El rover Curiosity de la NASA, valorado en 2.500 millones de dólares, está listo para capturar los detalles más finos del planeta Marte. El rover está diseñado para observar con gran precisión las condiciones ambientales, incluida la presión atmosférica y la fuerza gravitacional. Para ello se equipó su Unidad de Control Instrumental o UCI con sensores de presión. Estos sensores ayudarán a detectar los remolinos de polvo que son una característica del planeta y también detallarán la concentración de diferentes gases en la atmósfera en diferentes puntos. Echemos un vistazo a qué hace que un sensor de presión sea lo suficientemente capaz para realizar tareas tan específicas y dónde más se puede utilizar.
Un sensor de presión es un dispositivo que detecta la presión y la convierte en una señal eléctrica analógica cuya magnitud depende de la presión aplicada. Como convierten la presión en una señal eléctrica, también se les llama transductores de presión.
Necesidad de sensores de presión.
Desde hace mucho tiempo, los sensores de presión se han utilizado ampliamente en áreas como la automoción, la fabricación, la aviación, las mediciones biomédicas, el aire acondicionado, las mediciones hidráulicas, etc. Algunas áreas destacadas donde el uso de sensores de presión es inevitable son:
1. Dispositivos con pantalla táctil: Los dispositivos informáticos y los teléfonos inteligentes que tienen pantallas táctiles vienen con sensores de presión. Cada vez que se aplica una ligera presión a la pantalla táctil con un dedo o un lápiz, el sensor determina dónde se aplicó y, en consecuencia, genera una señal eléctrica que informa al procesador. Normalmente, estos sensores están ubicados en las esquinas de la pantalla. Por lo tanto, cuando se aplica presión, normalmente actúan dos o más sensores para proporcionar información de ubicación precisa.
2. Industria Automotriz: En la industria automotriz, los sensores de presión son parte integral del motor y su seguridad. En el motor, estos sensores monitorean la presión del aceite y del refrigerante y regulan la potencia que el motor debe entregar para alcanzar las velocidades apropiadas cada vez que se presiona el acelerador o se aplican los frenos al automóvil.
Por motivos de seguridad, los sensores de presión forman una parte importante del sistema de frenos antibloqueo (ABS). Este sistema se adapta al terreno de la carretera y consigue que, al frenar a alta velocidad, los neumáticos no se bloqueen y el vehículo no patine. Los sensores de presión en el ABS informan al procesador sobre las condiciones de la carretera, así como la velocidad a la que se mueve el vehículo.
Los sistemas de bolsas de aire también utilizan sensores de presión para que las bolsas de aire se activen para garantizar la seguridad de los pasajeros cada vez que el vehículo siente una gran presión.
3. Instrumentación Biomédica: En instrumentos como tensiómetros digitales y ventiladores, se requieren sensores de presión para optimizarlos según la salud y las necesidades del paciente.
4. Usos industriales: Los sensores de presión se utilizan para monitorear gases y sus presiones parciales en unidades industriales para que puedan ocurrir grandes reacciones químicas en condiciones ambientales controladas con precisión. En la industria petrolera, los sensores detallan la profundidad que ha alcanzado la plataforma petrolera durante la exploración.
5. Aviación: En los aviones, estos sensores son necesarios para mantener un equilibrio entre la presión atmosférica y los sistemas de control del avión. Esto no sólo protege los circuitos de la aeronave y diversos componentes internos, sino que también proporciona al sistema datos precisos sobre el entorno externo. Además, es necesario mantener niveles específicos de presión de aire en la cabina y en el vestíbulo de pasajeros para proporcionar condiciones respiratorias nominales.
6. Industria Marina: Para barcos y submarinos, se necesitan sensores de presión para estimar la profundidad a la que están operando y detallar las condiciones marinas para que los sistemas electrónicos puedan permanecer seguros. Las necesidades de oxígeno en proyectos submarinos también se regulan mediante sensores de presión.
Tipos de mediciones de presión
La medición de la presión puede ser relativa a un valor de referencia o en una escala absoluta.
1. Medición de presión absoluta: La presión medida en relación al vacío perfecto se llama
como presión absoluta. El vacío perfecto es una condición en la que no hay materia presente en la atmósfera y, por tanto, no hay presión de aire en esa región. Los sensores de presión absoluta tienen un uso limitado porque es imposible lograr un estado de vacío perfecto. En consecuencia, los sensores basados en la medición de presión absoluta requieren especificaciones estrictas para obtener resultados precisos. Los sensores basados en este tipo de medición se utilizan en mediciones de presión barométrica o relacionada con la altitud.
dos. Medición de presión diferencial: en la medición de presión diferencial se comparan presiones de dos posiciones diferentes. Por ejemplo, la diferencia de presión calculada midiéndola en diferentes pisos de un edificio alto nos dará la presión diferencial. Las mediciones de presión diferencial, generalmente realizadas en libras por pulgada cuadrada (psid), se aplican cuando se debe medir una gran cantidad de presión. Este tipo de mediciones se utilizan para monitorear la presión de suministro, donde se monitorea la presión a la que fluye el fluido en un medio, de modo que se pueda mantener la homogeneidad en el flujo.
Las mediciones de presión diferencial encuentran una aplicación importante en el monitoreo de filtros en varios tipos de sistemas de purificación. Toman como referencia la presión normal a la que los filtros limpian el fluido. Siempre que los filtros enfrentan el problema de obstrucción debido a contaminantes, estos sensores de presión proporcionan una lectura relativa a la presión normal. Esto ayuda a mantener el filtro limpio y operativo.
3. Medición de presión manométrica: Se puede definir como un subtipo de medición de presión diferencial donde comparamos la presión en cualquier punto con la presión atmosférica actual. La medición de la presión manométrica se utiliza en aplicaciones como la medición de la presión de los neumáticos o la presión arterial. No hay consistencia en las mediciones de presión manométrica porque la presión atmosférica varía con la altitud y, por lo tanto, sus aplicaciones se limitan a mediciones no críticas.
Tipos de sensores de presión
Tipos de sensores de presión
Según el tipo de aplicaciones en las que se utilizan, los sensores de presión se pueden clasificar en varios tipos. Sin embargo, los siguientes son los tipos más comunes de sensores de presión que se han utilizado ampliamente:
1. Tipo de medidor de tensión: estos sensores son similares a un puente de piedra de trigo en su funcionamiento. En el puente de piedra de trigo, la relación de resistencias de dos brazos adyacentes conectados a un extremo de la batería debe ser igual a la de los otros dos brazos conectados al otro extremo de la batería. Cuando las dos proporciones son iguales, el puente de piedra de trigo no genera producción. En el caso de un extensómetro, un brazo de puente de piedra de trigo está conectado a un diafragma. El diafragma se comprime y expande debido a la presión aplicada. Esta variación en el diafragma hace que varíe la salida en el puente. Se generaría un voltaje proporcional a cada desviación de la condición de equilibrio normal, de modo que cada movimiento de compresión o expansión del diafragma producirá una salida que indicará un cambio en las condiciones de presión. Dado que el cambio de resistencia es la causa principal de la diferencia de potencial, estos sensores también se denominan sensores de presión de tipo piezoresistivo.
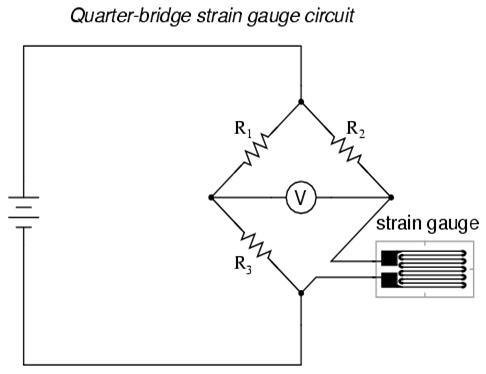
Figura 1: Diagrama del circuito del sensor de presión del extensómetro de cuarto de puente
dos. Sensor de presión capacitivo: un condensador tiene dos placas de metal y un dieléctrico intercalado entre ellas. En el sensor de presión capacitivo, una de estas placas metálicas puede moverse hacia adentro y hacia afuera para que la capacitancia entre ellas cambie debido a la variación en la distancia entre las placas. La placa móvil está conectada a un diafragma que detecta la presión y luego se expande o comprime en consecuencia. El movimiento del diafragma afectaría la posición de la placa metálica fija y la capacitancia podría variar.
Estos sensores, aunque son muy ineficaces a altas temperaturas, se utilizan ampliamente en el rango de temperatura ambiente debido a su salida lineal.
Figura 2: Diagrama que muestra la estructura interna del sensor de presión capacitivo
3. Sensor de presión piezoeléctrico: los cristales piezoeléctricos desarrollan una diferencia de potencial (es decir, se induce voltaje en las superficies) cada vez que se someten a cualquier presión mecánica. Estos sensores tienen el cristal montado sobre una base dieléctrica para que no haya fugas de corriente. Unido al cristal hay un eje horizontal al que está conectado un diafragma. Cada vez que el diafragma detecta presión, empuja el eje hacia abajo, lo que presuriza el cristal y se produce voltaje.
Figura 3: Imagen que muestra detalles del sensor de presión piezoeléctrico
Especificaciones, limitaciones y desafíos.
Especificaciones del sensor de presión
Como los sensores de presión tienen diversas aplicaciones, se adoptan ciertas especificaciones para que funcionen de manera óptima en un entorno particular. Algunas de las configuraciones principales se enumeran a continuación:
1. Rango de medición: Define la presión mínima y máxima entre las cuales el sensor está diseñado para operar sin sufrir daños. Este criterio es más esencial para los sensores diferenciales y manométricos, ya que sus mediciones son relativas y si la magnitud de la presión de referencia está fuera de su rango, no funcionarán.
dos. Temperatura de funcionamiento: Es el rango de temperatura bajo el cual el sensor funciona de manera óptima. Siempre es necesario hacer funcionar el sensor dentro del rango de temperatura establecido para que la salida sea consistente. En condiciones ambientales extremadamente cálidas o frías, es posible que los sensores no funcionen correctamente. Esto se aplica especialmente en el caso de los sensores de presión electrónicos que se utilizan en ordenadores con pantalla táctil y otros dispositivos.
3. Dimensiones del sensor: según la aplicación, el tamaño del sensor varía según el tipo de área donde se debe detectar presión. En consecuencia, las dimensiones del sensor son una consideración importante durante el diseño del sensor. Normalmente, se prefieren sensores de tamaño pequeño, ya que pueden instalarse fácilmente en lugares difíciles, como filtros de aire.
4. Tipo de medición: También es importante que el usuario sepa qué tipo de medición de presión está realizando el sensor: absoluta, manométrica o diferencial. Esto se debe a que diferentes técnicas de medición son seguidas por diferentes métodos de procesamiento y, por lo tanto, los resultados varían en consecuencia.
5. Precisión: Las mediciones de presión diferencial son la mejor manera de hacer que un sensor sea lo más preciso posible. Esto se debe a que la presión de referencia está más bajo el control del usuario que la atmósfera, como es el caso al medir la presión manométrica.
6. Repetibilidad: Esto se puede definir como la capacidad del sensor para producir el mismo resultado cuando se aplica repetidamente una cantidad específica de presión. La repetibilidad es una de las especificaciones más importantes de un sensor. Debido a que los sensores son de rango específico, la probabilidad de que sean calibrados a la misma presión es alta; por lo tanto, el sensor debe reproducir los resultados para la misma cantidad de presión, repetidamente.
7. Tipo de salida generada: La salida eléctrica generada por el sensor puede ser de varios tipos dependiendo de su diseño y de cuál sea el dispositivo de salida final. Algunos formatos conocidos en los que se genera salida son voltaje analógico; corriente analógica, señal digital (TTL), Interfaz RS232 y protocolo HART basado en conmutación de frecuencia.
8. Tiempo de respuesta: Esto denota el tiempo que transcurre entre los insumos aplicados y el resultado obtenido. Se espera que los sensores de presión tengan un tiempo de respuesta corto para que se puedan generar resultados instantáneos y, en el caso de variaciones rápidas de presión, el sistema también pueda responder rápidamente.
9. Voltaje de compensación: el voltaje de compensación se puede denominar como el voltaje de salida generado cuando no se aplica ninguna entrada. En el caso de los sensores diferenciales, los voltajes de desplazamiento se generan cuando no hay presión de referencia, y en el caso de la presión manométrica, se generan cuando se aplica presión ambiental al sensor. Los voltajes de compensación son necesarios para reducir el error en la salida y las salidas finales se calculan después de restarles los voltajes de compensación.
Limitaciones y desafíos:
Los sensores de presión tienen varias limitaciones que restringen su uso en diferentes áreas. La dependencia de la alta temperatura, la histéresis, la incapacidad de deducir variaciones rápidas y dinámicas de presión, la sensibilidad a las vibraciones externas, la irreparabilidad del conjunto de la placa electrónica, la sensibilidad a los campos eléctricos, magnéticos y de RF, las incompatibilidades con dispositivos externos son algunos de los desafíos que puede enfrentar un sensor en general. caras de presión. En algunas aplicaciones, los sensores de presión tienen una precisión limitada. Por ejemplo, en una pantalla táctil, la sensibilidad del sensor cuando se toca múltiples veces se ve afectada, mientras que en el sector de la aviación la alta presión puede limitar el funcionamiento del sensor.
Los sensores de presión son esencialmente necesarios para que un dispositivo responda de manera óptima a sus condiciones ambientales. Sus tipos y usos son muchos y seguirán evolucionando a medida que madure la tecnología de sensores. El uso extensivo de sensores de presión, como en pantallas táctiles o automóviles, degrada rápidamente su eficiencia y, por lo tanto, la robustez de los sensores de presión es también una prioridad creciente de la investigación industrial. Sin embargo, las herramientas con sensores de presión, y como ocurre con todas las demás herramientas, deben utilizarse con cuidado y comprobarse constantemente para garantizar resultados de calidad.