O processo de soldagem a laser, principalmente para soldagem de chapas metálicas, pode ser dividido em duas categorias: soldagem a laser contínuo de fibra e soldagem a laser pulsado YAG.
Com base no princípio da soldagem a laser, ela pode ser dividida em soldagem por condução de calor e soldagem por penetração profunda a laser. Quando a densidade de potência é inferior a 104 a 105 W/cm², é considerada soldagem por condução de calor. Isso resulta em penetração superficial e velocidade de soldagem mais lenta.
Por outro lado, quando a densidade de potência for superior a 105 a 107 W/cm², a superfície metálica formará “buracos” devido ao aquecimento e resultará em soldagem de penetração profunda a laser. Este método é caracterizado por sua rápida velocidade de soldagem e grande relação profundidade/largura.
O princípio da soldagem a laser por condução de calor envolve aquecer a superfície a ser processada por meio de radiação laser, guiar o calor da superfície por meio de transferência e difusão interna e derreter a peça de trabalho para formar uma poça fundida específica, controlando parâmetros do laser, como largura de pulso, energia, pico potência e frequência de repetição. Este método é adequado para soldagem de placas finas.
A soldagem por penetração profunda a laser é usada principalmente para soldagem de engrenagens e soldagem de chapas metalúrgicas, e o foco deste artigo está no princípio da soldagem por penetração profunda a laser.
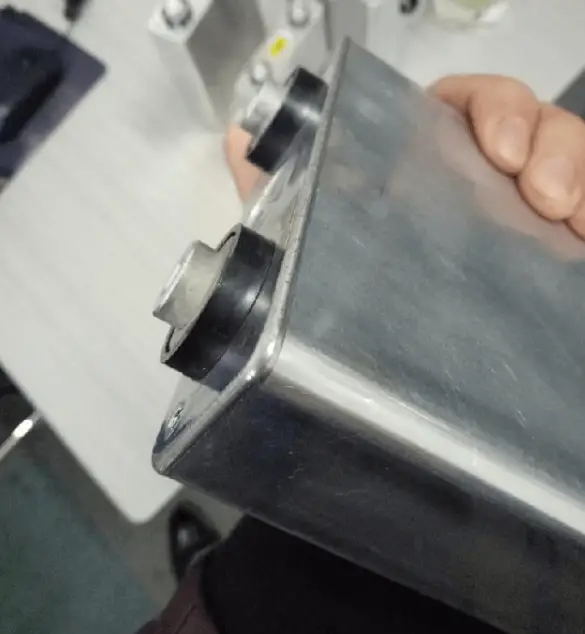
Soldagem da tampa superior da bateria de lítio com revestimento de alumínio – laser contínuo de fibra (célula de veículo de nova energia, principalmente alumínio da série 3)
1. Princípio da soldagem por penetração profunda a laser
A soldagem de penetração profunda a laser normalmente usa um feixe de laser contínuo de fibra óptica para unir materiais. O processo metalúrgico deste método é semelhante à soldagem por feixe de elétrons e é realizado através de uma estrutura em “buraco de fechadura”.
Quando o material é exposto a um laser de alta densidade de potência, ele evapora e cria pequenos furos. Os pequenos buracos, cheios de vapor, comportam-se como corpos negros e absorvem quase toda a energia do feixe incidente.
A temperatura dentro dos furos atinge aproximadamente 2.500 ℃ e o calor é transferido das paredes externas dos furos de alta temperatura para derreter o metal circundante.
Os pequenos orifícios são preenchidos com vapor de alta temperatura gerado pela evaporação contínua do material da parede sob a irradiação do laser. As quatro paredes dos furos são cercadas por metal fundido e o metal líquido é cercado por materiais sólidos.
Na maioria dos processos de soldagem convencionais e na soldagem por condução a laser, a energia é primeiro depositada na superfície da peça e depois transmitida para o interior através da condução.
O fluxo de líquido e a tensão superficial da parede fora das paredes do furo estão em equilíbrio dinâmico com a pressão contínua do vapor dentro da cavidade do furo. O feixe de laser entra continuamente nos pequenos orifícios e o material fora dos orifícios flui continuamente.
O movimento do feixe de laser mantém os pequenos furos e o metal fundido ao redor dos furos em um estado de fluxo estável.
Isso significa que os pequenos furos e o metal fundido avançarão com a velocidade do feixe principal, preenchendo a lacuna deixada para trás e solidificando-se para formar a solda.
Todos esses processos ocorrem tão rapidamente que a velocidade de soldagem pode facilmente atingir vários metros por minuto.

Soldagem a laser CW de fibra de alumínio de 6 séries (este é o piso ferroviário de alta velocidade)
2. Principais parâmetros do processo de soldagem por penetração profunda a laser
(1) Potência do laser
Existe um limite para a densidade de energia do laser na soldagem a laser. Se a densidade de energia do laser estiver abaixo deste valor, a penetração será superficial. Porém, se atingir ou ultrapassar esse valor, a penetração é bastante melhorada.
A geração de plasma, que significa o progresso da soldagem de penetração profunda estável, ocorre somente quando a densidade de potência do laser na peça excede o limite, que depende do material.
Quando a densidade de potência do laser está abaixo do limite, ocorre apenas a fusão da superfície da peça, resultando em soldagem por condução de calor estável.
Se a densidade de potência do laser estiver próxima da condição crítica para a formação do buraco de fechadura, o processo de soldagem torna-se instável, com alternância de soldagem por penetração profunda e soldagem por condução, resultando em flutuações significativas na profundidade de penetração.
Durante a soldagem de penetração profunda a laser, a potência do laser controla simultaneamente a profundidade de penetração e a velocidade de soldagem. A profundidade de penetração está diretamente relacionada à densidade de potência do feixe e é uma função da potência do feixe incidente e do ponto focal do feixe.
Em geral, para um feixe de laser de determinado diâmetro, a penetração aumenta à medida que a potência do feixe aumenta.

Cavalo de chaleira – soldagem a laser de pulso YAG (pode fazer diretamente a aparência da superfície)
(2) Ponto focal do feixe
O tamanho do ponto do feixe é uma variável crítica na soldagem a laser, pois determina a densidade de potência. No entanto, medir o tamanho do ponto para lasers de alta potência é uma tarefa desafiadora, apesar da disponibilidade de diversas tecnologias de medição indireta.
O limite do tamanho do ponto de difração do foco do feixe pode ser calculado usando a teoria da difração de luz, mas o tamanho real do ponto é maior devido à presença de aberrações nas lentes de foco.
O método mais simples de medição é o método do perfil de temperatura igual, que envolve a medição do ponto focal e do diâmetro da perfuração após queimar papel grosso e penetrar em uma placa de polipropileno.
Este método requer o domínio da potência do laser e do tempo de ação do feixe, o que pode ser alcançado por meio de prática e medição.
(3) Valor de absorção de material
A absorção do laser de materiais depende de várias propriedades importantes do material, como absortividade, refletividade, condutividade térmica, temperatura de fusão, temperatura de evaporação e assim por diante.
Existem dois fatores que afetam a absortividade dos materiais ao feixe de laser:
Primeiro, o coeficiente de resistência do material. Após medir a absortividade da superfície polida do material, verificou-se que a absortividade do material é diretamente proporcional à raiz quadrada do coeficiente de resistência, que muda com a temperatura.
Em segundo lugar, o estado superficial ou acabamento do material, que tem um impacto significativo na absortividade do feixe e, portanto, no efeito de soldagem.
Materiais com alta pureza e condutividade geral, como aço inoxidável e níquel, são os melhores para soldar.
Por outro lado, materiais de alta condutividade como cobre e alumínio são difíceis de soldar. A soldagem de alumínio da série 6 e superior é propensa a rachaduras e poros.
A soldagem do cobre geralmente depende dos requisitos da aplicação e pode ser feita com laser pulsado YAG e laser contínuo de fibra.
Na indústria joalheira, o ouro e a prata são geralmente soldados por pontos. No entanto, existem poucas aplicações industriais para soldagem destes materiais. O foco aqui está em aplicações industriais.
O comprimento de onda de saída do CO2 lasers é normalmente 10,6 μm. À temperatura ambiente, a taxa de absorção de materiais não metálicos, como cerâmica, vidro, borracha e plásticos, é muito alta, enquanto a taxa de absorção de materiais metálicos é baixa.
Contudo, uma vez que o material é derretido ou mesmo vaporizado, a sua absorção aumenta dramaticamente.
O método de revestimento superficial ou formação de uma película de óxido na superfície é altamente eficaz para melhorar a absorção dos feixes de luz.
(4) Velocidade de soldagem
A velocidade de soldagem tem um impacto significativo na profundidade de penetração. Aumentar a velocidade resultará em penetração mais superficial, mas uma velocidade muito baixa causará derretimento excessivo do material e resultará em penetração excessiva na peça de trabalho.
Portanto, existe uma faixa adequada de velocidades de soldagem para um material específico com uma determinada potência e espessura do laser, e a penetração máxima pode ser alcançada no valor de velocidade correspondente.

Soldagem de enchimento de fio de laser de pulso YGA de aço inoxidável (pode superar o problema de grandes juntas de topo e tratamento de superfície de aparência no estágio posterior)
(5) Gás de proteção
O gás inerte é frequentemente usado na soldagem a laser para proteger a poça de fusão. Em alguns casos, a proteção pode não ser necessária se o material puder ser soldado sem oxidação superficial.
No entanto, a maioria das aplicações utiliza hélio, argônio, nitrogênio ou outros gases para proteger a peça da oxidação durante a soldagem.
O hélio é um gás de proteção eficaz devido à sua alta energia de ionização, que permite que o feixe de laser passe suavemente e alcance a superfície da peça sem quaisquer impedimentos. No entanto, é relativamente caro.
O argônio é relativamente barato e possui alta densidade, proporcionando boa proteção. Porém, é propenso à ionização por plasma metálico de alta temperatura, o que reduz a potência efetiva do laser e a velocidade de soldagem, bem como a penetração.
A superfície da soldagem protegida por argônio é mais lisa em comparação com a superfície protegida por hélio.
O nitrogênio é o gás de proteção mais barato, mas não é adequado para alguns tipos de soldagem de aço inoxidável devido a problemas metalúrgicos, como absorção, que às vezes pode causar poros na área do colo.
O segundo objetivo do uso do gás de proteção é proteger a lente de foco da poluição por vapor metálico e pulverização catódica de gotículas líquidas, o que é especialmente importante na soldagem a laser de alta potência, onde o material ejetado se torna mais poderoso.
A terceira função do gás de proteção é dispersar a proteção de plasma produzida pela soldagem a laser de alta potência. O vapor metálico absorve o feixe de laser, ionizando-o em uma nuvem de plasma, e o gás de proteção ao redor do vapor metálico também ioniza devido ao aquecimento.
Se houver muito plasma, ele consumirá até certo ponto o feixe de laser. O plasma na superfície de trabalho atua como uma segunda fonte de energia, tornando a penetração mais rasa e a superfície da poça de soldagem mais larga.
A taxa de recombinação de elétrons pode ser aumentada aumentando a colisão de elétrons com íons e átomos neutros, reduzindo a densidade de elétrons no plasma.
Quanto mais leve o átomo neutro, maior será a frequência de colisão e maior será a taxa de recombinação.
Por outro lado, apenas o gás de proteção com alta energia de ionização não aumentará a densidade eletrônica devido à sua própria ionização.
Peso atômico (molecular) e energia de ionização de gases e metais comuns
Material | Ele | Ar | N | Al | mg | Fé |
Peso atômico (molecular) | 4 | 40 | 28 | 27 | 24 | 56 |
Energia de ionização (eV) | 24h46 | 15,68 | 14,5 | 5,96 | 7,61 | 7,83 |
Conforme mostrado na tabela, o tamanho da nuvem de plasma depende do tipo de gás de proteção utilizado. O hélio produz a menor nuvem de plasma, o nitrogênio produz a segunda menor e o argônio produz a maior. Quanto maior o tamanho do plasma, menor será a profundidade de penetração.
Esta diferença não se deve apenas aos diferentes níveis de ionização das moléculas de gás, mas também à diferença na difusão do vapor metálico causada pelas diferentes densidades do gás de proteção.
O hélio tem a menor ionização e densidade e pode limpar rapidamente o vapor metálico ascendente da poça de metal fundido.
Como resultado, o uso de hélio como gás de proteção pode inibir efetivamente o plasma e aumentar a penetração e a velocidade de soldagem. Além disso, é leve e dificilmente causa poros.
No entanto, na soldagem real, usar argônio como blindagem proporciona bons resultados. O efeito da nuvem de plasma na penetração é mais perceptível em baixas velocidades de soldagem e, à medida que a velocidade de soldagem aumenta, seu impacto diminui.
O gás de proteção é liberado na superfície da peça através de um bico a uma determinada pressão. O formato do bico e o diâmetro de saída são críticos, pois o bico deve ser grande o suficiente para cobrir a superfície de soldagem com o gás de proteção, mas também deve ter tamanho limitado para proteger eficazmente a lente e evitar poluição por vapor metálico ou respingos de metal. de danificar a lente.
A vazão também deve ser controlada, caso contrário, o fluxo laminar do gás protetor se tornará turbulento e o ar será aspirado para dentro da poça fundida, formando poros.
Para melhorar o efeito protetor, também pode ser utilizado o sopro lateral, onde o gás de proteção é injetado no pequeno orifício da soldagem de penetração profunda em um determinado ângulo através de um bico de pequeno diâmetro.
Isso não apenas reduz a nuvem de plasma na superfície da peça, mas também afeta o plasma no furo e a formação de pequenos furos, resultando em maior profundidade de penetração e em uma solda ideal com alta relação profundidade-largura.
No entanto, este método requer um controle preciso do tamanho e direção do fluxo de gás, pois podem ocorrer facilmente turbulência e danos à poça fundida, dificultando a estabilização do processo de soldagem.
(6) Distância focal da lente
O feixe de laser geralmente é focado durante a soldagem e uma lente com distância focal de 63 mm a 254 mm (2,5″ a 10″) é normalmente selecionada. O tamanho do ponto do foco é diretamente proporcional à distância focal; uma distância focal mais curta resulta em um ponto menor.
No entanto, a distância focal também afeta a profundidade focal, que aumenta com a distância focal. Isto significa que uma distância focal curta melhora a densidade de potência, mas requer uma manutenção precisa da distância entre a lente e a peça de trabalho para uma penetração adequada.
Na soldagem real, a menor profundidade focal usada é geralmente 126mm (5″). Quando uma junta maior ou maior soldagem for necessária, uma lente com distância focal de 254 mm (10″) pode ser selecionada, mas isso requer uma potência de saída de laser mais alta para o efeito de fechadura de penetração profunda desejado.
Para potências de laser superiores a 2 kW, especialmente para lasers de CO2 de 10,6 μm, o método de foco por reflexão é frequentemente usado, com espelhos de cobre polido como espelhos, para evitar o risco de danos ópticos às lentes de foco.
Espelhos de cobre são frequentemente recomendados para foco de feixe de laser de alta potência devido ao resfriamento eficaz.
(7) Posição de foco
Na soldagem a laser, a posição do foco é crucial para garantir a densidade de potência adequada. A variação na posição relativa entre o foco e a superfície da peça impacta significativamente a profundidade e largura da solda.
Na maioria das aplicações de soldagem a laser, o foco geralmente é definido em cerca de um quarto da penetração necessária abaixo da superfície da peça de trabalho.
(8) Posição do feixe laser
A qualidade final da solda durante a soldagem a laser de diferentes materiais é amplamente controlada pela posição do feixe de laser, sendo as juntas de topo mais sensíveis do que as juntas sobrepostas.
Por exemplo, ao soldar uma engrenagem de aço temperado em um tambor de aço de baixo carbono, o controle adequado da posição do feixe de laser resultará em uma solda composta principalmente de componentes de baixo carbono, que possuem excelente resistência à trinca.
Em certas situações, a geometria da peça a ser soldada necessita de um ângulo de deflexão para o feixe de laser. Quando o ângulo de deflexão entre o eixo do feixe e o plano da junta é inferior a 100 graus, a absorção da energia do laser pela peça permanece inalterada.
(9) Controle do aumento e diminuição gradual da potência do laser nos pontos inicial e final da soldagem
Na soldagem de penetração profunda a laser, pequenos furos estão presentes independentemente da profundidade da solda. Quando o processo de soldagem for concluído e o interruptor de alimentação for desligado, aparecerão pontos no final da soldagem.
Além disso, se a nova camada de soldagem a laser cobrir a solda anterior, poderá ocorrer absorção excessiva do feixe de laser, levando ao superaquecimento ou porosidade na soldagem.
Para evitar estes problemas, os pontos de início e fim da alimentação podem ser programados para permitir tempos de início e fim ajustáveis. Isto é conseguido aumentando eletronicamente a potência inicial de zero até o valor de potência definido rapidamente e ajustando o tempo de soldagem.
Finalmente, a potência é diminuída gradualmente do valor definido até zero no final da soldagem.
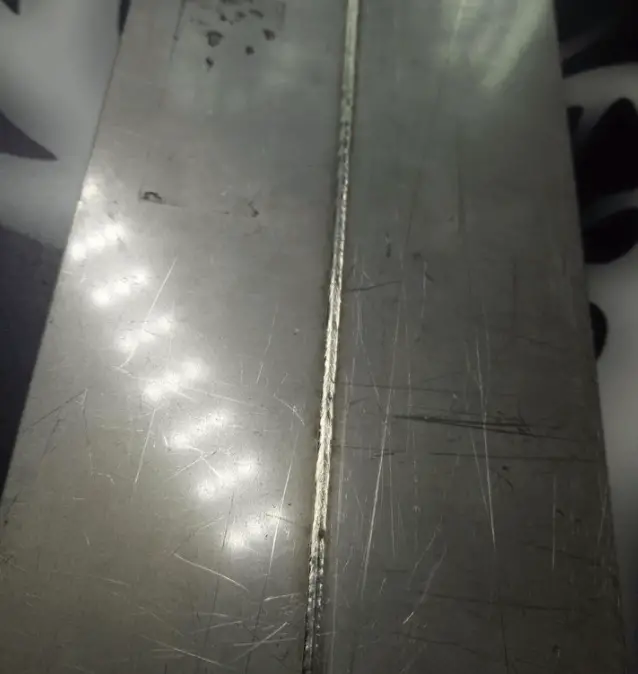
Soldagem contínua a laser de fibra óptica de aço inoxidável (adequada para soldagem de topo de pequenas placas com espessura de 0,2-3 mm)
3. Características, vantagens e desvantagens da soldagem por penetração profunda a laser
(1) Características da soldagem de penetração profunda a laser
- Soldagem com alta proporção de aspecto
O processo de soldagem de alta relação de aspecto é caracterizado por soldas profundas e estreitas, que são formadas direcionando uma cavidade cilíndrica de vapor de alta temperatura ao redor da peça de trabalho. Isto resulta na formação do metal fundido em torno da cavidade e estendendo-se até a peça de trabalho.
- Entrada Mínima de Calor
O processo de soldagem requer um aporte mínimo de calor devido à alta temperatura dentro do pequeno furo. Isto resulta em um processo de fusão rápido e uma baixa entrada de calor na peça de trabalho, levando a uma deformação térmica mínima e a uma pequena zona afetada pelo calor.
- Soldas de alta densidade
O vapor de alta temperatura dentro do pequeno orifício promove a agitação da poça de soldagem e o escape de gás, resultando em uma solda densa e de penetração sem poros. A rápida taxa de resfriamento após a soldagem ajuda a refinar a estrutura da solda.
- Soldas Fortes
O processo de soldagem não necessita de eletrodos ou fios de enchimento, e a fonte de calor é quente, levando à redução do teor de impurezas e à alteração do tamanho e distribuição da inclusão na poça fundida. Isto resulta em uma solda forte e tenaz que é pelo menos igual ou ainda mais forte que o metal original.
- Controle Preciso
O pequeno ponto de foco do laser permite alta precisão no posicionamento da solda. A saída do laser não tem “inércia” e pode ser interrompida e reiniciada rapidamente, tornando-a ideal para soldar peças complexas com tecnologia de movimento de feixe NC.
- Soldagem em atmosfera sem contato
O processo de soldagem em atmosfera sem contato envolve um feixe de fótons que fornece energia à peça sem qualquer contato físico. Isto significa que nenhuma força externa é aplicada à peça de trabalho e o laser não é afetado pelo magnetismo ou pelo ar.
(2) Vantagens da soldagem de penetração profunda a laser
- Alta velocidade de soldagem e deformação mínima
O laser focalizado usado na soldagem a laser tem uma densidade de potência muito maior em comparação aos métodos convencionais, permitindo velocidades de soldagem rápidas e zonas e deformações afetadas pelo calor mínimas. Isto torna possível soldar até mesmo materiais difíceis como o titânio.
- Manutenção Eficiente e Baixa
O feixe é fácil de transmitir e controlar, levando a uma substituição menos frequente da pistola de soldagem e do bico, e nenhum bombeamento de vácuo é necessário para a soldagem por feixe de elétrons. Isto reduz significativamente o tempo de inatividade auxiliar e aumenta o fator de carga e a eficiência da produção.
- Alta resistência e resistência
A purificação e a alta taxa de resfriamento durante a soldagem a laser resultam em alta resistência, tenacidade e propriedades abrangentes da solda.
- Custo-beneficio
A baixa entrada média de calor e a alta precisão de usinagem da soldagem a laser ajudam a reduzir o custo de reprocessamento. Além disso, o baixo custo operacional da soldagem a laser também ajuda a reduzir o custo geral de processamento da peça.
- Fácil de Automatizar
A soldagem a laser permite o controle eficaz da intensidade do feixe e o posicionamento preciso, facilitando a automatização do processo de soldagem.
(3) Desvantagens da soldagem de penetração profunda a laser
- Profundidade de soldagem limitada
- Requisitos rigorosos para montagem de peças
- Investimento inicial significativo em sistema laser