I. Eliminación de residuos
Después de soldar la pieza de trabajo, si se utilizan soldadura con gas o varillas de soldadura con núcleo fundente, es necesario limpiar inmediatamente el fundente y la escoria residuales de la soldadura y el área circundante antes de realizar una inspección visual y pruebas no destructivas.
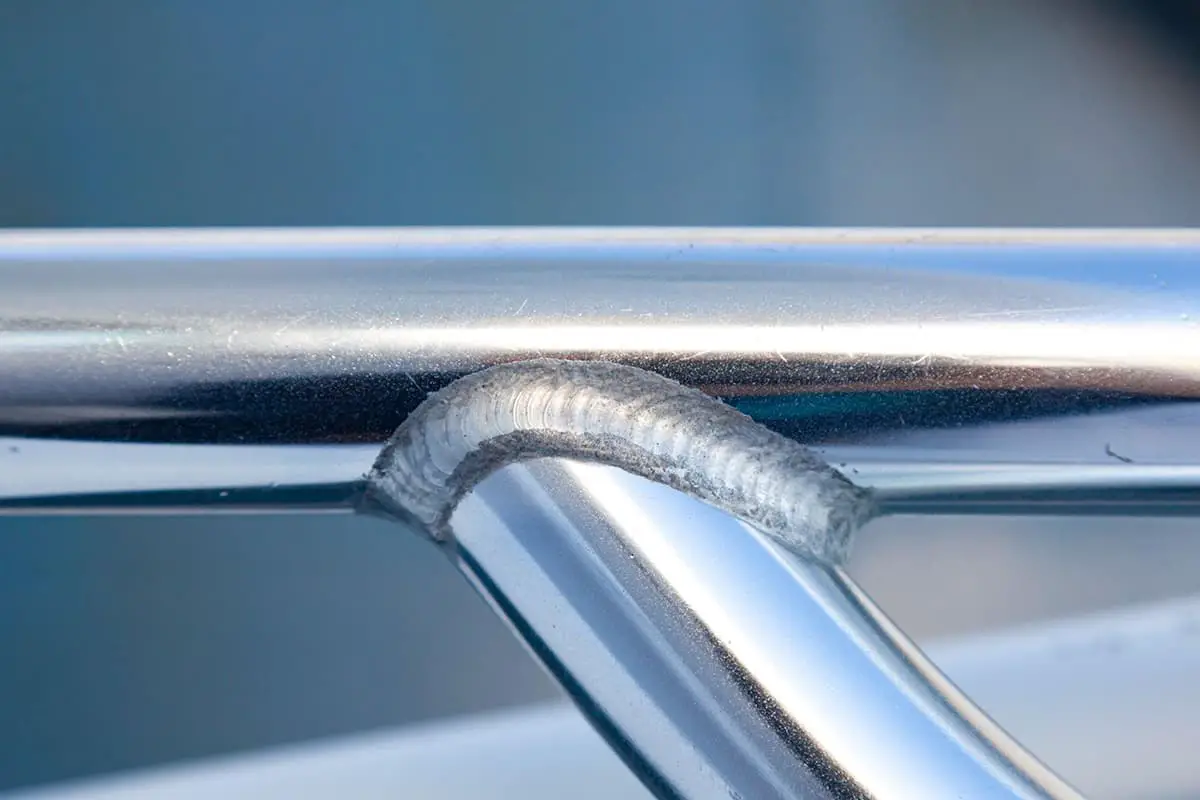
Este paso previene la corrosión de la soldadura y su superficie por escorias y fundentes residuales, evitando consecuencias indeseables. Los métodos comunes para la limpieza posterior a la soldadura son los siguientes:
(1) Frote en agua caliente entre 60°C y 80°C;
(2) Inmersión en dicromato de potasio (K2Cr2O2) o de 2% a 3% de anhídrido crómico (Cr2O2);
(3) Enjuague adicional en agua caliente entre 60°C y 80°C;
(4) Secado al horno o al aire.
Para probar la eficacia de eliminar el fundente residual, se puede colocar agua destilada sobre la soldadura de la pieza de trabajo. Luego se recoge el agua destilada y se coloca en un tubo de ensayo que contiene una solución de ácido nítrico al 5%. Si aparece un precipitado blanco, indica que el fundente residual no se ha eliminado por completo.
II. Tratamiento de superficies de soldadura
Mediante un proceso de soldadura adecuado y técnicas de operación correctas, la superficie de las soldaduras de aluminio y aleaciones de aluminio después de la soldadura tiene una apariencia uniforme, suave y sin ondulaciones.
El anodizado, especialmente cuando se combina con técnicas de pulido y teñido, da como resultado superficies decorativas de alta calidad. Se puede minimizar la zona afectada por el calor de la soldadura, reduciendo al mínimo los cambios de color inducidos por la anodización. Los procesos de soldadura rápidos pueden reducir significativamente la zona afectada por el calor. En consecuencia, la calidad del tratamiento de anodizado en las costuras soldadas por flash es buena.
Especialmente para piezas de soldadura de aleaciones que no pueden tratarse térmicamente para fortalecerlas en estado recocido, el contraste de color entre el metal base y la zona afectada por el calor es mínimo después de la anodización. La soldadura fuerte en horno e inmersión, que no implica calentamiento localizado, produce una apariencia de color metálico muy uniforme.
Las aleaciones que pueden tratarse térmicamente para reforzarlas, utilizadas a menudo en partes estructurales de edificios, suelen anodizarse después de soldarse. En estas aleaciones, el calor de las formas de soldadura precipita en los elementos de aleación.
Después del anodizado, aparecerán diferencias entre la zona afectada por el calor y la costura de soldadura. Estas zonas de halo cercanas al área de soldadura se pueden minimizar mediante una soldadura rápida o mediante el uso de bloques de enfriamiento y placas de sujeción. Estas zonas de halo, antes del anodizado y después de la soldadura, se pueden eliminar mediante un tratamiento de endurecimiento por precipitación.
Al tratar químicamente piezas soldadas, pueden producirse diferencias de color significativas entre el metal de soldadura y el metal base. Esto requiere una selección cuidadosa de la composición del metal de aportación, especialmente cuando contiene silicio, lo que puede afectar la combinación de colores.
Si es necesario, la soldadura se puede pulir mecánicamente. Los métodos comunes de pulido mecánico incluyen pulido, esmerilado, chorro abrasivo y chorro de arena. El pulido mecánico mejora la superficie de las piezas de aluminio mediante métodos físicos como esmerilado, desbarbado, pulido, pulido o arenado. El objetivo es conseguir la calidad superficial deseada en el menor número de pasos posible.
Sin embargo, el aluminio y sus aleaciones son metales blandos con altos coeficientes de fricción. El sobrecalentamiento durante el proceso de rectificado puede provocar potencialmente la deformación de las piezas soldadas o incluso provocar fracturas en los límites de grano del metal base. Por lo tanto, se requiere suficiente lubricación durante el proceso de pulido y se debe minimizar la presión sobre la superficie del metal.
III. Posterior a la soldadura de tratamiento térmico
El objetivo del tratamiento térmico post-soldadura es mejorar la estructura y el rendimiento de la unión soldada o eliminar tensiones residuales. Las aleaciones de aluminio tratables térmicamente pueden someterse a un tratamiento térmico posterior a la soldadura, restaurando la resistencia de la zona afectada por el calor del metal base cerca de su resistencia original.
Generalmente, el punto de falla de la unión ocurre dentro de la zona de fusión de la soldadura. Después del tratamiento térmico post-soldadura, la resistencia adquirida por el metal de soldadura depende principalmente del metal de aportación disperso.
1. Características de la soldadura de aluminio y aleaciones de aluminio.
(1) El aluminio se oxida fácilmente en el aire y durante la soldadura, formando óxido de aluminio (Al2O3) que tiene un alto punto de fusión y es extremadamente estable, lo que dificulta su eliminación. Esto evita que el material original se derrita y se fusione. La gran gravedad específica de la película de óxido impide que flote en la superficie, lo que provoca defectos como inclusiones de escoria, falta de fusión y penetración incompleta.
La película de óxido superficial del aluminio y la humedad absorbida pueden provocar porosidad en la costura de soldadura. Antes de soldar, la superficie debe limpiarse a fondo utilizando métodos químicos o mecánicos para eliminar la película de óxido. Se debe reforzar la protección durante la soldadura para evitar la oxidación.
Durante la soldadura con gas inerte de tungsteno (TIG), se debe utilizar una fuente de alimentación de corriente alterna para eliminar la película de óxido mediante una “limpieza catódica”. Al soldar con gas, se debe utilizar un fundente que elimine la película de óxido. Al soldar placas gruesas, el calor de soldadura puede aumentar. Por ejemplo, el arco de helio tiene mucho calor, por lo que se utiliza helio o gas de protección mixto argón-helio, o soldadura por arco metálico con gas de gran diámetro (GMAW) con corriente directa positiva, lo que elimina la necesidad de “limpieza catódica”.
(2) La conductividad térmica y el calor específico del aluminio y sus aleaciones son más del doble que los del acero al carbono y el acero de baja aleación. La conductividad térmica del aluminio es decenas de veces mayor que la del acero inoxidable austenítico.
Durante el proceso de soldadura, se puede transferir rápidamente una gran cantidad de calor al metal base, por lo tanto, al soldar aluminio y sus aleaciones, además de la energía consumida al fundir la piscina de metal, se desperdicia más calor en otras partes del metal. . Este desperdicio de energía es más importante que en la soldadura de acero. Para obtener uniones soldadas de alta calidad, se deben utilizar en la medida de lo posible fuentes de energía concentradas y de alta potencia. También se pueden utilizar precalentamiento y otras medidas de proceso.
(3) El coeficiente de expansión lineal del aluminio y sus aleaciones es aproximadamente el doble que el del acero al carbono y el del acero de baja aleación. El aluminio exhibe una contracción volumétrica significativa durante la solidificación, lo que provoca una deformación y tensión sustanciales durante la soldadura. Por lo tanto, se deben emplear medidas para evitar la deformación de la soldadura. La solidificación de un charco de soldadura de aluminio tiende a provocar cavidades por contracción, porosidad, agrietamiento en caliente y tensiones internas elevadas.
Para evitar la aparición de grietas por calor, la producción puede ajustar la composición del alambre de soldadura y el proceso de soldadura. En situaciones resistentes a la corrosión, se puede utilizar alambre de soldadura de aleación de aluminio y silicio para soldar aleaciones de aluminio, excluidas las aleaciones de aluminio y magnesio.
En las aleaciones de aluminio-silicio, la tendencia al craqueo en caliente es considerable cuando el contenido de silicio es del 0,5%. A medida que aumenta el contenido de silicio, el rango de temperatura de cristalización de la aleación disminuye, su fluidez mejora significativamente y su tasa de contracción disminuye, reduciendo en consecuencia la tendencia al craqueo en caliente.
Según la experiencia de producción, cuando el contenido de silicio es del 5% al 6%, no se produce agrietamiento en caliente, por lo tanto, el uso de alambre SAlSi (con un contenido de silicio del 4,5% al 6%) proporciona una mejor resistencia al agrietamiento.
(4) El aluminio tiene una fuerte reflectividad de la luz y el calor. Durante la transición del estado sólido al líquido, no se nota ningún cambio de color, lo que dificulta su evaluación durante el proceso de soldadura. El aluminio de alta temperatura tiene muy baja resistencia, lo que dificulta el soporte del baño de soldadura y es propenso a quemaduras.
(5) El aluminio y sus aleaciones pueden disolver una cantidad significativa de hidrógeno en estado líquido, pero casi nada en estado sólido. Durante la solidificación y el enfriamiento rápido del baño de soldadura, el hidrógeno no tiene tiempo de escapar, lo que conduce a la formación de porosidad de hidrógeno.
La humedad en la atmósfera del arco, los materiales de soldadura y la humedad adsorbida en la película de óxido superficial del material base son fuentes importantes de hidrógeno en la costura de soldadura. Por lo tanto, es necesario un control estricto de las fuentes de hidrógeno para evitar la formación de porosidad.
(6) Los elementos de aleación tienden a evaporarse y quemarse, reduciendo el rendimiento de la costura de soldadura.
(7) Si el metal base del material base se endurece por deformación o se trata con solución térmica, el calor de la soldadura puede reducir la resistencia de la zona afectada por el calor.
(8) El aluminio, que tiene una red cúbica centrada en las caras y no tiene formas alotrópicas, no sufre transición de fase durante el calentamiento y el enfriamiento. Esto da lugar a granos gruesos en la soldadura, que no pueden refinarse mediante transiciones de fase.
2. Métodos de soldadura
Casi todos los métodos de soldadura se pueden utilizar para soldar aluminio y sus aleaciones. Sin embargo, la adaptabilidad del aluminio y sus aleaciones a diferentes métodos de soldadura varía y cada método tiene sus propias aplicaciones.
La soldadura con gas y la soldadura por arco metálico protegido son simples y convenientes. La soldadura con gas se puede utilizar para reparar uniones en láminas de aluminio y piezas fundidas donde los requisitos de calidad no son altos. La soldadura por arco metálico protegido se puede utilizar para reparar piezas fundidas de aleaciones de aluminio.
La soldadura con gas protector (TIG o MIG) es el método más utilizado para soldar aluminio y sus aleaciones. Las láminas de aluminio y las aleaciones de aluminio se pueden soldar mediante soldadura con gas inerte de tungsteno de corriente alterna o soldadura con gas inerte de tungsteno pulsado.
Las placas de aluminio y aleaciones de aluminio se pueden soldar mediante soldadura por arco de helio y tungsteno, soldadura con gas inerte de tungsteno con una mezcla de argón y helio, soldadura con gas inerte de metal y soldadura con gas inerte de metal pulsado. Cada vez está más extendida la aplicación de la soldadura de metales con gas inerte y de la soldadura de metales con gas inerte pulsado (argón o mezcla de argón y helio).
3. Materiales de soldadura
(1) Alambre de soldadura
Además de considerar el buen desempeño del proceso de soldadura, la selección de alambres de soldadura de aluminio y aleación de aluminio debe garantizar que la resistencia a la tracción y la plasticidad (mediante pruebas de flexión) de las juntas a tope cumplan con los requisitos especificados de acuerdo con los requisitos del recipiente.
Se deben cumplir los requisitos de resistencia al impacto para las aleaciones de aluminio y magnesio con un contenido de magnesio superior al 3%. Para recipientes con requisitos de resistencia a la corrosión, la resistencia a la corrosión de la junta soldada debe alcanzar o estar cerca del nivel del material base. Por tanto, la selección del alambre de soldadura se basa principalmente en las propiedades del aluminio.
1) La pureza del alambre de soldadura de aluminio puro generalmente no es inferior a la del material original;
2) La composición química del alambre de soldadura de aleación de aluminio es generalmente similar o cercana a la del material original;
3) El contenido de elementos resistentes a la corrosión (magnesio, manganeso, silicio, etc.) en el alambre de soldadura de aleación de aluminio generalmente no es inferior al del material original;
4) Al soldar diferentes tipos de materiales de aluminio, elija el alambre de soldadura basándose en el material original más fuerte y resistente a la corrosión;
5) Las aleaciones de aluminio de alta resistencia (aleaciones de aluminio reforzadas con tratamiento térmico) que no requieren resistencia a la corrosión pueden usar alambres de soldadura de diferentes composiciones, como alambres de soldadura de aleación de aluminio y silicio resistentes a grietas como SAlSi-1 (tenga en cuenta que el La resistencia puede ser menor que la del material original).
(2) Gas protector
El gas protector es argón, helio o una mezcla de ellos. Para soldadura TIG de corriente alterna de alta frecuencia, utilice más del 99,9% de argón puro. La soldadura de corriente continua de polaridad positiva es adecuada para helio.
En soldadura MIG se recomienda utilizar argón con la adición de un 50% a un 75% de helio cuando el espesor de la placa sea de 75 mm. El argón debe cumplir los requisitos de GB/T 4842-1995 “Argón puro”. La presión del cilindro de argón es insuficiente y no se puede utilizar cuando es inferior a 0,5 MPa.
(3) Electrodos de tungsteno
En la soldadura por arco de argón se utilizan cuatro tipos de electrodos de tungsteno: tungsteno puro, tungsteno toriado, tungsteno de cerio y tungsteno de circonio. Los electrodos de tungsteno puro tienen puntos de fusión y ebullición altos, lo que los hace menos propensos a derretirse, evaporarse, quemarse los electrodos y contaminarse la punta.
Sin embargo, tienen una menor capacidad de emisión de electrones. Los electrodos de tungsteno toriado, fabricados añadiendo entre un 1% y un 2% de óxido de torio al tungsteno puro, tienen una mayor capacidad de emisión de electrones, permiten una mayor densidad de corriente y mantienen un arco más estable. Sin embargo, el torio es ligeramente radiactivo, por lo que se deben tomar medidas de protección adecuadas durante su uso.
Los electrodos de cerio-tungsteno se fabrican añadiendo entre un 1,8% y un 2,2% de óxido de cerio (con impurezas ≤0,1%) al tungsteno puro. Estos electrodos tienen baja función de trabajo electrónico, alta estabilidad química, permiten alta densidad de corriente y no tienen radioactividad. Son los electrodos más utilizados en la actualidad.
Los electrodos de circonio y tungsteno pueden evitar la contaminación del electrodo de metal base. Sus puntas son fáciles de mantener y tienen forma semiesférica, lo que las hace adecuadas para soldadura CA.
(4) Flujo
El fundente utilizado en la soldadura con gas se compone de cloruros y fluoruros de elementos como potasio, sodio, litio y calcio, que pueden eliminar la película de óxido.
4. Preparación antes de soldar
(1) Limpieza previa a la soldadura
Antes de soldar aluminio y sus aleaciones, es imprescindible retirar cuidadosamente la película de óxido y grasa de la línea de soldadura de la pieza y de la superficie del hilo de soldadura.
La calidad de esta limpieza incide directamente en el proceso de soldadura y en la calidad de la unión, como por ejemplo la tendencia a generar porosidad en la soldadura y diversas propiedades mecánicas. Esta limpieza normalmente se logra mediante métodos de limpieza químicos o mecánicos.
1) Limpieza Química
La limpieza química es muy eficiente y de calidad constante, lo que la hace adecuada para limpiar alambres de soldadura y piezas pequeñas producidas en masa. La inmersión y el fregado son dos métodos comunes.
Para desengrasar las superficies se utilizan disolventes orgánicos como acetona, gasolina y queroseno, seguido de un lavado alcalino utilizando una solución de NaOH del 5 % al 10 % a entre 40 °C y 70 °C durante 3 a 7 minutos (más tiempo para el aluminio puro, pero sin exceder). 20 minutos), luego enjuague con agua corriente.
Posteriormente se realiza un lavado ácido con una solución de HNO3 al 30%, a temperatura ambiente hasta 60°C, durante 1 a 3 minutos, seguido de otro enjuague con agua corriente y secado con aire o baja temperatura.
2) Limpieza Mecánica
La limpieza mecánica se utiliza a menudo cuando la pieza de trabajo es grande, el ciclo de producción es largo, se trata de soldadura multicapa o cuando la pieza de trabajo se vuelve a contaminar después de una limpieza química.
Primero, se utilizan disolventes orgánicos como acetona o gasolina para desengrasar la superficie, seguido de un cepillo con un cepillo de cobre o acero inoxidable de 0,15 mm a 0,2 mm de diámetro hasta que se revela un brillo metálico.
Generalmente se desaconseja el uso de muelas abrasivas o papel de lija común para evitar que queden granos de arena en la superficie del metal, que podrían ingresar al baño de soldadura durante la soldadura y causar inclusiones de escoria u otros defectos. Alternativamente, se pueden utilizar raspadores o limas para limpiar la superficie a soldar.
Después de limpiar la pieza y el alambre de soldadura, reaparecerá una película de óxido durante el almacenamiento, especialmente en ambientes húmedos o contaminados por vapores ácidos o básicos, donde la película de óxido crece aún más rápido.
Por tanto, se debe minimizar el tiempo de almacenamiento desde el final de la limpieza hasta el inicio de la soldadura. En condiciones de humedad, la soldadura generalmente debe realizarse dentro de las 4 horas posteriores a la limpieza. Si el tiempo de almacenamiento después de la limpieza es demasiado largo (por ejemplo, supera las 24 horas), se debe repetir el proceso de limpieza.
(2) Placa de respaldo
El aluminio y sus aleaciones presentan baja resistencia a altas temperaturas y el aluminio fundido fluye fácilmente, lo que provoca un posible colapso del metal de soldadura durante la soldadura. Para garantizar una penetración completa sin colapso, a menudo se utilizan placas de respaldo para soportar el baño de soldadura y el metal adyacente.
Las placas de respaldo pueden estar hechas de grafito, acero inoxidable, acero al carbono, placas de cobre o barras de cobre. Se hace una ranura curva en la superficie de la placa de respaldo para asegurar la formación de soldadura en la parte posterior.
Alternativamente, se puede realizar soldadura por un lado con conformado por ambos lados sin placa de soporte, pero esto requiere operaciones de soldadura especializadas o la aplicación de medidas de proceso avanzadas, como un estricto control de retroalimentación automática de la energía de soldadura.
(3) Precalentamiento antes de soldar
Las piezas de aluminio delgadas y pequeñas generalmente no requieren precalentamiento. El precalentamiento se puede realizar para espesores entre 10 mm y 15 mm, con temperaturas que oscilan entre 100°C y 200°C según el tipo de aleación de aluminio.
Para calentar se pueden utilizar técnicas como llamas de oxiacetileno, hornos eléctricos o sopletes. El precalentamiento ayuda a minimizar la deformación de la soldadura y reducir defectos como la porosidad.
5. Tratamiento post-soldadura
(1) Limpieza posterior a la soldadura
El fundente y la escoria de soldadura residuales que quedan sobre y cerca de la soldadura pueden dañar la película de pasivación de la superficie de aluminio e incluso corroer las piezas de aluminio, por lo que requieren una limpieza minuciosa. Para piezas de forma simple con requisitos generales, se pueden utilizar métodos de limpieza sencillos, como enjuague con agua caliente o cepillado con vapor.
Para piezas de aluminio de formas complejas y de alta exigencia, después de cepillarlas en agua caliente con un cepillo rígido, se deben remojar en una solución acuosa de ácido crómico o solución de dicromato de potasio con una concentración del 2-3% a aproximadamente 60° C. 80 °C durante 5 a 10 minutos y luego frotar con un cepillo duro.
Luego se deben enjuagar con agua caliente y secar al horno o con aire caliente. También es aceptable el secado natural.
(2) Tratamiento térmico post-soldadura
Generalmente, no es necesario el tratamiento térmico después de soldar contenedores de aluminio. Sin embargo, si el material de aluminio en uso muestra una sensibilidad significativa al agrietamiento por corrosión bajo tensión bajo las condiciones del medio en contacto con el contenedor, es necesario someterse a un tratamiento térmico posterior a la soldadura para eliminar las altas tensiones de soldadura, reduciendo así la tensión en el contenedor. por debajo del límite de fisuración por corrosión bajo tensión.
Este requisito debe indicarse especialmente en los documentos de diseño del contenedor antes de realizar un tratamiento térmico para aliviar tensiones después de la soldadura. Si se requiere un tratamiento térmico de recocido posterior a la soldadura, la temperatura recomendada para el aluminio puro, 5052, 5086, 5154, 5454, 5A02, 5A03, 5A06, etc., es 345°C; para 2014, 2024, 3003, 3004, 5056, 5083, 5456, 6061, 6063, 2A12, 2A24, 3A21, etc., es 415 ℃; para 2017, 2A11, 6A02, etc., es 360 ℃.
Dependiendo del tamaño y los requisitos de la pieza de trabajo, la temperatura de recocido se puede ajustar hacia arriba o hacia abajo entre 20°C y 30°C, mientras que el tiempo de retención puede variar de 0,5 a 2 horas.