1. Definición y clasificación de soldadura unilateral y conformado bilateral.
1.1 Definición de soldadura por un solo lado y conformado por ambos lados.
La soldadura por una cara y el conformado por ambas caras son métodos y habilidades esenciales para los soldadores que participan en la soldadura de recipientes a presión, silos importantes y calderas. También se utiliza en la fabricación e instalación de importantes estructuras de acero soldadas que requieren una penetración total pero que no se pueden procesar ni volver a soldar en la parte posterior de los componentes.
Durante esta soldadura no son necesarias otras medidas auxiliares. Sin embargo, cuando se requiere el posicionamiento de la soldadura en la raíz de la ranura, se deben reservar diferentes espacios de acuerdo con los diferentes métodos de soldadura.
Cuando la soldadura se realiza en el lado frontal de la ranura, se pueden obtener soldaduras uniformes, regulares y calificadas tanto en el lado frontal como en el posterior de la ranura. Esta operación de soldadura poco convencional se conoce como “soldadura por un lado y conformado por dos lados”.
1.2 Clasificación de soldadura unilateral y conformado bilateral.
1.2.1 Método de soldadura por arco intermitente
Para comenzar el proceso de soldadura, coloque el panel de prueba con el extremo ligeramente separado en el lado izquierdo. Colóquelo para formar arco y utilice un arco largo para precalentar los componentes de soldadura durante un período de tiempo determinado. Luego presione el arco y mueva el electrodo hacia un lado entre los dos bordes romos para soldar.
A medida que el metal fundido del borde romo se conecta con el metal fundido del electrodo, escuche el sonido de "porfirina", que indica una unión exitosa. Entonces se apagará la luz del arco.
Durante cada arco continuo, el centro del electrodo de soldadura debe estar alineado a 2/3 del recorrido a través del charco de soldadura. Esto asegura que ambos lados del borde romo se derritan al mismo tiempo. Tan pronto como se escuche el sonido de la “porfirina”, apague rápidamente el arco, permitiendo que el baño de soldadura recién formado cubra aproximadamente 2/3 del baño de soldadura formado previamente.
1.2.2 Método de soldadura por arco continuo
La soldadura por arco continuo es una tecnología que implica quemar continuamente el arco durante la soldadura sin apagar la luz del arco. Utiliza un pequeño espacio en la ranura y una pequeña corriente de soldadura al principio, manteniendo una soldadura continua por arco corto.
Los elementos básicos de esta tecnología implican golpear el arco con el electrodo y aplicar una presión mínima. Luego, en el punto inicial de la soldadura, se utiliza el método de movimiento del electrodo en forma de diente de sierra con paso pequeño para girar el electrodo hacia los lados y precalentar los componentes de soldadura.
La varilla de soldadura debe enviarse hacia la raíz lo más posible para impulsar la acción de rotura del electrodo. Cuando se escucha un sonido de “porfirina”, la soldadura formará un agujero disuelto. El arco debe transferirse inmediatamente a cualquier posición en la superficie de la ranura y luego se debe utilizar un cierto ángulo de electrodo entre las superficies de la ranura.
La operación implica pequeñas acciones ininterrumpidas que duran unos 2 segundos. Cuando el arco derrita la raíz de la ranura en ambos lados aproximadamente 1,5 mm, la varilla de soldadura debe elevarse entre 1 y 2 mm. El electrodo debe girarse en zigzag con un pequeño paso para que el arco quede delante del orificio de fusión mientras se realiza la soldadura hacia adelante.
Durante la soldadura, es crucial asegurarse de que el centro de la varilla de soldadura esté alineado con el borde frontal del baño de soldadura y la unión del metal base, de modo que cada nuevo baño de soldadura se superponga al baño de soldadura generado anteriormente. Durante la extinción del arco, el electrodo debe llevarse lentamente hacia el lado derecho o izquierdo, detrás del baño de soldadura, y elevarse para extinguir el arco.
Al soldar juntas, el arco debe encenderse a una distancia de 10 a 15 mm del cráter al principio y el electrodo debe moverse hasta la mitad del cráter a velocidad normal. Luego se debe presionar el electrodo hacia abajo y cuando se escuche un sonido de “porfirina”, se debe realizar una ligera oscilación durante 1-2 segundos. Después de eso, el electrodo debe elevarse entre 1 y 2 mm para que pueda moverse hacia adelante para soldar mientras se funde el frente del orificio de fusión.
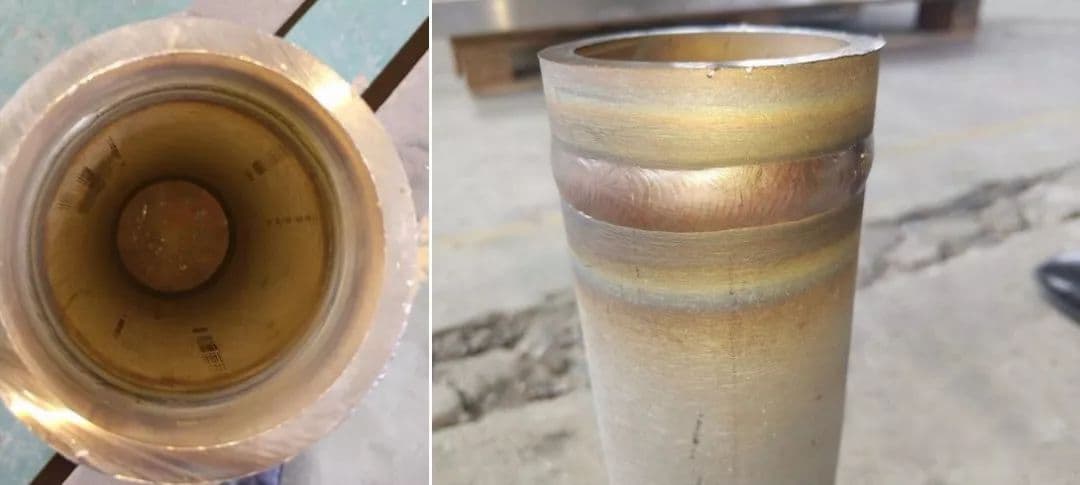
2. Análisis del proceso de soldadura a tope de placas y conformado a doble cara.
2.1 Preparación antes de soldar
(1) Espesor de la placa: 12 mm, Especificación: 300 × 200 mm.
Corte el tablero con oxígeno y gas acetileno o use tijeras y máquinas cortadoras, y luego use métodos mecánicos como cepilladoras o amoladoras angulares para procesar ranuras en forma de V.
No se permiten chaflanes en la parte posterior de las ranuras.
Asegúrese de que las ranuras sean rectas, lisas y libres de rebabas, protuberancias y otras imperfecciones.
(2) Para limpiar el panel de prueba, utilice una lima para quitar las esquinas afiladas de la ranura, manteniendo el tamaño del borde romo entre 0,5 y 1,0 mm. Elimina óxido, aceite, óxidos y otros contaminantes de la ranura y dentro de los 20 mm en ambos lados, dejando un brillo metálico.
(3) Montaje del panel de prueba y soldadura por puntos.
Realice soldadura por puntos en ambos extremos de la parte posterior del tablero de prueba y deje un margen de contracción.
Establezca el espacio del extremo de la soldadura en 3,0-3,5 mm, el espacio del extremo de la soldadura en 3,5-4,0 mm y la longitud de la soldadura colocada en aproximadamente 10-15 mm.
Asegúrese de que la soldadura en su lugar esté apretada, especialmente en el extremo final de la soldadura.
Para evitar cualquier impacto negativo en la soldadura continua o fractura durante la soldadura causada por la reducción del espacio de la ranura en la sección no soldada debido a la contracción de la soldadura, reserve un margen de deformación inversa durante la soldadura en posición, es decir, una deformación inversa del ángulo de soldadura de 3°-. 4°.
(4) Equipo de soldadura: máquina de soldadura por arco CC serie ZXG.
Tipo de fuente de alimentación y polaridad: asegúrese de que la varilla de soldadura de CC no se vea afectada por la humedad y el deterioro, que el núcleo de soldadura esté libre de óxido y que el revestimiento no se agriete ni se caiga.
Hornee la varilla de soldadura a 350-400 ℃ antes de usarla, mantenga una temperatura constante durante 2 horas y suelde en cuatro capas.
(5) Fije la placa de prueba: coloque la placa de prueba antideformación horizontalmente sobre el marco de soldadura a una altura adecuada.
El soldador no debe sentarse mientras suelda y debe trabajar en posición agachada.
El ángulo de la ranura de la placa de prueba es de 60°.
2.2 Operación de soldadura
2.2.1 Soldadura de la capa inferior
La soldadura de imprimación se puede realizar mediante soldadura general, soldadura por arco final o soldadura por arco continuo.
Para iniciar el proceso de soldadura, se debe encender el arco en el lado interior de la ranura del panel de prueba y presionar el arco inferior. La varilla de soldadura debe balancearse suavemente hacia adelante y hacia atrás entre los dos bordes romos de la ranura hasta que el hierro fundido en el borde se combine con la gota fundida de la varilla de soldadura, produciendo un sonido de "porfirina" y formando el primer charco derretido.
En esta etapa, debe haber un orificio de disolución delante del tanque de disolución con una profundidad de 0,5 a 1,0 mm en ambos lados de la ranura de la placa de prueba.
Para el funcionamiento de la varilla de soldadura se adopta el método de soldadura por oscilación transversal en forma de zigzag o media luna. La longitud del arco oscilante debe ser menor o igual al diámetro del electrodo. Se utiliza un arco corto para enviar el hierro fundido a través de la raíz de la ranura hasta la parte posterior de la pieza soldada.
Cuando la varilla de soldadura se transporta a ambos lados de la ranura, se requiere una pausa de 1 a 2 segundos. Esta pausa conduce a una buena fusión del metal de aportación y el metal base y también evita la formación de esquinas afiladas en la unión de soldadura y ranura, lo que es útil para la eliminación de escoria.
2.2.2 Ángulo del electrodo
El ángulo incluido de la dirección de soldadura directa es de 70°-80°.
Un ángulo de electrodo adecuado conduce a la separación de la escoria fundida del hierro fundido, manteniendo el baño fundido limpio y brillante en todo momento y evitando la sedimentación.
Puntos clave de la varilla de soldadura: mirar, escuchar, ser preciso y breve.
El ángulo incluido para la dirección de soldadura directa debe estar entre 70° y 80°.
Un ángulo de electrodo adecuado ayuda a separar la escoria fundida del hierro fundido, mantiene el charco fundido limpio y brillante y evita la sedimentación.
Los puntos principales para utilizar una varilla de soldar son: observar, escuchar, ser preciso y trabajar eficientemente.
“Observar” significa prestar atención a la forma del baño de soldadura y al tamaño del orificio de soldadura, lo que determina la altura y la resistencia de la soldadura posterior.
El charco de fusión debe tener forma redonda u ovalada y siempre brillante y transparente para separar la escoria del hierro fundido.
El orificio de fusión debe ser tal que el arco funda todos los bordes romos de ambos lados y penetre de 0,5 a 1,0 mm en el metal base de cada lado.
Cuando el orificio es demasiado grande, la soldadura en la parte posterior es demasiado alta y, en casos graves, puede producirse un cordón de soldadura o una quemadura.
Para remediar esta situación, se debe aumentar la velocidad de soldadura, se debe aumentar el rango de oscilación del electrodo hacia ambos lados de la ranura y se debe reducir el ángulo incluido entre el electrodo y la dirección de soldadura.
Cuando el orificio es demasiado pequeño, la raíz de la ranura no está completamente soldada y la fusión de la raíz de la soldadura no es buena.
Para solucionar esto, se debe presionar el arco inferior para aumentar el ángulo de la varilla de soldadura en la dirección de avance, disminuir la velocidad de soldadura y la amplitud de oscilación, reducir el ángulo entre la varilla de soldadura y la dirección de soldadura de avance y mantener la forma de la piscina de soldadura y el tamaño del orificio de soldadura.
Durante la soldadura, es esencial controlar la dirección del flujo del hierro fundido y la solución.
El arco eléctrico siempre debe arder delante del hierro fundido.
La fuerza de soplado inverso del gas generado por el arco eléctrico y la fusión del recubrimiento se utiliza para soplar el hierro fundido hacia la parte trasera del baño fundido, asegurando la penetración de la soldadura, la separación de la escoria fundida y el hierro, y reduciendo posibles defectos de inclusión y escoria en la soldadura. porosidad.
Además, es necesario observar siempre la fusión de la ranura soldada.
El borde posterior del baño de soldadura debe estar completamente fusionado con las ranuras de ambos lados.
"Escuchar" significa que el soldador no debe distraerse durante la soldadura y debe escuchar el sonido de "porfirina" cuando el arco rompe la placa de prueba.
Si no se escucha este sonido, el arco no romperá la raíz de la ranura y continuar soldando dará como resultado una soldadura impermeable.
Generalmente, mantenga el extremo del electrodo a 2 o 3 mm de distancia de la raíz de la ranura.
“Preciso” significa que la posición de contacto del arco debe ser precisa. Cada nuevo baño de soldadura debe superponerse al anterior en 2/3 para garantizar que 1/3 del arco esté directamente delante del baño de soldadura.
Cuando el soldador escucha el sonido “por por”, debe apagar rápidamente el arco detrás del baño de soldadura. De esta forma se puede ejercer plenamente el efecto protector del arco sobre el baño fundido, evitando la formación de poros.
Corto” se refiere al tiempo de extinción del arco y soldadura a tope, que debe completarse lo más rápido posible; de lo contrario, pueden ocurrir defectos de contracción en frío y grietas en el metal debido a una fusión insuficiente entre los baños de soldadura.
Para evitar agujeros de contracción en frío, aumente la frecuencia de extinción del arco y reduzca el tiempo de contacto del arco. Mientras que el baño fundido anterior todavía está líquido, el siguiente baño fundido ya debe estar formado, de modo que el baño fundido permanezca en un estado de alta temperatura.
Para el método de ruptura de dos puntos, la frecuencia de extinción del arco debe ser de 50 a 60 veces por minuto, mientras que para el método de ruptura de un solo clic, la frecuencia de extinción del arco debe ser de aproximadamente 80 veces por minuto.
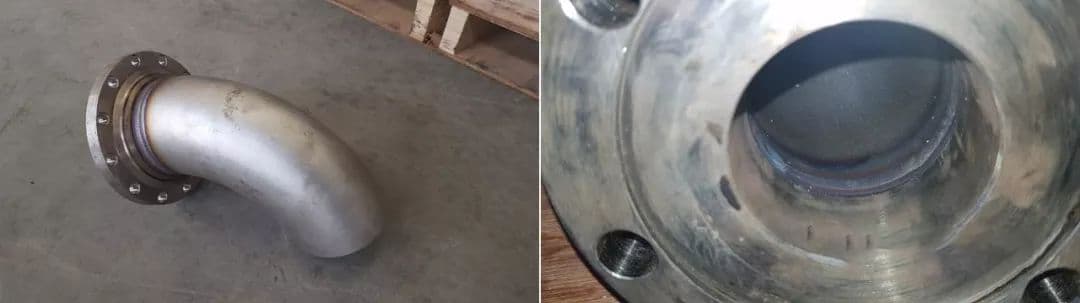
2.2.3 Juntas
Los diferentes tipos de juntas se clasifican en conexiones calientes y conexiones frías, y sus descripciones se proporcionan por separado a continuación.
Conexión en caliente:
Para soldar en el estado de cráter caliente del arco, golpee el arco en la pendiente, 10 a 15 segundos detrás del cráter. Suelde hacia el tope del arco frontal para aumentar gradualmente la temperatura en el fondo del cráter. Luego presione el electrodo a lo largo del orificio prefabricado. Cuando escuche el sonido de la “porfirina”, deténgase y levante el electrodo para realizar una soldadura normal.
Es mejor reemplazar el electrodo lo antes posible.
Conexión fría:
Cuando el cráter del arco se haya enfriado, retire el cráter del arco y los primeros 10 mm de escoria fundida del acero al carbono. Limpie el área y reemplace la varilla de soldadura.
En el punto más bajo de la pendiente, presione rápidamente la varilla de soldadura a lo largo del orificio prefabricado. Cuando escuche el sonido de "porfirina", haga una pausa de aproximadamente 1 segundo antes de levantar la varilla de soldadura para comenzar la soldadura normal.
Existen dos métodos para la técnica de soldadura por rotura de arco: las técnicas de perforación con un clic y con dos clics.
Para la técnica de perforación de dos clics, el arco se enciende en ambos lados de la ranura y primero se deja caer una gota de hierro fundido sobre el borde romo izquierdo, seguida de una gota de hierro fundido sobre el borde romo derecho, alternando gradualmente.
Esta técnica de soldadura es adecuada para trabajos con grandes espacios en el conjunto de soldadura.
Para el método de penetración con un solo clic, el arco enciende los bordes romos a ambos lados de la ranura y se funde simultáneamente.
El modo básico de funcionamiento es el siguiente: encender el arco.
Al soldar, comience formando un arco en el interior de la ranura en el borde anterior del panel de prueba. Precaliente la pieza inicial con un arco largo, luego baje el arco y mueva el electrodo hacia adelante y hacia atrás entre los dos bordes romos.
Cuando el hierro fundido en el borde romo de la ranura se combina con la gota de metal del electrodo y se escucha un sonido de "porfirina", se formará el primer charco fundido y el arco se extinguirá.
En este punto, el extremo frontal del primer baño fundido se convertirá en un orificio fundido, que debe perforarse entre 0,5 y 1,0 mm de profundidad en ambos lados de la placa de prueba. Reemplace la junta de la varilla de soldadura.
El método para cambiar la varilla de soldadura durante la soldadura por arco es básicamente el mismo que el de la soldadura por arco continuo. Antes de cambiar la varilla de soldadura, para evitar agujeros de contracción en frío debido a la extinción del arco, el arco no debe apagarse demasiado rápido. Se deben enviar dos o tres gotas de hierro fundido al borde o al norte del charco fundido con anticipación, se debe llenar el charco fundido posterior y se debe controlar la temperatura del charco fundido para enfriarlo lentamente.
Se debe formar un orificio de soldadura delante del baño de soldadura. Presione el arco en un lado de la ranura y suelde unos 10 mm antes de apagar el arco. Esto asegura que el hierro fundido en el baño fundido trasero esté lleno y sea suficiente para evitar defectos de contracción en frío.
Después de cambiar rápidamente el electrodo, el arco debe iniciarse entre 10 y 15 mm del frente del cráter. Una vez encendido, se debe retirar el arco y precalentar el metal a soldar con un arco largo.
Luego se debe presionar el arco unos 10 mm detrás del cráter. La varilla de soldadura debe operarse continuamente hasta la raíz del cráter.
Después de escuchar el sonido de la “porfirina”, se debe detener el arco durante unos 2 segundos para extinguirlo. Luego, se debe utilizar el método original de soldadura por arco intermitente para continuar soldando.
Tenga en cuenta lo siguiente:
(1) El espesor de la soldadura de imprimación delante y detrás de la ranura debe estar entre 1,5 y 2,0 mm.
(2) Los soldadores deben girar la barra usando sus muñecas de manera flexible.
(3) Se deben realizar cuatro soldaduras de 300 mm de longitud cada una.
2.2.4 Soldadura de capa de relleno
Una vez enfriada la escoria de soldadura de la capa anterior, retirar con cuidado las escorias y salpicaduras, prestando especial atención a las esquinas.
Después de quitar la espuma, use un cepillo de alambre para limpiar el área hasta que la superficie metálica quede expuesta.
Inicie el arco a 10 mm del inicio de la soldadura y luego regrese el arco al punto inicial de la soldadura.
Utilice un electrodo en forma de media luna o de diente de sierra y haga una pausa breve cuando el electrodo oscile hacia cualquier lado de la ranura para estabilizar el arco.
Muévase rápidamente por el centro de la ranura, manteniendo el arco lo más bajo posible. Esto ayudará a facilitar la eliminación de impurezas en las esquinas afiladas del canal profundo y evitará la inclusión de escoria.
Mantenga el equilibrio en el baño fundido y en ambos lados de la ranura para evitar que se forme escoria en la unión entre el metal de aportación y el metal base. Esto es difícil de aclarar.
El ángulo incluido entre la varilla de soldadura y el progreso de la soldadura debe ser de 75°-85°.
Adopte un arco corto al soldar y asegúrese de que el baño de soldadura sea redondo u ovalado con forma y tamaño consistentes.
Mantenga una velocidad de soldadura uniforme y un espesor constante de la lechada de soldadura.
Utilice métodos térmicos al soldar la junta.
Antes de cambiar la varilla de soldadura para detener el arco, agregue ligeramente hierro fundido al baño de soldadura formado.
Después de un cambio rápido de la varilla de soldadura, inicie el arco unos 10 mm delante del cráter del arco.
Luego dibuje el arco hasta 2/3 del cráter, rellene el cráter primero y luego continúe con la soldadura normal.
Escalone las uniones de conexión de cada capa de soldadura.
La altura de relleno de la última capa debe ser entre 0,5 y 2,0 mm más baja que la superficie del metal base, y la forma debe ser alta en ambos lados y cóncava en el medio.
Asegúrese de que la soldadura sea suave y que la ranura sea excesiva para garantizar que la ranura sea claramente visible al soldar la cubierta. Esto ayudará a garantizar que el borde soldado de la tapa esté recto.
2.2.5 Soldadura de la capa de cobertura
El método de formación del arco para la capa de cobertura es el mismo que para la capa de relleno. Utilice un electrodo en forma de media luna o de diente de sierra transversal.
La amplitud de oscilación del electrodo debe ser ligeramente mayor que la de la capa de relleno. Asegúrese de que la amplitud de la oscilación sea constante durante toda la oscilación y que la velocidad del electrodo sea uniforme.
La forma del charco de soldadura es ovalada. Intente mantener la forma y el tamaño de la piscina aproximadamente iguales y utilice soldadura por arco corto.
Cuando la varilla de soldadura oscila hacia el borde de la ranura, estabilice el arco y detenga la punta. La fusión en el borde de la ranura debe ser de aproximadamente 1,0 a 2,0 mm.
Ambos lados de los bordes de soldadura deben estar bien fusionados para evitar socavaduras.
La velocidad de avance de la soldadura debe ser uniforme para que la superficie de soldadura sea suave y hermosa.
Cuando utilice uniones de varillas para soldar, adopte el método de unión en caliente.
Antes de reemplazar la varilla de soldadura para apagar el arco, agregue ligeramente hierro fundido al baño de soldadura.
Después de reemplazar la varilla de soldadura, golpee el arco aproximadamente 10 mm delante del cráter, luego lleve el arco hacia atrás hasta 2/3 del cráter, rellene el cráter y luego realice la soldadura convencional.
Si la parte de la articulación está desviada, la parte de la articulación será más alta. Si la unión se desvía, se producirá un defecto en la separación de la soldadura.
3. Defectos comunes de la soldadura por un solo lado y el conformado por ambos lados.
En resumen, los defectos comunes que pueden ocurrir durante la unión a tope de placa con placa, la soldadura de un lado y el proceso de conformado de dos lados incluyen: bolsas de aire, penetración incompleta, fusión incompleta y formación de cordones de soldadura, entre otros.
En el siguiente apartado analizaremos y detallaremos estos posibles defectos con más detalle.
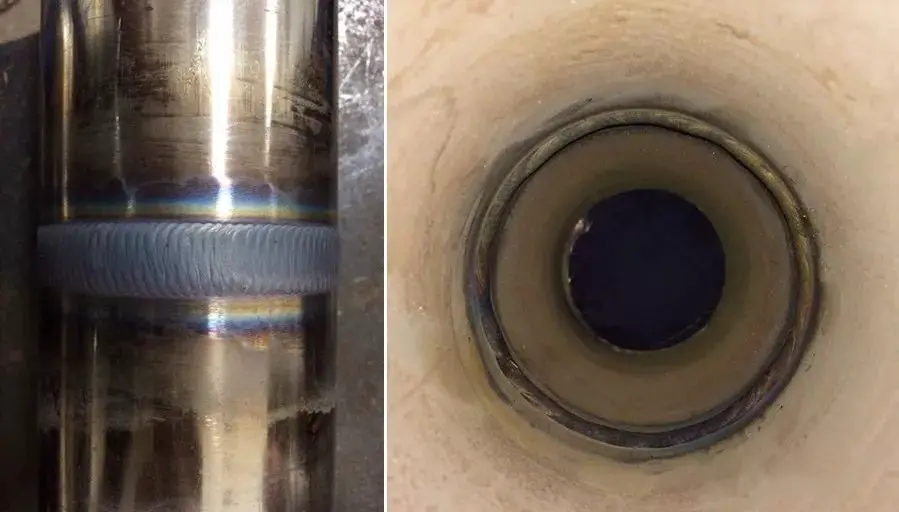
3.1 Porosidad
Los agujeros de aire se forman en el metal de soldadura cuando el gas presente en el baño de soldadura no puede escapar antes de que el metal de soldadura se solidifique durante la soldadura.
Este gas puede ser absorbido por el baño de soldadura del ambiente externo, siendo el hidrógeno y el monóxido de carbono los gases más comunes. También puede producirse como resultado de la reacción del metal durante la soldadura.
Por ejemplo, si el metal base contiene una cantidad excesiva de azufre, se formarán bolsas de gas durante el proceso de fusión con el metal del electrodo.
(1) A continuación se analizan las principales causas de la porosidad durante la soldadura:
La superficie del metal base o metal de aportación a soldar debe estar limpia y libre de impurezas como manchas de aceite y óxido.
Es importante asegurarse de que el fundente o electrodo de soldadura esté completamente seco antes de soldar, ya que la presencia de humedad puede hacer que se descomponga en gas durante el proceso de soldadura, lo que provocará un aumento en la formación de poros.
La baja energía lineal durante la soldadura da como resultado un rápido enfriamiento del baño de soldadura, lo que dificulta que el gas escape del metal de soldadura de manera oportuna.
Una desoxidación inadecuada del metal de soldadura también puede provocar una mayor formación de poros de oxígeno.
Los factores ambientales, como la humedad excesiva en días lluviosos o con niebla, pueden hacer que la soldadura absorba humedad del aire circundante durante la soldadura, aumentando aún más la formación de porosidad.
(2) Daño a los estomas.
Existen varias especificaciones que regulan el número de poros permitidos.
Sin embargo, la presencia de orificios de aire durante la soldadura puede reducir el área seccional efectiva de la soldadura, aflojar la junta, reducir su resistencia y provocar accidentes de producción, como fugas.
La porosidad también puede generar defectos estructurales que provocan tensiones concentradas y dañan los componentes, reduciendo así su resistencia y afectando su vida útil.
Por ello, es fundamental analizar las causas de la aparición de los poros de forma individual y evitar factores externos que puedan provocar su formación. Este enfoque ayudará a minimizar la aparición de poros durante la soldadura.
3.2 Penetración y fusión incompletas
3.2.1 Causas de penetración incompleta
(1) El ángulo de la ranura de la placa de prueba puede reducirse, el borde ciego puede ser demasiado grande o el espacio de montaje puede ser demasiado pequeño, lo que da como resultado una longitud de soldadura por puntos insuficiente y una soldadura demasiado delgada. Las tensiones de tracción y contracción durante la soldadura pueden hacer que el espacio en el punto de soldadura por puntos disminuya o que el electrodo seleccionado sea demasiado grande, impidiendo que el metal depositado llegue a la raíz de la ranura.
(2) Una velocidad de soldadura demasiado rápida o una corriente de soldadura demasiado pequeña pueden provocar una disminución de la fuerza de penetración del arco, baños de soldadura poco profundos y una fusión insuficiente de los bordes de soldadura. El tiempo de combustión del arco de soldadura estallado en ambos lados de la ranura también puede ser demasiado corto para formar un orificio de cierto tamaño.
(3) Un ángulo inadecuado del electrodo o una desviación magnética del arco pueden causar que el calor del arco se pierda o se desvíe hacia un lado, lo que resulta en una penetración incompleta.
(4) Durante la soldadura con imprimación, puede ocurrir una penetración incompleta de la junta. Esto es algo común en la soldadura de placas después de cambiar la varilla de soldadura. La temperatura del arco de impacto disminuye, provocando una gran diferencia de temperatura entre las piezas soldadas y no soldadas, se realiza un gran espacio entre las placas de prueba y la soldadura antes de alcanzar la temperatura de precalentamiento requerida. Como resultado, el arco en la junta no puede atravesar rápidamente el borde romo de la pieza de prueba, lo que provoca una sección de penetración incompleta en la junta y produce defectos.
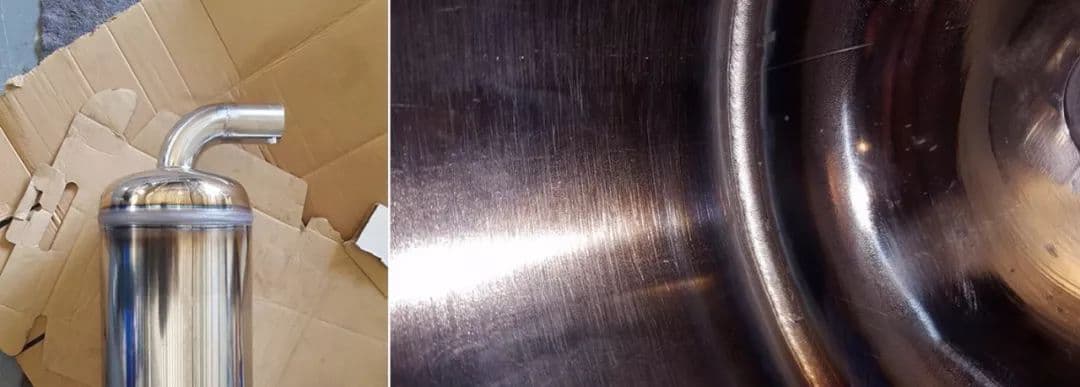
3.2.2 Medidas para prevenir defectos de penetración incompleta
(1) Elija el ángulo correcto del electrodo.
Al realizar la soldadura de respaldo, es importante controlar adecuadamente la velocidad de soldadura para garantizar que el arco funda completamente la raíz.
(2) Limpie a fondo la soldadura de ranura para eliminar aceite, óxido u otros residuos.
(3) Durante el proceso de soldadura, si el electrodo excéntrico provoca la desviación del arco, ajuste inmediatamente el ángulo del electrodo. Gire el electrodo en la dirección opuesta a la desviación del arco para alinear el arco con el baño de soldadura o reemplace el electrodo.
(4) Supervise de cerca la condición de la fusión durante la soldadura para garantizar una fusión adecuada.
3.3 Superposición
(1) El borde biselado es demasiado romo y el espacio de montaje es demasiado grande.
(2) Durante la soldadura plana, la corriente de soldadura excesiva y la velocidad de soldadura lenta pueden hacer que aumenten la temperatura y el volumen del borde de soldadura. Esto puede provocar que el metal líquido caiga debido a la gravedad.
(3) El ángulo incorrecto de la varilla de soldadura también puede ser un problema durante la soldadura.
Medidas de prevención para la superposición de soldadura:
(1) Elija el tamaño apropiado para el borde ciego y el espacio de montaje, y ajuste el tamaño del orificio de fusión durante el proceso de soldadura.
(2) Controle estrictamente la temperatura actual e intermedia.
(3) Elija un ángulo de electrodo apropiado y gire el electrodo más rápido en el medio y más lento en ambos lados.
(4) Observe atentamente el estado del baño de soldadura.
(5) Si se emiten más chispas pequeñas desde el baño de soldadura, apague el arco inmediatamente para disminuir la temperatura del baño de soldadura antes de continuar con el proceso de soldadura.