Resumen:
La conexión de aluminio y acero puede producir piezas de automóvil ligeras. Sin embargo, el agrietamiento de compuestos intermetálicos causado por la soldadura de estos metales diferentes puede afectar significativamente el rendimiento de la unión.
Este post presenta los principales métodos de soldadura láser de aluminio y acero y explica el estado de la investigación en los últimos años.
El acero galvanizado es un sustrato de acero recubierto con capas de zinc de diferentes espesores. El proceso de galvanizado se clasifica en galvanoplastia y galvanización en caliente.
La capa de zinc no sólo proporciona protección física sino que también ofrece protección electroquímica al sustrato de acero.
Debido a su excelente resistencia a la corrosión, el acero galvanizado se utiliza ampliamente en diversos sectores como el transporte, la energía eléctrica, la construcción, las instalaciones de calefacción, la instrumentación y el mobiliario.
En particular, la aplicación de acero galvanizado ordinario, acero galvanizado de alta resistencia y acero galvanizado de ultra alta resistencia en la industria del automóvil mejora la resistencia a la corrosión y prolonga la vida útil de la carrocería y otras piezas.
Sin embargo, la presencia de una capa de zinc dificulta la soldadura por fusión de placas de acero galvanizado. Esto se debe a que el punto de fusión del zinc es 420 ℃, su punto de ebullición es 908 ℃, mientras que el punto de fusión del acero base es 1300 ℃ y su punto de ebullición es 2861 ℃.
Durante el proceso de fusión y soldadura, el zinc tiende a evaporarse y oxidarse ampliamente, lo que provoca defectos como poros, fusión incompleta y grietas.
El aluminio y sus aleaciones son conocidos por sus propiedades livianas (con una densidad de 2,7 g/cm3), alta resistencia específica, excelente conductividad eléctrica y térmica, resistencia a la corrosión y la capacidad de conservar buenas propiedades mecánicas incluso a bajas temperaturas.
En el mundo actual, la energía, la seguridad y la protección del medio ambiente se han convertido en cuestiones cruciales. Con la creciente preocupación por la contaminación ambiental y la crisis energética, lograr vehículos livianos se ha convertido en un enfoque global.
En consecuencia, se han llevado a cabo extensas investigaciones sobre estructuras compuestas de aluminio/magnesio, aluminio/titanio, titanio/aluminio y aluminio/acero en todo el mundo.
Las estructuras compuestas de aluminio/acero aprovechan al máximo las ventajas de ambos materiales para reducir el peso y la contaminación, y han encontrado amplias aplicaciones en las industrias de la automoción, la aviación y la construcción naval.
La aplicación de conexiones de aluminio y acero en el panel de la puerta de un automóvil se ilustra en la siguiente figura.
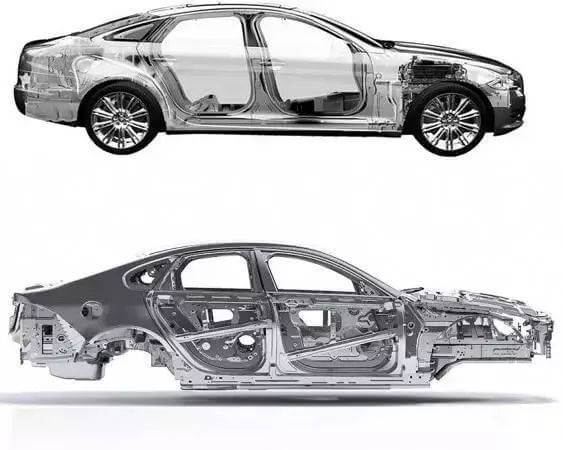
La tecnología de soldadura por arco láser híbrida, como se muestra en el diagrama esquemático experimental de la Fig. 2, es un método de soldadura nuevo y eficiente desarrollado en la década de 1970.
La alta densidad de energía del láser permite una penetración más profunda, pero la capacidad de puenteo de espacios es deficiente y la precisión del ensamblaje debe ser alta.
El rango de calentamiento del arco es amplio, lo que permite obtener una soldadura más amplia, pero el puente del arco hasta el espacio es bueno.
Al utilizar sus respectivas características, la tecnología de soldadura por arco láser híbrida puede lograr una soldadura a tope amplia y una gran penetración.
El plasma producido por el láser puede estabilizar el arco, haciendo que el proceso de soldadura híbrida sea adaptable y eficiente.
Honggang Donga et al. inventó un método para conectar metales diferentes utilizando grandes fuentes de calor de arco y láser compuesto.
La patente se centra en la soldadura híbrida con fuente de calor por arco láser con un punto pequeño, que no se puede aplicar a la conexión entre acero y aluminio, acero y cobre y otros metales diferentes.
En este método, el láser tiene un efecto estabilizador obvio sobre el arco, que se utiliza para fundir el metal de aportación y el metal base de bajo punto de fusión.
El láser de punto grande puede controlar con precisión la entrada de calor.
Las pruebas de propiedad de tracción en uniones de aleación de aluminio 5A02 y acero galvanizado obtenidas mediante este método muestran que la posición de falla de la muestra ocurre en la zona afectada por el calor de soldadura en un lado del metal base de aleación de aluminio, y no en la zona de conexión de soldadura fuerte. La resistencia de la unión puede alcanzar los 153,1 MPa. Qin y otros adoptan la soldadura compuesta por láser MIG de acero galvanizado/aleación de aluminio y alambre de soldadura AlSi5.
Los resultados experimentales muestran que la interfaz de soldadura fuerte produce de 2 a 4 μm y los grupos de fases son FeAl2, Fe3Al5 y Fe4Al13. La resistencia máxima a la tracción de la junta es de 247,3 MPa.
Wangshujun et al. También utilizó la tecnología de soldadura híbrida láser MIG y experimentó con tres soldaduras diferentes: AlSi5, AlSi12 y AlMg5 para estudiar los efectos de los compuestos intermetálicos, la microestructura de la soldadura y la formación después de la adición de Si y Mg.
Los resultados muestran que aumentar el contenido de Si puede refinar los granos en la zona de fusión y aumentar la microdureza de la zona de fusión. La microdureza de la soldadura Al-Si en la zona de fusión es mayor que la de la soldadura Al-Mg.
El espesor promedio de la capa de compuesto intermetálico para soldaduras de AlSi12, AlSi5 y AlMg5 es de 0,90 μm, 1,49 μm y 2,64 μm, respectivamente.
Se concluyó que la presencia de Si en soldaduras inhibe la difusión de Fe y reduce la formación de compuestos intermetálicos.
El análisis XRD de la capa intermedia revela que las capas de compuestos intermetálicos correspondientes a AlSi5 y AlSi12 constan de las fases Fe2Al5, Fe4Al13 y Al0,5Fe3Si0,5, mientras que las correspondientes a AlMg5 constan de las fases FeAl2, Fe2Al5 y Fe4Al13.
La resistencia conjunta de las soldaduras de AlMg5, AlSi5 y AlSi12 es de 178,9 MPa, 172,43 MPa y 144 MPa, respectivamente.
Se concluyó que un aumento en el contenido de Si es perjudicial para la resistencia de las juntas, mientras que la adición de Mg aumenta la resistencia de las juntas. Sin embargo, no se ha explicado cómo el Si y el Mg afectan la fuerza de las articulaciones.
Tommy y col. realizó un estudio sobre la interacción entre el láser y el arco de plasma durante la soldadura por arco láser híbrido y desarrolló un cabezal de soldadura por arco láser coaxial híbrido.
l soldadura láser
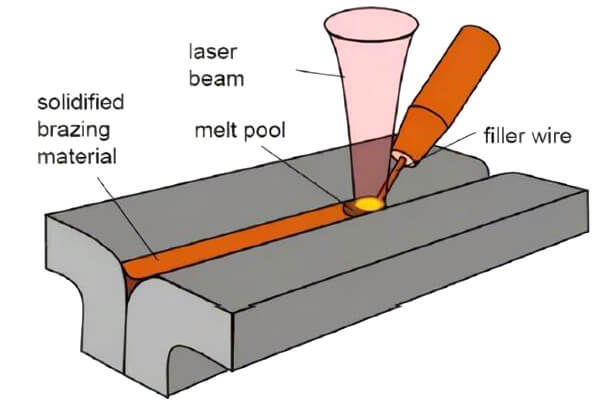
La soldadura fuerte implica el uso de soldadura con un punto de fusión más bajo que el del metal base. Al calentar a una temperatura superior al punto de fusión de la soldadura e inferior al punto de fusión del metal base, la soldadura se funde mientras el metal base permanece sólido.
Luego, la soldadura líquida humedece el metal base y, bajo la acción capilar del espacio de soldadura fuerte, llena automáticamente cualquier espacio en el metal base y se difunde con él para crear una unión fuerte.
La soldadura fuerte por fusión combina las características de la soldadura fuerte y la soldadura por fusión, lo que la hace ideal para conectar materiales diferentes con grandes diferencias en propiedades físicas.
Cuando se sueldan acero y aluminio, el acero permanece sólido mientras que el aluminio y la soldadura se funden. La conexión de soldadura fuerte resultante se forma en el lado de acero/soldadura, mientras que la soldadura por fusión se produce en el lado de soldadura/aluminio.
El principio básico de la soldadura fuerte por fusión para acero y aluminio es combinar aluminio fundido y soldadura con acero sólido a través de una reacción de interfaz.
En este método, se puede agregar o no soldadura para fines de soldadura.
Peyre et al. realizó un estudio sobre la unión de acero galvanizado y aleaciones de aluminio mediante soldadura fuerte por fusión láser sin soldadura.
Sus hallazgos indican que se forma una capa de interfaz de 2 a 20 μm de espesor a lo largo de la interfaz acero-aluminio.
La capa se compone principalmente de la fase Fe2Al5, con una dureza de hasta 1200HV. Esto provoca grietas en la junta, provocando una reducción significativa de las propiedades mecánicas de la junta.
La evaporación del zinc produce poros, pero una capa de zinc de 10 μm de espesor promueve la humectación y la extensión del aluminio sobre el acero.
Las pruebas de tracción indican que el flujo del recubrimiento sobre la superficie del acero galvanizado puede inhibir la evaporación del zinc. El acero no galvanizado, sin embargo, tiene una baja resistencia mecánica.
Para controlar la formación de compuestos intermetálicos Fe-Al y mejorar el rendimiento de la unión, algunos investigadores han utilizado soldadura durante la soldadura fuerte con láser para cambiar la composición química de la unión.
Serra et al. utilizó soldadura 4047 (Al-12Si) en la conexión de soldadura fuerte por fusión láser de aluminio/acero, lo que dio como resultado una unión continua sin macrodefectos significativos y una capa delgada de compuesto intermetálico Fe Al-Si en la interfaz acero/soldadura.
Se investigó el efecto del Si sobre el crecimiento de compuestos intermetálicos Fe-Al utilizando soldadura de Al-12Si. El mecanismo propuesto sugiere que el Si reduce la temperatura de fusión del aluminio, influye en la viscosidad y la tensión superficial del aluminio fundido y, posteriormente, afecta el ángulo y el ancho de humectación de la soldadura.
Además, algunos estudiosos han añadido Mg, Cu y otros elementos a la soldadura para explorar el efecto de la aleación de soldadura en la microestructura y las propiedades de la soldadura.
Dharmendra et al. realizó una prueba de soldadura fuerte por fusión en una junta traslapada hecha de acero galvanizado DP600 y aleación de aluminio AA6016 utilizando láser Nd:YAG de pulso continuo.
En la prueba utilizaron alambre de soldadura de Zn-Al que contenía 85 % de Zn y 15 % de Al y variaron la potencia del láser, la velocidad de soldadura y la velocidad de alimentación del alambre.
Los investigadores descubrieron que el espesor de la capa de reacción estaba entre 3 y 23 μm.
Cuando el aporte de calor estuvo entre 60 y 110J/mm, la resistencia a la tracción de la unión alcanzó los 220MPa, con la posición de fractura ubicada lejos de la soldadura y cerca del lado de la aleación de aluminio.
A velocidades de soldadura de 0,5 y 0,8 m/min, los espesores correspondientes de los compuestos intermetálicos fueron de 8 y 12 μm, respectivamente.
Los ensayos de tracción demostraron que la unión presentó mayor resistencia mecánica cuando el espesor del compuesto intermetálico estuvo entre 8 y 12μm.
Si el espesor era inferior a 8μm, la resistencia mecánica aumentaba a medida que aumentaba la capa intermetálica, mientras que si era superior a 12μm, la resistencia mecánica disminuía.
Se explicó que cuando la capa compuesta es delgada, se inicia el agrietamiento a lo largo de la frágil capa compuesta intermetálica, lo que resulta en una resistencia a la fractura muy baja.
Por otro lado, cuando la capa compuesta es gruesa, la resistencia mecánica también es baja debido a la fragilidad de la capa en relación con otras zonas.
Laukant et al. realizó una prueba de soldadura fuerte por fusión láser utilizando soldadura ZnAl2 sobre aluminio/acero. Los resultados mostraron que se produjeron capas de compuestos intermetálicos de aproximadamente 5 μm de FeAl y que la fuerza de corte de la unión alcanzó hasta 9 KN.
De manera similar, Rajashekhara Shabadi et al. realizó una prueba de soldadura fuerte por fusión láser utilizando soldadura ZnAl30 en AA6016 y acero galvanizado con bajo contenido de carbono. El compuesto intermetálico formado en los resultados de la prueba es principalmente Fe2Al5Znx, que también puede contener ZnFeAl3, con un espesor de aproximadamente 10μm.
Recientemente, algunos académicos han realizado experimentos de soldadura fuerte por fusión láser en acero aluminizado de alta resistencia y aleaciones de aluminio.
Por ejemplo, Windmann et al. Realizó una prueba de soldadura fuerte por fusión láser utilizando soldadura AlSi3Mn y descubrió la formación de la fase Al8Fe2Si en la interfaz AlSi3Mn/Mn22B5.
Además, el espesor del compuesto intermetálico creado en la interfaz Mn22B5/AlSi3Mn es de 2 a 7 μm, y la resistencia al corte de la junta es de 21 a 74 MPa.
Al precalentar la superficie del acero antes de soldar, la resistencia de la unión se puede aumentar de 210 a 230 MPa.
Investigaciones recientes han demostrado que tanto la soldadura de Al-Si como la de Zn-Al crean inevitablemente compuestos intermetálicos.
Sin embargo, la secuencia de crecimiento de los compuestos intermetálicos FeAl-Si y la identificación de la fase de reacción de la soldadura Zn-Al requieren más investigación.
La soldadura por fusión láser es una tecnología prometedora para conectar acero y aluminio.
Conclusión
La soldadura por arco láser híbrida se utiliza principalmente para soldar placas más gruesas debido a su alta eficiencia de soldadura.
La soldadura fuerte por fusión por láser tiene un gran potencial de aplicación en la producción de automóviles ligeros.
El proceso de soldadura fuerte por fusión por láser se ha utilizado para conectar metales delgados y diferentes hechos de aluminio y acero mediante soldaduras de Al-Si y Zn-Al.
Sin embargo, todavía existen varios desafíos en la soldadura láser de aleaciones de acero galvanizado/aluminio para la fabricación de automóviles. Por ejemplo, la baja absortividad del material a la energía láser da como resultado la generación de plasma, lo que puede afectar la estabilidad del proceso de soldadura.
Además, el proceso de conectar aluminio y acero puede producir compuestos intermetálicos frágiles de Fe-Al. Además, es necesario considerar la compatibilidad metalúrgica de la soldadura fundida con el metal base de aleación de aluminio y su humectabilidad con el acero del metal base.
Finalmente, es crucial controlar y prevenir defectos de soldadura como poros, grietas, fusión incompleta e inclusión de escoria.