Las conexiones de metal y polímero son estructuras ligeras ideales para automóviles. El proceso de conectar eficazmente materiales compuestos como el polímero reforzado con fibra de carbono (CFRP) o el polímero reforzado con fibra de vidrio (GFRP) y componentes metálicos ha recibido mucha atención con la aparición de estructuras automotrices livianas (ver Figura 1).
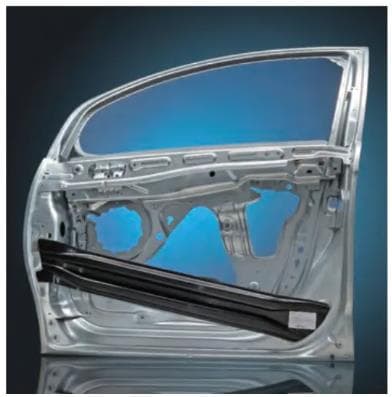
La unión entre diferentes materiales es crucial para los aspectos funcionales y de seguridad en la industria del automóvil.
Los requisitos de la industria automovilística son claros: el proceso de encolado debe ser rápido, fiable y automatizado.
La Tabla 1 enumera los tres métodos más comunes para conectar materiales compuestos y componentes metálicos en procesos industriales, entre los cuales la soldadura láser puede ser el método más reciente, pero aún necesita más investigación y mejora. Estos problemas no sólo implican la eficiencia, sino también la resistencia y el envejecimiento de las piezas de conexión. Este artículo discutirá estas preguntas en detalle.
Tabla 1: Métodos de conexión para materiales compuestos.
Fijación Mecánica | Pegamento adhesivo | soldadura por láser |
Beneficios:
– Proceso rápido y barato – Tecnología madura |
Beneficios:
– Varias pegatinas para diferentes aplicaciones. – Adecuado para unir materiales compuestos |
Beneficios:
– Proceso rápido y confiable – Alta resistencia de las articulaciones – No se requieren materiales adicionales |
Desventajas:
– Los agujeros pueden comprometer la resistencia de las fibras y los materiales compuestos. – Peso adicional de los sujetadores |
Desventajas:
– Requiere una extensa preparación de la superficie – Largo tiempo de procesamiento – Requiere materiales adicionales |
Desventajas:
– Se requiere equipo especializado – Limitado a materiales termoplásticos |
Conceptos básicos de la tecnología de soldadura láser.
El proceso de soldadura láser oculta para unir materiales compuestos y piezas metálicas consta principalmente de dos pasos. En el primer paso, la pieza metálica se trata con láser para formar una microestructura en su superficie.
Este proceso se puede lograr utilizando un láser de fibra monomodo de onda continua con una potencia nominal de aproximadamente 1 kW. El láser escanea la superficie de la pieza metálica para formar una ranura regular con una geometría de borde cortante (ver Figura 2).
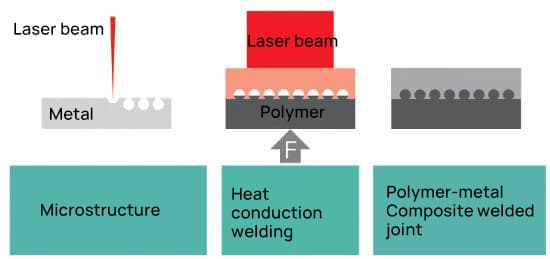
Debido a la alta intensidad del rayo láser, el metal se funde parcialmente y se vaporiza durante el proceso de ablación. La presión de evaporación pulveriza el material y parte del material salpicado se solidifica en el borde de la ranura, formando un cierto grado de estructura de borde afilado en la ranura.
Para hacer que el polímero se una más estrechamente a la superficie del metal, se puede aumentar la densidad de la microestructura de la superficie, por ejemplo, escaneando las ranuras con el rayo láser en un ángulo de 90° (ver Figura 3).
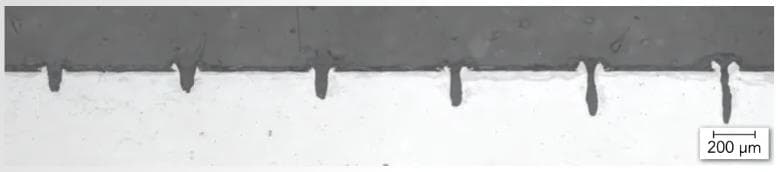
Hay otro proceso que puede lograr esta estructuración superficial. Este proceso se puede llevar a cabo utilizando láseres de pulso ultracorto (USP) para crear una estructura de superficie similar a una esponja con protuberancias cónicas.
Esta estructura superficial puede obtenerse de diversos materiales, como acero, aluminio, silicio y titanio. La adhesión del polímero a esta superficie es mejor que la de la microestructura producida mediante procesamiento con láser de fibra. El único problema es que la velocidad de procesamiento de los láseres USP es más lenta.
Dado que los láseres USP alcanzan una potencia de nivel medio de kilovatios (como se esperaba en otro proyecto de Fraunhofer), pueden ser una mejor opción para microestructurar superficies metálicas utilizadas para unir materiales compuestos.
En la segunda etapa de unión de materiales compuestos con piezas metálicas, el polímero se calienta hasta que se funde.
Luego, el polímero se presiona en la microestructura de la superficie de la pieza metálica y, después del enfriamiento, se logra una buena unión entre el polímero y la pieza metálica.
Existen diferentes métodos para calentar el polímero: un método implica calentar el polímero (como en el moldeo por inyección tradicional) y luego presionarlo en la ranura, mientras que otro método implica calentar la pieza metálica y presionarla sobre el polímero frío.
La conducción de calor hace que el polímero se derrita y fluya hacia la microestructura de la superficie de la pieza metálica. Ambos métodos pueden formar una conexión compuesta de polímero y metal.
El primer paso de la microestructuración láser es un proceso rápido y sin contacto. El proceso de conexión real se puede integrar fácilmente en procesos de producción existentes, como el moldeo por inyección o el estampado. Por tanto, el método de soldadura láser es generalmente un proceso rápido y económico, adecuado para la producción en masa.
Prueba de estrés mecánico
En aplicaciones prácticas, las piezas compuestas conectadas de metal y polímero pueden estar sujetas a cargas multiaxiales, en fase o fuera de fase. Para todas las aplicaciones surgen varias preguntas: ¿cuánta presión puede soportar esta junta? ¿Dónde se romperá? ¿Qué significa esto para el proceso de conexión?
Los expertos de Fraunhofer ILT en Alemania llevaron a cabo una serie de pruebas de presión utilizando diferentes materiales para responder estas preguntas (ver Figura 4). En un caso, fabricaron una muestra de prueba compuesta por una placa de acero inoxidable de 1,5 mm de espesor y una tira de polipropileno (PP) reforzada con fibra de vidrio de 3 mm de espesor para pruebas de tracción y corte, y un PP no reforzado para pruebas de tracción.
La superficie metálica se procesó con un láser de fibra monomodo con una potencia nominal de 1 kW y un diámetro enfocado de aproximadamente 40 μm para formar una estructura de ranura de borde cortante reproducible. La pieza de polímero se calentó con un láser semiconductor de 3 kW (potencia de aproximadamente 300-700 W), con un tamaño de punto de 7,5 x 25 mm2 . Las dos piezas se fijaron entre sí con una presión de sujeción de 3 bar, y el área de conexión de la probeta de tracción-cortante (acero + PP) fue de 150 mm 2 mientras que la de la probeta de tracción (acero + PP) fue de 100 mm 2 .
Se probaron destructivamente cinco especímenes de cada tipo. La resistencia de la conexión de la microestructura con una separación entre ranuras de 400 μm se probó bajo una carga de tracción y corte de 13,1 MPa, y la resistencia de la conexión con una separación entre ranuras de 300 μm se midió bajo una carga de tracción y corte de 15,5 MPa. En el ensayo de carga de tracción, las probetas soportaron cargas de 5,1 MPa (espaciamiento entre ranuras de 400 μm) y 9,1 MPa (espaciamiento entre ranuras de 300 μm), respectivamente.
Por supuesto, las microestructuras densas tienen una mejor adhesión, pero cabe señalar que las microestructuras densas aumentarán el tiempo de procesamiento.
Los investigadores realizaron pruebas similares en placas de aleación de magnesio. Todos los resultados de las pruebas mostraron que la tecnología de soldadura láser puede establecer una conexión fuerte y confiable entre piezas de metal y polímero.
Test de envejecimiento
Otra cuestión en la producción de automóviles es si este tipo de conexiones pueden responder a las exigencias del cambio climático y la corrosión.
Para responder a esta pregunta, los investigadores realizaron varias pruebas. Realizaron pruebas estándar de cambio climático en muestras de conexiones compuestas según VW PV 1200, con temperaturas que oscilaban entre 80 y 40 °C.
Un ciclo de prueba duró 12 horas, repetido durante 2, 10 y 30 ciclos. Se realizaron pruebas destructivas de resistencia a la tracción y al corte en las muestras antes y después de las pruebas de cambio climático.
Todos los resultados de las pruebas mostraron que las muestras podían soportar valores de presión entre 8 y 15 MPa. Durante la prueba se produjo un fenómeno interesante fuera de la zona de pegado.
Después de repetir la prueba durante 30 ciclos, las piezas fuera del área de unión no pasaron la prueba de resistencia. En otras palabras, el área de unión era incluso más fuerte que la del material de polipropileno original.
Este fenómeno fue aún más pronunciado en la prueba de corrosión. La prueba de niebla salina se realizó durante 7 días según VDA62I-415. La prueba incluyó niebla salina y condiciones de alta humedad. Antes de las pruebas, todas las muestras podían soportar fuerzas de aproximadamente 8 MPa y 15 MPa.
Después de la prueba de corrosión, todos los materiales PP/T40 se rompieron fuera del área de unión, mientras que los materiales GFRP se rompieron dentro del área de unión, pero con mayor resistencia que antes de la corrosión. Las probetas de acero presentaban oxidación, principalmente en la zona de la microestructura.
Hubo una evidente penetración de corrosión en el área de unión, pero esto no afectó significativamente a la resistencia de la unión. El área de la microestructura fuera del área de unión de la placa de aluminio también mostró signos de corrosión, pero no dentro del área de unión. Una conclusión sencilla es que se debe evitar cualquier área abierta de microestructura en el metal.
Las pruebas han demostrado que la tecnología de conexión láser puede establecer conexiones altamente fiables entre placas de metal y plástico.
Las pruebas estándar de intemperie y corrosión no afectaron la resistencia de la unión. Después de un período de envejecimiento, el plástico en sí, no la zona de unión, se rompió. Deben evitarse las áreas abiertas de microestructura en el metal.