La tecnología de soldadura láser se caracteriza por una alta eficiencia y flexibilidad del proceso. En el proceso de fabricación de automóviles, se puede utilizar para soldar carrocerías y diversos componentes automotrices, reduciendo el peso total de la carrocería, mejorando la precisión del ensamblaje de la carrocería y satisfaciendo las demandas de peso ligero y rendimiento de seguridad mejorado en la fabricación de automóviles.
También ayuda a reducir los costos de ensamblaje y estampado en la fabricación de automóviles, mejorando así la integración de la carrocería.
Por lo tanto, la forma de aplicar activa y eficazmente la tecnología de soldadura láser se ha convertido en una consideración para los fabricantes de automóviles actuales. Este artículo analizará en detalle la aplicación de la tecnología de soldadura láser.
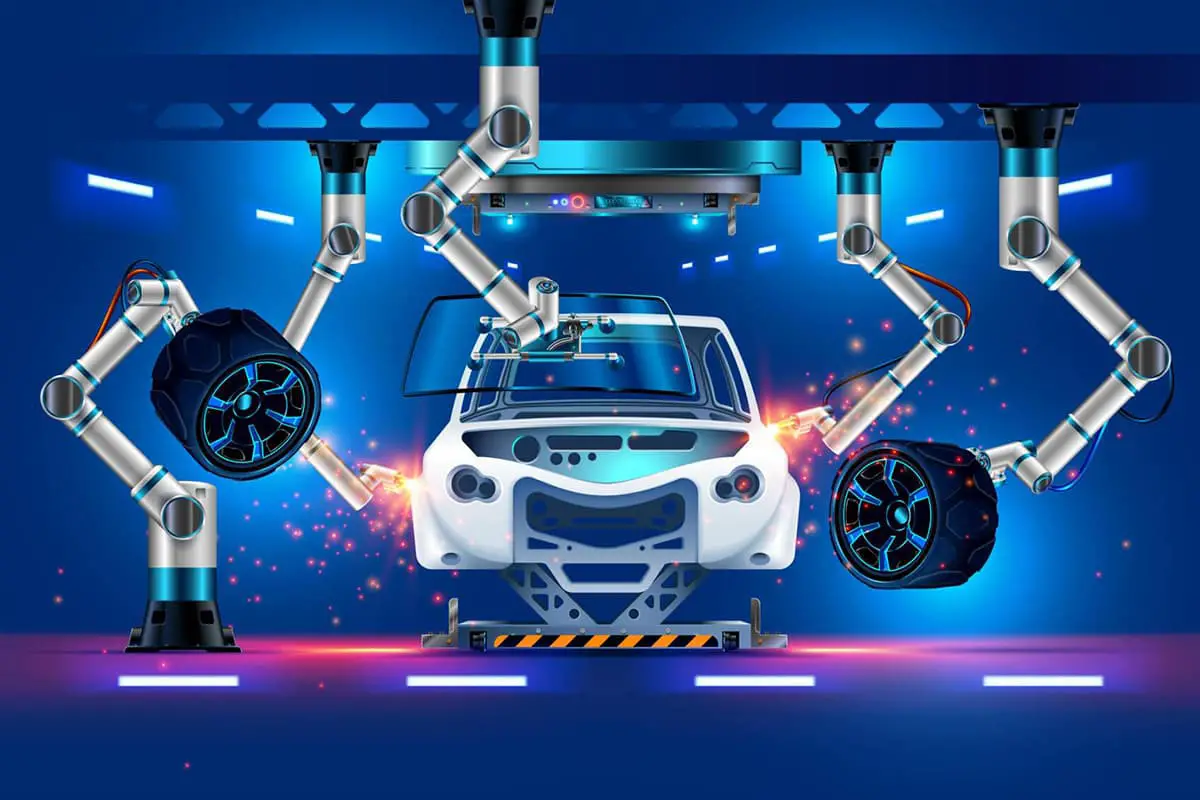
1. Descripción general de la tecnología de soldadura láser
1.1 Principio de la tecnología de soldadura láser
La soldadura láser, fundamentalmente una tecnología de soldadura por fusión, utiliza un rayo láser como fuente principal de energía. Mediante una determinada fuerza de impacto, se completa la soldadura de las piezas.
La generación del rayo láser se realiza mediante un oscilador óptico. Cuando un rayo láser de alta potencia actúa sobre la superficie del metal, puede vaporizarlo rápidamente. A medida que el líquido del metal fundido rodea el orificio vaporizado, se forma una costura de soldadura bajo la reacción de tensión y el método de calentamiento y enfriamiento, completando finalmente la soldadura del metal.
Es importante tener en cuenta que el rayo láser tiene diferentes densidades a diferentes potencias, lo que afecta la profundidad de la costura de soldadura. A medida que aumenta la densidad del rayo láser, aumenta la profundidad de fusión, lo que da como resultado una costura de soldadura más profunda. Por otro lado, reducirá la profundidad de la masa fundida, haciéndola menos profunda.
1.2 Ventajas y desventajas de la tecnología de soldadura láser
Las ventajas de la tecnología de soldadura láser desempeñan un papel importante en la fabricación de automóviles actual, y se reflejan principalmente en los siguientes aspectos: la soldadura real está sujeta a un rango pequeño de afectación por el calor y a una deformación menor. La calidad y precisión de la soldadura son relativamente altas, lo que garantiza la estética y al mismo tiempo garantiza la calidad.
La operación de soldadura específica es flexible, eficiente y puede satisfacer las necesidades de la empresa. El ruido de la construcción es bajo y tiene un impresionante efecto de ahorro de energía. Es adecuado para soldar materiales frágiles, de alta resistencia y con alto punto de fusión. Consulte la Tabla 1 para obtener más detalles.
Tabla 1: Comparación de puntuaciones de diferentes tecnologías de soldadura
Proyecto de comparación | soldadura por láser | Soldadura por haz de electrones | soldadura por arco con gas inerte de tungsteno | Soldadura por resistencia |
Eficiencia de soldadura | 6 | 7 | 4 | 8 |
Gran relación de profundidad | 9 | 8 | 3 | 4 |
Morfología de la sección transversal de soldadura. | 8 | 8 | 5 | 5 |
Soldadura a presión atmosférica | 9 | 3 | 7 | 9 |
Soldar materiales de alta reflectividad | 4 | 8 | 7 | 8 |
costo | 4 | 3 | 8 | 8 |
Costos operativos | 6 | 6 | 7 | 9 |
fiabilidad | 8 | 4 | 8 | 9 |
Alta velocidad de soldadura | 9 | 9 | 8 | dos |
- Nota: 1-10 es la puntuación de la evaluación, siendo 1 la más baja y 10 la más alta.
Sin embargo, la tecnología de soldadura láser también tiene algunas desventajas, específicamente: altos requisitos para las posiciones de soldadura, centrándose en el alcance de los requisitos de soldadura. No apto para materiales con espesores importantes.
El efecto de soldadura se ve afectado cuando se sueldan materiales con alta conductividad térmica. La baja eficiencia de conversión de energía y el rápido tiempo de solidificación de la costura de soldadura, hasta cierto punto, restringen el efecto de soldadura.
2. Aplicaciones prácticas de la tecnología de soldadura láser.
2.1 Soldadura por conducción láser
En el ámbito de la tecnología de soldadura láser, la soldadura por conducción láser se refiere al proceso en el que dos o más piezas se fusionan en un todo unificado después de fundirse y enfriarse, logrando una soldadura efectiva. Este método no requiere flujo adicional, lo que ofrece una ventaja de ahorro de costos.
Durante el funcionamiento, bajo el efecto del rayo láser, la temperatura superficial de las piezas a soldar alcanza rápidamente el punto de ebullición, vaporizando el metal y creando una cavidad, como se ilustra en la Figura 1.
La cavidad deja de profundizarse cuando la presión de retroceso del vapor metálico se equilibra con la tensión superficial y la gravedad del metal líquido. La soldadura se completa cuando se cierra la cavidad de profundidad estable, lo que marca la finalización de la soldadura láser de penetración profunda.
Actualmente, en la fabricación de automóviles, la soldadura por conducción láser se aplica ampliamente en el montaje de carrocerías, agrupamiento y soldadura de componentes. Por ejemplo, los modelos Volkswagen como Passat, Tiguan y Jettas emplean este método de soldadura al soldar los paneles laterales. Asimismo, determinados modelos de Peugeot y Citroën utilizan soldadura por conducción láser en sus puertas.
Además, según los tipos de cordones de soldadura, existen varias clasificaciones, incluidos cordones rectos simples, cordones múltiples y cordones no lineales. Debido a la simplicidad de producir un solo cordón de soldadura, ha sido ampliamente adoptado.
Volkswagen en Alemania fue pionera en la aplicación de la soldadura por puntos con láser al chasis del modelo Audi en 1985, y Toyota en Japón siguió en 1986 con la soldadura por láser alimentada por alambre para la estructura lateral de la carrocería del vehículo.
La aplicación masiva de la tecnología de soldadura por puntos láser en América del Norte comenzó en 1993, cuando Estados Unidos pretendía aumentar la competitividad de los automóviles estadounidenses en comparación con los japoneses con el Proyecto 2 mm.
Hasta la fecha, casi todos los fabricantes de automóviles de renombre en todo el mundo han adoptado ampliamente la tecnología de soldadura por puntos láser, cubriendo componentes estructurales como molduras laterales, paneles interiores de puertas, molduras de parabrisas, carcasas de ruedas, tableros, piso y pilares centrales.
Estados Unidos fue uno de los primeros en introducir láseres de alta potencia en la industria automotriz, con docenas de estaciones de procesamiento láser en el área de Detroit centradas en el corte de piezas metálicas de automóviles y equipos de soldadura. Este avance redujo el tiempo necesario para rediseñar los automóviles de cinco a dos años.
General Motors en Estados Unidos ha implementado más de veinte líneas de producción de procesamiento láser y Ford Motor Company ha empleado láseres Nd:YAG combinados con robots industriales para soldar carrocerías de automóviles, reduciendo significativamente los costos de fabricación.
En 2000, el 50% de las líneas de producción de soldadura por puntos por resistencia de los tres principales fabricantes de automóviles de Estados Unidos fueron reemplazadas por líneas de soldadura por láser.
En Japón, la aplicación exitosa de la soldadura láser en líneas de producción ha atraído la atención mundial, ya que la mayoría de los fabricantes de automóviles de todo el mundo ahora emula el método innovador de soldar láminas delgadas de acero con láser antes de transformarlas en piezas de carrocería.
Muchas empresas automotrices de renombre han establecido líneas de producción especializadas en soldadura láser: la línea de soldadura para ensamblaje de pisos de automóviles de Thyssen, la línea de procesamiento láser de engranajes de Volkswagen y Mercedes-Benz, que ha instalado equipos de procesamiento láser en 8 de las 18 fábricas.
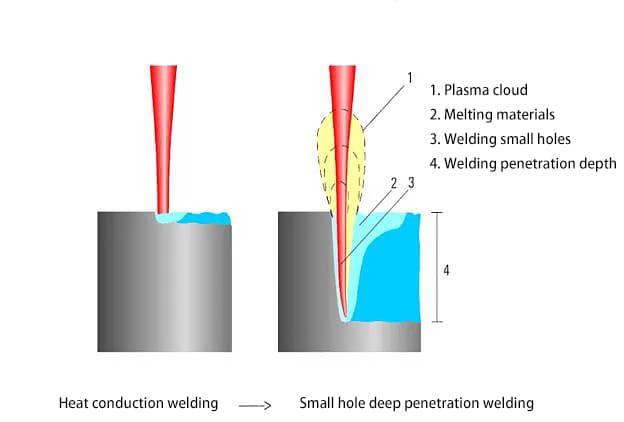
2.2 Soldadura de relleno con hilo láser
En la tecnología de soldadura láser, el principio de la soldadura por relleno con hilo láser consiste en añadir un material de soldadura específico a la costura de soldadura. El rayo láser funde el material de soldadura añadido y forma una unión soldada.
En comparación con los métodos tradicionales de soldadura inalámbrica, la soldadura por hilo láser ofrece importantes ventajas. No sólo amplía el rango de aplicación de la soldadura láser, sino que también permite soldar placas gruesas con menor potencia, consiguiendo una alta calidad de soldadura.
Es importante tener en cuenta que en la soldadura de relleno con alambre láser, tanto el alambre de soldadura como el material base deben estar fundidos. Esto crea pequeños agujeros en el material base, lo que permite que el alambre y el material base se fusionen completamente y formen un nuevo charco fundido mixto.
Este baño fundido mixto difiere significativamente del alambre de soldadura y del material base, lo que potencialmente mejora ciertas deficiencias de rendimiento del material base. El uso de alambre de soldadura con una composición adecuada como material de relleno garantiza que la costura de soldadura tenga una alta resistencia al desgaste y la corrosión.
2.3 Soldadura híbrida por arco láser
En la soldadura láser, el principio de la soldadura híbrida por arco láser combina una fuente de calor láser con un arco eléctrico para actuar juntos en un único baño fundido, logrando así la soldadura. Como se muestra en la Figura 2, este método de soldadura presenta una deformación mínima, alta velocidad y gran adaptabilidad.
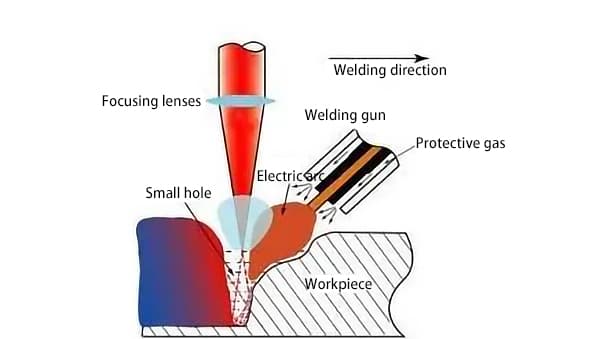
En la producción de la serie de automóviles Audi AG en Alemania, la soldadura por arco láser híbrido se aplica a la soldadura de las carrocerías más importantes fabricadas totalmente en aluminio. Esta carrocería pertenece a la lujosa serie Audi A8 de segunda generación, diseñada centrándose en la seguridad contra impactos y la resistencia a la deformación torsional. Los cordones de soldadura producidos mediante soldadura híbrida por arco y láser cumplen todos los requisitos y presentan tenacidad, alta resistencia y fusión profunda.
Para satisfacer las altas expectativas de los clientes respecto de este automóvil, cada detalle se elabora meticulosamente para garantizar la calidad de fabricación. Los estrechos cordones de soldadura de la soldadura láser híbrida cumplen con los altos estándares de apariencia requeridos para las piezas de trabajo, eliminando la necesidad de tiras de plástico para rellenar las esquinas en la parte superior de la estructura de la carrocería del automóvil.
En la fabricación de vehículos ligeros se deben cumplir todos los requisitos mencionados anteriormente, junto con algunas condiciones especiales, y el proceso de producción de una carrocería totalmente de aluminio tiene requisitos aún más estrictos.
2.4 Soldadura láser remota
En la tecnología de soldadura láser, la soldadura láser remota permite el procesamiento a larga distancia con la ayuda de cabezales galvanómetros de escaneo de alta velocidad, realizando soldaduras con rayos láser de diferentes potencias en las piezas.
Debido a sus ventajas tecnológicas únicas, se utiliza ampliamente en los techos solares panorámicos de Mercedes-Benz y en las soldaduras laterales de los automóviles Volkswagen y Audi. En la actualidad, a la hora de aplicar la soldadura remota láser en la fabricación de automóviles, ofrece las siguientes ventajas:
(1) Alta precisión de posicionamiento, que permite una soldadura rápida para satisfacer las necesidades de fabricación de las empresas automotrices.
(2) La capacidad de combinar diferentes resistencias estructurales para soldar, satisfaciendo las necesidades de diversas formas de costura de soldadura.
La soldadura láser remota requiere materiales y equipos de alta calidad. Con componentes más gruesos, no es posible reducir la profundidad de la costura de soldadura, lo que da como resultado una menor resistencia al corte en la soldadura.
2.5 Soldadura láser
En la tecnología de soldadura láser, la soldadura fuerte por láser ofrece ventajas como formas estéticamente agradables y un sellado fuerte junto con una alta resistencia de la soldadura. El principio fundamental consiste en enfocar un rayo láser en la superficie del alambre de relleno, fundirlo y luego rellenarlo en el área de soldadura para completar el proceso de soldadura fuerte.
Aunque es similar a la soldadura por fusión, el material base no se funde en este método. Por lo tanto, el material de soldadura fuerte debe tener un punto de fusión más bajo que el material base, lo que permite una soldadura efectiva a través del material de soldadura fuerte líquido, como se ilustra en la Figura 3.
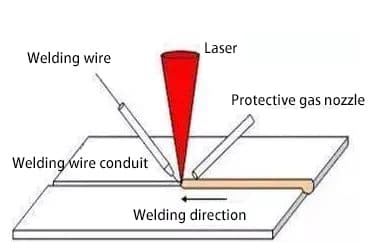
Actualmente, la soldadura fuerte por láser se utiliza para soldar tapas de maletero en vehículos Volkswagen, Haima, Chery y Audi. También se utiliza frecuentemente en las uniones del techo y del marco lateral de marcas como Cadillac, Porsche, Ford y Volkswagen.
Al utilizar esta técnica, es fundamental considerar el impacto de diversos factores en el proceso de soldadura, especialmente parámetros del proceso como la velocidad de soldadura, la potencia del láser y el diámetro del haz. Estos parámetros deben ajustarse y diseñarse de acuerdo con los requisitos de soldadura específicos para garantizar la eficacia de la soldadura fuerte por láser.
Los equipos de soldadura fuerte por láser normalmente integran la lente de procesamiento de soldadura fuerte en un brazo robótico. El rayo láser se enfoca en la unión de las láminas, derritiendo el alambre de relleno (por ejemplo, alambre de cobre-silicio) para conectar las piezas. El éxito de este método radica en conseguir una resistencia de la unión cercana a la de la soldadura, y sus soldaduras son conocidas por su belleza.
Las soldaduras producidas mediante soldadura fuerte por láser son reconocidas por sus altas propiedades de sellado y su apariencia suave y limpia, lo que hace que el retrabajo sea casi innecesario. Por ejemplo, las carrocerías de vehículos se pueden pintar directamente después de la limpieza.
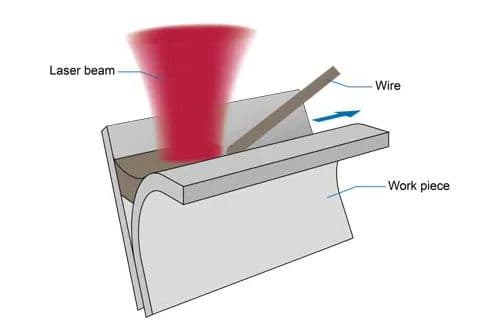
Los láseres de diodo Laserline gozan de gran prestigio en todo el mundo por su practicidad en el campo de la soldadura fuerte por láser. Se han implementado con éxito más de 800 láseres de diodo LDF para uso a largo plazo en aplicaciones de ensamblaje de carrocerías de automóviles en todo el mundo. La soldadura fuerte por láser de alta calidad no sólo requiere una alta resistencia de la soldadura y un impacto térmico mínimo, sino que también exige un atractivo estético de las conexiones de soldadura.
Una importante ventaja de procesamiento de los láseres semiconductores es la estabilidad del baño de soldadura que producen. Además, el módulo de tres haces desarrollado por Laserline ha demostrado mayores ventajas en aplicaciones de soldadura fuerte, asegurando conexiones de soldadura de alta calidad sin reducir la velocidad de soldadura, incluso cuando se sueldan materiales difíciles como láminas de acero galvanizado en caliente.
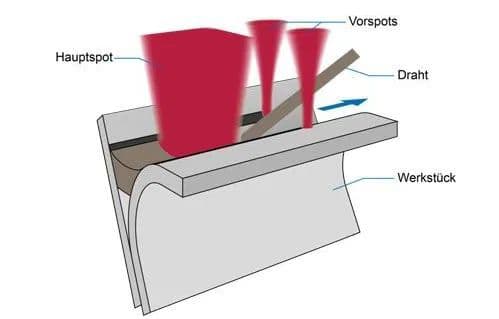
En la producción de carrocerías de automóviles, la soldadura fuerte por láser ya se ha convertido en un método de procesamiento convencional.
Sin embargo, el uso cada vez mayor de materiales de láminas de acero galvanizado ha introducido algunos desafíos, como un aumento de las salpicaduras de partículas durante la soldadura y la ondulación en la conexión soldada, lo que requiere una reducción en la velocidad de procesamiento para evitar estos problemas.
Laserline ha desarrollado una solución innovadora: utilizar un módulo multihaz, con vigas laterales colocadas delante de la viga principal, para eliminar primero la capa galvanizada alrededor del cordón de soldadura, garantizando así un proceso de soldadura suave sin necesidad de reducir la velocidad de soldadura. . Esta técnica ha sido bien recibida en la industria.
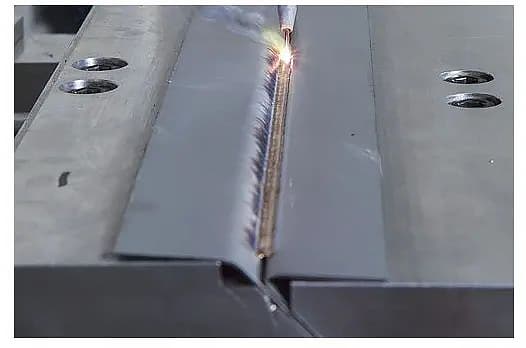
La soldadura tradicional con láser de diodo de chapa de acero galvanizado emplea tecnología de haz único, con la fuente láser integrada en el robot de soldadura. Gracias a la estabilidad del baño de fusión producido por los láseres de diodo, es posible recubrir el láser con plata o latón como material base.
Las soldaduras son estéticamente agradables y de alta calidad. Volkswagen Touran realizó una vez una comparación experimental entre un láser YAG de 4 kW y un láser de diodo de 6 kW para soldadura fuerte en Wolfsburg, Alemania. La estabilidad operativa del láser de diodo LDF se ha confirmado en la producción en masa.
Conclusión
Para la industria del automóvil, las diferentes tecnologías de soldadura láser ofrecen distintos valores de utilización.
Elegir el método de soldadura adecuado para diferentes partes de un vehículo puede mejorar la calidad general de la fabricación de automóviles y satisfacer las necesidades de las empresas automotrices en términos de costos y eficiencia de soldadura.
Al analizar los principios, ventajas y desventajas de las tecnologías de soldadura láser, este artículo explora los efectos de las aplicaciones de la soldadura láser por autofusión, la soldadura láser de relleno con alambre, la soldadura láser por arco compuesto, la soldadura láser remota y la soldadura fuerte por láser en la fabricación de automóviles.
Proporciona experiencia en soldadura para la industria automotriz, tiene como objetivo mejorar el nivel de soldadura de las empresas automotrices y promueve el desarrollo saludable y sostenible de la industria automotriz.