Foi demonstrado através de exemplos que metal e plástico podem ser efetivamente “conectados” usando soldagem a laser.
Deve-se notar que o termo “soldado” não é totalmente preciso e deve ser substituído por “conectado”.
Conforme mostrado na Figura 1, a porta do carro é reforçada com plástico de fibra de vidro.
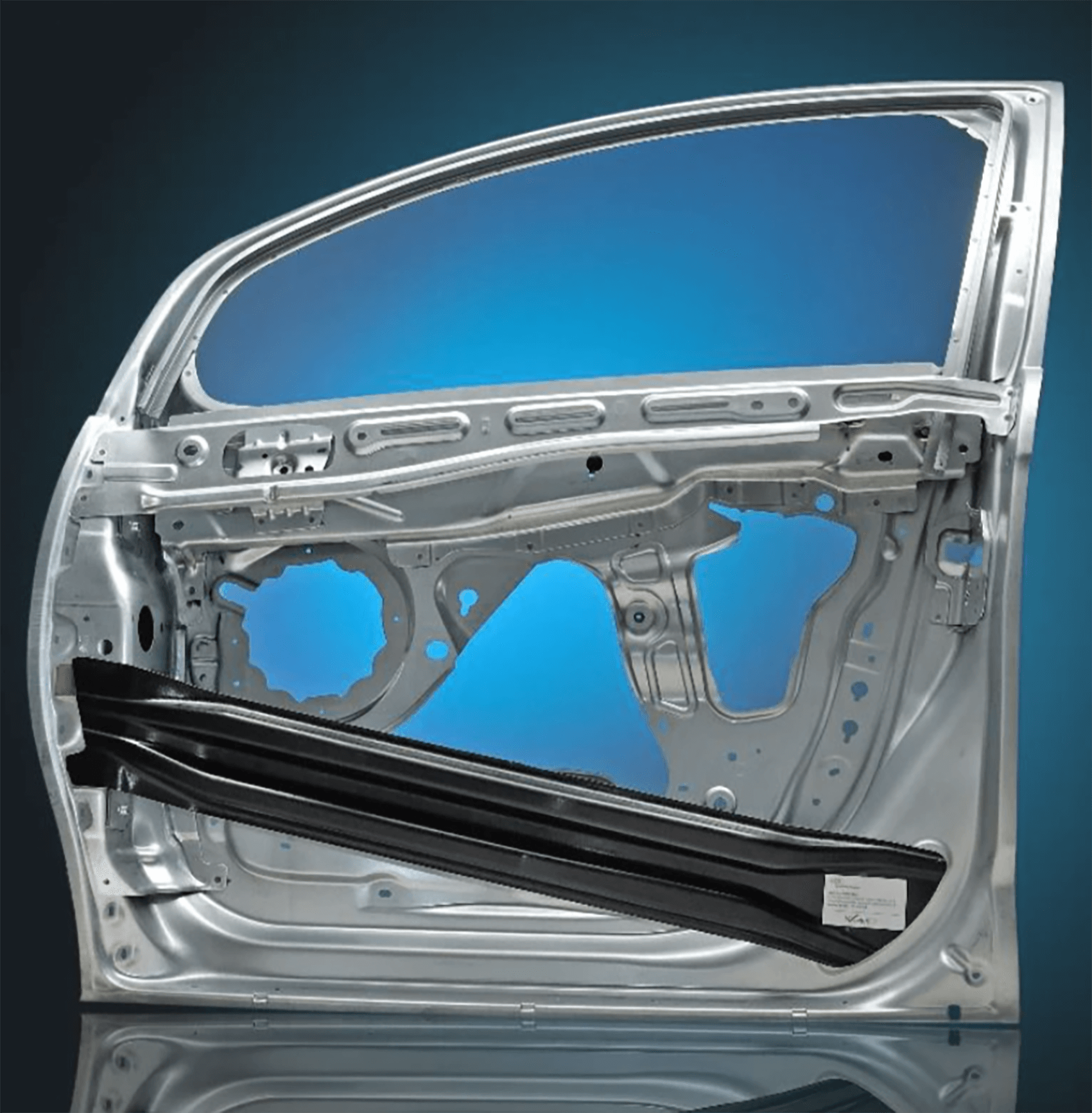
Fig. 1 Porta do carro reforçada com plástico de fibra de vidro
Com o foco crescente na redução de peso na indústria automobilística, há uma necessidade crescente de conexões eficazes entre componentes metálicos e plásticos, particularmente aqueles que contêm fibra de carbono reforçada ou fibra de vidro.
Para atender às demandas das operações aceleradas da linha de montagem na indústria automobilística, é necessária uma solução para conexões rápidas, confiáveis e automatizadas entre esses materiais.
A seguir estão três dos métodos mais comumente usados para unir peças compostas e metálicas na indústria: (liste os métodos).
Destes, a tecnologia de conexão baseada em laser é o avanço mais recente. No entanto, apesar do seu potencial, ainda existem vários desafios que devem ser enfrentados nesta tecnologia, incluindo questões relacionadas com a eficiência, resistência das articulações e envelhecimento. Este artigo fornecerá um exame aprofundado desses desafios.
(1) Conexão Mecânica: Este método é rápido, econômico e fornece uma conexão estável. No entanto, o processo de criação de furos no material compósito pode perturbar a distribuição das fibras e enfraquecer a resistência geral do compósito. Além disso, o uso de conectores como parafusos acrescenta peso à montagem.
(2) Colagem: Existe uma grande variedade de adesivos disponíveis para conectar vários materiais. Porém, a superfície deve ser pré-tratada, o processo de colagem é mais demorado, deve-se usar adesivo, o que aumenta o custo geral da ligação.
(3) Conexão Laser: A conexão do laser é rápida, confiável e fornece uma conexão forte sem a necessidade de materiais auxiliares. No entanto, atualmente está limitado ao uso apenas com termoplásticos.
1. Fundamentos da tecnologia de conexão a laser
O processo de conexão a laser de peças termoplásticas e metálicas envolve duas etapas.
Na primeira etapa, uma microestrutura é formada na superfície das peças metálicas por meio de processamento a laser. Isso normalmente é realizado usando um laser de fibra de 1 kW.
O laser varre a superfície e cria um padrão regular de ranhuras e recortes (como mostrado na Fig. 2).
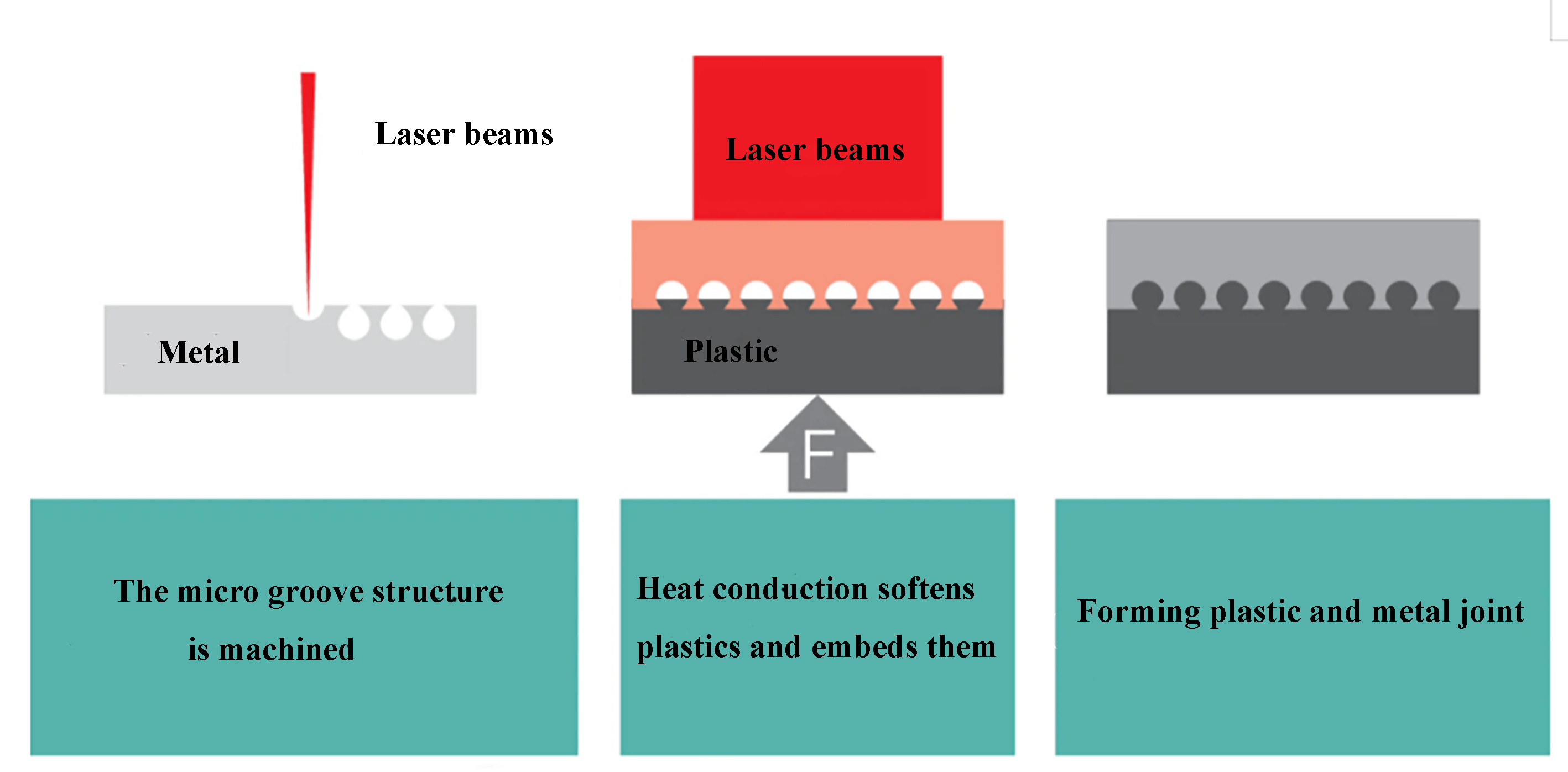
Fig. 2 Processo de colagem a laser de plástico e metal
A alta densidade de potência do feixe de laser causa fusão parcial e evaporação do metal durante a ablação. O metal fundido é expelido por evaporação de alta pressão e solidifica na borda das ranhuras para formar a estrutura recortada.
Para aumentar a aderência do plástico nesta superfície, pode-se aumentar o número e a densidade das ranhuras, conforme mostra a figura 3.

Fig. 3 Várias varreduras de feixe de laser para obter um bom formato de ranhura
Um método alternativo envolve o uso de um laser especial de pulso ultracurto (USP) para criar uma superfície esponjosa com protuberâncias cônicas. Esta técnica pode ser aplicada a superfícies de aço, alumínio, silício e titânio, resultando em melhor resistência de ligação para plásticos em comparação com superfícies processadas com lasers de fibra. No entanto, o único desafio é que o laser USP opera a uma velocidade mais lenta.
Na segunda etapa, o plástico é aquecido até derreter e depois pressionado sobre a superfície metálica. Após o resfriamento, o plástico está firmemente ligado ao metal.
Existem vários métodos para aquecer plásticos, como usar uma placa quente, radiação infravermelha ou outros processos para aquecer diretamente o plástico, ou aquecer as peças metálicas e pressioná-las sobre o plástico frio, fazendo com que o plástico derreta e flua em pequenas estruturas através condução de calor.
A primeira etapa da microusinagem a laser é rápida e sem contato, tornando-a ideal para integração em processos de produção existentes e produção em massa.
2. Teste de força de conexão
Em aplicações práticas, a junta entre metal e plástico estará sujeita a cargas. Qual é a pressão máxima que este tipo de conexão composta pode suportar e onde ela irá quebrar?
O Hoff Laser Technology Research Institute, na Alemanha, conduziu uma série de testes de estresse em vários materiais para responder a essas perguntas (Figura 4).
Um dos conteúdos do teste é o seguinte:
- O teste de cisalhamento foi realizado em uma placa de aço inoxidável de 1,5 mm e um conector plástico PP de 3 mm com fibra de vidro.
- Um teste de tração foi realizado em uma placa de aço inoxidável de 1,5 mm e um conector de plástico PP de 3 mm (excluindo fibra de vidro).
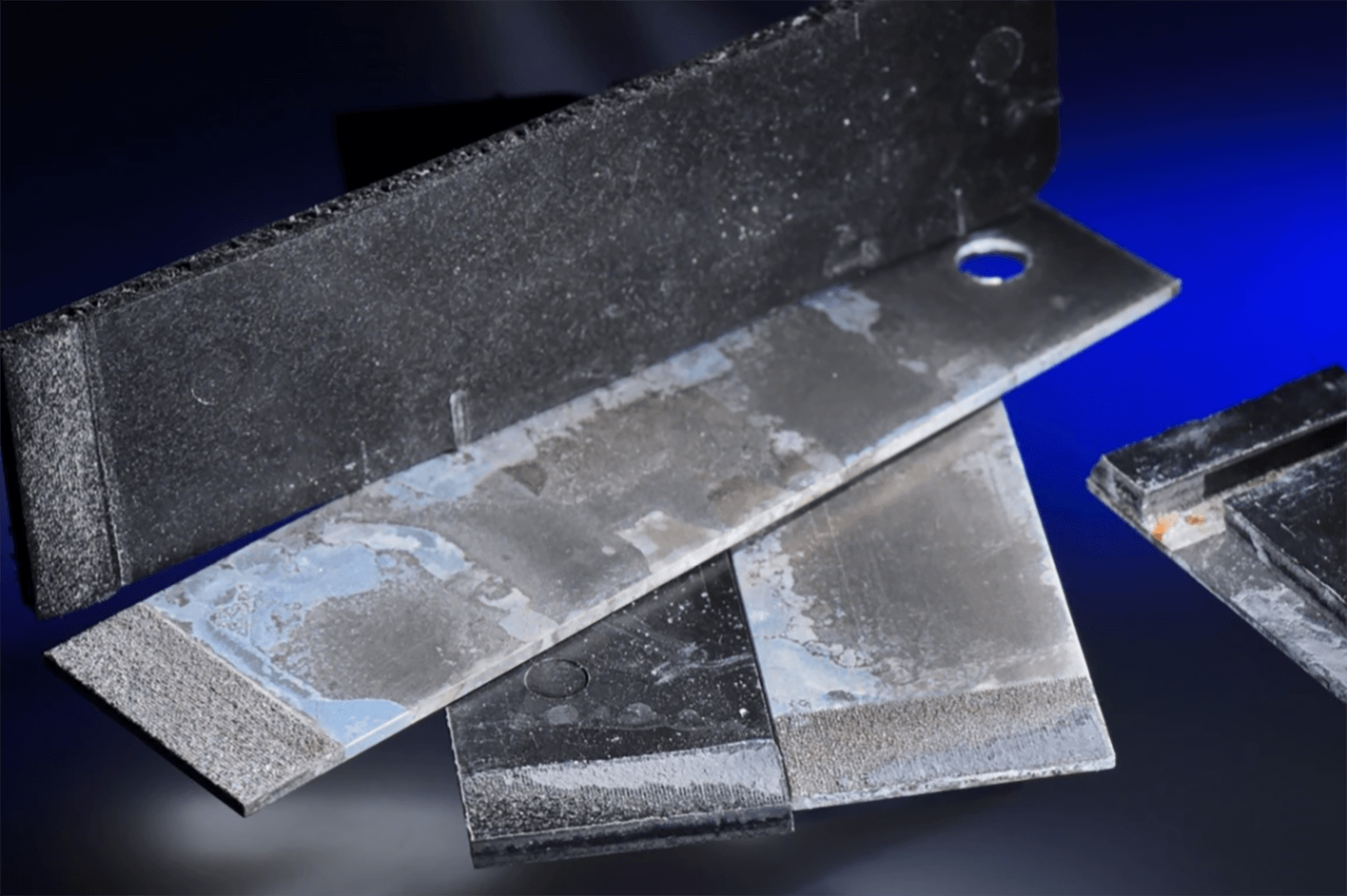
Fig. 4 Superfície de fratura da junta de metal e plástico após teste de corrosão
Um laser de fibra monomodo de 1 kW é utilizado para microprocessar a superfície do metal, com um diâmetro de ponto de aproximadamente 40 micrômetros. O laser produz uma estrutura de ranhura reproduzível na superfície do metal. O plástico é aquecido usando um laser semicondutor de potência nominal de 3 kW, com tamanho de ponto de 7,5 mm x 25 mm. As duas partes são fixadas com uma pressão de 0,3 MPa.
Os resultados dos testes são os seguintes:
- Para a ligação entre aço inoxidável e PP com fibra de vidro, a área de ligação é de 150 mm².
- Para a ligação entre aço inoxidável e PP a área de ligação é de 100 mm².
Testes destrutivos foram realizados em 5 amostras de cada um dos dois tipos acima.
Para a ligação entre aço inoxidável e PP com fibra de vidro foi realizado um ensaio de resistência ao cisalhamento. Os resultados são os seguintes:
- Quando o espaçamento entre ranhuras era de 400 micrômetros, a carga de cisalhamento máxima era de 13,1 MPa.
- Quando o espaçamento entre ranhuras era de 300 micrômetros, a carga de cisalhamento máxima era de 15,5 MPa.
Para a ligação entre aço inoxidável e PP foi realizado um ensaio de resistência à tração. Os resultados são os seguintes:
- Quando o espaçamento entre ranhuras era de 400 micrômetros, a carga de tração máxima era de 5,1 MPa.
- Quando o espaçamento entre ranhuras era de 300 micrômetros, a carga de tração máxima era de 9,1 MPa.
É evidente que uma distribuição densa de ranhuras melhora a resistência da conexão. No entanto, deve-se notar que uma distribuição densa de canais também aumentará o tempo de microusinagem.
Um experimento semelhante também foi conduzido em uma folha de magnésio.
Todos os testes demonstraram que a tecnologia de ligação baseada em laser cria uma conexão forte e confiável entre componentes metálicos e plásticos.
3. Teste de envelhecimento
Outra preocupação importante nos produtos automotivos é a sua resistência aos impactos das mudanças climáticas e da corrosão. Para responder a esta questão, especialistas do Hoff Laser Technology Institute, na Alemanha, realizaram vários testes.
No experimento, diversos metais (aço e alumínio) e plásticos (PP com 30% de fibra de vidro e PP com 40% de talco) foram conectados por meio de tecnologia laser. Para o teste de mudanças climáticas foi utilizado o padrão VW PV 1200, com temperaturas variando de 80°C a 40°C.
Cada ciclo de teste durou 12 horas e foi repetido duas vezes, 10 vezes e 30 vezes, respectivamente. A resistência ao cisalhamento destrutivo das amostras foi testada antes e depois de cada ciclo. Os resultados mostraram que todas as amostras apresentaram resistência ao cisalhamento variando de 8 a 15 MPa.
Uma observação interessante foi feita no teste: após 30 ciclos, todas as amostras de PP preenchidas com pó de talco apresentaram rachaduras fora da área de conexão durante o teste de resistência, indicando que a junta era mais resistente que o material PP a granel.
Resultado semelhante foi observado no teste de resistência à corrosão, que foi conduzido de acordo com a norma VDA 621-415 durante 7 dias, incluindo névoa salina e condições de alta umidade. Antes do teste, todas as amostras apresentavam resistência ao cisalhamento de 8-5 MPa. Após o teste de corrosão, o teste de cisalhamento mostrou que todas as amostras de PP contendo pó de talco apresentavam trincas fora da área de conexão, enquanto a amostra de PP contendo fibra de vidro quebrou na área da junta, mas sua resistência era maior do que antes do teste.
A corrosão foi observada no aço inoxidável, especialmente em sua microestrutura, e a área de ligação a laser mostrou penetração de corrosão óbvia, mas não teve efeito significativo na resistência de ligação. Também havia sinais de corrosão na microestrutura fora da área da junta, mas não dentro da área da junta.
Portanto, pode-se concluir que a microestrutura não deve ser exposta a ambientes abertos.
4. Conclusão
A técnica de conexão de metal e plástico usando tecnologia laser foi testada e demonstrou produzir conexões fortes e confiáveis. Os resultados dos testes climáticos e de corrosão não mostraram impacto na resistência da junta. Após passarem pelo envelhecimento, as amostras mostraram que as fraturas ocorreram no corpo plástico, e não no ponto de conexão.