Conexões de metal e polímero são estruturas leves ideais para automóveis. O processo de conexão eficaz entre materiais compósitos, como polímero reforçado com fibra de carbono (CFRP) ou polímero reforçado com fibra de vidro (GFRP) e componentes metálicos, tem recebido muita atenção com o surgimento de estruturas automotivas leves (ver Figura 1).
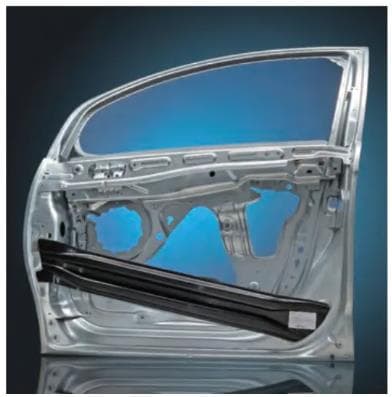
A ligação entre diferentes materiais é crucial para aspectos funcionais e de segurança na indústria automotiva.
Os requisitos da indústria automotiva são claros: o processo de colagem deve ser rápido, confiável e automatizado.
A Tabela 1 lista os três métodos mais comuns para conectar materiais compósitos e componentes metálicos em processos industriais, entre os quais a soldagem a laser pode ser o método mais recente, mas ainda precisa de mais pesquisas e melhorias. Estas questões não envolvem apenas eficiência, mas também envolvem a resistência e o envelhecimento das peças de conexão. Este artigo discutirá essas questões em detalhes.
Tabela 1: Métodos de conexão para materiais compósitos
Fixação Mecânica | Colagem adesiva | Soldagem a laser |
Vantagens:
– Processo rápido e barato – Tecnologia madura |
Vantagens:
– Vários adesivos para diferentes aplicações – Adequado para conectar materiais compósitos |
Vantagens:
– Processo rápido e confiável – Alta resistência articular – Não são necessários materiais adicionais |
Desvantagens:
– Furos podem comprometer a resistência das fibras e materiais compósitos – Peso adicional dos fixadores |
Desvantagens:
– Requer extensa preparação de superfície – Longo tempo de processamento – Requer materiais adicionais |
Desvantagens:
– Equipamento especializado necessário – Limitado a materiais termoplásticos |
Básico da tecnologia de soldagem a laser
O processo de soldagem a laser oculto para conectar materiais compósitos e peças metálicas consiste principalmente em duas etapas. Na primeira etapa, a peça metálica é tratada com laser para formar uma microestrutura em sua superfície.
Este processo pode ser alcançado usando um laser de fibra monomodo de onda contínua com potência nominal de cerca de 1 kW. O laser varre a superfície da peça metálica para formar uma ranhura regular com uma geometria de borda cortante (veja a Figura 2).
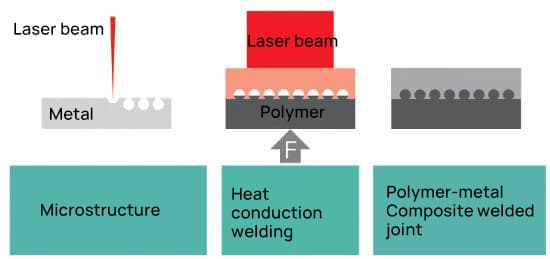
Devido à alta intensidade do feixe de laser, o metal derrete parcialmente e vaporiza durante o processo de ablação. A pressão evaporativa pulveriza o material, e parte do material respingado solidifica na borda da ranhura, formando um certo grau de estrutura de borda cortante na ranhura.
Para fazer com que o polímero se ligue mais à superfície metálica, a densidade da microestrutura da superfície pode ser aumentada, por exemplo, escaneando as ranhuras com o feixe de laser em um ângulo de 90° (ver Figura 3).
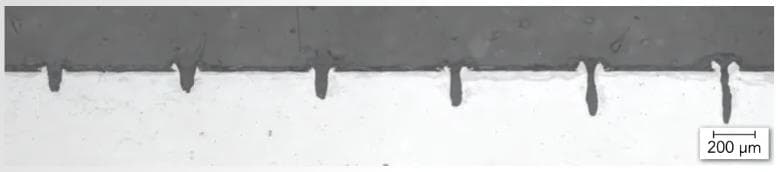
Existe outro processo que pode conseguir essa estruturação superficial. Este processo pode ser realizado usando lasers de pulso ultracurto (USP) para criar uma estrutura de superfície semelhante a uma esponja com saliências cônicas.
Esta estrutura de superfície pode ser obtida em vários materiais, como aço, alumínio, silício e titânio. A adesão do polímero nesta superfície é melhor que a da microestrutura produzida pelo processamento a laser de fibra. O único problema é que a velocidade de processamento dos lasers USP é mais lenta.
Uma vez que os lasers USP atingem a potência média do nível de quilowatts (como esperado em outro projeto Fraunhofer), eles podem ser uma escolha melhor para microestruturação de superfícies metálicas usadas para colagem de materiais compósitos.
Na segunda etapa de conexão de materiais compósitos com peças metálicas, o polímero é aquecido até derreter.
Em seguida, o polímero é pressionado na microestrutura da superfície da peça metálica e, após o resfriamento, consegue-se uma boa ligação entre o polímero e a peça metálica.
Existem diferentes métodos para aquecer o polímero: um método envolve aquecer o polímero (como na moldagem por injeção tradicional) e depois pressioná-lo na ranhura, enquanto outro método envolve aquecer a peça metálica e pressioná-la sobre o polímero frio.
A condução de calor faz com que o polímero derreta e flua para a microestrutura na superfície da peça metálica. Ambos os métodos podem formar uma conexão composta polímero-metal.
A primeira etapa da microestruturação a laser é um processo rápido e sem contato. O processo de conexão real pode ser facilmente integrado aos processos de produção existentes, como moldagem por injeção ou estampagem. Portanto, o método de soldagem a laser é geralmente um processo rápido e econômico, adequado para produção em massa.
Teste de estresse mecânico
Em aplicações práticas, peças compostas conectadas por metal e polímero podem estar sujeitas a cargas multiaxiais, em fase ou fora de fase. Para todas as aplicações, surgem diversas questões: quanta pressão essa junta pode suportar? Onde isso vai quebrar? O que isso significa para o processo de conexão?
Especialistas do Fraunhofer ILT na Alemanha realizaram uma série de testes de pressão utilizando diferentes materiais para responder a estas perguntas (ver Figura 4). Em um caso, eles fizeram um corpo de prova composto por uma placa de aço inoxidável com 1,5 mm de espessura e uma tira de polipropileno (PP) reforçado com fibra de vidro com 3 mm de espessura para testes de tração e cisalhamento, e um PP não reforçado para testes de tração.
A superfície metálica foi processada com um laser de fibra monomodo com potência nominal de 1 kW e diâmetro focalizado de cerca de 40 μm para formar uma estrutura de ranhura de borda cortante reproduzível. A parte do polímero foi aquecida com um laser semicondutor de 3 kW (potência de cerca de 300-700 W), com tamanho de ponto de 7,5×25 mm2. As duas peças foram fixadas entre si com uma pressão de fixação de 3 bar, e a área de ligação do corpo de prova de tração-cisalhamento (aço + PP) foi de 150 mm2enquanto o do corpo de prova de tração (aço + PP) foi de 100 mm2.
Cinco corpos de prova de cada tipo foram testados destrutivamente. A resistência da conexão da microestrutura com espaçamento entre ranhuras de 400 μm foi testada sob uma carga de tração e cisalhamento de 13,1 MPa, e a resistência da conexão com um espaçamento entre ranhuras de 300 μm foi medida sob uma carga de tração e cisalhamento de 15,5 MPa. No ensaio de carga de tração, os corpos de prova suportaram cargas de 5,1 MPa (espaçamento entre ranhuras de 400 μm) e 9,1 MPa (espaçamento entre ranhuras de 300 μm), respectivamente.
É claro que microestruturas densas apresentam melhor adesão, mas deve-se notar que microestruturas densas aumentarão o tempo de processamento.
Os pesquisadores realizaram testes semelhantes em placas de liga de magnésio. Todos os resultados dos testes mostraram que a tecnologia de soldagem a laser pode estabelecer uma conexão forte e confiável entre peças de metal e polímero.
Teste de envelhecimento
Outra questão na produção de automóveis é se tais conexões podem atender aos requisitos das mudanças climáticas e da corrosão.
Para responder a esta pergunta, os pesquisadores realizaram vários testes. Eles realizaram testes padrão de mudanças climáticas em amostras de conexão composta de acordo com VW PV 1200, com temperatura variando de 80-40°C.
Um ciclo de teste durou 12 horas, repetido por 2, 10 e 30 ciclos. Testes destrutivos de resistência à tração e cisalhamento foram realizados nas amostras antes e depois do teste de mudanças climáticas.
Todos os resultados dos testes mostraram que as amostras poderiam suportar valores de pressão entre 8-15 MPa. Um fenômeno interessante ocorreu fora da área de colagem durante o teste.
Depois de repetir o teste por 30 ciclos, as peças fora da área de colagem falharam no teste de resistência. Em outras palavras, a área de ligação era ainda mais resistente que a do material original de polipropileno.
Este fenômeno foi ainda mais pronunciado no teste de corrosão. O teste de névoa salina foi realizado durante 7 dias de acordo com VDA62I-415. O teste incluiu névoa salina e condições de alta umidade. Antes do teste, todos os corpos de prova podiam suportar forças de cerca de 8 MPa e 15 MPa.
Após o teste de corrosão, todos os materiais PP/T40 quebraram fora da área de ligação, enquanto os materiais GFRP quebraram dentro da área de ligação, mas com maior resistência do que antes da corrosão. Os corpos de prova de aço apresentaram ferrugem, principalmente na área da microestrutura.
Houve penetração óbvia de corrosão na área de ligação, mas isso não afetou significativamente a resistência da ligação. A área da microestrutura fora da área de colagem da placa de alumínio também apresentou sinais de corrosão, mas não dentro da área de colagem. Uma conclusão direta é que quaisquer áreas abertas de microestrutura no metal devem ser evitadas.
Os testes mostraram que a tecnologia de conexão a laser pode estabelecer conexões altamente confiáveis entre placas metálicas e plásticos.
Os testes padrão de clima e corrosão não afetaram a resistência da adesão. Após um período de envelhecimento, o próprio plástico, e não a área de colagem, quebrou. Devem ser evitadas áreas abertas de microestrutura no metal.