I. Problemas al soldar metales diferentes
Problemas inherentes a la soldadura de metales disímiles han impedido su desarrollo, como la constitución y comportamiento de la zona de fusión en metales disímiles.
El daño a la estructura por la soldadura de metales diferentes a menudo ocurre en la zona de fusión, ya que las características del cristal de soldadura difieren a lo largo de los segmentos cerca de la zona de fusión, lo que lleva a la formación de una capa de transición con un rendimiento deficiente y cambios de composición.
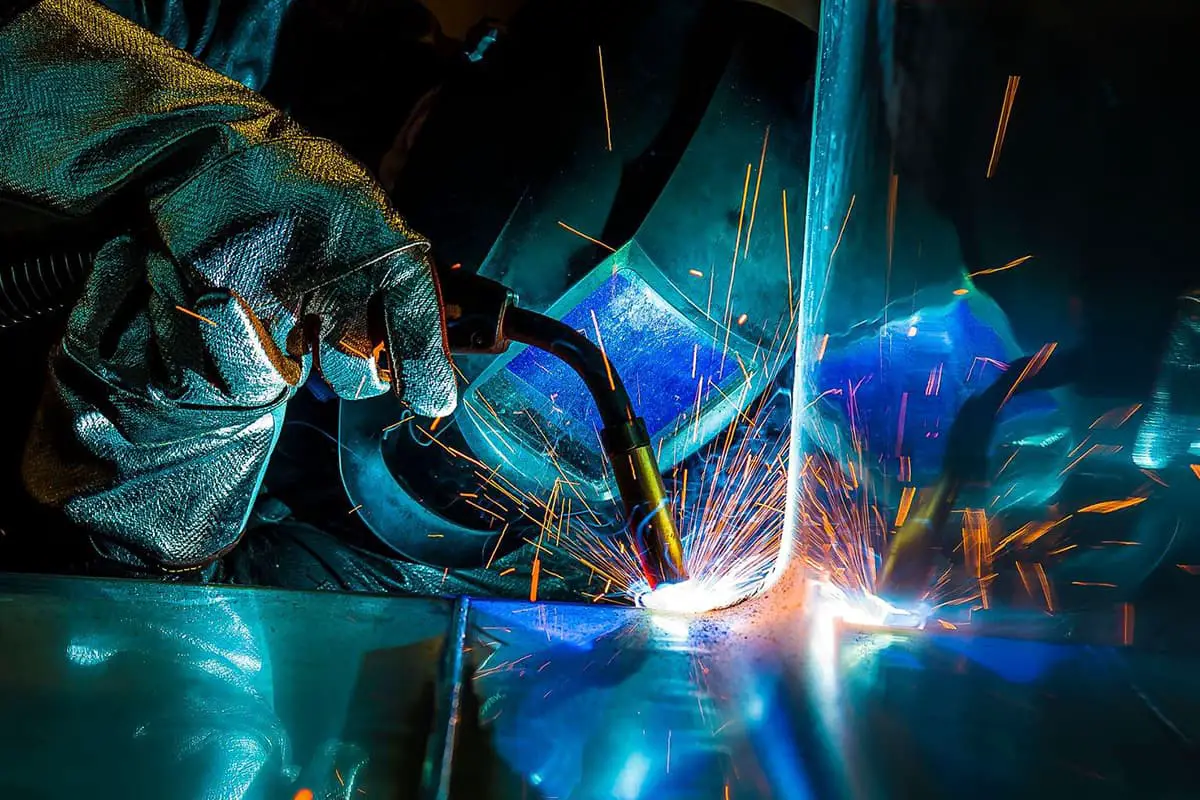
Además, debido a la exposición prolongada a altas temperaturas, la capa de difusión en esta región se expandirá, aumentando aún más la heterogeneidad del metal.
Además, durante o después de soldar metales diferentes, o después de un tratamiento térmico o una operación a alta temperatura, es común observar el fenómeno de que el carbono del lado de baja aleación “migre” a través del límite de la soldadura hacia la soldadura de alta aleación, formando capas. de descarburación y carburación a ambos lados de la línea de fusión.
Esto da como resultado una capa de descarburación en el material original de baja aleación y una capa de carburación en el lado de soldadura de alta aleación.
El impedimento y prevención del uso y desarrollo de disímiles estructuras metálicas se manifiestan principalmente en las siguientes áreas:
1. A temperatura ambiente, las propiedades mecánicas del área de unión soldada de metales diferentes (como tracción, impacto, flexión, etc.) generalmente superan el rendimiento del material soldado original.
Sin embargo, después de un funcionamiento prolongado a alta temperatura, el rendimiento de la zona de unión es inferior al del material original.
2. Existe una zona de transición martensítica entre la soldadura austenítica y el material base perlítico.
Esta zona tiene menor tenacidad y es una capa frágil de alta dureza, que es un área débil que conduce a la falla del componente. Reduce la confiabilidad de la estructura soldada.
3. El tratamiento térmico posterior a la soldadura o la migración de carbono durante la operación a alta temperatura pueden dar como resultado la formación de una capa carburizada y una capa descarburada en ambos lados de la línea de fusión.
Generalmente se cree que la capa descarburada, debido a la reducción de carbono, provoca cambios significativos en la estructura y propiedades del área (generalmente degradación), haciéndola propensa a fallas prematuras durante el servicio.
Los sitios de falla de muchas tuberías de alta temperatura en servicio o bajo prueba se concentran en la capa descarburada.
4. La falla está relacionada con condiciones como el tiempo, la temperatura y el estrés cíclico.
5. El tratamiento térmico posterior a la soldadura no puede eliminar la distribución de tensiones residuales en el área de la junta.
6. Inhomogeneidad de la composición química.
Al soldar metales diferentes, los metales en ambos lados del cordón de soldadura y la composición de la aleación del cordón de soldadura difieren significativamente.
Durante el proceso de soldadura, tanto el material original como el material de soldadura se derretirán y mezclarán.
Este nivel de uniformidad de la mezcla cambia con el proceso de soldadura, y el grado de uniformidad de la mezcla puede variar mucho en diferentes ubicaciones de la junta soldada, lo que lleva a una falta de homogeneidad en la composición química de la junta soldada.
7. Inhomogeneidad de la estructura metalográfica.
Debido a la discontinuidad de la composición química de la junta soldada y la experiencia del ciclo térmico de soldadura, aparecen diferentes estructuras en diferentes áreas de la junta soldada, lo que a menudo resulta en formaciones estructurales extremadamente complejas en algunas áreas.
8. Rendimiento discontinuo.
La composición química y la estructura metalúrgica de las uniones soldadas provocan variaciones en sus propiedades mecánicas.
La resistencia, dureza, plasticidad, tenacidad, resistencia al impacto, fluencia a altas temperaturas y rendimiento duradero difieren significativamente en las distintas regiones de la junta soldada.
Esta inconsistencia sustancial provoca diferentes comportamientos en diferentes regiones de la articulación en condiciones idénticas, manifestándose como áreas de debilitamiento y fortalecimiento.
Particularmente en condiciones de alta temperatura, las uniones soldadas de metales diferentes a menudo fallan prematuramente durante el servicio.
II. Características de soldar diferentes metales utilizando diferentes métodos.
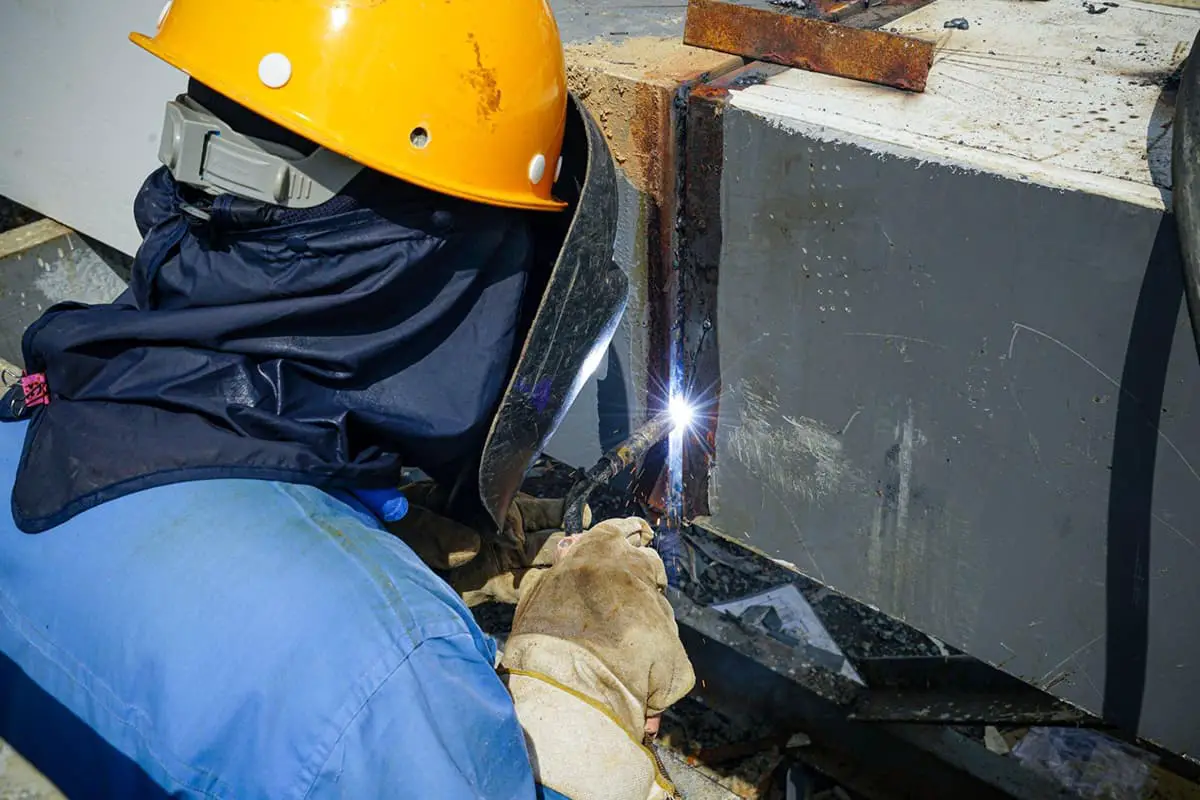
La mayoría de los métodos de soldadura se pueden aplicar para soldar metales diferentes, pero al elegir un método de soldadura y establecer mediciones del proceso, se deben tener en cuenta las características de la soldadura de metales diferentes.
Según los requisitos del material base y la unión soldada, la soldadura por fusión, la soldadura por presión y otros métodos han encontrado aplicaciones en la soldadura de diferentes metales, cada uno con sus propias ventajas y desventajas.
1. Soldadura por fusión
La soldadura por fusión se utiliza ampliamente para soldar metales diferentes.
Los métodos comunes de soldadura por fusión incluyen soldadura con electrodo revestido, soldadura por arco sumergido, soldadura por arco con gas protegido, soldadura por electroescoria, soldadura por arco de plasma, soldadura por haz de electrones y soldadura por láser.
Para reducir la dilución, ralentizar la velocidad de fusión o controlar la cantidad de fusión de diferentes metales base, normalmente se eligen métodos con mayor densidad de energía de la fuente de calor, como la soldadura por haz de electrones, la soldadura por láser o la soldadura por arco de plasma.
Para minimizar la profundidad de fusión, se pueden adoptar medidas tecnológicas como arco indirecto, alambre de soldadura oscilante, electrodo de banda y alambre de soldadura adicional no electrificado.
Sin embargo, en cualquier caso, siempre que se trate de soldadura por fusión, parte del material base siempre se fundirá en la costura de soldadura, provocando su dilución.
Además, también formará compuestos intermetálicos, estructuras eutécticas, etc.
Para paliar estos efectos adversos, es imperativo controlar y reducir el tiempo de residencia de los metales en estado líquido o sólido a altas temperaturas.
Sin embargo, a pesar de las continuas mejoras y avances en los métodos y procedimientos de soldadura por fusión, sigue siendo un desafío resolver todos los problemas asociados con la soldadura de diferentes tipos de metales.
Dada la diversidad de metales y la amplia gama de requisitos de rendimiento, junto con los diferentes estilos de juntas, en muchos casos, se debe emplear soldadura a presión u otros métodos de soldadura para resolver problemas de soldadura específicos relacionados con diferentes juntas metálicas.
2. Soldadura a presión
La mayoría de los métodos de soldadura a presión sólo calientan los metales a soldar hasta un estado plástico o no lo calientan en absoluto, caracterizándose principalmente por la aplicación de una determinada presión.
En comparación con la soldadura por fusión, la soldadura a presión tiene ciertas ventajas al soldar juntas de metales diferentes, siempre que la forma de la junta lo permita y la calidad de la soldadura cumpla con los requisitos, la soldadura a presión suele ser una opción más razonable.
Durante la soldadura a presión, la superficie de unión de diferentes metales puede fundirse o permanecer sólida, pero debido al efecto de la presión, incluso si hay metal fundido en la superficie, será expulsado (como en la soldadura por flash y la soldadura por fricción). .
Sólo en algunos casos el metal fundido permanece después de soldar bajo presión (como en la soldadura por puntos).
La soldadura a presión, debido a la falta de calor o a la baja temperatura de calentamiento, puede mitigar o evitar los efectos adversos del ciclo térmico sobre las propiedades del metal base y prevenir la formación de compuestos intermetálicos frágiles.
Algunas formas de soldadura a presión pueden incluso exprimir los compuestos intermetálicos que se han formado en la unión.
Además, durante la soldadura a presión no se producen cambios relacionados con la dilución en las propiedades del metal de soldadura.
Sin embargo, la mayoría de los métodos de soldadura a presión tienen ciertos requisitos en cuanto a la forma de las juntas.
Por ejemplo, la soldadura por puntos, la soldadura por costura y la soldadura ultrasónica deben utilizar juntas traslapadas; al menos una parte debe tener una sección transversal rotacional en soldadura por fricción; La soldadura explosiva solo es aplicable a conexiones de áreas más grandes.
Los equipos de soldadura a presión tampoco están todavía muy extendidos. Sin duda, estos factores limitan el rango de aplicación de la soldadura a presión.
3. Otros métodos
Además de la soldadura por fusión y la soldadura por presión, existen otros métodos para soldar metales diferentes. Por ejemplo, la soldadura fuerte es un método que utiliza un metal de aportación para unir diferentes metales base.
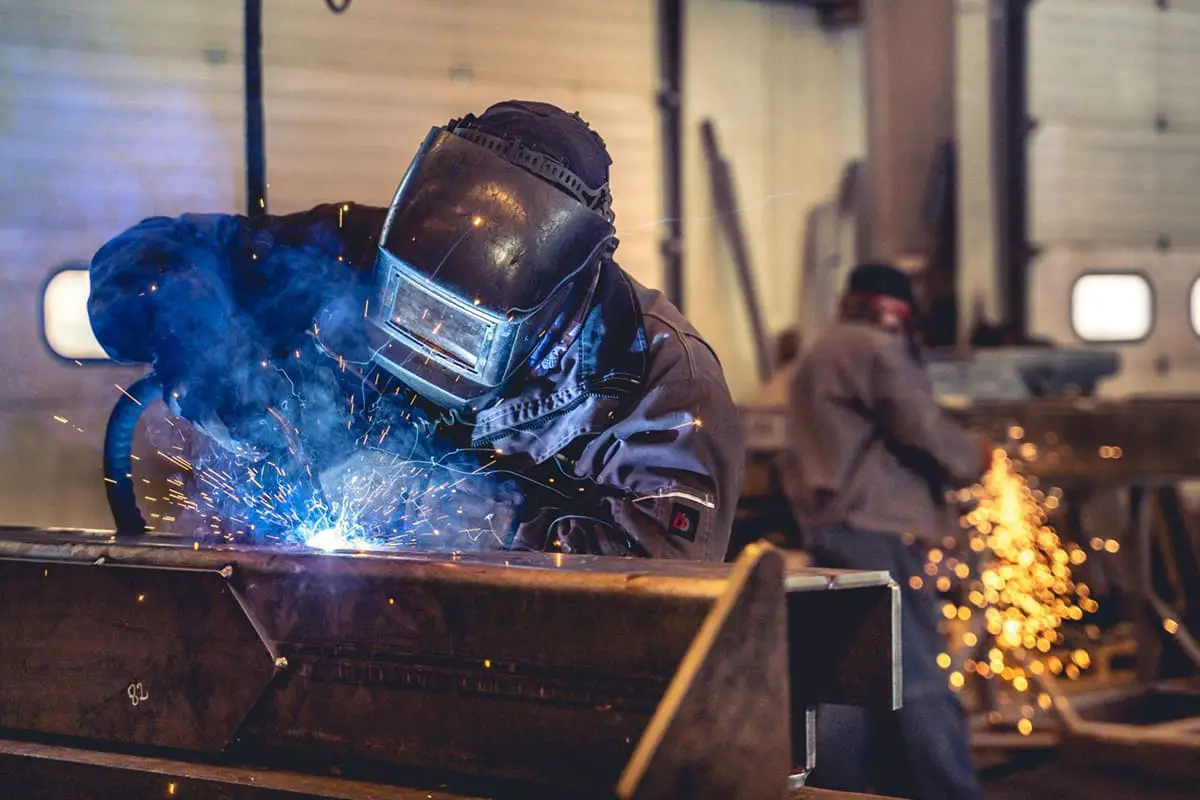
Sin embargo, aquí la atención se centra en un tipo especial de método de soldadura fuerte.
Una de esas técnicas se conoce como soldadura fuerte por fusión, en la que el material con un punto de fusión más bajo en una unión metálica diferente se somete a soldadura por fusión y el material con un punto de fusión más alto se somete a soldadura fuerte. El metal de aportación normalmente corresponde al metal base con un punto de fusión bajo.
Como tal, el proceso entre el metal de aportación y el metal base de bajo punto de fusión es esencialmente un proceso de soldadura por fusión del mismo metal y no presenta ningún desafío único.
La interacción entre el metal de aportación y el metal base de alto punto de fusión es un proceso de soldadura fuerte. El metal base no se funde ni cristaliza, evitando muchos problemas relacionados con la soldadura.
Sin embargo, esto requiere que el metal de aportación humedezca el metal base de forma eficaz.
Otra técnica se conoce como soldadura fuerte eutéctica o soldadura fuerte por difusión eutéctica. Este método implica calentar la superficie de contacto de metales diferentes a una cierta temperatura que forma un eutéctico de bajo punto de fusión en el punto de contacto.
Este eutéctico de bajo punto de fusión se vuelve líquido a esta temperatura, creando esencialmente un método de soldadura fuerte que no requiere metal de aportación adicional.
Naturalmente, esto requiere que los dos metales formen un eutéctico de bajo punto de fusión.
Durante la soldadura por difusión de metales diferentes, se introduce una capa intermedia y, bajo baja presión, la capa intermedia se funde o forma un eutéctico de bajo punto de fusión al entrar en contacto con los metales a soldar.
Esta fina capa de líquido, después de un período específico de conservación del calor, permite que la capa intermedia se difunda completamente en el metal base y se vuelva uniforme, lo que da como resultado una unión metálica diferente sin una capa intermedia.
Estos métodos suelen implicar una pequeña cantidad de metal líquido durante el proceso de soldadura, por lo que también se les llama soldadura de transición de fase líquida. Su característica común es la ausencia de estructuras fusionadas en la articulación.
III. Consideraciones para soldar metales diferentes
1. Considerar las propiedades físicas, mecánicas y la composición química de las soldaduras.
El. Desde la perspectiva de igual resistencia, seleccione varillas de soldadura que satisfagan la resistencia del metal base.
Alternativamente, considerando la soldabilidad del metal base, elija varillas de soldadura que no tengan la misma resistencia, pero que ofrezcan buena soldabilidad.
Sin embargo, se debe considerar que la estructura soldada cumple con los requisitos de igual resistencia e igual rigidez.
B. Asegúrese de que la composición de la aleación coincida o se acerque a la del metal base.
w. Cuando el metal base contiene una mayor cantidad de impurezas nocivas como carbono (C), azufre (S) y fósforo (P), elija varillas de soldadura con resistencia superior al agrietamiento y a la porosidad. Se sugiere utilizar varillas de soldadura del tipo titanio-calcio. Si esto no resuelve el problema, se pueden utilizar varillas de soldadura del tipo sodio bajo en hidrógeno.
2. Considere las condiciones de trabajo y los requisitos de rendimiento de la soldadura.
El. Cuando se somete a cargas dinámicas y cargas de impacto, además de asegurar resistencia, se requiere alta tenacidad al impacto y alargamiento.
En este caso, elija varillas de soldadura con un bajo contenido en hidrógeno, titanio-calcio y óxido de hierro.
B. Si las piezas soldadas están en contacto con medios corrosivos, es necesario seleccionar una varilla de soldadura de acero inoxidable adecuada en función del tipo, concentración y temperatura de funcionamiento del medio, así como si se trata de corrosión general o corrosión intergranular.
w. Durante las condiciones de operación que involucran desgaste, diferencie si es desgaste general o desgaste por impacto, y si el desgaste ocurre a temperatura ambiente o a alta temperatura.
d. Para operaciones en condiciones de temperatura extrema, elija varillas de soldadura que garanticen un rendimiento mecánico a baja o alta temperatura.
3. Considere la complejidad de la forma del ensamblaje, el nivel de rigidez, el estado de preparación de la abertura de soldadura y la posición de soldadura.
El. Para soldar piezas con formas complejas o alto espesor, el metal de soldadura experimenta importantes tensiones de contracción durante el enfriamiento, lo que puede provocar grietas.
Es fundamental elegir varillas de soldadura con alta resistencia al agrietamiento, como varillas con bajo contenido de hidrógeno, varillas de alta tenacidad o varillas de óxido férrico.
B. Para soldar piezas que no se pueden invertir debido a ciertas condiciones, es necesario seleccionar varillas de soldadura capaces de realizar soldadura en todas las posiciones.
w. Para soldar piezas donde el área de soldadura es difícil de limpiar, elija varillas que sean altamente oxidantes e insensibles a la piel oxidada y a la grasa, para evitar la aparición de defectos como agujeros de aire.
4. Considere el equipo del sitio de soldadura.
En lugares sin máquinas de soldar de CC, no es apropiado elegir varillas de soldadura que solo funcionen con energía de CC. En su lugar, se deben seleccionar varillas que puedan usar energía CA y CC.
Ciertos materiales de acero, como el acero perlítico resistente al calor, requieren un alivio de la tensión posterior a la soldadura.
Sin embargo, si las condiciones del equipo o las limitaciones estructurales inherentes impiden el tratamiento térmico, se recomienda utilizar varillas fabricadas con materiales básicos no metálicos, como el acero inoxidable austenítico, que no requieren tratamiento térmico posterior a la soldadura.
5. Considerar mejorar las técnicas de soldadura y proteger la salud de los trabajadores.
En lugares donde las varillas de soldadura ácidas y alcalinas cumplen los requisitos, se deben preferir las varillas ácidas.
6. Considere la productividad laboral y la racionalidad económica.
Cuando el rendimiento es el mismo, se deben seleccionar varillas de soldadura ácidas y de menor precio en lugar de alcalinas.
Entre las varillas de soldadura ácidas, las de titanio y titanio-calcio son más caras.
Teniendo en cuenta la situación de los recursos minerales de nuestro país, debemos promover fuertemente el uso de barras recubiertas de hierro y titanio.
3. Considere la complejidad de la forma de montaje, el nivel de rigidez, el estado de preparación de la abertura de soldadura y la posición de soldadura.
El. Para soldar piezas con formas complejas o alto espesor, el metal de soldadura experimenta importantes tensiones de contracción durante el enfriamiento, lo que puede provocar grietas. Es fundamental elegir varillas de soldadura con alta resistencia al agrietamiento, como varillas con bajo contenido de hidrógeno, varillas de alta tenacidad o varillas de óxido férrico.
B. Para soldar piezas que no se pueden invertir debido a ciertas condiciones, es necesario seleccionar varillas de soldadura capaces de realizar soldadura en todas las posiciones.
w. Para soldar piezas donde el área de soldadura es difícil de limpiar, elija varillas que sean altamente oxidantes e insensibles a la piel oxidada y a la grasa, para evitar la aparición de defectos como agujeros de aire.