de placas metálicas com baixos pontos de fusão.
- Baixa eficiência de soldagem e velocidade lenta.
- A superfície de soldagem é áspera, exigindo retificação adicional para obter uma superfície lisa.
- Força de soldagem limitada.
Vantagens da soldagem a laser
As principais técnicas de soldagem a laser incluem soldagem por autofusão, soldagem por oscilação, soldagem por enchimento de fio, soldagem por galvanômetro e soldagem composta que combinam vários métodos de soldagem.
A Tabela 1 destaca as vantagens da tecnologia de soldagem a laser em comparação à soldagem a arco tradicional.
Para indústrias de fabricação de chapas metálicas de alta qualidade que exigem produtos de alto valor agregado com qualidade consistente, pequenas lacunas de solda e alta eficiência, a soldagem a laser é a melhor escolha.
Tabela 1 Comparação das características entre soldagem a laser e soldagem a arco
Soldagem a arco | Soldagem a laser |
É necessária corrente de alta densidade e o efeito térmico é grande | Baixo calor de soldagem, pequena deformação e efeito térmico |
Penetração superficial e baixa resistência de soldagem | Penetração profunda e alta resistência de soldagem |
Tipo de contato, limitado por espaço | Tipo sem contato, menos limitado por espaço |
Grande corrente de partida de arco e grande faixa de soldagem | Pequeno ponto de soldagem, capaz de soldar peças de precisão |
Os operadores têm requisitos elevados e exigem certificados de operação especiais. | Baixos requisitos para operadores |
Baixa eficiência de soldagem e velocidade lenta de soldagem | Alta eficiência de soldagem e velocidade de soldagem rápida |
Poluição e perda de eletrodo | Sem perda de eletrodo |
A superfície é áspera e requer retificação posterior. | A morfologia da superfície é estável e basicamente não há necessidade de retificação posterior. |
Parâmetros do processo de soldagem a laser
Índice de costura de soldagem a laser
Os requisitos para o efeito de soldagem de peças de chapa metálica variam dependendo das necessidades do cliente. Estes requisitos refletem-se principalmente nos seguintes indicadores:
- Morfologia da superfície (por exemplo, côncava, plana ou convexa)
- A relação profundidade-largura da poça de fusão
- Ausência de defeitos como poros, rachaduras, impurezas e rebaixos
A morfologia da superfície da solda pode ser alterada ajustando fatores como potência de soldagem, desfocagem e modo de emenda. A relação profundidade/largura da poça de fusão é um fator importante para determinar a resistência da solda.
Para clientes que possuem requisitos de resistência para seus produtos de soldagem, uma série de etapas devem ser executadas, incluindo corte de fio, incrustação, retificação e polimento, teste de corrosão e análise metalográfica microscópica. Este processo reflete a dureza da solda, que está intimamente relacionada à relação profundidade/largura. O índice de resistência à tração da solda também pode ser determinado através de um teste de resistência à tração. A Figura 2 mostra a análise metalográfica da taxa de penetração.
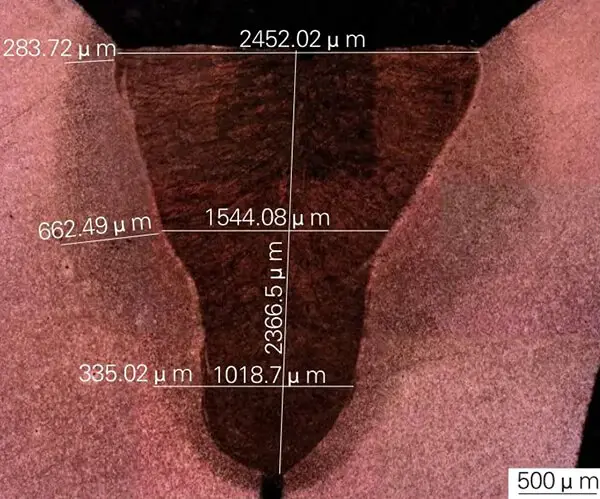
Fig. 2 análise metalográfica da taxa de penetração
Em certos ambientes de trabalho, as soldagens podem apresentar defeitos como poros, rachaduras, impurezas e rebaixos, o que pode representar sérios riscos à segurança. Por exemplo, alguns produtos exigem padrões rigorosos de estanqueidade ao ar e à água.
A Figura 3 mostra uma comparação entre soldas normais e soldas com defeitos.
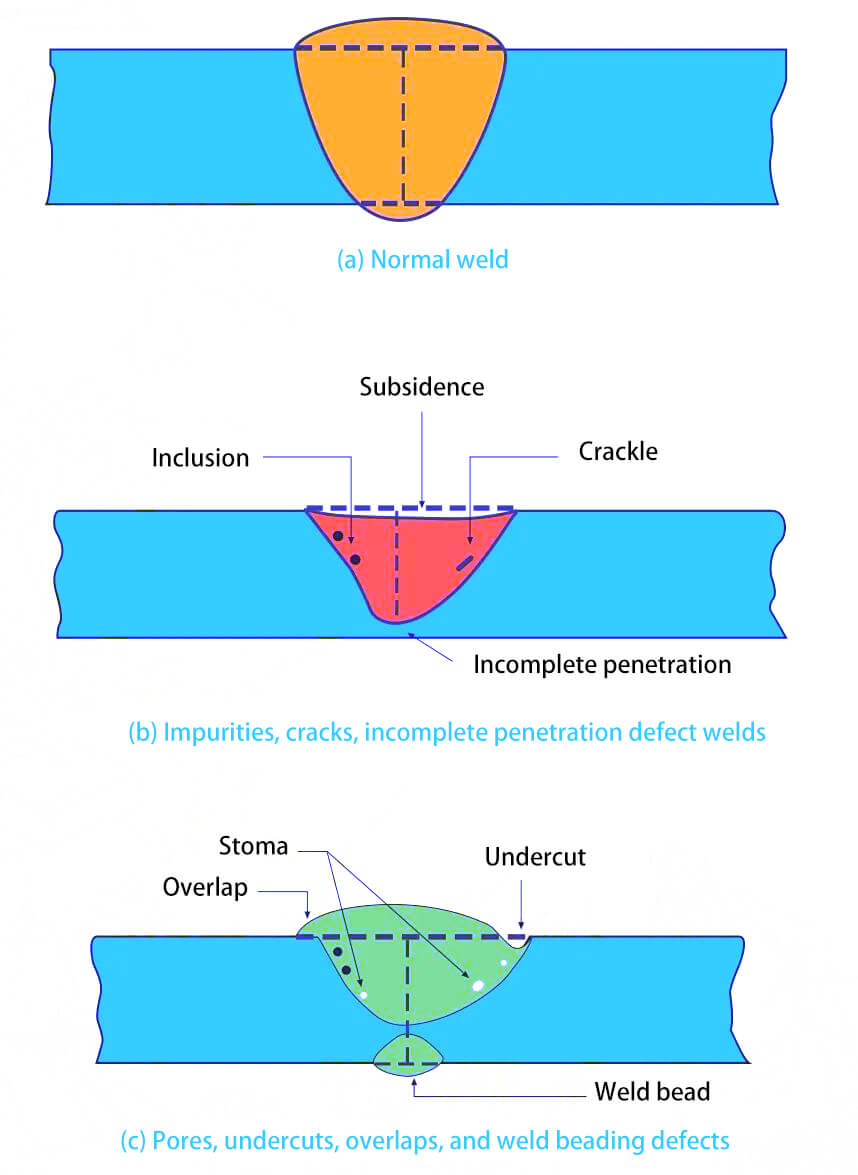
Fig.3 diagrama de costura de solda
Fatores que influenciam a soldagem a laser
Vários fatores impactam diretamente a soldagem a laser, incluindo temperatura de soldagem, ponto de fusão dos materiais de soldagem, taxa de absorção do laser dos materiais de soldagem e influência térmica.
Em termos do processo de soldagem, fatores como propriedades do material, potência do laser, velocidade de soldagem, posição do foco, gás de proteção e folga da solda devem ser levados em consideração.
A absortividade do laser dos materiais de soldagem afeta a qualidade da solda. Materiais como alumínio e cobre apresentam maior absortividade do laser, enquanto o aço carbono e o aço inoxidável apresentam menor absortividade do laser. Materiais de soldagem com alta absortividade normalmente requerem mais energia para derreter e formar uma poça de fusão estável.
A potência do laser é a fonte de energia para a soldagem a laser e desempenha um papel crítico na determinação do efeito da soldagem. Quanto maior for a potência do laser, melhor será o efeito de soldagem. No entanto, muita potência do laser pode levar à instabilidade da poça de fusão e à redução da profundidade. Portanto, escolher o valor apropriado da potência do laser é crucial.
Existe uma relação inversa entre velocidade de soldagem e penetração. Velocidades de soldagem mais rápidas resultam em menor consumo de energia, enquanto velocidades mais lentas podem causar superaquecimento, especialmente em materiais sensíveis ao calor, como o alumínio.
A posição do foco afeta diretamente a penetração e a largura da solda. Quando o foco está localizado na superfície do material de soldagem, ele é denominado foco zero. Quando o foco está acima ou abaixo do material de soldagem, é denominado foco excêntrico. O ponto de foco zero é o menor e tem a maior densidade de energia, enquanto a soldagem fora de foco tem uma densidade de potência mais baixa, mas um ponto de luz maior, tornando-o adequado para soldar peças com um alcance maior.
O tipo e método de proteção do gás também afetam o processo de soldagem. A função do gás de proteção não é apenas prevenir a oxidação durante a soldagem, mas também suprimir a nuvem de plasma gerada durante a soldagem a laser. A escolha do gás de proteção pode afetar a aparência e a cor da superfície da solda.
A folga da solda da peça a ser soldada está relacionada à penetração, largura e morfologia da solda. Uma folga de solda muito grande pode resultar em dificuldade de fusão e combinação, bem como expor o laser e potencialmente danificar a ferramenta ou a peça de trabalho. Aumentar o ponto de luz ou oscilação pode melhorar a soldagem, mas a melhoria é limitada.
Análise de teste de soldagem
O teste de soldagem foi realizado utilizando um robô Yaskawa GP25, laser Prima, junta de soldagem ospri (diâmetro do núcleo 100μm, distância focal 300mm) e alimentador de fio WSX. O efeito de soldagem foi testado em placa de aço carbono Q235 de 1,5 mm, aço inoxidável SS304 e placa de liga de alumínio da série 3.
Com base na experiência, a seguinte referência pode ser fornecida para o processo de teste:
Para o teste de soldagem de chapa fina de 1mm, pode-se utilizar uma potência inicial de 1kW e uma velocidade de soldagem de 30mm/s. A potência de referência pode ser calculada como P=A·X, onde A é um coeficiente constante (A≥0) e X é a espessura da placa. À medida que a espessura da placa aumenta, o coeficiente constante A diminui gradativamente e também é influenciado pelo método de soldagem.
Análise do processo de soldagem de chapa de aço carbono
Consulte a Tabela 2 para obter os parâmetros do processo de soldagem por oscilação da chapa de aço carbono Q235 com espessura de 1,5 mm.
Tabela 2 Parâmetros do processo de soldagem oscilante da placa de aço carbono Q235
NÃO. |
Potência laser (kW) |
Velocidade de soldagem (mm/s) |
Alcance de balanço (milímetros) |
Velocidade de balanço (mm/s) |
Efeito de soldagem |
1 | 1.6 | 32 | 1 | 143 | bom |
2 | 1.6 | 31 | 1 | 148 | bom |
3 | 1.6 | 30 | 1 | 148 | bom |
4 | 1.7 | 33 | 1 | 151 | bom |
5 | 1.7 | 32 | 1 | 152 | bom |
6 | 1.7 | 34 | 1 | 150 | bom |
7 | 1,8 | 35 | 1 | 153 | bom |
8 | 1,8 | 35 | 1 | 154 | bom |
9 | 1,8 | 36 | 1 | 154 | bom |
10 | 1,9 | 36 | 1 | 156 | bom |
11 | 1,9 | 37 | 1 | 155 | bom |
12 | 1,9 | 37 | 1 | 160 | bom |
Os dados de teste mostram que durante a soldagem por oscilação de placas de aço carbono, a potência do laser deve ser aumentada com o aumento da velocidade de soldagem, garantindo ao mesmo tempo que a faixa de oscilação permanece inalterada. Se a velocidade de oscilação for muito lenta, a solda ficará irregular.
Em geral, menos energia é necessária para a soldagem por autofusão de aço carbono em comparação com a soldagem oscilante de autofusão de aço carbono, e menos energia é necessária para a soldagem oscilante de autofusão de aço carbono em comparação com a soldagem de enchimento de fio oscilante de aço carbono. A energia necessária é controlada principalmente pela potência e velocidade, com maior potência e velocidade mais rápida exigindo mais energia.
Idealmente, para equilibrar qualidade e eficiência, a velocidade de soldagem deve ser aumentada tanto quanto possível. No entanto, uma soldagem muito rápida pode causar instabilidade e ser limitada pela potência do laser e pelas propriedades do material. Portanto, normalmente se busca um equilíbrio entre potência e velocidade.
Análise do processo de soldagem de placas de alumínio
No teste, o diâmetro do núcleo da fibra óptica selecionada foi de 100μm. Para soldar materiais altamente refletivos e absorventes de calor, como alumínio e cobre, é necessária uma densidade de potência mais alta para a fusão. Neste caso, é necessária soldagem com foco zero.
A soldagem de foco zero permite densidade de potência máxima com potência mínima, tornando-a ideal para soldar peças pequenas e derreter o metal para formar uma poça de fusão. A Tabela 3 fornece os parâmetros do processo de soldagem para diferentes materiais.
Tabela 3 Comparação dos parâmetros do processo de soldagem de diferentes materiais
NÃO. |
Potência laser (kW) |
Velocidade de soldagem (mm/s) |
Espessura da placa |
Alcance de balanço (milímetros) |
Velocidade de balanço (mm/s) |
Efeito clareador | Material |
1 | 1,5 | 2.1 | 1,5 | 1 | 300 | Bom | Aço carbono Q235 |
2 | 1,5 | 1,8 | 1,5 | 1 | 300 | Bom | Liga de alumínio de 3 séries |
3 | 2 | 2,0 | 2 | 1 | 300 | Bom | Aço carbono Q235 |
4 | 2 | 1.7 | 2 | 1 | 300 | Bom | Liga de alumínio de 3 séries |
Os dados do teste indicam que, com outros parâmetros permanecendo constantes, o efeito de soldagem ideal para a liga de alumínio da série 3 requer uma velocidade de soldagem mais lenta em comparação com o aço carbono Q235, pois é necessário mais calor.
Análise do processo de sopro branco de aço inoxidável
A Tabela 4 mostra a comparação dos parâmetros do processo de branqueamento para cordões de soldagem de aço inoxidável com espessura de 1,5mm. A comparação do efeito de soldagem pode ser vista na Figura 4.
Os parâmetros de soldagem das três soldas da Figura 4 (da esquerda para a direita) correspondem aos números de série 1, 2 e 3 da Tabela 4, respectivamente.
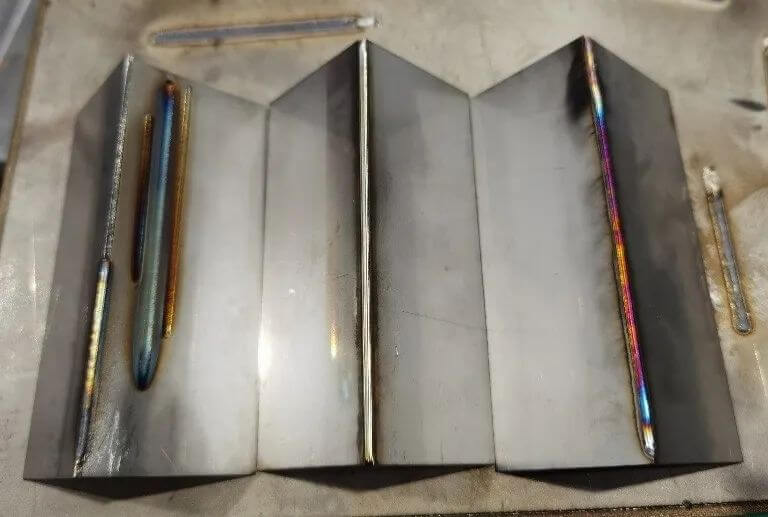
Fig. 4 Comparação do efeito de soldagem
Tabela 4 Comparação dos parâmetros do processo de branqueamento de cordões de soldagem de aço inoxidável
NÃO. | Potência laser (kW) |
Velocidade de soldagem (mm/s) |
Espessura da placa | Alcance de balanço (milímetros) |
Velocidade de balanço (mm/s) |
Efeito clareador |
1 | 1.2 | 1.7 | 1,5 | 1 | 300 | pobre |
2 | 1,5 | 1,8 | 1,5 | 1 | 300 | bom |
3 | 1.6 | 1,8 | 1,5 | 1 | 300 | pobre |
Para obter uma superfície branqueada no aço inoxidável, é necessário resfriar e cristalizar rapidamente o metal em uma atmosfera de gás de proteção após a fusão a laser. Se a potência for muito alta, muito calor ficará retido na placa metálica, causando resfriamento lento e aumento do risco de oxidação e descoloração. Se a potência for muito baixa, o metal pode não derreter completamente.
Se a velocidade for muito rápida, as ferramentas de sopro podem não ser suficientes, afetando o efeito de sopro. Se a velocidade for muito lenta, haverá acúmulo excessivo de calor. Para conseguir uma superfície branqueada, é importante encontrar um equilíbrio entre potência, velocidade e sopro.
Se não for possível obter uma superfície branqueada numa só tentativa, poderá ser possível fazê-lo soldando uma camada com uma potência ligeiramente superior e depois reduzindo a potência para uma segunda camada.
Conclusão
Durante o processo de soldagem a laser, para garantir resultados de soldagem de alta qualidade, é importante considerar uma série de fatores, incluindo propriedades do material, potência do laser, velocidade de soldagem, posição do foco, gás de proteção e folga da solda.
Para materiais comumente usados, como aço carbono, aço inoxidável e placas de alumínio, os parâmetros de teste iniciais mencionados anteriormente podem ser usados como referência e depois ajustados de acordo com as características específicas do material e os requisitos do cliente para alcançar o efeito de soldagem desejado.