Soldadura por arco de acero galvanizado.
El recubrimiento de zinc sobre acero galvanizado puede presentar desafíos durante la soldadura. Las principales dificultades incluyen:
- Mayor sensibilidad a las grietas y porosidad en la soldadura.
- Evaporación de zinc y generación de hollín.
- Fusión y destrucción de recubrimientos de zinc y escorias de óxido.
De estos problemas, las grietas de soldadura, la porosidad y la escoria son las principales preocupaciones.
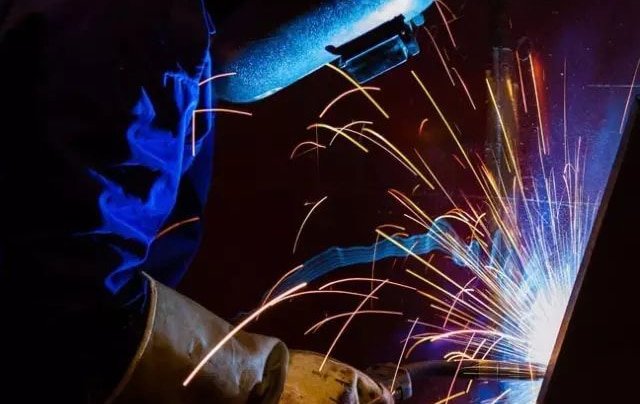
Soldabilidad
(1) La grieta
Durante el proceso de soldadura, el zinc fundido puede acumularse en la superficie del baño de soldadura o en la base de la soldadura. El punto de fusión más bajo del zinc en comparación con el hierro hace que el hierro en el baño fundido se solidifique primero, lo que permite que el zinc líquido penetre a lo largo de los límites de grano del acero, lo que lleva a una disminución en la fuerza de unión intercristalina.
Además, la formación de compuestos metálicos frágiles, como Fe3Zn10 y FeZn10, entre el zinc y el hierro reduce aún más la plasticidad del metal de soldadura. Esto lo hace propenso a agrietarse a lo largo de los límites del cristal debido a la tensión residual de la soldadura.
1) Factores que afectan la sensibilidad al crack
① Espesor del recubrimiento de zinc: El espesor del recubrimiento de zinc sobre acero galvanizado afecta su sensibilidad al agrietamiento. Una capa delgada de zinc da como resultado una menor sensibilidad a las grietas, mientras que una capa más gruesa sobre acero galvanizado en caliente conduce a una mayor sensibilidad a las grietas.
② Espesor de la pieza: El espesor de la pieza también influye en la sensibilidad a las grietas; las piezas más gruesas tienen una mayor tensión de restricción de soldadura y una mayor sensibilidad a las grietas.
③ Espacio libre de ranura: un espacio libre de ranura más grande aumenta la sensibilidad a las grietas.
④ Método de soldadura: Los diferentes métodos de soldadura también pueden afectar la sensibilidad a las grietas. La soldadura por arco manual produce una menor sensibilidad a las grietas, mientras que el uso de gas CO2 para soldar puede causar una mayor sensibilidad a las grietas.
2) Métodos para prevenir el agrietamiento
① Preparación para soldar: Antes de soldar, es necesario crear una ranura en forma de V, Y o X en el lugar de soldadura de la lámina galvanizada. La capa de zinc se puede eliminar cerca de la ranura con oxiacetileno o chorro de arena. Es importante no dejar demasiado espacio libre, siendo la recomendación general de 1,5 mm.
② Selección de materiales de soldadura: para reducir la probabilidad de grietas, es importante elegir materiales de soldadura con bajo contenido de silicio. Para la soldadura con protección gaseosa se debe utilizar un alambre de soldadura con bajo contenido de silicio. La soldadura manual se puede realizar utilizando un electrodo de tipo titanio o un electrodo de titanio-calcio.
(2) Estoma
La capa de zinc cercana a la ranura puede sufrir oxidación (ZnO) y vaporización debido al calor generado durante la soldadura por arco, lo que provoca la emisión de humo y vapor blancos. Esto puede resultar fácilmente en porosidad en la soldadura. Cuanto mayor sea la corriente de soldadura, más intensa será la evaporación del zinc y mayor será la probabilidad de que se produzca porosidad.
La soldadura con electrodos de titanio y calcio-titanio tiende a producir una menor porosidad en el rango de corriente media. Por otro lado, tanto las corrientes bajas como las altas durante la soldadura con electrodos de soldadura de tipo celulosa y con bajo contenido de hidrógeno pueden causar porosidad.
Es importante controlar el ángulo del electrodo para que esté en el rango de 30 a 70° para reducir el riesgo de porosidad.
(3) Evaporación de zinc y hollín
La capa de zinc cerca del baño fundido durante la soldadura se oxida a ZnO y se vaporiza debido al calor del arco, creando una cantidad significativa de polvo. El principal componente de este polvo es el ZnO, que puede tener efectos nocivos en el sistema respiratorio de los trabajadores.
Es importante garantizar una buena ventilación durante la soldadura para reducir el riesgo para los trabajadores.
Bajo las mismas especificaciones de soldadura, soldar con un electrodo de óxido de titanio genera menos polvo en comparación con el uso de un electrodo de soldadura con bajo contenido de hidrógeno, que tiende a producir una mayor cantidad de polvo.
(4) Escoria de óxido
Cuando se utiliza una corriente de soldadura baja, el ZnO formado durante el proceso de calentamiento puede quedar atrapado y formar escoria de ZnO. El ZnO es estable y tiene un alto punto de fusión de 1800°C. La presencia de grandes bloques de escoria de ZnO puede tener un impacto negativo significativo en la plasticidad de la soldadura.
Sin embargo, cuando se utiliza un electrodo de tipo óxido de titanio, la distribución de ZnO es pequeña y uniforme, lo que tiene poco efecto sobre la plasticidad y la resistencia a la tracción de la soldadura. Por otro lado, cuando se utilizan electrodos de celulosa o hidrógeno, el ZnO en la costura de soldadura es mayor y más abundante, lo que da como resultado un rendimiento de soldadura deficiente.
Proceso de soldadura de acero galvanizado
El acero galvanizado se puede soldar mediante varias técnicas, incluida la soldadura manual por arco eléctrico, la soldadura por electrodo de fusión con protección de gas, la soldadura por arco de argón y la soldadura por resistencia.
(1) Soldadura por arco manual
1) Preparación de soldadura
Para reducir la cantidad de polvo de soldadura y prevenir la formación de grietas y porosidad durante la soldadura, es necesario preparar la pendiente adecuada antes de soldar y eliminar la capa de zinc cerca de la ranura. Esta eliminación se puede lograr mediante llama o chorro de arena.
Es importante controlar el espacio de la ranura para que esté en el rango de 1,5 a 2 mm, y para piezas más gruesas el espacio se puede aumentar a 2,5 a 3 mm.
2) Selección de electrodos
El principio para seleccionar una varilla de soldadura es garantizar que las propiedades mecánicas del metal de soldadura sean lo más similares posible a las del material base. Además, es importante controlar la cantidad de silicio en el electrodo de soldadura para que se mantenga por debajo del 0,2%.
Lectura relacionada: ¿Cómo elegir la varilla de soldadura adecuada?
Las uniones realizadas con electrodos de soldadura de ilmenita, óxido de titanio, celulosa, titanio-calcio y bajo contenido de hidrógeno pueden presentar una resistencia satisfactoria. Sin embargo, los electrodos con bajo contenido de hidrógeno y celulosa tienden a generar escoria y porosidad en las soldaduras, por lo que no se usan comúnmente.
Para láminas de acero galvanizado de acero dulce, se prefieren las varillas de soldadura J421/J422 o J423. Para chapas de acero galvanizado con un nivel de resistencia superior a 500MPa se deben utilizar varillas de soldadura E5001 o E5003. Para chapas de acero galvanizado con resistencia superior a 600MPa, las varillas de soldadura recomendadas son E6013, E5503 o E5513.
Al soldar se recomienda utilizar un arco corto y evitar la oscilación del arco para minimizar la expansión de la zona de fusión de la capa galvanizada, garantizar la resistencia a la corrosión de la pieza y reducir la cantidad de hollín generado.
(2) Soldadura con protección de gas y electrodo de fusión
Para soldar acero galvanizado se recomienda la soldadura con protección de gas, como la soldadura con gas CO2 o una mezcla de Ar+CO2 o Ar+O2. El tipo de gas protector utilizado puede tener un impacto significativo en el contenido de Zn en la soldadura. El uso de CO2 puro o CO2+O2 produce un mayor contenido de Zn en la costura de soldadura, mientras que el uso de Ar+CO2 o Ar+O2 conduce a un menor contenido de Zn. La corriente de soldadura tiene un efecto mínimo sobre el contenido de Zn en la soldadura, con una ligera disminución a medida que aumenta la corriente.
La soldadura con protección de gas produce más polvo de soldadura en comparación con la soldadura por arco manual, por lo que es importante prestar especial atención al escape. El tamaño y la composición del hollín se ven influenciados principalmente por la corriente y el gas de protección; una mayor corriente o una mayor cantidad de CO2 u O2 en el gas provocan más hollín. El contenido de ZnO en el hollín también aumenta, con un contenido máximo de alrededor del 70%.
La profundidad de fusión del acero galvanizado es mayor que la del acero no galvanizado bajo las mismas especificaciones de soldadura. Las juntas en T, las juntas traslapadas y la soldadura hacia abajo son más propensas a la porosidad, y la velocidad de soldadura tiene un impacto significativo, especialmente para las aleaciones de acero galvanizado. En la soldadura multilínea, las líneas de soldadura posteriores son más sensibles a la porosidad que las líneas anteriores.
La composición del gas protector tiene poco efecto sobre las propiedades mecánicas de las uniones y, habitualmente, se utiliza CO2 puro para soldar. Los parámetros de soldadura para juntas a tope en forma de I, juntas traslapadas y juntas en T de placas de acero galvanizado que utilizan soldadura con CO2 se enumeran en las tablas 1-3.
Tabla 1 Parámetros de especificación para la soldadura con CO2 de una junta a tope de placa de acero galvanizado en forma de I
Espesor/mm | Espacio libre/mm | Posición de soldadura | Velocidad de alimentación de alambre/mm*s-1 | Tensión de arco/V | Corriente de soldadura/A | Velocidad de soldadura/mm*s-1 | Observación |
---|---|---|---|---|---|---|---|
1.6 | 0 | Soldadura plana | 59,2~80,4 | 17~20 | 70~90 | 5.1~7.2 | Alambre de soldadura ER705-3
Diámetro 0,9 mm. Extensión seca 6,4 mm |
Soldadura vertical hacia abajo | 82,5 | 17 | 90 | 5.9 | |||
Soldadura Horizontal | 50,8 | 18 | 100 | 8.5 | |||
Soldadura aérea | 50,8~55 | 18~19 | 100~110 | - | |||
3.2 | 0,8~1,5 | Soldadura plana | 71,9 | 20 | 135 | 5.5 | |
soldadura vertical | 71,9 | 20 | 135 | 7.6 | |||
Soldadura Horizontal | 71,9 | 20 | 135 | 6.8 | |||
Soldadura aérea | 71,9 | 20 | 135 | 5.5 |
Tabla 2 Parámetros de especificación para la soldadura con CO2 de juntas superpuestas de placa de acero galvanizado
Espesor/mm | Posición de soldadura | Velocidad de alimentación de alambre/mm*s-1 | Tensión de arco/V | Corriente de soldadura/A | Velocidad de soldadura/mm*s-1 | Observación |
---|---|---|---|---|---|---|
1.6 | Soldadura plana | 50,8 | 19 | 110 | 5.1~6.8 | Alambre de soldadura ER705-3
Diámetro 0,9 mm. Extensión seca 6,4 mm |
Soldadura Horizontal | 50,8 | 19~20 | 100~110 | 5,5 ~ 6,8 | ||
Soldadura aérea | 50,8 | 19~20 | 100~110 | 4.2~5.1 | ||
soldadura vertical | 50,8 | 18 | 100 | 5,5 ~ 6,8 | ||
3.2 | Soldadura plana | 67,2 | 19 | 135 | 3.8~4.2 | |
Soldadura Horizontal | 67,2 | 19 | 135 | 3.8~4.2 | ||
Soldadura vertical hacia abajo | 67,7 | 19 | 135 | 5.1 | ||
Soldadura aérea | 59.2 | 19 | 135 | 3.4~3.8 |
Tabla 3 Parámetros de especificación para soldadura con CO2 de junta a tope de placa de acero galvanizado en forma de T (junta en ángulo)
Espesor/mm | Posición de soldadura | Velocidad de alimentación de alambre/mm*s-1 | Tensión de arco/V | Corriente de soldadura/A | Velocidad de soldadura/mm*s-1 | Observación |
---|---|---|---|---|---|---|
1.6 | Soldadura plana | 50,8~55 | 18 | 100~110 | - | Alambre de soldadura ER705-3
Diámetro 0,9 mm. Extensión seca 6,4 mm |
soldadura vertical | 55~65,6 | 19 | 110~120 | - | ||
Soldadura aérea | 55 | 19~20 | 110 | 5.9 | ||
Soldadura Horizontal | 59.2 | 20 | 120 | 5.1 | ||
3.2 | Soldadura plana | 71,9 | 20 | 135 | 4.7 | |
Soldadura Vertical | 71,9 | 20 | 135 | 5.9 | ||
Soldadura Horizontal | 71,9 | 20 | 135 | 4.2 | ||
Soldadura aérea | 71,9 | 20 | 135 | 5.1 |