Se ha demostrado con ejemplos que el metal y el plástico se pueden "unir" eficazmente mediante soldadura láser.
Cabe señalar que el término "soldado" no es del todo exacto y debería sustituirse por "conectado".
Como se muestra en la Figura 1, la puerta del automóvil está reforzada con plástico de fibra de vidrio.
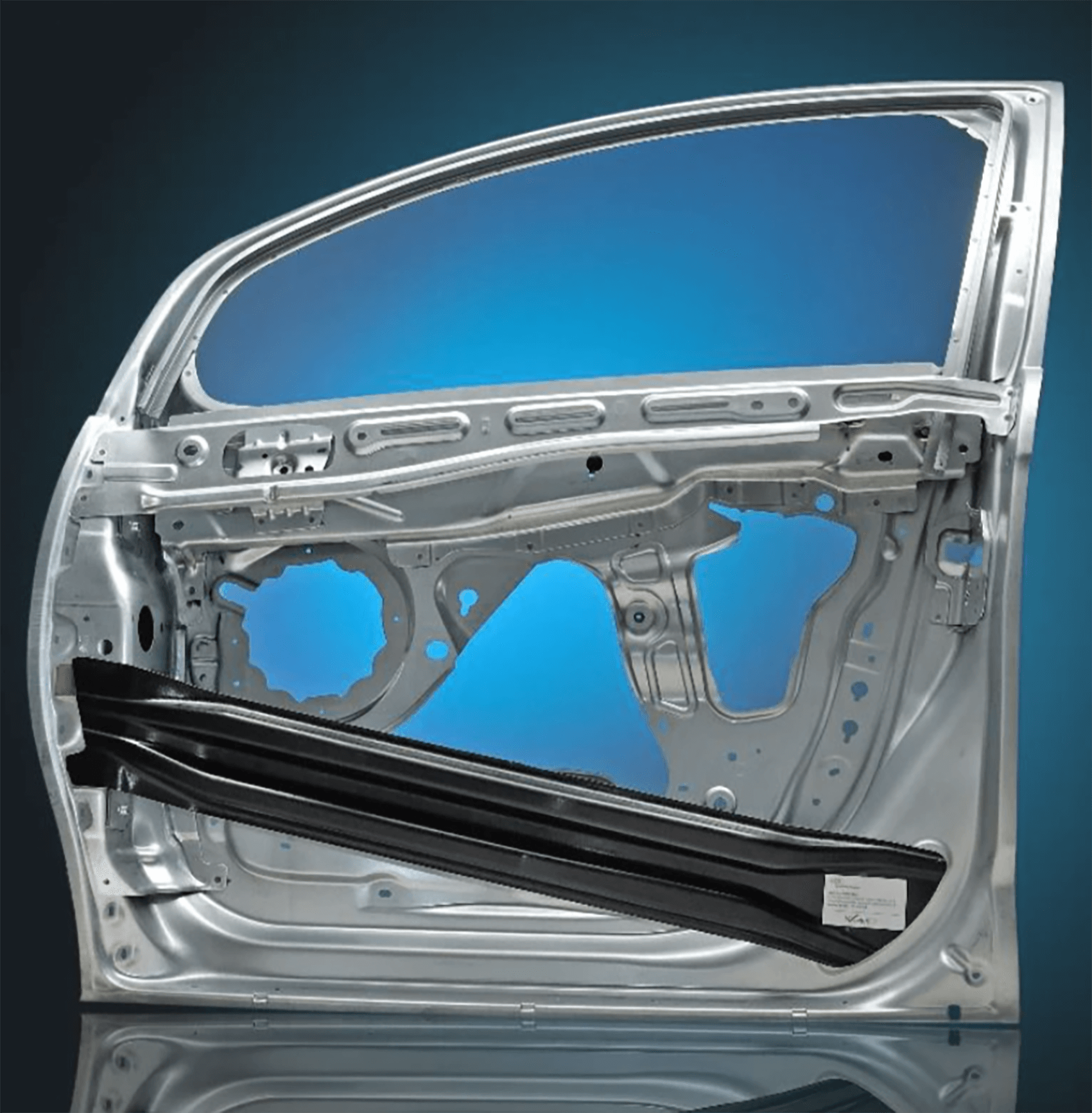
Fig. 1 Puerta de coche reforzada con plástico de fibra de vidrio.
Con el creciente enfoque en la reducción de peso en la industria automotriz, existe una creciente necesidad de conexiones efectivas entre componentes metálicos y plásticos, particularmente aquellos que contienen fibra de carbono reforzada o fibra de vidrio.
Para satisfacer las demandas de las rápidas operaciones de la línea de montaje en la industria automotriz, se necesita una solución para conexiones rápidas, confiables y automatizadas entre estos materiales.
Los siguientes son tres de los métodos más utilizados para unir piezas metálicas y compuestas en la industria: (enumere los métodos).
De ellos, la tecnología de conexión basada en láser es el avance más reciente. Sin embargo, a pesar de su potencial, aún quedan varios desafíos que enfrentar con esta tecnología, entre ellos cuestiones relacionadas con la eficiencia, la resistencia de las juntas y el envejecimiento. Este artículo proporcionará un examen en profundidad de estos desafíos.
(1) Conexión mecánica: este método es rápido, económico y proporciona una conexión estable. Sin embargo, el proceso de creación de agujeros en el material compuesto puede alterar la distribución de las fibras y debilitar la resistencia general del compuesto. Además, el uso de conectores como tornillos añade peso al conjunto.
(2) Unión: existe una amplia variedad de adhesivos disponibles para conectar varios materiales. Sin embargo, la superficie debe tratarse previamente, el proceso de unión lleva más tiempo y se debe utilizar adhesivo, lo que aumenta el coste general de la unión.
(3) Conexión láser: La conexión láser es rápida, confiable y proporciona una conexión fuerte sin necesidad de materiales auxiliares. Sin embargo, actualmente su uso está limitado únicamente a termoplásticos.
1. Conceptos básicos de la tecnología de conexión láser
El proceso de conexión láser de piezas termoplásticas y metálicas consta de dos pasos.
En el primer paso, se forma una microestructura en la superficie de las piezas metálicas mediante procesamiento láser. Normalmente, esto se logra utilizando un láser de fibra de 1 kW.
El láser escanea la superficie y crea un patrón regular de ranuras y hendiduras (como se muestra en la Fig. 2).
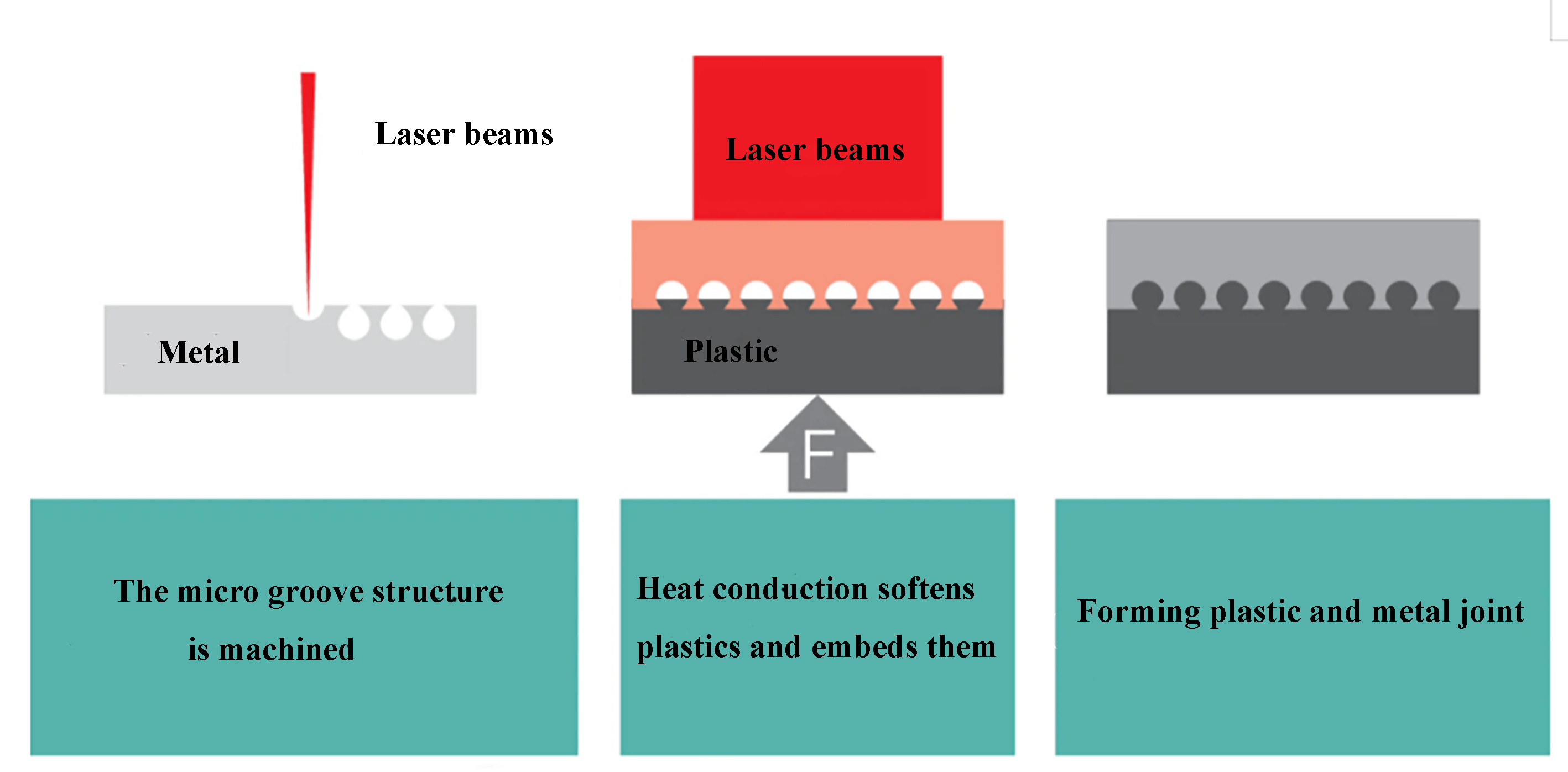
Fig. 2 Proceso de unión láser de plástico y metal
La alta densidad de potencia del rayo láser provoca la fusión parcial y la evaporación del metal durante la ablación. El metal fundido es expulsado por evaporación a alta presión y se solidifica en el borde de las ranuras para formar la estructura festoneada.
Para aumentar la adherencia del plástico a esta superficie, se puede aumentar el número y densidad de ranuras, como se muestra en la figura 3.

Fig. 3 Múltiples escaneos con rayo láser para obtener una buena forma de ranura
Un método alternativo implica el uso de un láser especial de pulso ultracorto (USP) para crear una superficie esponjosa con protuberancias cónicas. Esta técnica se puede aplicar a superficies de acero, aluminio, silicio y titanio, lo que da como resultado una resistencia de unión mejorada para los plásticos en comparación con las superficies procesadas con láseres de fibra. Sin embargo, el único desafío es que el láser USP opera a una velocidad más lenta.
En la segunda etapa, el plástico se calienta hasta que se derrita y luego se presiona sobre la superficie del metal. Después del enfriamiento, el plástico queda firmemente adherido al metal.
Existen varios métodos para calentar plásticos, como usar una placa caliente, radiación infrarroja u otros procesos para calentar directamente el plástico, o calentar piezas metálicas y presionarlas sobre plástico frío, lo que hace que el plástico se derrita y fluya hacia pequeñas estructuras a través de la conducción de calor. .
El primer paso del micromecanizado láser es rápido y sin contacto, lo que lo hace ideal para la integración en procesos de producción existentes y producción en masa.
2. Prueba de resistencia de la conexión
En aplicaciones prácticas, la unión entre metal y plástico estará sometida a cargas. ¿Cuál es la presión máxima que puede soportar este tipo de conexión compuesta y dónde fallará?
El Instituto de Investigación de Tecnología Láser Hoff en Alemania llevó a cabo una serie de pruebas de estrés en varios materiales para responder estas preguntas (Figura 4).
Uno de los contenidos de la prueba es el siguiente:
- La prueba de corte se realizó sobre una placa de acero inoxidable de 1,5 mm y un conector de plástico PP de 3 mm con fibra de vidrio.
- Se realizó una prueba de tracción en una placa de acero inoxidable de 1,5 mm y un conector de plástico PP de 3 mm (excluyendo fibra de vidrio).
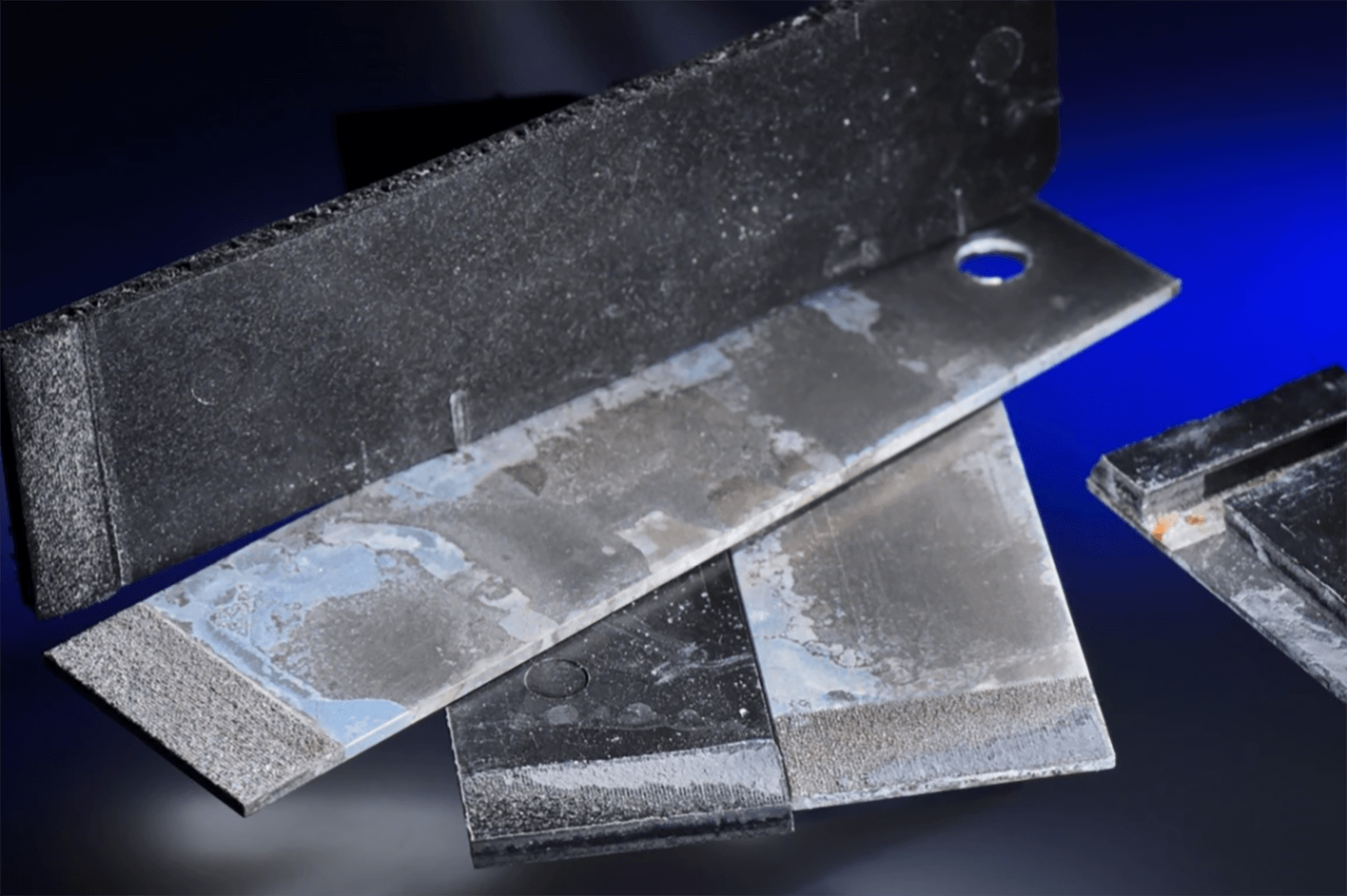
Fig. 4 Superficie de fractura de una junta de metal y plástico después de la prueba de corrosión
Se utiliza un láser de fibra monomodo de 1 kW para microprocesar la superficie del metal, con un diámetro de punto de aproximadamente 40 micrómetros. El láser produce una estructura de ranura reproducible en la superficie del metal. El plástico se calienta mediante un láser semiconductor de potencia nominal de 3 kW, con un tamaño de punto de 7,5 mm x 25 mm. Las dos partes se fijan con una presión de 0,3 MPa.
Los resultados de la prueba son los siguientes:
- Para la unión entre acero inoxidable y PP con fibra de vidrio, el área de conexión es de 150 mm².
- Para la conexión entre acero inoxidable y PP, el área de conexión es de 100 mm².
Se llevaron a cabo pruebas destructivas en 5 muestras de cada uno de los dos tipos anteriores.
Para la conexión entre acero inoxidable y PP con fibra de vidrio se realizó una prueba de resistencia al corte. Los resultados son los siguientes:
- Cuando la separación entre ranuras era de 400 micrómetros, la carga de corte máxima fue de 13,1 MPa.
- Cuando la separación entre ranuras era de 300 micrómetros, la carga de corte máxima fue de 15,5 MPa.
Para la unión entre acero inoxidable y PP se realizó una prueba de resistencia a la tracción. Los resultados son los siguientes:
- Cuando la separación entre ranuras era de 400 micrómetros, la carga de tracción máxima fue de 5,1 MPa.
- Cuando la separación entre ranuras era de 300 micrómetros, la carga de tracción máxima fue de 9,1 MPa.
Es evidente que una distribución densa de ranuras mejora la resistencia de la conexión. Sin embargo, cabe señalar que una distribución densa de canales también aumentará el tiempo de micromecanizado.
También se realizó un experimento similar con una lámina de magnesio.
Todas las pruebas demostraron que la tecnología de unión basada en láser crea una conexión fuerte y confiable entre componentes de metal y plástico.
3. Prueba de envejecimiento
Otra preocupación importante en los productos automotrices es su resistencia a los impactos del cambio climático y la corrosión. Para responder a esta pregunta, los expertos del Instituto de Tecnología Láser Hoff de Alemania llevaron a cabo varias pruebas.
En el experimento se unieron mediante tecnología láser diversos metales (acero y aluminio) y plásticos (PP con un 30% de fibra de vidrio y PP con un 40% de talco). Para la prueba de cambio climático se utilizó el estándar VW PV 1200, con temperaturas que oscilaron entre 80°C y 40°C.
Cada ciclo de prueba duró 12 horas y se repitió dos veces, 10 veces y 30 veces, respectivamente. La resistencia al corte destructivo de las muestras se probó antes y después de cada ciclo. Los resultados mostraron que todas las muestras presentaron resistencia al corte entre 8 y 15 MPa.
En la prueba se hizo una observación interesante: después de 30 ciclos, todas las muestras de PP llenas con talco mostraron grietas fuera del área de conexión durante la prueba de resistencia, lo que indica que la unión era más fuerte que el material de PP en masa.
Un resultado similar se observó en la prueba de resistencia a la corrosión, que se realizó según VDA 621-415 durante 7 días, incluyendo niebla salina y condiciones de alta humedad. Antes de las pruebas, todas las muestras tenían una resistencia al corte de 8-5 MPa. Después de la prueba de corrosión, la prueba de corte mostró que todas las muestras de PP que contenían talco tenían grietas fuera del área de conexión, mientras que la muestra de PP que contenía fibra de vidrio se rompió en el área de la junta, pero su resistencia era mayor que antes de la prueba.
Se observó corrosión en el acero inoxidable, especialmente en su microestructura, y el área de unión por láser mostró una penetración de corrosión obvia, pero no tuvo un efecto significativo sobre la resistencia de la unión. También se encontraron signos de corrosión en la microestructura fuera de la zona de la junta, pero no dentro de la zona de la junta.
Por tanto, se puede concluir que la microestructura no debe exponerse a ambientes abiertos.
4. Conclusión
Se ha probado y demostrado que la técnica de conectar metal y plástico mediante tecnología láser produce conexiones fuertes y confiables. Los resultados de las pruebas climáticas y de corrosión no mostraron ningún impacto en la resistencia de las juntas. Después del envejecimiento, las muestras mostraron que las fracturas se produjeron en el cuerpo de plástico y no en el punto de conexión.