La microestructura del acero martensítico (MS) es predominantemente martensítica. Tiene una alta resistencia a la tracción, con una resistencia máxima que alcanza los 1600 MPa. Para aumentar su plasticidad, el acero debe ser templado, lo que le permitirá mantener una conformabilidad suficiente a pesar de su alta resistencia.
Actualmente, el acero martensítico tiene el mayor nivel de resistencia entre las placas de acero de alta resistencia disponibles comercialmente.
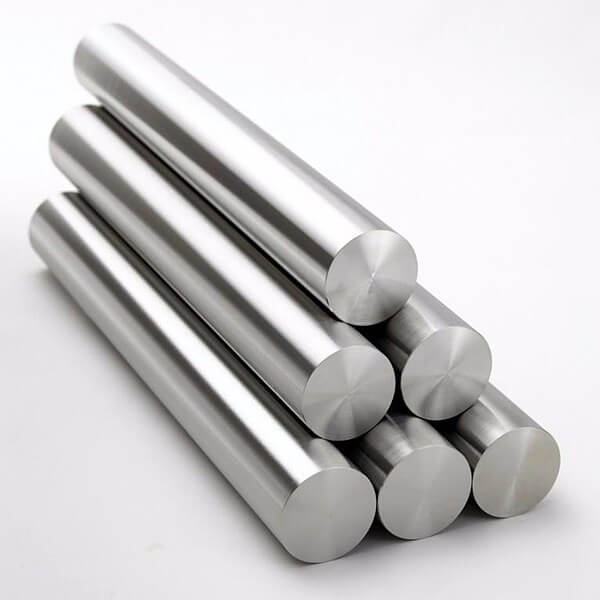
El acero martensítico se clasifica en dos tipos:
- Acero simple de la serie Cr13, incluidos 1Cr13, 2Cr13, 3Cr13, 4Cr13, etc.
- Acero martensítico reforzado con aleación multielementos como 1Cr11MoV y 1Cr12WMoV, que tiene como base Cr12 e incluye elementos como W, Mo, V, Ti, Nb y otros para aumentar su resistencia térmica.
El acero martensítico es conocido por su fuerte tendencia al templado, que se puede lograr enfriando con aire austenita a alta temperatura para formar una estructura de martensita. Sin embargo, el 1Cr13 con bajo contenido de carbono forma una estructura semimartensítica con martensita y ferrita después del enfriamiento.
El primer tipo de acero martensítico se utiliza principalmente en condiciones generales de resistencia a la corrosión, como en atmósferas, agua de mar y ácido nítrico, así como en componentes que requieren un cierto nivel de resistencia. El último tipo se utiliza principalmente para acero resistente al calor.
Soldabilidad del acero martensítico.
Los aceros martensíticos tienen una fuerte tendencia a endurecerse. Cuando se enfría con aire, se puede producir martensita de alta dureza. Sin embargo, esto también conduce a la peor soldabilidad entre todos los aceros inoxidables y los aceros de alta aleación resistentes al calor.
Los siguientes problemas se encuentran comúnmente durante la soldadura:
1. Soldadura por fisura en frío
Este es un problema bien conocido del acero martensítico.
Por un lado, se debe a su alta templabilidad. Por otro lado, también se debe a la baja conductividad térmica de la martensita, que puede provocar importantes tensiones internas durante la soldadura.
En particular, el acero martensítico con alto contenido de carbono y las estructuras de soldadura rígidas son propensos a desarrollar grietas en frío durante la soldadura.
Para resolver esto, a menudo son necesarias medidas como el precalentamiento y el tratamiento térmico posterior a la soldadura.
2. Debilitamiento de las uniones soldadas
(1) Fragilidad por sobrecalentamiento cerca de la costura
Los aceros martensíticos suelen situarse en el límite de la martensita y la ferrita debido a sus características compositivas.
Cuando la velocidad de enfriamiento es alta, se pueden formar grandes granos de martensita cerca de la junta, reduciendo su plasticidad.
Si la velocidad de enfriamiento es baja, se formará una estructura gruesa de ferrita sólida y carburos, lo que disminuye significativamente la forma de la junta.
Por tanto, es fundamental controlar la velocidad de enfriamiento durante la soldadura.
(2) Debilidad debida al temperamento
Los aceros martensíticos y sus uniones soldadas pueden ser susceptibles a la fragilización por temple, lo que puede reducir significativamente su tenacidad a la fractura, cuando se calientan y enfrían lentamente en el rango de temperatura de 375 a 575°C.
Por lo tanto, es crucial evitar este rango de temperatura durante el tratamiento térmico para evitar la fragilidad del temperamento.

Puntos clave del proceso de soldadura del acero martensítico
1. Método de soldadura
El acero martensítico se puede soldar utilizando todos los métodos de soldadura por fusión, excepto la soldadura con gas, incluida la soldadura por arco de metal protegido, la soldadura por arco sumergido, la soldadura por arco de argón y tungsteno y la soldadura por arco de metal con argón, entre otras.
Sin embargo, debido a su alta sensibilidad al agrietamiento en frío, es importante limpiar minuciosamente la pieza soldada y secar la varilla de soldadura antes de soldar para garantizar condiciones bajas o incluso ultra bajas de hidrógeno.
Cuando el grado de restricción de la junta es alto, se recomienda utilizar soldadura por arco de argón y tungsteno o soldadura por arco de argón y metal.
Para minimizar el riesgo de grietas por frío, es importante aumentar adecuadamente el aporte de calor de soldadura, evitando el sobrecalentamiento y la fragilidad en las proximidades de la soldadura.
2. Materiales de soldadura
La elección de los materiales de soldadura debe basarse en el tipo de acero, el método de soldadura y las condiciones de trabajo de la unión.
Para garantizar que la unión funcione como se desea, es importante elegir materiales de soldadura que tengan una composición química cercana a la del metal base. Sin embargo, esto puede causar que la soldadura y la zona afectada por el calor se endurezcan y se vuelvan quebradizas.
A menudo es necesario un tratamiento térmico después de soldar para evitar el agrietamiento en frío. Cuando el tratamiento térmico no es posible, se pueden utilizar materiales de soldadura de acero austenítico de tipo 25-20 y 25-13 para formar soldaduras austeníticas, lo que puede aliviar la tensión de soldadura y reducir la tendencia al agrietamiento en frío debido al aumento del contenido de hidrógeno.
Las soldaduras austeníticas tienen buena plasticidad y tenacidad, pero baja resistencia, lo que las hace sólo adecuadas para uniones bajo condiciones de carga estática de baja tensión. Además, la gran diferencia en las propiedades termofísicas entre la soldadura y el metal base puede generar tensiones adicionales en la interfaz de la unión cuando se trabaja a altas temperaturas, lo que lleva a una falla temprana de la unión, por lo que no son adecuados para aplicaciones de alta temperatura.
Los electrodos con bajo contenido de hidrógeno se utilizan normalmente para soldadura por arco con varillas de soldadura y deben secarse a 400-450°C durante dos horas antes de soldar. La soldadura por arco sumergido debe utilizar un alto flujo alcalino o un ácido débil con bajo contenido de silicio, como HJ172, HJ173 o HJ251. La soldadura TIG se utiliza principalmente para soldadura de respaldo y soldadura de piezas delgadas en soldadura multicapa.
3. Precalentamiento y temperatura entre pasadas
Precalentar y mantener la temperatura entre pasadas son pasos cruciales para evitar el agrietamiento en frío durante la soldadura.
La temperatura de precalentamiento debe determinarse basándose en el contenido de carbono del acero y luego teniendo en cuenta el grado de restricción de la junta, la composición del metal de aportación y el método de soldadura. La Tabla 1 proporciona temperaturas de precalentamiento recomendadas, entradas de calor, etc. basado en la clasificación del contenido de carbono.
Si la junta tiene un alto grado de restricción, es necesario aumentar la temperatura de precalentamiento y la temperatura entre pasadas en consecuencia. La temperatura entre pasadas no debe ser inferior a la temperatura de precalentamiento.
Para soldar con materiales de soldadura de acero austenítico, es posible que no sea necesario precalentar o precalentar a baja temperatura dependiendo del espesor de la soldadura.
Tabla 1 Temperatura de precalentamiento y aporte de calor recomendados para soldar acero martensítico
Fracción de masa de carbono (%) | Rango de temperatura de precalentamiento/℃ | Entrada de calor de soldadura | Requisitos de tratamiento térmico posterior a la soldadura |
Por debajo de 0,10 | 100-150 | Aporte calorífico medio | Por espesor de pared |
0,10 ~ 0,20 | 150~250 | Aporte de calor moderado | Se requiere tratamiento térmico para cualquier espesor. |
0,20-0,50 | 250~300 | Alto aporte de calor | Se requiere tratamiento térmico para cualquier espesor. |
4. Tratamiento térmico post-soldadura
El tratamiento térmico posterior a la soldadura es otra medida importante para evitar el agrietamiento en frío durante la soldadura.
Cuando se utilizan materiales de soldadura con una composición similar a la del metal base, normalmente se requiere un tratamiento térmico de enfriamiento posterior a la soldadura. Por otro lado, cuando se suelda con materiales de soldadura de acero austenítico, generalmente no es necesario un tratamiento térmico posterior a la soldadura.
Para garantizar la transformación completa de austenita en martensita después de la soldadura, es importante evitar el tratamiento de revenido inmediatamente después de la soldadura. La junta debe enfriarse a una temperatura inferior al punto Ms y mantenerse a esa temperatura durante un tiempo específico antes de someterse a un tratamiento de templado a alta temperatura. Esto se debe a que si el templado se realiza inmediatamente después de la soldadura, la austenita se transformará en perlita y los carburos precipitarán a lo largo del límite del grano de austenita, haciendo que la unión sea muy quebradiza.
Sin embargo, para evitar el agrietamiento en frío, no se debe realizar un tratamiento de revenido a alta temperatura después de que la junta se haya enfriado a temperatura ambiente. Normalmente, el tratamiento de templado se lleva a cabo cuando la junta se enfría a 100-150°C.