El cobre y las aleaciones de cobre se utilizan ampliamente debido a sus propiedades integrales únicas y superiores. El cobre y las aleaciones de cobre tienen una excelente conductividad eléctrica y térmica, alta resistencia a la oxidación y a la corrosión en agua dulce, agua salada, soluciones alcalinas y productos químicos orgánicos.
Sin embargo, son susceptibles a la corrosión en ácidos oxidantes. Las aleaciones de cobre tienen buena trabajabilidad en frío y en caliente y mayor resistencia. El cobre y las aleaciones de cobre se han utilizado ampliamente en industrias como la eléctrica, electrónica, química, alimentaria, energética, de transporte, aeroespacial y de defensa.
Existen varios tipos de cobre y aleaciones de cobre que se producen en la producción industrial y la mayoría de los países los clasifican según su composición química. El cobre y las aleaciones de cobre se pueden clasificar en cobre puro, latón, bronce y cobre blanco, entre otros.
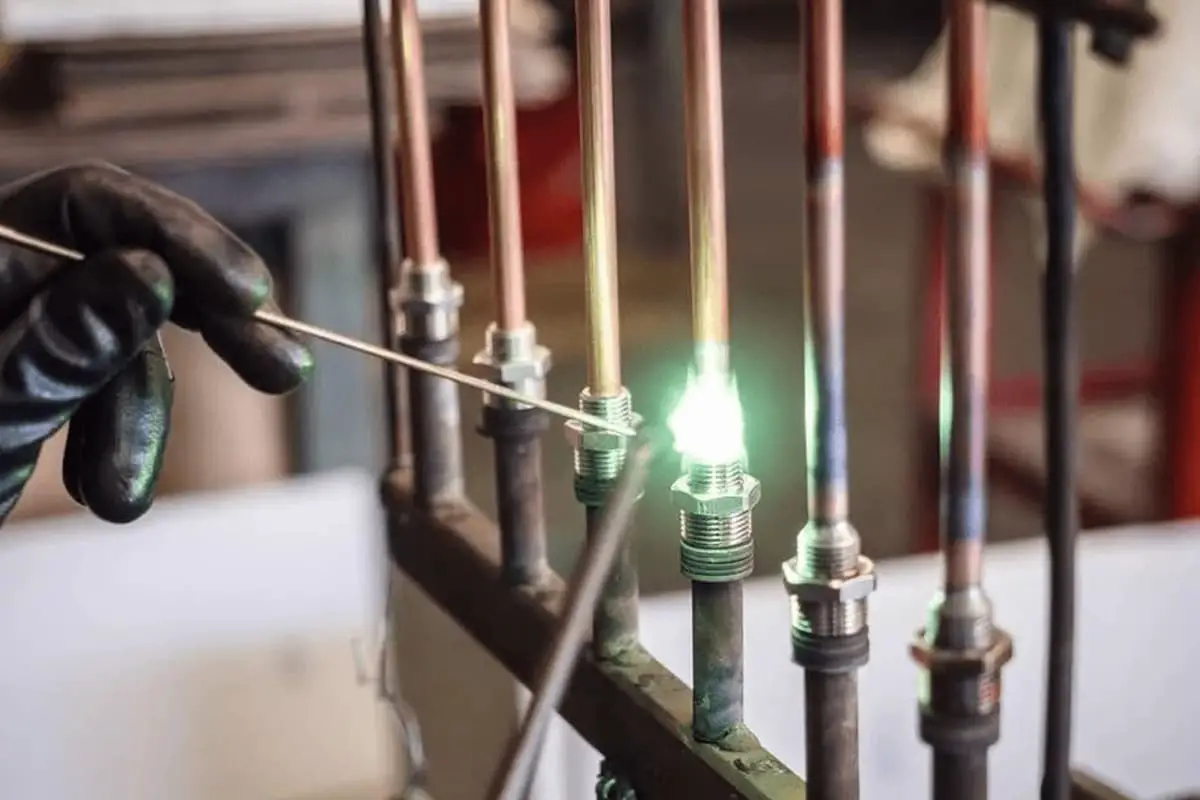
El cobre puro recocido blando se utiliza generalmente para soldar estructuras. Los tipos comunes de cobre puro incluyen T1, T2, T3, T4 y cobre desoxidado (cobre libre de oxígeno) TU1, TU2, etc. El latón es una aleación de cobre compuesta principalmente de zinc.
El latón y las aleaciones especiales de latón de uso común incluyen H62, H68, H96, HPb59-1, HSn62-1, etc. El bronce originalmente se refería a aleaciones de cobre y estaño, pero ahora se usa comúnmente para describir aleaciones de cobre que no tienen zinc o níquel como elemento de aleación principal. Los tipos comunes de bronce incluyen bronce al estaño (QSn4-3), bronce al aluminio (QAl9-2), bronce al silicio (QSi3-1), etc.
Además, las aleaciones de cobre con níquel como elemento de aleación principal se denominan cobre blanco.
1. Soldabilidad del cobre y aleaciones de cobre.
La soldabilidad del cobre y las aleaciones de cobre es comparativamente baja, lo que hace que la soldadura sea mucho más desafiante en comparación con el acero con bajo contenido de carbono. Las principales dificultades se observan en los siguientes aspectos:
(1) Mala capacidad de formación de soldadura:
Al soldar cobre y la mayoría de las aleaciones de cobre, es probable que haya dificultades para lograr la fusión, una penetración incompleta de la junta y una mala formación de la superficie. Esto se debe principalmente a la alta conductividad térmica del cobre. La conductividad térmica del cobre y la mayoría de las aleaciones de cobre es de 7 a 11 veces mayor que la del acero al carbono ordinario.
Como resultado, el calor se disipa rápidamente de la zona de soldadura. Cuanto más gruesa sea la pieza, más severa será la disipación de calor. Aunque el cobre tiene un punto de fusión y una capacidad calorífica específica más bajos en comparación con el hierro, sigue siendo un desafío alcanzar la temperatura de fusión en la zona de soldadura, lo que dificulta la fusión del metal base y el metal de aportación.
Además, la excelente conductividad térmica del cobre genera una zona afectada por el calor más amplia, lo que puede provocar una deformación significativa cuando la pieza tiene poca rigidez. Por otro lado, cuando la rigidez es alta, puede provocar importantes tensiones de soldadura en la pieza de trabajo.
La mala formación de la superficie en cobre y aleaciones de cobre se atribuye principalmente al hecho de que la tensión superficial durante la fusión es un tercio de la del acero y la fluidez es de 1 a 1,5 veces mayor que la del acero, lo que lo hace más susceptible a la pérdida de metal durante la fusión. derritiendo.
Por lo tanto, al soldar cobre puro y la mayoría de las aleaciones de cobre altamente conductoras, además de utilizar métodos de soldadura de alta potencia y alta densidad de energía, también es necesario incorporar diversos grados de precalentamiento. No está permitido utilizar soldadura unilateral sin soporte, y al realizar soldadura unilateral, se debe agregar una placa de soporte para controlar la formación de la junta soldada.
(2) Alta susceptibilidad al agrietamiento por calor en soldaduras y zonas afectadas por el calor:
La tendencia al agrietamiento térmico en las soldaduras está relacionada con la influencia de las impurezas en la soldadura y también está influenciada por las tensiones generadas durante el proceso de soldadura. El oxígeno es una impureza común que se encuentra en el cobre y tiene un impacto significativo en la tendencia de las soldaduras a agrietarse por calor.
A altas temperaturas, el cobre reacciona con el oxígeno del aire para formar Cu 2 O. El Cu 2 O es soluble en cobre líquido pero no en cobre sólido, formando un eutéctico de bajo punto de fusión. Las impurezas como el Bi y el Pb en el cobre y las aleaciones de cobre tienen puntos de fusión bajos.
Durante el proceso de solidificación del baño de soldadura, forman eutécticos de bajo punto de fusión que se distribuyen entre las dendritas o los límites de los granos, provocando una fragilidad térmica significativa en el cobre y las aleaciones de cobre. Cuando la soldadura está en la fase sólido-líquido, los eutécticos de bajo punto de fusión en la zona afectada por el calor se funden nuevamente bajo la influencia de las tensiones de soldadura, lo que resulta en un agrietamiento térmico.
El cobre y las aleaciones de cobre tienen coeficientes de expansión lineal y tasas de contracción relativamente altos, y también exhiben una fuerte conductividad térmica. Al soldar, se requieren fuentes de calor de alta potencia, lo que da como resultado una zona afectada por el calor más amplia. Como resultado, las uniones soldadas experimentan importantes tensiones internas, que es otro factor que conduce al agrietamiento en las soldaduras de cobre y aleaciones de cobre.
Además, al soldar cobre puro, el metal de soldadura consta de una estructura monofásica. Debido a la alta conductividad térmica del cobre puro, la soldadura tiende a formar granos gruesos. Esto agrava aún más la formación de grietas térmicas.
Por lo tanto, para evitar la formación de grietas térmicas al utilizar soldadura por fusión para soldar cobre y aleaciones de cobre, se deben tomar las siguientes medidas metalúrgicas:
1) Controlar estrictamente el contenido de impurezas (como oxígeno, bismuto, plomo, azufre, etc.) en el cobre.
2) Aumentar la capacidad de desoxidación de la soldadura agregando elementos de aleación como silicio, manganeso, fósforo, etc., al alambre de soldadura.
3) Seleccionar materiales de soldadura que puedan obtener una estructura dúplex, que perturbe la continuidad de las películas eutécticas de bajo punto de fusión y cambie la dirección de los granos columnares.
4) Implementar medidas como precalentamiento y enfriamiento lento para reducir las tensiones de soldadura, minimizar el tamaño del espacio de la raíz y aumentar las dimensiones del paso de la raíz para evitar la formación de grietas.
(3) Susceptibilidad a la formación de porosidad:
Cuando se suelda por fusión cobre y aleaciones de cobre, la tendencia a formar porosidad es mucho más significativa en comparación con el acero con bajo contenido de carbono. Para reducir y eliminar la porosidad en las soldaduras de cobre, las principales medidas son reducir las fuentes de hidrógeno y oxígeno y precalentar para prolongar la existencia del baño fundido, facilitando el escape de los gases.
Utilice alambres de soldadura con desoxidantes fuertes como aluminio, titanio, etc. (que también puede eliminar nitrógeno e hidrógeno) o agregar elementos como aluminio y estaño a aleaciones de cobre puede producir buenos resultados en términos de desoxidación.
(4) Disminución del rendimiento de las juntas de soldadura:
Durante el proceso de soldadura por fusión de cobre y aleaciones de cobre, las uniones soldadas sufren un severo crecimiento de grano, evaporación y quema de elementos de aleación, así como infiltración de impurezas, lo que lleva a una disminución de las propiedades mecánicas, la conductividad eléctrica y la resistencia a la corrosión. uniones soldadas.
1) Disminución significativa de la ductilidad:
La soldadura y la zona afectada por el calor exhiben un engrosamiento del grano, y varios eutécticos frágiles de bajo punto de fusión aparecen en los límites de los granos, debilitando la fuerza de unión del metal y reduciendo significativamente la ductilidad y tenacidad de la unión. Por ejemplo, cuando se utilizan electrodos de soldadura de cobre puro para soldadura por arco o soldadura por arco sumergido, el alargamiento de la unión es sólo aproximadamente del 20% al 50% del del material base.
2) Disminución de la conductividad eléctrica:
Agregar cualquier elemento al cobre disminuirá su conductividad eléctrica. Por tanto, la fusión de impurezas y elementos de aleación durante el proceso de soldadura deteriorará, hasta cierto punto, la conductividad eléctrica de las uniones de cobre.
3) Disminución de la resistencia a la corrosión:
La resistencia a la corrosión de las aleaciones de cobre se consigue mediante la aleación con elementos como zinc, manganeso, níquel, aluminio, etc. La evaporación y oxidación de estos elementos durante el proceso de soldadura por fusión reducirá en cierta medida la resistencia a la corrosión de la unión. La generación de tensiones de soldadura también aumenta el riesgo de fisuración por corrosión bajo tensión.
Las medidas para mejorar el rendimiento de la unión pasan principalmente por controlar el contenido de impurezas, reducir la quema de la aleación y realizar tratamientos térmicos para modificar la microestructura de la soldadura. También es beneficioso minimizar el aporte de calor durante la soldadura y aplicar un tratamiento de alivio de tensión después de la soldadura.
2. Selección de métodos de soldadura.
Actualmente, existen muchos métodos de soldadura disponibles para cobre y aleaciones de cobre. Los métodos de soldadura comúnmente utilizados incluyen soldadura con gas, soldadura por arco de metal protegido, soldadura con gas inerte de tungsteno (TIG), soldadura por arco de argón con electrodo consumible y soldadura por arco sumergido.
La selección de los métodos de soldadura debe basarse en la composición, el espesor, las características estructurales y los requisitos de rendimiento del material a soldar.
El cobre es el metal con mejor conductividad térmica entre los metales de soldadura más utilizados. Por lo tanto, la soldadura de cobre y sus aleaciones requiere métodos de soldadura de alta potencia y alta densidad de energía.
Se prefiere una mayor eficiencia térmica y energía más concentrada. Los diferentes espesores de materiales tienen diferente adaptabilidad a diversos métodos de soldadura.
Por ejemplo, las placas delgadas son más adecuadas para soldadura TIG y soldadura con gas. Las placas medianas y gruesas son más adecuadas para soldadura por arco sumergido, soldadura por arco de argón con electrodo consumible y soldadura por haz de electrones. Para placas gruesas, se recomienda la soldadura MIG y la soldadura por arco metálico protegido.
3. Selección de materiales de soldadura.
1) Alambre de soldadura:
Además de cumplir con los requisitos metalúrgicos y de proceso generales, el alambre de soldadura para soldar cobre y aleaciones de cobre debe controlar principalmente el contenido de impurezas y mejorar la capacidad de desoxidación para prevenir la formación de grietas térmicas y porosidad.
Para soldar cobre puro, se añaden principalmente al alambre de soldadura elementos desoxidantes como Si, Mn, P. Los alambres de soldadura comúnmente utilizados incluyen alambre de soldadura de cobre de alta pureza HSCu, que a menudo se usa en soldadura con gas junto con el solvente CJ301 y soldadura por arco sumergido junto con el fundente HJ431.
2) Electrodos de soldadura:
Los electrodos de soldadura por arco para cobre se pueden dividir en tipos de cobre y bronce, siendo los electrodos de bronce los más utilizados. Debido a la tendencia del zinc del latón a evaporarse, los electrodos de cobre rara vez se utilizan para soldadura por arco.
En estos casos se pueden utilizar electrodos de bronce. Los electrodos de cobre de uso común incluyen el electrodo de cobre puro T107 y el electrodo de bronce de silicio T207.
4. Preparación previa a la soldadura
Los requisitos para el pretratamiento de soldaduras de cobre y aleaciones de cobre son relativamente estrictos. La limpieza previa a la soldadura de cobre y aleaciones de cobre implica principalmente la eliminación de películas de aceite y óxido. Antes de retirar la película de óxido, limpie la ranura y las impurezas a un intervalo de 30 mm en ambos lados de la junta con gasolina o acetona.
Luego limpie la ranura de la contaminación por aceite con una solución de hidróxido de sodio al 10% a una temperatura de 30-40°C y luego enjuáguela con agua. Remoje la junta en una solución de ácido nítrico al 35%-40% durante 2-3 minutos, enjuáguela nuevamente con agua y séquela.
La eliminación de películas de óxido se puede realizar mediante limpieza mecánica y química. Para la limpieza mecánica, utilice una rueda de alambre neumática o un cepillo de alambre para pulir la superficie del alambre de soldadura y la pieza soldada hasta que se vea un brillo metálico.
La limpieza química implica sumergir la soldadura en una solución mixta de 70 ml/l de HNO3, 100 ml/l de H2SO4 y 1 ml/l de HCl para su limpieza, seguido de neutralización con una solución alcalina, enjuague con agua limpia y luego secado al aire tibio.
5. Puntos clave del proceso de soldadura
Soldadura de gas:
La soldadura con gas es adecuada para soldar piezas delgadas de cobre, reparar piezas de cobre o soldar estructuras no críticas.
1) Precalentamiento antes de soldar:
Generalmente, el precalentamiento es necesario para la soldadura con gas de cobre puro para evitar que se produzcan tensiones internas, grietas, porosidad y penetración incompleta. La temperatura de precalentamiento para placas delgadas y piezas soldadas pequeñas es de alrededor de 400-500 °C, mientras que para piezas soldadas gruesas y grandes, la temperatura de precalentamiento debe aumentarse a 600-700 °C. La temperatura de precalentamiento del latón y el bronce puede ser ligeramente inferior.
2) Selección de parámetros de soldadura y técnica de soldadura: el cobre tiene una alta conductividad térmica, por lo que la energía de la llama utilizada para soldar es generalmente 1 o 2 veces mayor que la utilizada para soldar acero al carbono. Al soldar cobre puro, se debe utilizar estrictamente una llama neutra.
Una llama oxidante puede provocar la oxidación de la soldadura y la quema de los elementos de aleación. Una llama de cementación puede aumentar el contenido de hidrógeno en la soldadura y provocar la formación de porosidad.
Cuando se sueldan láminas delgadas con gas, se debe utilizar el método de soldadura a la izquierda, ya que ayuda a suprimir el crecimiento del grano. Cuando el espesor de la pieza es superior a 6 mm, se prefiere el método de soldadura por el lado derecho, ya que permite un calentamiento a mayor temperatura del metal base y proporciona una mejor visibilidad del baño de soldadura, lo que hace que la operación sea más conveniente.
El movimiento del soplete debe ser lo más rápido posible y cada cordón de soldadura no debe interrumpirse aleatoriamente. Es preferible completar cada cordón de soldadura en una sola pasada.
Al soldar costuras largas, se debe dejar un margen adecuado para la contracción antes de soldar y se debe realizar el posicionamiento antes de soldar. Se debe utilizar el método de juego segmentado durante la soldadura para reducir la deformación.
Para soldaduras de cobre sujetas a esfuerzos o de mayor importancia, se deben tomar medidas de martillado y tratamiento térmico de las uniones post-soldadura. Después de soldar piezas delgadas de cobre, se debe martillar inmediatamente la zona afectada por el calor en ambos lados de la soldadura.
Para tableros de espesor medio superior a 5 mm, se deben calentar a 500-600 °C antes de martillarlos. Después del martillado, la pieza de trabajo debe calentarse a 500-600 °C y luego enfriarse rápidamente en agua, lo que puede mejorar la plasticidad y dureza de la junta.
6. Ejemplos típicos de soldadura de cobre y aleaciones de cobre de uso común.
Hay una camisa de electrodo de agua, hecha de cobre desoxidado TU1. La unión del electrodo se suelda mediante soldadura MIG y el proceso de soldadura específico se muestra en la Tabla 5-37.
Tabla 5-37 Tarjeta de proceso de soldadura para junta TU1
Tarjeta de proceso de soldadura para soldadura de juntas. | Número | |||
Diagrama conjunto: ![]() |
Material de base | ATU1 | ATU1 | |
Espesor del material base | 15mm | 15mm | ||
Posición de soldadura | Soldadura plana | |||
Técnica de soldadura | Ruta de soldadura recta | |||
Temperatura de precalentamiento | 500℃ | |||
Temperatura entre pasadas | ≥500℃ | |||
Diámetro de la boquilla | Φ26mm | |||
Gas protector | Aire | Caudal de gas (l/min) | Frente: 25~30 Para volver: |
Secuencia de soldadura | |
1 | Inspeccione las dimensiones de la ranura y la calidad de la superficie. |
dos | Retire cualquier aceite o suciedad de la ranura y sus alrededores. Limpie la grasa con una solución de agua de NaOH al 10 % a una temperatura de 30 ~ 40 ℃, luego enjuague con agua limpia y seque. Retire la película de óxido lijando con una rueda de alambre de acero inoxidable, luego enjuague con agua alcalina, luego enjuague con agua limpia y seque. |
3 | Realice una soldadura por puntos para la primera capa utilizando una técnica de soldadura por colocación externa. La longitud debe ser de 100 mm y la distancia entre los puntos de soldadura no debe exceder los 300 mm. Si aparecen grietas en la costura de soldadura, elimínelas y vuelva a soldar. |
4 | Empalme los electrodos en un accesorio especialmente diseñado. Precaliente la pieza de trabajo usando calefacción eléctrica, con una temperatura de precalentamiento de 500°C, y asegúrese de que la temperatura de la capa intermedia no sea inferior a 500°C. |
5 | Comience a soldar desde el exterior para evitar la formación de cordones de soldadura en el interior de la costura de soldadura. Asegure la redondez del círculo interior del electrodo y la suavidad de la superficie interior. |
6 | Realizar inspección visual. |
7 | Enderezar si es necesario. |
8 | Realizar tratamiento térmico post-soldadura. |
Parámetros de especificación de soldadura
Pases | Método de soldadura | Grado del material de soldadura | Especificación del material de soldadura | Tipos de corriente y polaridad. | Corriente de soldadura (amperios) | Voltaje del arco (voltios) | Velocidad de soldadura (mm/por pasada) | Comentarios |
1~2 | MIG (Semiautomático) | HSCu | 1.6 | DCEP | 350~400 | 30~35 | 250~300 |