La soldadura de barras colectoras de cobre no es común en la construcción de energía de nuestra empresa debido a sus altos requisitos y dificultad. Sin embargo, para las barras eléctricas de la planta de carbón se eligieron barras colectoras de cobre, por su conductividad superior.
Después de llevar a cabo experimentos de soldadura y aplicaciones de soldadura de productos, la filial de soldadura ha dominado esencialmente la tecnología de soldadura de barras colectoras de cobre, sentando las bases para la futura soldadura de barras colectoras de cobre en nuestra empresa y elevando nuestra tecnología de soldadura a un nuevo nivel.
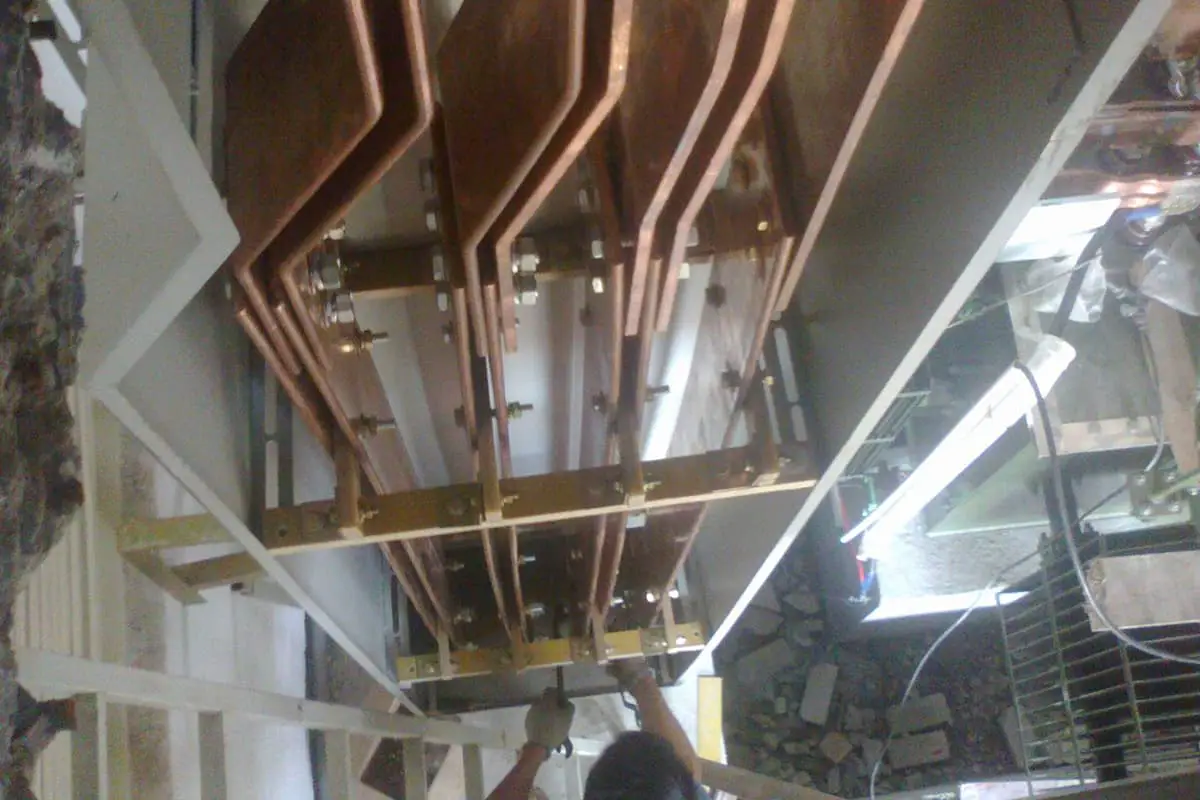
1 . Características y proceso de soldadura de barras colectoras de cobre.
La conexión de barras colectoras de cobre en centrales eléctricas implica principalmente dos métodos: fijación por tornillos y soldadura. El cobre tiene una excelente conductividad eléctrica, conductividad térmica, resistencia al calor y formabilidad. El cobre puro industrial no tiene menos del 99,5% de ωcu.
dos . Características de la soldadura de cobre.
2.1 Alta conductividad térmica
La conductividad térmica del cobre puro a temperatura ambiente es 8 veces mayor que la del acero al carbono. Para calentar un trozo de cobre puro hasta su temperatura de fusión, se requiere una gran cantidad de calor.
Por lo tanto, se requiere una fuente de calor concentrada durante la soldadura; de lo contrario, el calor se disipará rápidamente. Al soldar cobre puro, se debe precalentar la pieza de trabajo.
2.2 Alta sensibilidad al craqueo térmico
Varios materiales a base de cobre siempre contienen una cierta cantidad de impurezas que forman un eutéctico de bajo punto de fusión. La presencia de una película eutéctica de bajo punto de fusión sobre la parte solidificada o en la zona afectada por el calor puede provocar grietas bajo tensión de soldadura.
2.3 Alta tendencia a los poros
Los poros en el metal de soldadura de cobre son causados principalmente por hidrógeno. Cuando el cobre puro contiene una cierta cantidad de oxígeno o cuando el gas CO se disuelve en cobre puro, los poros también pueden ser causados por el vapor de agua y la reacción del CO con O para generar gas CO2.
Generalmente, los poros se distribuyen en el centro de la soldadura y cerca de la línea de fusión.
2.4 Tendencia al deterioro del desempeño conjunto
Durante la soldadura, el cobre sufre inevitablemente oxidación y desgaste hasta cierto punto, lo que provoca diversos defectos de soldadura. Esto podría conducir potencialmente a una disminución de la resistencia, plasticidad, resistencia a la corrosión y conductividad eléctrica de la unión soldada.
En el proceso de soldadura por fusión de cobre, el tamaño de grano en la zona de soldadura y afectada por el calor aumenta significativamente, afectando en cierta medida las propiedades mecánicas de la unión.
Para mejorar el rendimiento de la unión, no sólo es crucial minimizar los efectos térmicos, sino también controlar el contenido de impurezas de la soldadura y modificar el metal de soldadura mediante aleación.
3 . Proceso de soldadura de autobuses de cobre
3.1 Selección del método de soldadura
Los métodos de soldadura más comunes para el cobre son la soldadura con gas y la soldadura manual con gas inerte de tungsteno (TIG).
Sin embargo, para mejorar la calidad de la soldadura, se prefiere la soldadura TIG manual. Este método de soldadura es superior debido a su calor concentrado, baño de fusión de fácil control y, principalmente, su efectividad en la soldadura de materiales con un espesor (δ) inferior a 12 mm.
La soldadura TIG proporciona un arco estable, una excelente protección y un funcionamiento flexible, lo que la hace especialmente adecuada para soldadura de espesor medio.
3.2 Selección de materiales de soldadura
Los materiales de soldadura de cobre se refieren a alambres y fundentes de soldadura. Alambre de soldadura de relleno: Al realizar soldadura TIG manual, es necesario agregar manualmente alambre de soldadura de relleno. La marca, la composición del alambre de soldadura y la procesabilidad de la soldadura, las propiedades mecánicas de las juntas y la resistencia a la corrosión están estrechamente relacionadas.
Al elegir el alambre para soldadura de aporte, las primeras consideraciones deben ser la marca del metal base, el espesor de la placa, la estructura del producto y las condiciones de construcción.
Por lo tanto, al soldar barras colectoras de cobre, se selecciona un alambre de soldadura de relleno con una composición similar al metal base. Los parámetros técnicos del alambre de soldadura de cobre se muestran en la Tabla 1.
Tabla 1: Parámetros técnicos del alambre de soldadura de cobre
Nota | Modelo estándar GB | Composición química primaria | Fracción de masa (%) |
Punto de fusión | Uso primario |
SA201 (Scu-2) |
HSCu | Sn-1.1 | Si-0.4 | 1050 | Soldadura por arco de cobre puro y tungsteno (Uso del Flujo 301) |
HS201(Scu-2) | Mn-0,4 | Cobre (se mantuvo) |
Parámetros técnicos del alambre de soldadura de cobre.
Soldadura: Durante la soldadura por arco de argón, la superficie del metal fundido tiende a oxidarse para formar óxido cuproso (Cu2O). Su presencia a menudo provoca defectos como porosidad de la soldadura, grietas e inclusiones de escoria. Los parámetros técnicos de la soldadura se muestran en la Tabla 2.
4. Preparación previa a la soldadura
La preparación previa a la soldadura se refiere principalmente a la limpieza de la pieza de trabajo y los materiales de soldadura, y al diseño y procesamiento de la ranura antes de soldar.
Es fundamental limpiar la superficie del alambre de soldadura y ambos lados de la ranura de la placa de cobre dentro de los 30 mm para eliminar grasa, humedad, óxidos y otras impurezas. El procesamiento de ranuras se realiza mediante un cincel neumático o una máquina biseladora.
Los tipos de procesamiento de ranuras para soldadura de cobre se muestran en la Tabla 3.
Tabla 2: Parámetros técnicos del fundente para soldadura
Nota | Componentes primarios (por fracción de masa) % | Punto de fusión (℃) | Ámbito de aplicación | |||||
Na2B407 | H3B03 | En F | NaCl | KCI | Otro | |||
CJ301 | 16,5-18,5 | 76-79 | – | – | – | AIP04 4-5.5 |
650 | Soldadura de cobre con gas |
Tabla 3: Tipos de procesamiento de ranuras de soldadura para cobre
Nombre del material | Espesor de la placa (mm) | Diagrama | Tipo de bisel | Tipo de articulación | Dimensiones de la estructura conjunta | ||
El | B (mm) |
PAG (mm) |
|||||
Cobre puro | ≤3 |
|
forma de yo | Junta a tope | – | 1-2 | |
≥4 |
|
formato V | Junta a tope | 30°-35° | B | 1-2 | |
≤12 |
|
Forma de V única | Junta en T | 50°~60° | 2-3 | 1-2 |
Nota: 'b' se puede configurar de acuerdo con los requisitos del proceso y la separación de las juntas en el sitio.
Tabla 4: Parámetros del proceso de soldadura para cobre
Espesor de la placa (mm) |
Diámetro del electrodo de tungsteno (mm) |
Diámetro del alambre de soldadura (mm) |
corriente de soldadura (A) |
Flujo de cloro gaseoso (l/min) |
Temperatura de precalentamiento (ºC) |
1-4 | 2.0 | 2.0 | 140-220 | 15-16 | 200-300 |
5-12 | 2.5 | 2.0 | 240-260 | 16-18 | 600-650 |
5. Puntos clave para soldar barras colectoras de cobre
5.1 El lugar de soldadura del bus de cobre debe mantener una temperatura ambiente superior a 5°C;
5.2 El gas de protección utilizado es argón;
5.3 El alambre de soldadura de la barra colectora de cobre debe ser alambre de cobre puro HS201. se agrega fundente CJ301 y luego se mezcla con etanol anhidro (alcohol) hasta obtener una consistencia pastosa, que luego se extiende sobre la superficie de soldadura biselada antes de soldar;
5.4 El alambre de soldadura se calienta y se recubre con CJ301 antes de soldar;
5.5 Para seleccionar los parámetros del proceso de soldadura, la soldadura manual por arco de tungsteno utiliza electrodo positivo de corriente continua (DCEP); los parámetros del proceso de soldadura de cobre puro se muestran en la Tabla 4;
5.6 La máquina de soldar debe funcionar bien, con ajuste de corriente flexible y operación conveniente;
5.7 El método de precalentamiento de la barra colectora de cobre es el calentamiento eléctrico o por llama;
5.8 Para la selección de la temperatura de precalentamiento, las piezas con un espesor δ inferior a 4 mm se pueden precalentar adecuadamente, mientras que aquellas con un espesor δ superior a 4 mm se deben precalentar a una temperatura de 600-650 ℃;
5.9 Se debe evitar en la medida de lo posible la soldadura en condiciones restrictivas. Es necesario un control estricto de la temperatura entre pasadas durante el proceso de soldadura, utilizando soldadura con pequeña oscilación y baja energía de línea;
5.10 La costura de soldadura debe ser soldada por puntos, con una longitud no menor a 10 mm. El número de puntos de soldadura debe estar distribuido uniformemente y no ser inferior a tres;
5.11 Para soldar piezas con un espesor δ mayor a 4mm se debe utilizar un proceso de soldadura multicapa y multipasada;
5.12 Los puntos negros causados por las altas temperaturas durante la soldadura deben limpiarse inmediatamente. La limpieza entre pasadas debe realizarse con un cepillo de acero inoxidable;
5.13 Se debe comprobar la calidad de los puntos de soldadura antes de soldar. La soldadura sólo puede continuar después de confirmar que no hay defectos;
5.14 Se deben reforzar los pasos intermedios de inspección. Por ejemplo, después de la soldadura por puntos, entre capas de soldadura y después de completar toda la soldadura, las inspecciones deben realizarse estrictamente de acuerdo con los requisitos del proceso de soldadura para garantizar la calidad de la soldadura.